Story at a glance:
- Materials matter, and sustainable solutions every step of the way ultimately add up to a better project in the long run, architects says.
- Leaders like GCP Applied Technologies are continually stepping up to fill the need for innovative, sustainable construction products.
Big or small, the choices architecture and design teams make every day add up to whether a project contributes to a more sustainable world or not.
“It’s incredibly important. We want to work with manufacturers and suppliers who share our passion for advancing sustainable solutions and making the most progress,” says Stephen Katz, a technical director in Gensler’s Chicago office. “Manufacturers have a really deep understanding of their process and where they get their materials. Some of the solutions that are out there are really going to come from the manufacturing and fabrication side.”
Innovation in Action
Companies like GCP, a Saint-Gobain company, have long been committed to innovating with new solutions for more sustainable construction. Areas like waterproofing, fireproofing, and weatherproofing are among their top products aiming to make projects more energy-efficient while reducing carbon footprint in the manufacturing and build process.
Evolution of Fireproofing
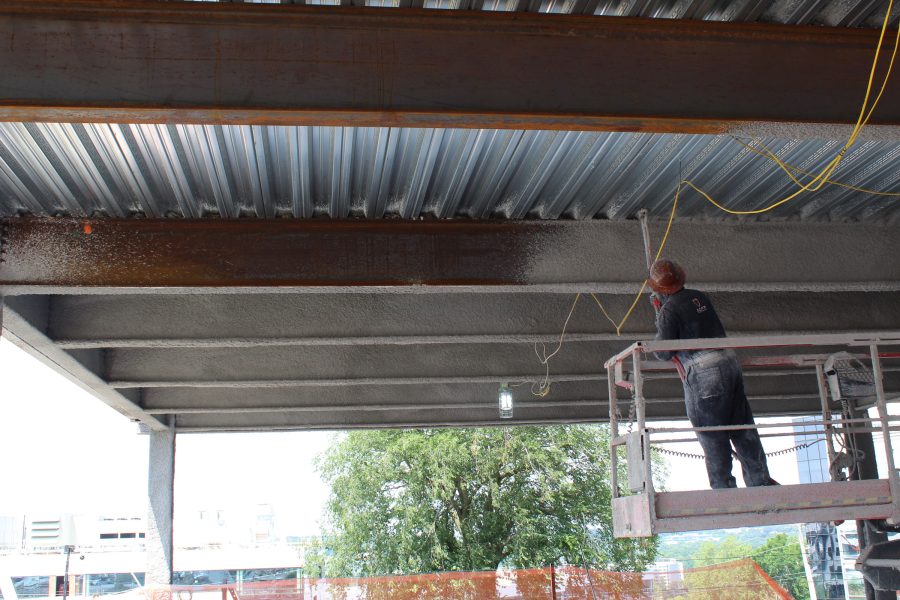
GCP’s MONOKOTE is designed to reduce the rate of temperature rise in steel or concrete in the event of a fire. Photo courtesy of GCP Applied Technologies
The fireproofing industry is ahead of the game, according to John Dalton, GCP’s fire protection technical service manager. “We have gone well beyond what most architects are requiring now in terms of environmental or sustainability attributes.”
GCP continues to look at new technologies to enhance the performance and sustainability characteristics of its solutions, including MONOKOTE® Fireproofing—a product that has been around in one form or another since 1938. “We have been at the forefront of that development for almost a century, and we are keen to be around for the next one,” Dalton says. “I am excited about what the next five to 10 years will bring in terms of our formulations and product characteristics.”
Solutions like MONOKOTE have about half the GWP compared to competitors’ products, with 70% of materials made from a hydro-powered plant. MONOKOTE also has third-party verified Environmental Product Declaration to back up its attributes.
MONOKOTE is designed to reduce the rate of temperature rise in steel or concrete in the event of a fire. This prolongs the structural integrity of the elements, which allows more people to leave a building in an emergency situation and gives first responders time to save the building. It’s been used in some of the world’s biggest projects—from the MGM City Center in Las Vegas to New York City’s Freedom Tower and Canary Wharf in London.
Contractor-friendly, MONOKOTE is typically spray-applied and can be pumped easily into the upper floors of tall buildings. It is less abrasive and less challenging to pump, so users can choose to inject it to reduce set time and increase yield of the material if they prefer.
Longevity Makes a Difference
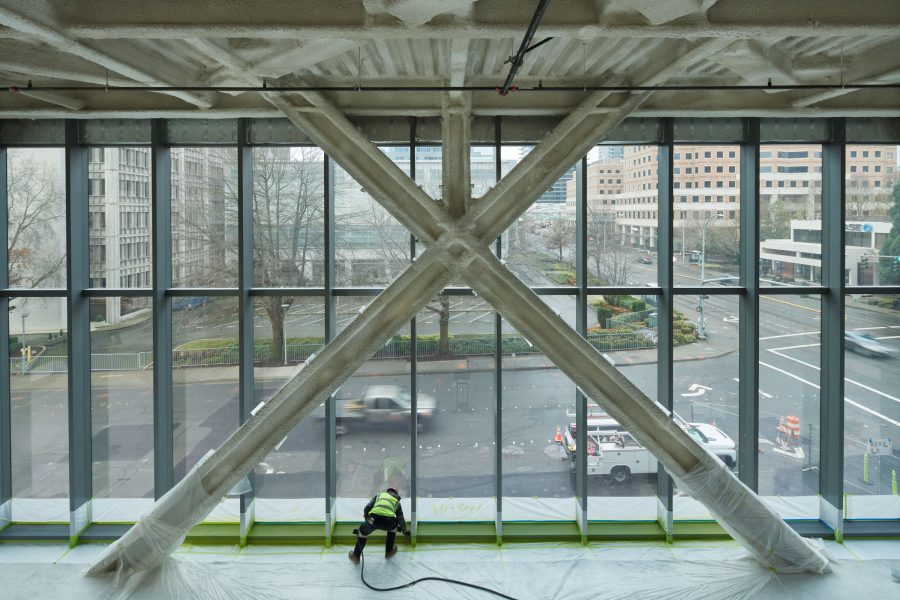
Photo courtesy of GCP Applied Technologies
“MONOKOTE Fireproofing is considered a cementitious product, and it has a long track record of being robust and that it will remain in place for the life cycle of the building,” Dalton says. “Cementitious fireproofing is mixed with water and pumped as a slurry, and there is a competing fiber-based dry-mix technology that has a reputation for being less robust, but it is inexpensive. We regularly get updates from contractors with photos of 50-year-old MONOKOTE in the same condition as it was in when it was first applied. A solution is only cheap if you don’t have to repair or replace it.”
He says MONOKOTE is like getting two for one—you pay for the durability, and the low GWP is a bonus. “We feel that is the case with the use of cementitious. Most architects and specifications now require it in lieu of the other technology. The other technology has an eye-wateringly high GWP, too—almost two times that of MONOKOTE.”
It’s big enough to make a measurable difference.
Still, he says the architectural industry has been slow in using sustainability as a selection metric for fireproofing, as it’s such a small part of a building’s embodied carbon. That said, the past five years have been promising, as more teams look to earn LEED points, considering any solutions that help to lower GWP add up. “The pending release of LEED V5 and its heavy focus on embodied carbon has sharpened people’s minds on this, and we expect it to be more of a ‘thing’ in the future,” Dalton says. “We have seen several recent specifications where GWP is a metric, used as you would with any other performance characteristic like bond strength or abrasion resistance. It has been heartening to see it being a deciding factor in several recent project awards in the Midwest.”
As understanding of materials evolves, the movement toward choosing building materials with low embodied carbon grows. “Fireproofing can be as much as 2% of the embodied carbon in a building. While not huge like, say, steel or concrete, it’s big enough to make a measurable difference—like the recycling of your single soda can. Certainly more than carpet,” Dalton says.
Evolution of Waterproofing
More sustainable waterproofing strategies are being adopted now than before, too, according to Iltaz Alam, senior building envelope product manager at GCP who oversees commercial waterproofing. GCP has always worked to develop durable, innovative products that are long-lasting and sustainable, Alam says.
Recently the company launched its latest Preprufe Liquid Flashing, which reduces the need for additional materials and multiple product logistics to complete a waterproof pre-applied penetration detailing. Based on a typical pipe penetration detail, it reduces up to 20% of global warming potential when compared to traditional detailing. “It’s durable, and it keeps groundwater away from the structure. That’s a big environmental plus right there,” Alam says.
This innovative product reduces installation time as well as the amount of material used to complete pre-applied detail, he says. “Previously you would need to use some kind of liquid membrane, some sheets, and some construction tape. Now GCP has come up with a material that avoids the need of all those additional materials like tape or other types of liquid membrane. It’s just liquid flashing.”
The user applies the liquid flashing, and it will bond to the concrete continuously, he says—the same way GCP’s current Preprufe membrane bonds.
Alam says the team is always pushing for more sustainable sources in its products, too. The more these types of solutions are available, the more accessible and affordable they will become, he says, while further reducing installation timeline and total carbon footprint.
Choices Add Up
Katz says areas like fireproofing and waterproofing can make a big difference on projects. He points to an above-grade wall with waterproofing as an example. “If that waterproofing product fails, there can be a cascade of other issues, which in turn affects the amount of operational carbon the project requires,” he says. “Or maybe the building doesn’t last as long, which leads to a hit on embodied carbon for replacement value. We really want to understand the nature of the waterproofing product as well as whether the source materials or production methods are heavy in embodied carbon.”
Katz says architects at Gensler look at the whole picture when considering a project’s sustainability, especially as the firm works to declare all of its work completely carbon neutral in 2030. “Are they produced far from the project site? Can the manufacturers report the reliable embodied carbon data? All those factors go into that selection process,” he says.
Can the manufacturers report the reliable embodied carbon data? All those factors go into that selection process.
When it comes to something like fireproofing a steel building, for example, he says that project typically has a spray-on cementitious-based fireproofing. “The Portland cement in that product has a big embodied carbon hit usually. How can we use as little as possible of that, and use it really efficiently, so it still meets a fire rating at a building? Ideally we’re able to specify a low carbon, cementitious fireproofing. We want to meet the code requirement but not use more than we need to.”
Dalton says GCP has been excited to explore this, too. “Where we see potential is the removal of Portland cement from our products. Portland cement is typically a pretty bad actor when it comes to embodied carbon. That has been a focus for us over the past several years. We’ve finally completed a series of tests with UL, and we have replaced the Portland cement with Portland Limestone Cement to allow us to significantly reduce the embodied carbon of our products.”
GCP is also looking at Alternative Cementitious Materials, or ACMs. “That has been a big focus for us from a sustainability point of view. That is where the industry is going, and we’re happy to be a part of it,” Dalton says.
More Solutions
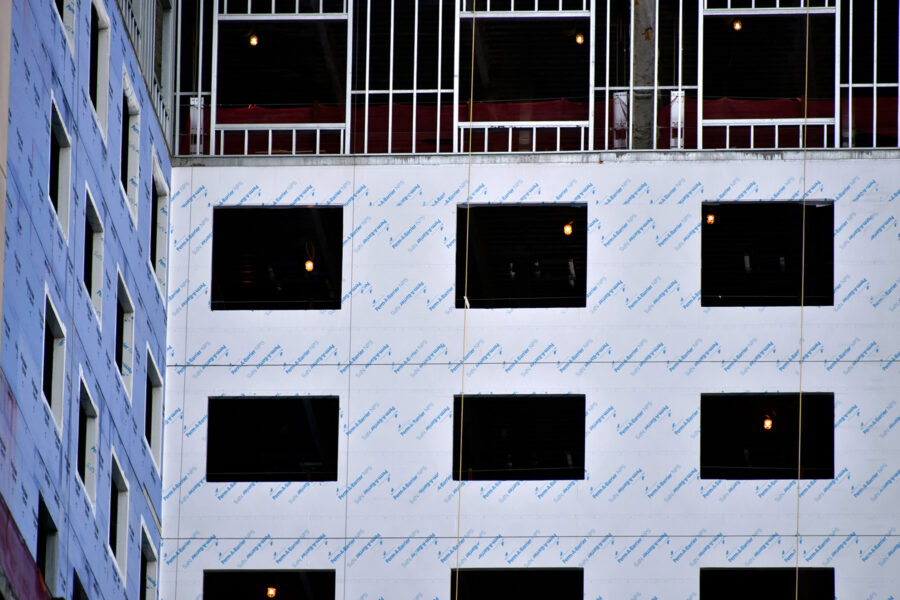
Photo courtesy of GCP
GCP’s latest PERM-A-BARRIER® ULTRA™ wall membrane and flashing is yet another innovation. Alam says the new impermeable sheet membrane pushes into the envelope to provide a more durable solution when it comes to very high temperatures—for example, a south-facing building in the southern part of the US. There a building’s wall cavity or parapet temperature can go up more than 170 or 180 degrees Fahrenheit with reflections from another building due to radiation and convection, he says.
“In those situations you need a flashing solution that is stable for a longer period of time, for the duration of the building in such demanding climatic conditions,” he says, adding that a flashing solution that is not durable could bleed through and impact the long-term durability of the tie-ins.
He says ULTRA is stable up to 300 degrees Fahrenheit. The same material can also be used on the roofing parapet. “With climate change we are seeing that every year average temperature is only increasing and not decreasing. For example, Texas this year is facing the warmest weather in a long time. Climate change is happening, and we need to be prepared and think about how the building materials we are innovating are suitable for the future.”
GCP also recently acquired International Cellulose, with more low carbon, high- performance products in the area of insulation that are designed to last the life of a building. Solutions like K-13 Thermal Insulation can help in terms of light reflectance, too, as well as improve acoustical performance and overall sustainability of a project.
Many more innovations are likely on the way. “We have to be willing to push the envelope and offer better solutions,” Dalton says. As manufacturers it’s our responsibility, he says—both to innovate but also to use less raw materials. Then the industry will be forced to follow suit.
Specification is key, Alam says. “Once architects make the decision to use more sustainable products, everyone will be encouraged to contribute and innovate because no one will want to be left behind.”