Story at a glance:
- Metal composite material (MCM) is typically made of 70% recycled content.
- Coatings for MCM can come in a variety of finishes and textures.
- MCM is more lightweight than sheet metal and still offers durability.
Contemporary buildings in cities across the globe utilize metal composite material (MCM). The use of metal composite panels around the world has contributed to the market size increasing. The global metal composite panel market size is projected to reach $7233.8 million by 2026.
MCM was originally known as aluminum composite material or ACM and was introduced in 1969. MCM is manufactured by bonding thin metal skins to both sides of a lightweight thermoplastic core. This core material can be either polyethylene or a proprietary mineral-filled, fire-resistant material.
A variety of metals can be used to create MCM—including aluminum, copper, stainless steel, zinc, and titanium. When installed, these corrosion-resistant panels are visually indistinguishable from solid sheets of the same metals. Copper and zinc develop a natural patina over time, while stainless steel and titanium maintain their appearance.
To protect the MCM skin, the panel is finished with a primer system on both sides and a color coat on the outward-facing side. Some finishes also have an additional clear coat to enhance and preserve a special effect, like a metallic or prismatic look.
As the demand for MCM panels continues to grow, it’s important to understand the benefits this versatile material has to offer. Below are just a few reasons MCM has become such a popular sustainable building material.
1. It’s sustainable.
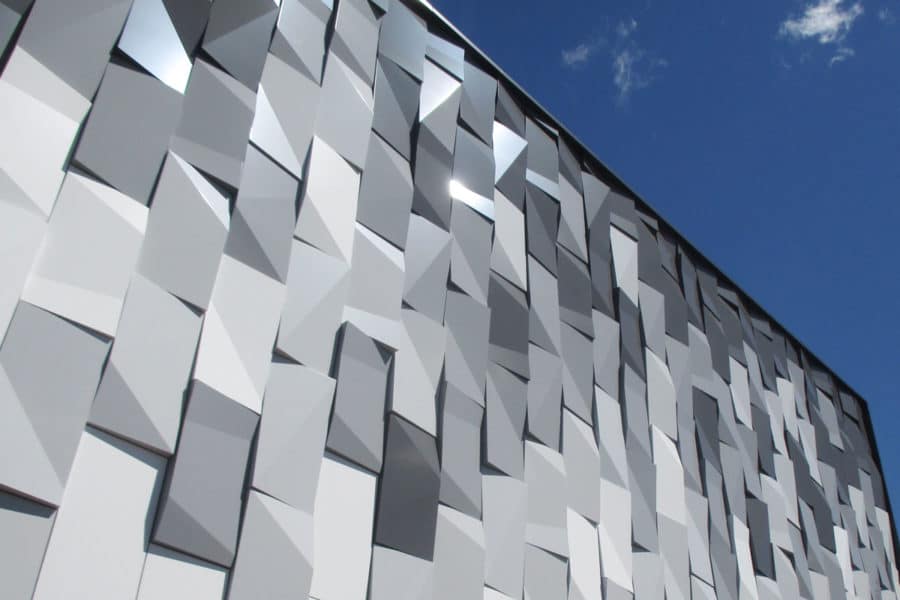
Photo courtesy of ALPOLIC
One of the best benefits of MCM is how sustainable it is. For example, approximately 70% of MCM by weight is made of recycled content.
The high recycled content of ALPOLIC MCM can support LEED projects looking to qualify for an innovation credit. The coatings and paints for MCM also contribute to its sustainability. Most architectural stock colors also earn a “cool” rating from the Cool Roof Rating Council by reflecting heat instead of absorbing radiant energy, reducing energy usage.
MCM manufacturers like ALPOLIC keep sustainability at the forefront of their processes. ALPOLIC uses a factory-applied, die-coated paint system that virtually eliminates harmful VOCs before they enter the atmosphere. Precision die-coating also creates less paint waste and promotes sustainable manufacturing.
“At ALPOLIC we’re committed to transparency in the manufacturing industry, supporting the adoption of Environmental Product Declarations and being the first in the industry to promote Product Transparency Declarations. Manufactured in our American headquarters in Chesapeake, Virginia, we actively strive each day to reduce our energy consumption and environmental impact,” wrote Michael Bowie, technical support specialist at ALPOLIC, in a previous contribution for gb&d.
ALPOLIC also offers an Operation Encore Program, which encourages new and innovative uses for expired MCM. Components accepted through this recycling program are distributed to their appropriate industry recycling streams and can be used in a variety of projects.
2. It’s affordable.
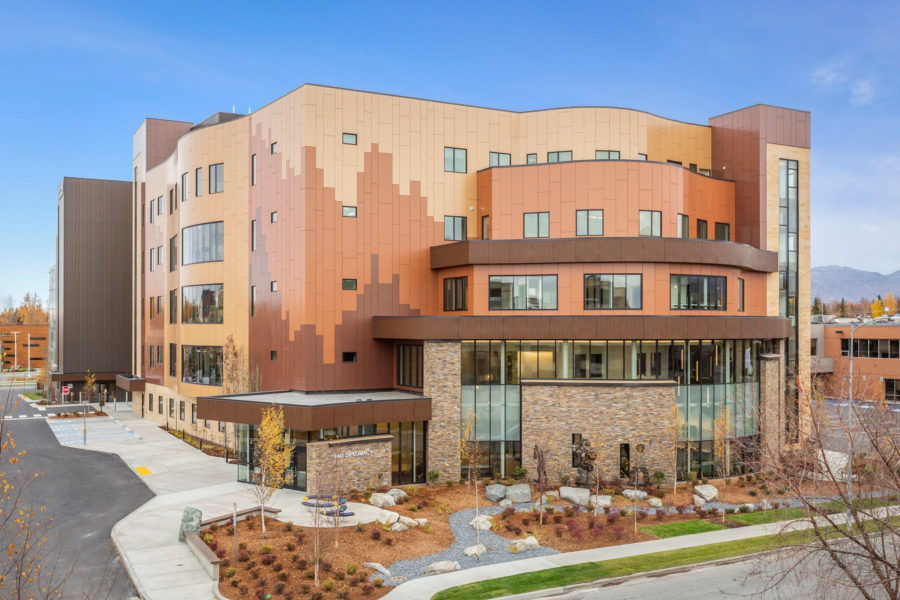
The Alaska Native Medical Center features 10,000 square feet of three custom colors in ALPOLIC MCM. Photo courtesy of ALPOLIC
Initial construction costs are often lower with MCM systems because panels can typically be installed faster than alternative exterior products like precast, granite, or brick, according to the Metal Construction Association. The lightweight MCM systems can save money by reducing structural steel requirements as less structural support is needed.
Ongoing maintenance costs are also reduced because of continuing improvements in paint finishes for MCM. Since MCM panel systems retain their color and finish over time, there is often a reduction in the need for refurbishing costs.
The manufacturing and installation process of MCM also contributes to its affordability. “In as little as 1,000 square feet, affordable MCM can be produced to custom order with manageable lead times, but sometimes faster is better. With more than 100 finishes in stock, these premium materials are ready to deliver exceptional results,” Bowie says.
3. It’s durable.
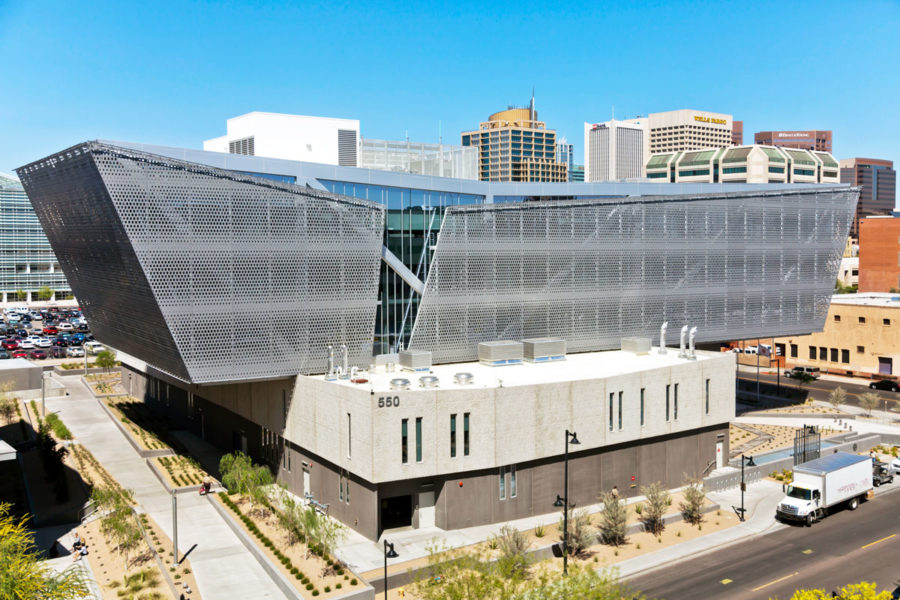
Photo courtesy of ALPOLIC
MCM is a material known for its durability. MCM panels retain their color and finish for decades, ensuring buildings maintain their aesthetic and property value for the long term.
MCM’s durability can also withstand extreme weather. “The superior fabrication capabilities of MCM enable architectural possibilities ranging from advanced rainscreens designed to withstand hurricane force-winds to incredible angled, radiused, and even origami-like forms that would be prohibitively expensive or outright impossible to create using other materials,” Bowie says.
The paint systems for MCM contribute to the material durability by being easy to clean without the need for harsh chemicals. MCM coatings are typically warranted not to fade, crack, or peel for 10, 20, or 30 years.
4. It can have a range of finishes.
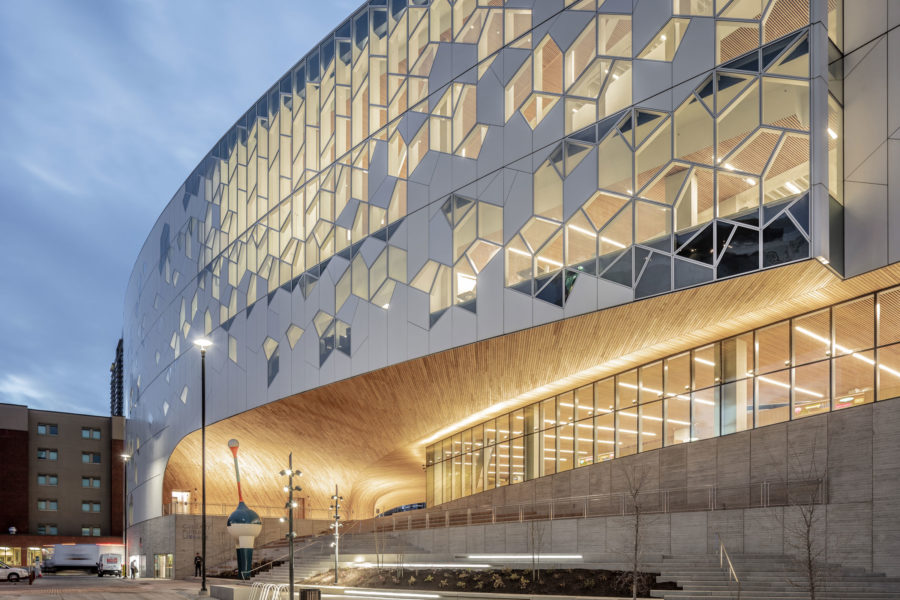
Calgary Library. This 240,000-square-foot green engineering marvel was designed by architectural firms Snøhetta and Dialogue to showcase local western cedar and inspire with geometric patterns created by ALPOLIC MCM. Photo courtesy of MCA-ALPOLIC Division
There are two main categories of paint used to coat MCM: thermoset and thermoplastic.
Thermosets, like polyester and FEVE paints, have clear resin bases allowing for a broad range of colors and glosses. Thermoset paints, once cured, are not susceptible to pressure mottling. FEVE paints ensure exceptional color accuracy and provide the widest gloss ranges in the industry.
Thermoplastics, like the fluoropolymer PVDF paints, are a dispersion of 70% PVDF and 30% clear resin. Thermoplastics allow for the paint to soften with exposure to heat or pressure.
“Fluoropolymer paints are inherently resistant to post-paint applications. They do not readily accept applications such as ink printing. This is also what makes these paint systems somewhat graffiti resistant,” wrote Jack Finn, specialty sales manager for ALPOLIC, in a previous contribution for gb&d. “In contrast, most polyester paints can be printed upon, including with UV inkjet. When considering what the final application is, interior or exterior, printed or not, the paint type chosen can be an indicator of the success expected.”
Coatings for MCM can come in solids, micas, metallics, prismatics, decorative metals, shimmer effects, and even realistic stone or timber patterns. It’s even possible to provide a multi-color finish on a single panel.
“The finish possibilities of MCM have revolutionized the look of today’s most eye-catching buildings. Gloss ranges from 6 to 70 allow for understated matte and the most opulent high gloss in shades across the spectrum,” Bowie says. “MCM can shimmer with special effects and prismatic finishes can even change appearance depending on the viewing angle. Printed patterns create the look of marble and timber without the cost, weight, or maintenance.”
5. It can form a variety of shapes.
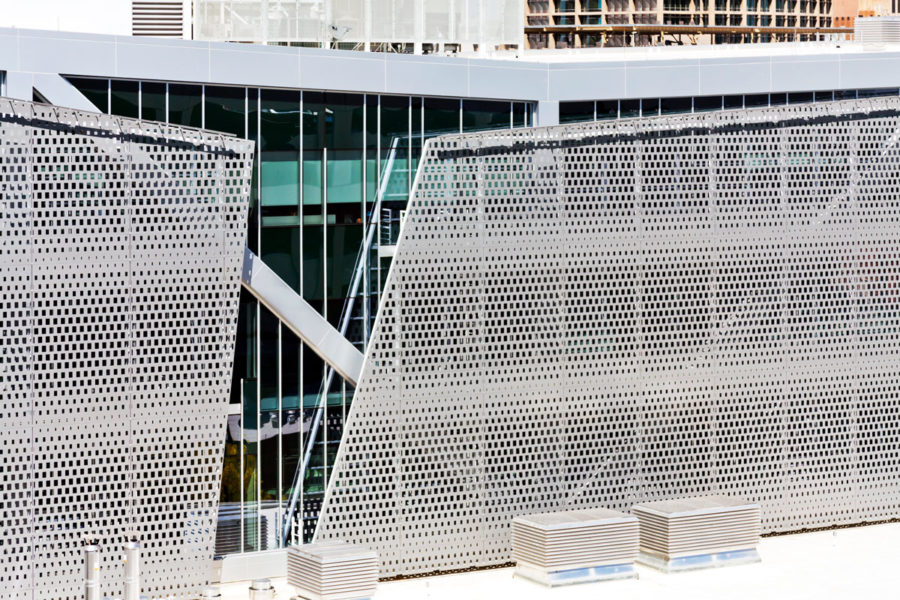
Photo courtesy of ALPOLIC
“MCM can be used to create a practically unlimited world of complex forms and shapes. These composite materials are far more versatile and easier to fabricate than solid sheet plate metal. Cutting, grooving, punching, drilling, bending, rolling, and many other fabrication techniques are easy to perform using ordinary woodworking or metalworking tools—with no special tools required,” Bowie says.
Reputable MCM manufacturers like ALPOLIC produce sheets that are trimmed, squared, and offer a protective film that performs double duty—protecting the finish and providing directional arrows for installation assistance. MCM materials can be flipped to order and delivered with the finish side facing up or down as requested.
Thanks to MCM’s light weight, it doesn’t distort the same way traditional sheet metal might. The thermoplastic core makes MCM far lighter than sheet metal, with no loss in rigidity. This makes MCM easier to install with superior flatness and vibration damping.