Story at a glance:
- An efficient thermal insulation material can aid in lowering energy bills as well as have a positive effect on the environment.
- The thermal resistance, or R-value, of thermal insulation materials varies depending on the physical property.
- The effectiveness of thermal insulation materials depends on climate compatibility.
With the effects of climate change becoming more evident, extreme temperature conditions are more common. Many cities around the world are experiencing variations in weather patterns that they aren’t accustomed to, which has manifested itself in the degradation of infrastructure, like energy demands that can cripple power grids. Many homeowners are feeling the burden, struggling to maintain comfortable home temperatures as high oil prices inflate energy bills.
Whether installing radiant barriers or putting in a few cool walls, homeowners can take many avenues to make their homes more energy-efficient, but insulation is important. Thermal insulation is responsible for making the internal temperature of a building stable, and finding an efficient material can help to reduce the energy required for heating/cooling the house, conversely creating lower energy bills. This can also have a positive effect on the environment by reducing the burning of fuel in power plants, which will reduce the emission of greenhouse gasses.
Thermal insulation plays a key role in making a home more energy-efficient, but finding the right material can be tricky. From bulky blankets of fiberglass to futuristic aerogels, there’s a myriad of options to choose from. Here is our guide to understanding the differences between thermal insulation materials.
Fiberglass
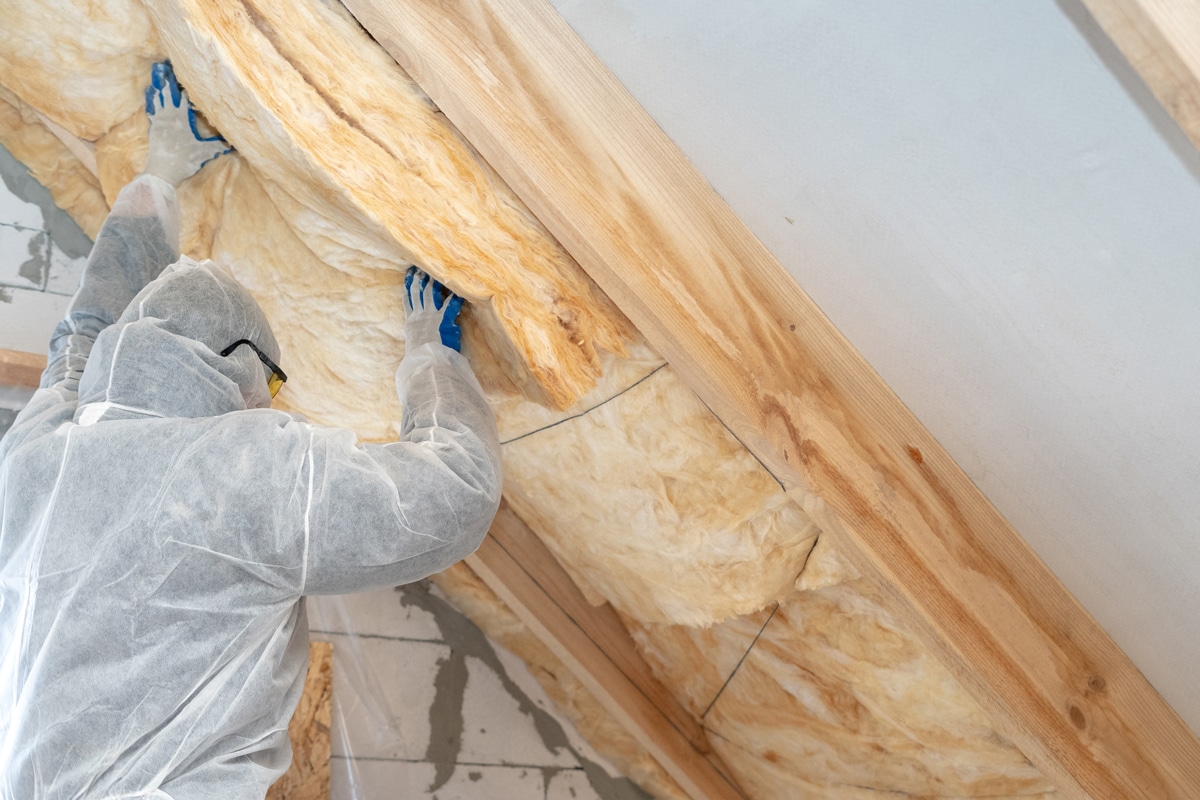
Usually dulled out in batts installed in pieces or rolls, fiberglass remains one of the most common forms of insulation. Photo by Brizmaker
Made up of molten glass and spun into fibers, fiberglass remains one of the most common forms of insulation due to its adaptability, affordability, and effectiveness. Usually dulled out in batts that are installed in pieces or rolls that are rolled out, fiberglass can also come in a loose-fill form blown out using a machine as well as rigid boards and rolls for ducts. Fiberglass thermal insulation is both fire- and moisture-resistant, and much of the material is recyclable.
Due to its commonality, the mass production of fiberglass has made it one of the cheaper options for thermal insulation material, and its adaptive properties make it ideal for DIY projects. The thermal resistance, or R-value, of fiberglass ranges around 2.2 to 2.7 per inch of thickness, but comparatively speaking that’s low when stacked to other available options. Over time that value can decrease due to sagging or settling.
Fiberglass insulation is the most ubiquitous option out there when it comes to thermal insulation, but that doesn’t mean it’s the best for every project.
Pros of Fiberglass
- Affordable. Fiberglass insulation is by far the most affordable type of insulation, regardless of whether it is bought in batt, board, or blown form.
- Fire-retardant. Because it is constructed primarily from glass and sand (i.e. inorganic materials), fiberglass insulation will not burn when exposed to fire, though it can melt if subjected to extremely high temperatures; this means fiberglass insulation can help reduce the speed at which a fire spreads.
- Recyclable. Fiberglass is considered to be a relatively eco-friendly insulation material thanks to its inherent recyclability and reuse of recycled content—indeed, most fiberglass insulation contains approximately 30% recycled material.
Cons of Fiberglass
- Can be dangerous to handle. Fiberglass insulation is made up of tiny glass fibers and can cause skin irritation if handled without gloves and respiratory problems when installed without wearing a respirator or mask.
- May attract pests. The relative softness and warmth of fiberglass insulation can attract pests, especially those of the rodent variety, who may decide to nest within the insulation itself or carry off bits of it to line their nests.
- Energy-intensive production. The production of fiberglass insulation is an extremely energy-intensive process that involves the melting of siliceous minerals and other materials in high-heat furnaces, of which emit large amounts of CO2.
Sheep’s Wool
While not particularly common, sheep’s wool insulation has become an attractive alternative to conventional insulation in recent years thanks to its inherent thermal properties and eco-friendly status. Sheep’s wool insulation possesses a typical R-value between 3.5 and 3.8 per inch, putting it on the level with cellulose, mineral wool, and even certain polyurethane insulations.
As a material wool is considered to be extremely sustainable due to the fact that sheep naturally produce it throughout their lives. Carbon also makes up a significant amount of wool’s molecular structure (50%) due to the grasses and plants eaten by sheep.
In addition to being an excellent thermal insulator, wool also helps reduce noise transfer—in fact, wool is a natural sound absorber capable of reducing noise by as much as 50%, allowing for a much quieter and comfortable indoor environment.
Pros of Sheep’s Wool
- Fire-resistant. In the event of a fire, sheep’s wool will not help fuel the blaze—rather, wool only chars when exposed to flames, as there isn’t enough oxygen in the air to support full combustion.
- Humidity-resistant. Rather than absorbing ambient moisture caused by humidity, wool actually adsorbs moisture, meaning it traps and stores water molecules inside of its porous fibers before allowing them to evaporate into the air.
- Improves air quality. Wool absorbs VOCs from the air and stores them in its core, where it then breaks them down at the molecular level; scientific research suggests that wool is capable of purifying indoor air in this manner for up to 30 years.
Cons of Sheep’s Wool
- Expensive. Wool typically costs more than other insulation materials, thereby increasing a project’s overall construction expenses.
- Susceptible to insect damage. As anyone with an old wool sweater knows, wool is often targeted by moths, silverfish, carpet beetles and other insects, reducing the product’s longevity.
- Chemical treatments. In order for wool insulation to be protected from insects, it must be treated first; unfortunately, most treatments contain unwanted chemicals like borax that have been linked to certain reproductive issues.
Mineral Wool
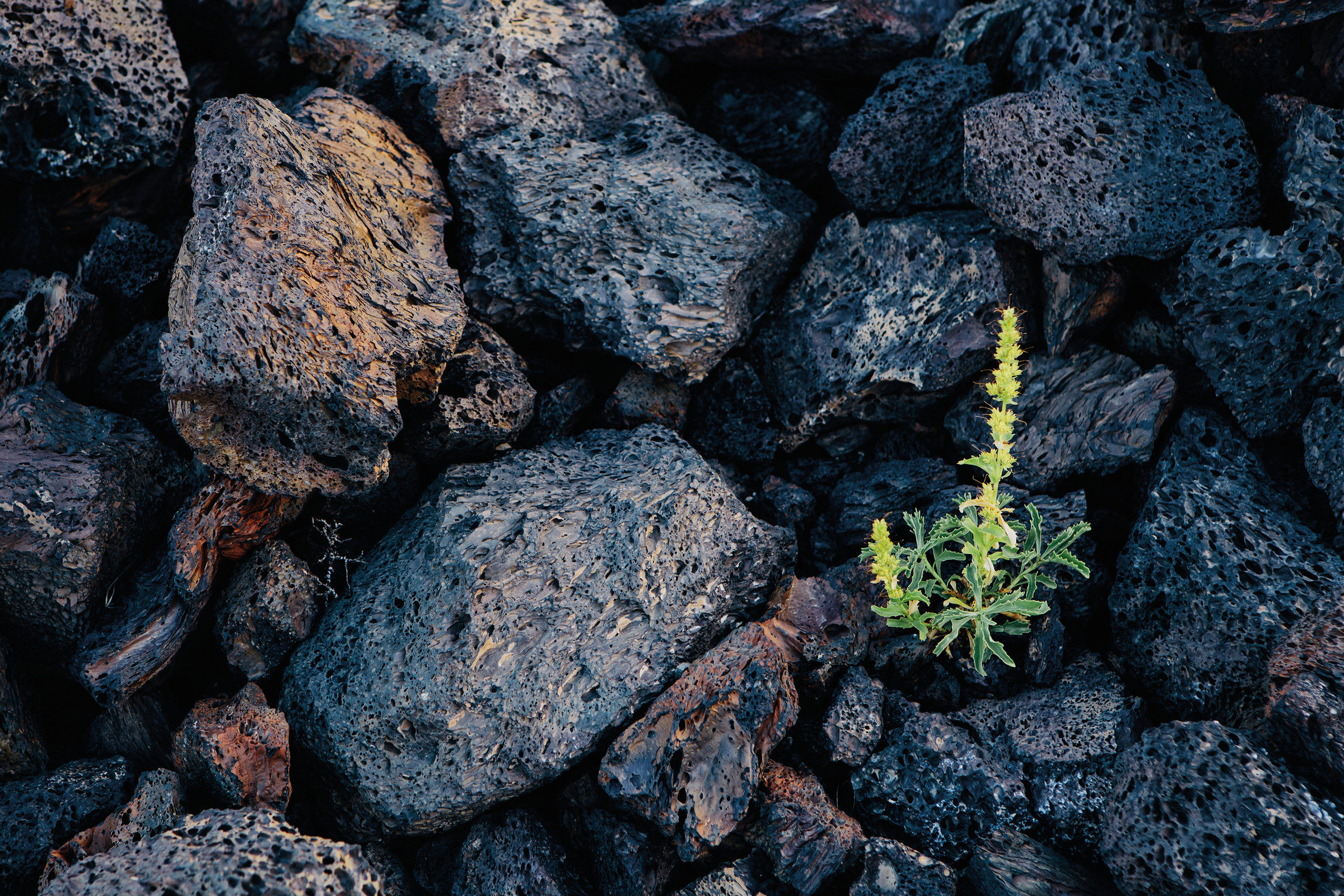
ROCKWOOL transforms volcanic rock into quality stone wool insulation that’s both performance tested and ranked high in use among the residential construction market. Photo courtesy of Rockwool
Composed of rock or slag, mineral wool consists of mostly post-industrial recycled content. Much like fiberglass, mineral wool thermal insulation can come in many forms, from roll and batts to loose-fill, but its R-value sits around 3.0 to 3.3 per inch of thickness. The thermal performance of mineral wool holds up over time, and its high heat manufacturing process strips it of organic matter—making it a poor medium for moisture and mold.
Mineral wool’s natural components make it extremely durable and a great choice when considering longevity, but it is more costly on the front end. That extensive, high-heat manufacturing process increases the price and uses a lot of energy, but once installed that energy is recuperated within five months. Mineral wool is also heavy, which can make it less ideal for some projects, but its materials are recyclable and inherently non-combustible, adding to the fire resistance of a building.
While not as ubiquitous as fiberglass, a lot of great options for mineral wool exist on the market, including ROCKWOOL, which transforms volcanic rock into quality stone wool insulation that’s both performance tested and ranked high in use among the residential construction market.
“We tend toward ROCKWOOL on all of our projects,” Chris Laumer-Giddens, vice president of the architecture and construction firm LG Squared, told gb&d in a previous article. “They’re making it more accessible to the residential construction market, which is where we spend most of our time. I’ve tried the other stuff, and it just doesn’t have the same performance and usability.”
Pros of Mineral Wool
- Moisture-resistant. Mineral wool insulation is naturally moisture-resistant and is capable of retaining its insulative properties even when wet.
- Non-combustible. One of the major advantages of mineral wool insulation is its inherent non-combustibility—the material will not burn until temperatures reach over 1,800℉; this makes mineral wool insulation an ideal choice in regions where wildfires are common, as it can help reduce the spread of fires from building to building.
- Sound dampening. Because it is so much denser than other forms of insulation, mineral wool also serves as an acoustic dampener, reducing the transfer of noise into or out of a building.
Cons of Mineral Wool
- Heavy. Mineral wool is much denser than most other types of insulation, meaning it is heavier and can be difficult to work with.
- Can be harmful. Similar to fiberglass insulation, mineral wool can irritate the skin and cause respiratory issues if it is not handled properly.
- Cost. Mineral wool insulation comes with higher per-square-foot costs than most other types of insulation, making it one of the more expensive options in terms of up-front expenses.
Cellulose
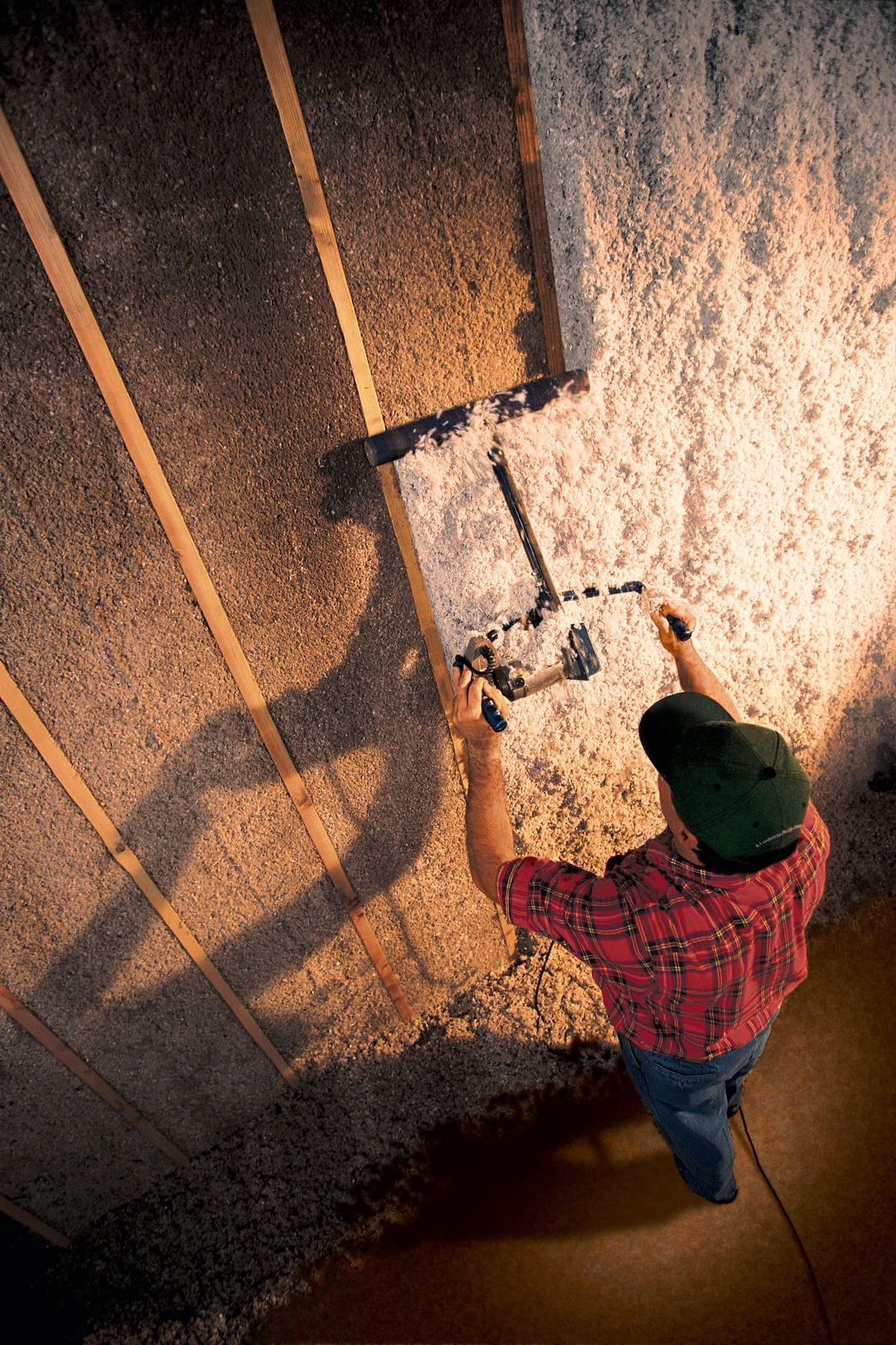
Greenfiber’s wall insulation starts as a plant material, is made into paper, and reused as insulation. Photo courtesy of Greenfiber
Cellulose thermal insulation material is growing in popularity due to its highly sustainable nature. Made from primarily recycled paper products reduced to small pieces and fiberized, cellulose typically comes as either loose-fill or dense packed. It has a typical R-value of 3.2 to 3.8 per inch thickness, and its manufacturing process makes it more affordable. Although naturally more flammable, cellulose can be treated with chemicals like boric acid to increase its fire resistance, also making it less desirable to pests and mold.
As a whole cellulose insulation is considered to be one of the most sustainable options on the market, and companies like Greenfiber have embraced that concept, taking steps to help the environment by using less energy consumption in the manufacturing process.
“Greenfiber uses a low-energy manufacturing process that results in materials with the least-embodied energy of most major insulation products. The production process generates little no waste or byproducts because we leverage recovered material to start with,” Jason Todd, director of market development and building science at Greenfiber, previous told gb&d.
Pros of Cellulose
- Sustainable. Most cellulose insulation is produced using recovered and recycled natural materials, making it a very sustainable option that will biodegrade over time once it reaches the end of its operational lifespan.
- Easy to install. While it can be a bit messy, installing cellulose insulation is a relatively simple and straightforward process that is DIY friendly, provided one has access to a blower machine.
- Affordable. While it is often more expensive than fiberglass (especially in terms of installation), cellulose is typically one of the more affordable options when it comes to insulation; this is largely thanks to the fact that cellulose insulation uses recycled and easily-accessible materials.
Cons of Cellulose
- Susceptible to moisture. Because it is made from organic paper products, cellulose insulation is susceptible to moisture damage if it does not receive adequate ventilation, making it a poor option in regions with high humidity; the installation of a vapor barrier can help reduce the chances of moisture infiltration, but does not completely eliminate the possibility.
- Can be dusty. While not true of wet-blown cellulose, the installation of dry-blown cellulose insulation can be extremely dusty and requires a certified breathing mask to avoid inhalation.
- Loses R-value over time. After it is installed cellulose insulation has a tendency to sag and settle over time as well as compact any pre-existing insulation already in place, which in turn reduces its R-value and overall insulative ability.
Polystyrene
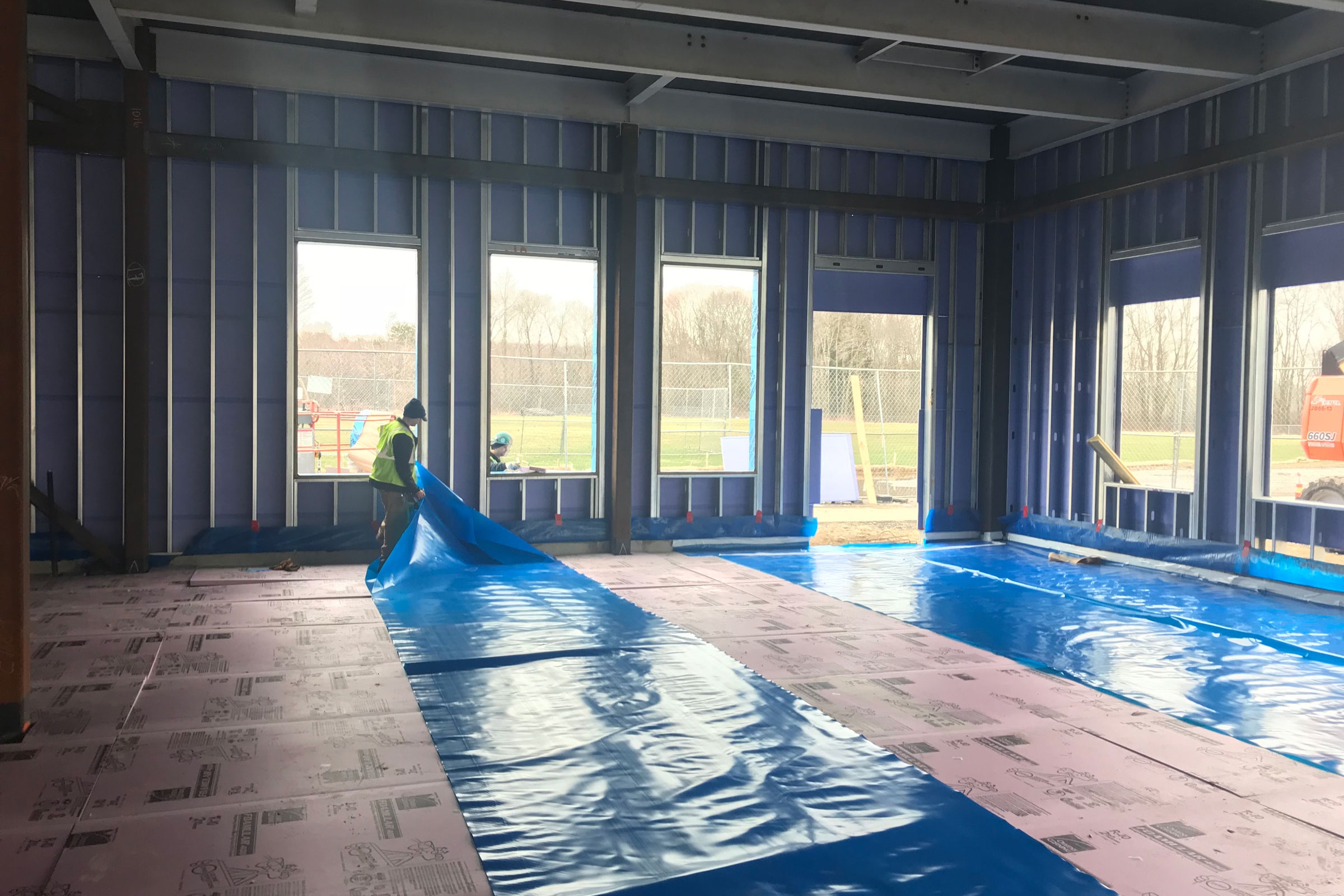
Polystyrene boards are lightweight and water-resistant, and their low water absorption helps to prevent mold. Photo courtesy of ISI Building Products
Polystyrene is a versatile polymer made up of colorless, transparent thermoplastic. There are two common varieties of polystyrene insulation—extruded and expanded—of which have slightly different manufacturing processes and subsequent characteristics.
In the case of expanded polystyrene (EPS) insulation, blowing agents, steam, and molds are used to expand the polystyrene into the desired form. EPS is the lighter of the two, is thicker, and typically possesses an R-value of around 4.0 per inch of thickness. EPS is extremely versatile and may be used in above-grade construction to insulate floors, walls, roofs, and HVAC systems.
Extruded polystyrene (XPS) insulation, on the other hand, is manufactured using blowing agents, heat, and a specialized extruding machine. XPS has an average R-value of around 5.0 per inch and has a higher water vapor diffusion resistance than EPS insulation, meaning it is not as permeable to air or water. This higher resistance to moisture infiltration makes XPS insulation especially ideal for basements, foundations, and other below-grade applications.
Both types of polystyrene foam boards can be brittle, however, and their upfront costs are more than fiberglass, making them riskier. Their chemical makeup isn’t biodegradable and can create toxins when burning, but their high R-value and sound dampening properties makes polystyrene an attractive option.
Pros of Polystyrene
- Versatile. The chemical composition and molecular structure of polystyrene insulation allows it to be shaped and molded into various forms, making it an extremely versatile option with a range of applications.
- Lightweight. Both varieties of polystyrene insulation are lighter than many other types of insulation, making them easier to handle, transport, and install, which in turn helps reduce project costs.
- Water-resistant. Polystyrene is a water-resistant material that retains its insulative properties even when exposed to water and moisture; this makes polystyrene insulation incredibly resilient to mold and mildew growth.
Cons of Polystyrene
- Potential health risks. When it is exposed to sunlight or high heat—such as from a fire—polystyrene insulation can release styrene, a toxic chemical that is known to cause irritation, headaches, hearing loss, and even certain cancers.
- Energy-intensive production. The production and manufacturing of polystyrene is extremely energy-intensive and releases a significant amount of CO2 into the atmosphere.
- Limited service temperature. Like any building material, polystyrene insulation will become malleable and melt at a certain temperature, with both EPS and XPS possessing a service temperature of 165℉—a temperature most building envelopes exceed during the hottest summer months.
Polyurethane Foam
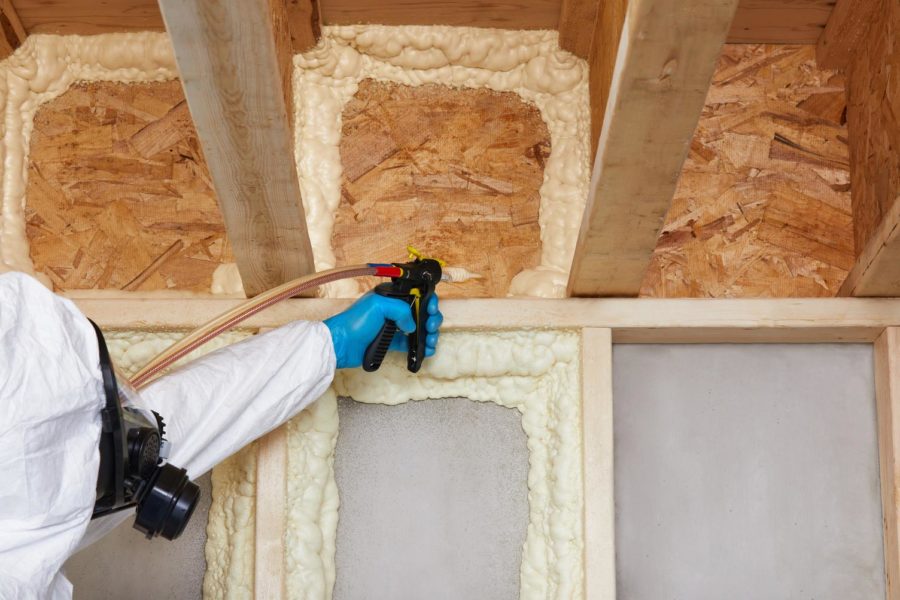
Froth-Pak is an all-in-one kit for contractors to quickly and efficiently seal out moisture, dust, and allergens and improve energy efficiency, building resilience, and comfort. Photo courtesy of DuPont
Polyurethane foam, more commonly marketed as spray foam, is an insulation material that contains low-conductivity gas in its cells. Spray foam comes in two types, open-cell and closed-cell, and the R-value depends on what kind is used. Closed-cell spray foam typically has an R-value around 6 to 7 per inch of thickness. It works well in climates with high humidity due to its tendency to expand and solidify, making it impermeable to moisture. DuPont offers an array of insulating foams through their Great Stuff product line, one of which is their closed-cell polyurethane spray foam, Froth-Pak.
“Froth-Pak is an all-in-one, self-contained, easily portable kit for our professional contractors to quickly and efficiently fill larger gaps and penetrations to seal out moisture, dust, and allergens while improving energy efficiency, building resilience, and comfort for homeowners,” Amy Radka, DuPont’s retail marketing director, previously told gb&d.
Open-cell spray foam, on the other hand, is less dense, and the air-filled cells give the material a spongier texture. Open-cell spray foam has a typical R-value of 3.6 to 3.9, and it’s not as moisture-resistant as closed-cell, but it is the cheaper of the two options with a greater expansion rate.
Regardless of the form, polyurethane spray foam is considered to be relatively eco-friendly, as it is one of the most energy-efficient insulation materials on the market with its high R-values and penance for longevity. Over time production of polyurethane foams has been refined to decrease the amount of damage that it once had on the environment, and while the verdict is still out on its potential health risks, polyurethane spray foam continues to grow as a popular option for energy-efficient renovations.
Pros of Polyurethane Foam
- Expands. Polyurethane foam expands once it is applied, a quality that allows it to completely fill the cavity it is sprayed into, thereby creating an extremely airtight seal.
- Easy to install. Polyurethane foam insulation is incredibly easy to install and cures very quickly, reducing the total installation time and costs.
- Waterproof. While not true of open-cell polyurethane foam, closed-cell polyurethane foam insulation is highly resistant to water absorption and infiltration, reducing the likelihood of moisture damage.
Cons of Polyurethane Foam
- Flammable. While most organic materials are considered flammable, polyurethane foam insulation will, upon ignition, burn rapidly and produce an intense heat, thick smoke, and potentially toxic gasses including carbon monoxide, carbon dioxide, benzene, and others; the flammability of polyurethane foam can be reduced in part through the addition of fire retardants.
- Hazardous. When polyurethane foam insulation is applied it releases toxic chemical vapors into the air that can cause skin, eye, and respiratory system irritation; polyurethane insulation also continues to off-gas VOCs into the air over time, which can lead to future health problems.
Polyisocyanurate Foam
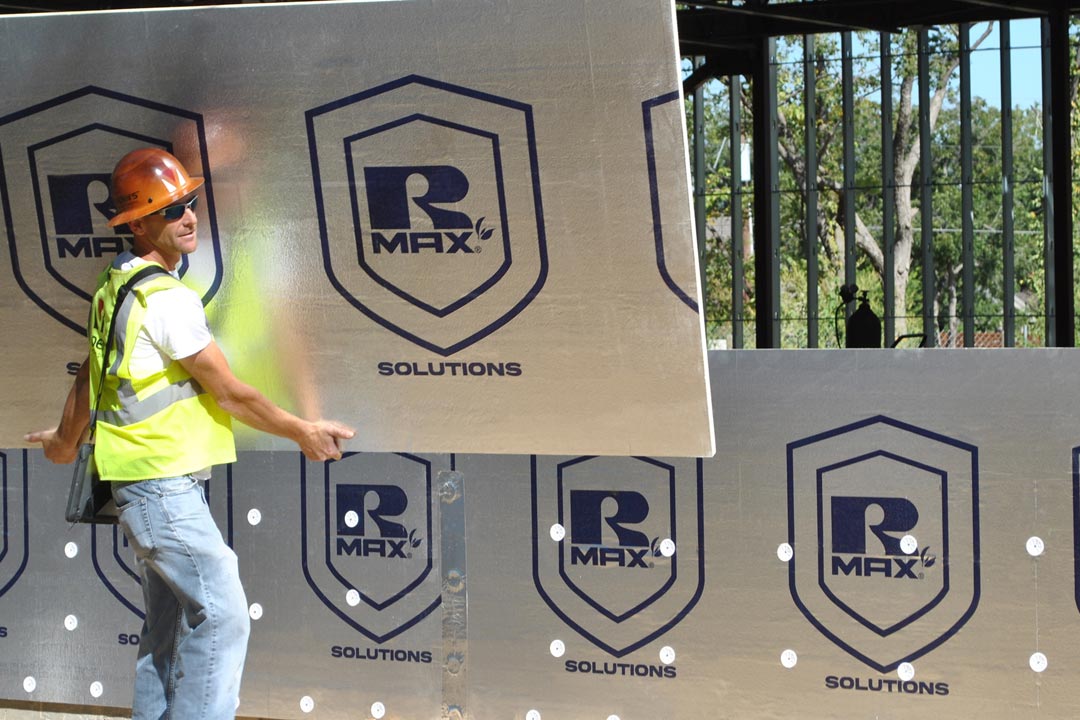
Foil-faced polyiso can act as a building’s air and water resistive barrier while meeting NFPA 285 fire codes, enabling the elimination of exterior gypsum and other air barriers. Photo courtesy of Rmax
Polyisocyanurate foam—also referred to as PIR or polyiso—is a kind of thermoset plastic insulation produced as a closed-cell, rigid, continuous foam board. Most polyiso foam boards feature a facer on one or both sides, with water-resistant foil facers being the most common. Like closed-cell polyurethane foam, PIR has one of the highest R-values on the market and averages between 6 and 6.5 per inch, making it an attractive option for projects targeting high-efficiency standards.
“With an R-value of 6.5 per inch, polyiso’s thermal properties surpass other rigid foam plastics by 20 to 70%, making it a clear choice for continuous insulation—a must for any sustainable project, given that HVAC costs often make up the vast majority of a building’s energy bill,” Greg Fantin, vice president of marketing at Rmax, previously wrote for gb&d.
Rmax is one of North America’s leading providers of polyiso insulation solutions and offers a range of products for both above- and below-grade applications.
Pros of Polyisocyanurate Foam
- Water resistance. Polyiso foam is naturally water resistant and has a low water absorption rate thanks to its closed-cell structure; the moisture-resistance of polyiso insulation can be improved further through the addition of water resistant facers.
- Compressive strength. Polyisocyanurate’s high density affords it a high compressive strength relative to that of other rigid foam board insulations, allowing it be used without issue in a variety of below-grade applications.
- Fire resistance. Because it is classified as a thermoset material, polyiso foam insulation will not melt or drip when exposed to fire but will rather char and retain its overall shape, ultimately helping to slow the spread of flames.
Cons of Polyisocyanurate Foam
- Cost. On average polyisocyanurate foam insulation costs more per unit of R-value than closed-cell polyurethane foams, despite possessing the same insulative capabilities.
- May lose R-value in cold weather. Like fiberglass, some polyisocyanurate insulations actually lose R-value when temperatures drop below 50°F, making them ill-suited for projects in colder climes; this can, however, be mitigated in part by changing the type of blowing agents used during manufacturing.
- Fire toxicity. In the event of a fire, polyisocyanurate foam can produce large quantities of toxic effluents like hydrogen cyanide, especially when fire conditions change from well-ventilated to under-ventilated; the fire toxicity of polyiso is rivaled only by that of polyurethane foams.
Cementitious Foam
Cementitious foam insulation is a type of non-expanding thermal insulation made primarily from magnesium oxide extracted from seawater, supplemented by a marginal amount of water, ceramic talc, and a foaming agent. It is similar to closed-cell polyurethane spray foam in that it becomes rigid and solid after being sprayed into an enclosed space, but unlike many polyurethane foams, cementitious foam insulation is completely nontoxic and does not off-gas VOCs as it cures or after it has dried.
Cementitious foam insulation has a typical R-value of 3.9 per inch of thickness, putting it on par with polystyrene and open-cell polyurethane insulation. Because of its overall composition and the fact that it does not contain any organic materials, cementitious foam is nonflammable and can help projects exceed fire protection requirements.
In addition to being non-combustible, cementitious foams are also moisture- and mold-resistant, making them an excellent insulation choice in regions that regularly experience high humidity and precipitation.
Pros of Cementitious Foam
- Lightweight. Contrary to what one might expect from the name, cementitious foam insulation is actually very lightweight and may be crumbled away if necessary to expose pipes or wires.
- Pest resistant. Once installed cementitious foam insulation is both insect- and rodent-resistant.
- Recyclable. Cementitious foam insulation can be recycled once it has reached the end of its operational lifespan, reducing a project’s overall contribution to landfill waste and resource extraction.
Cons of Cementitious Foam
- Lack of availability. Despite having been around for several decades, cementitious foam insulation isn’t as readily available as other varieties of foam insulation, meaning it can be difficult to source.
- Cost. Despite possessing a lower R-value than closed-cell polyurethane foam insulation, cementitious foam insulation is approximately 20% more expensive; costs can also increase due to the aforementioned lack of availability.
- Curing time. Due to its chemical composition, cementitious foam insulation has a longer cure time than most organic foams; and because cementitious foam is water-based and off-gasses water vapor as it dries, it requires ventilation and sometimes even a dehumidifier to cure properly.
Aerogel
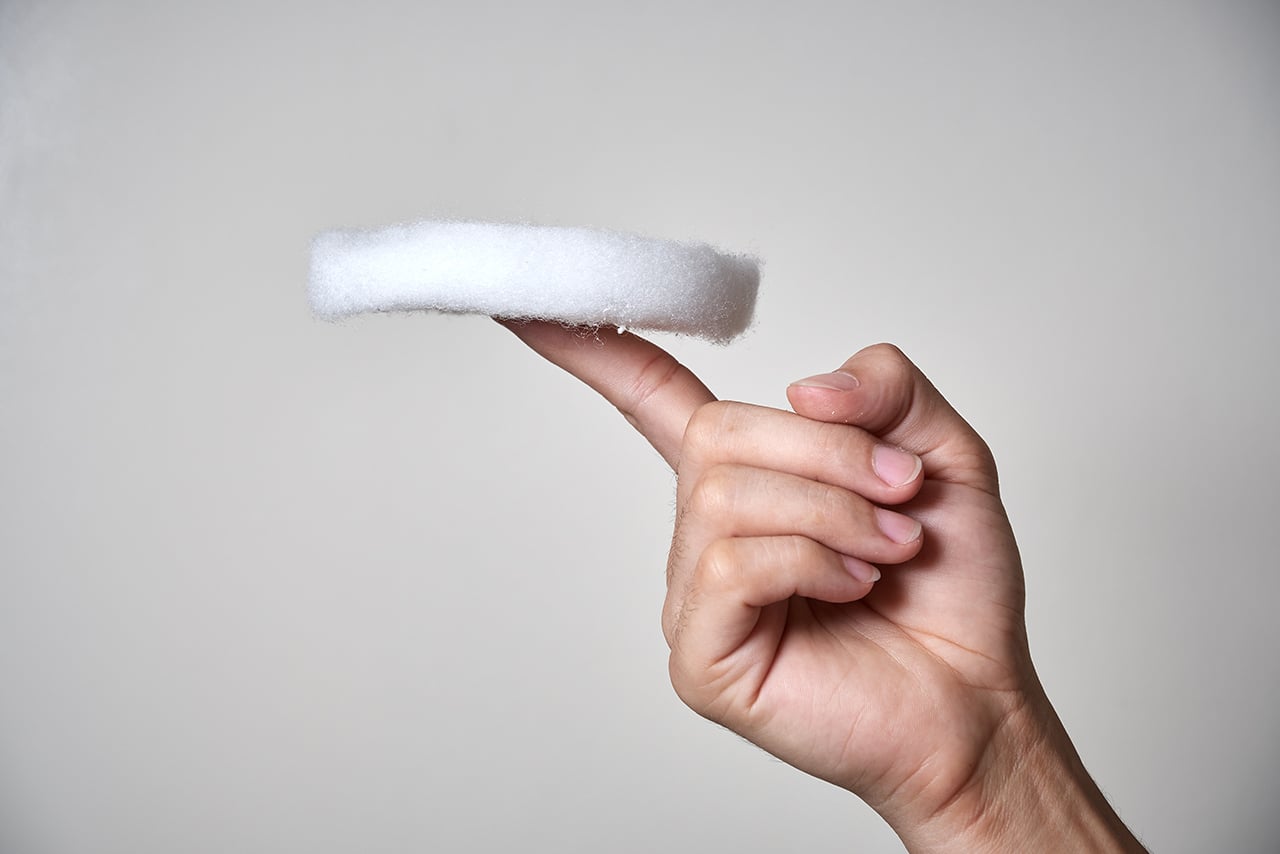
Aerogels have a high gas content that gives them an impressive R-value of 10.3 per inch of thickness. Photo courtesy of The National University of Singapore
Moving into more innovative territory, aerogel thermal insulating materials aren’t necessarily new, but their growing availability has increased their ease of application over the years.
Usually composed of silica aerogels are generally transparent in appearance and have a high gas content that gives them an impressive R-value of 10.3 per inch of thickness. This incredible propensity for low thermal conductivity makes it the most energy-efficient insulation material out there, greatly reducing a building’s heating and cooling energy usage.
“The ability to decrease building energy demand overall by using highly effective aerogel based insulation materials made from environmental waste is essential,” Hai Minh Dong, associate professor of mechanical engineering at the National University of Singapore Faculty of Engineering, told gb&d in a previous interview. “The water repellent property of the aerogels allows them to be adaptable to both dry and rainy weather, and their structure remains stable for more than six months.”
One of the main drawbacks to aerogels, however, is that they can be very brittle, potentially making them more difficult to use in areas with higher tension.
Pros of Aerogel
- Extremely insulative. Out of all types of insulation, aerogel has the highest R-value per inch of thickness, meaning less material is required to do a better job of preventing heat transfer into or out of a building.
- Lightweight. Aerogel insulations are approximately 95% porous, meaning they consist almost entirely of air—as such, they are extremely lightweight and incredibly easy to work with.
- Water repellant. Silica-based aerogel insulations are naturally hydrophobic, meaning they do not absorb or retain moisture but instead repel it altogether, making them highly resistant to the mold or mildew growth.
Cons of Aerogel
- Cost. Thanks to its relative newness and complex manufacturing process, aerogel is the single most expensive insulation option on the market, typically costing upwards of $10.00 per square foot.
- Brittle. Most silica-based aerogels are quite brittle to the touch as a result of their porosity, pore size distribution, and general chemical composition; aerogel insulation can be strengthened through polymer-reinforcement, but this further raises the price.
- Can be hazardous. While silica-based aerogel insulations are not known to be either carcinogenic or toxic, they are considered to be a mechanical irritant as a result of their hydrophobic nature, which can cause drying of the skin, eyes, and mucous membranes when improperly handled.
Matt Noel contributed to this article.