Nestled in the Berkshire Mountains along the banks of the Green River, in the heart of the town of Williamstown, Massachusetts, is Cable Mills Apartments. In its heyday, the previously General Cable Mill manufactured twine and, years later, wire and cable. Over time the mill complex became an abandoned ruin consisting of 15 buildings, eight of which were renovated over 14 years under the design leadership of Finegold Alexander Architects. The eight buildings total over 96,000 square feet and were renovated, restored, and redesigned into 61 one-, two-, and three-bedroom residences with a long list of amenities.
Faced with a housing shortage and the added expense of urban infill projects, developers are transforming abandoned mills in gateway cities into high-end loft residences. This nationwide multi-family trend looks to satellite suburbs across the Rustbelt and Sunbelt regions and presents a low-carbon alternative to building on greenfield. Firms like The Architectural Team and Finegold Alexander Architects have developed expertise in renovating former mills like the Cable Mills Apartments and reimagining how to better use these existing structures for multi-family and mixed-use.
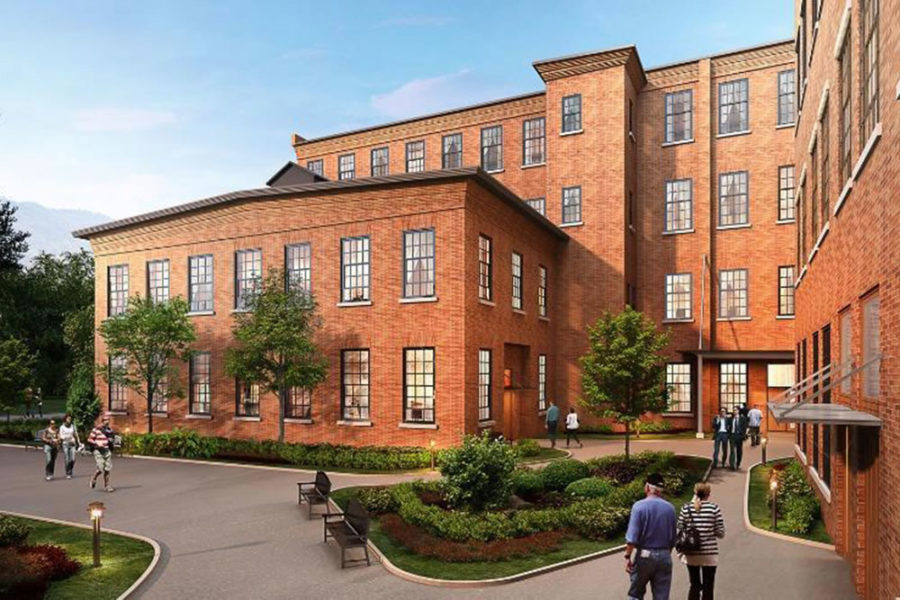
Courtesy of Cable Mills
“It’s a perfect storm of housing demand and the post-Covid remote workforce era,” explains Scott Maenpaa, project manager at The Architectural Team in Boston, a firm that specializes in mill reuse and renovation. As demand for part-time office space closer to home increases, Maenpaa has observed a shift toward true mixed-use adaptive reuse projects with retail on street level, offices in the middle, and residential above.
Conveniently located on the outskirts of large cities, the reuse of extremely carbon-intense structures is a boon to multi-family housing, the local economy, and the carbon economy. As these new urban hubs, downtowns, gateway cities, and “Zoom Towns” develop, their sizes and location fit a “10-minute city” model—one that provides residents with entertainment, housing, workplaces, and retail within close proximity.
These old, sturdy mill structures, some up to 200-years-old, were once staples of early American manufacturing. With their large spans, they are ideal for consumers seeking high ceilings, open floor plans, and an industrial-chic look. “The character and aesthetics of these buildings are so appealing to people,” says Maenpaa. However, practical considerations for a successful multi-family development reach far beyond aesthetics. Factors such as energy efficiency and acoustic remediation require extreme attention and expertise to ready mill buildings for new life.
Renovation Beyond Aesthetics
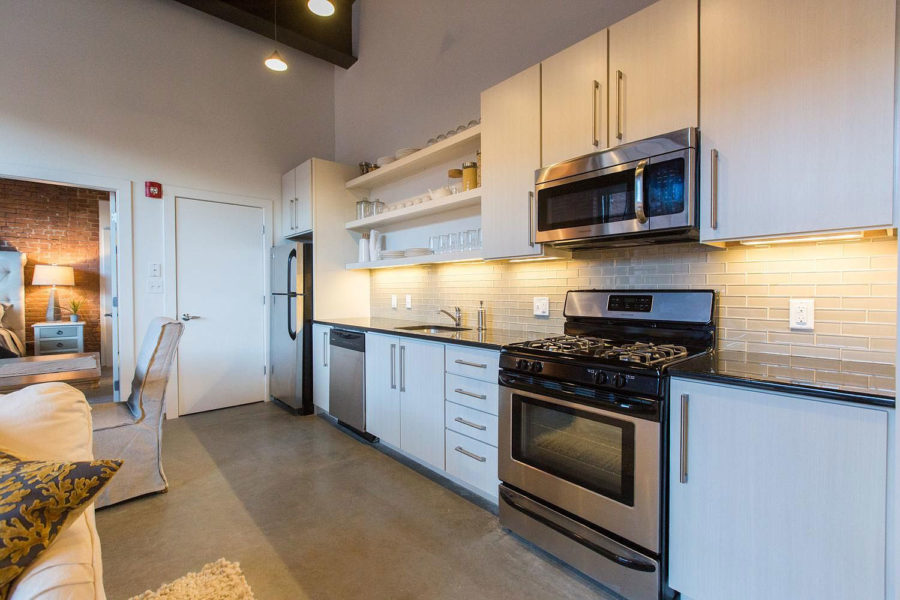
Photo courtesy of Cable Mills
Old factory floors, windows, and walls require several renovation considerations to meet acoustical comfort levels that suit the expectations for sound separations in high-end, multi-family housing. Old floors with thick, chestnut planks that are 10 to 12-inches wide and long are striking and rich in history. But acoustic bridging through this old flooring presents a major concern. In some cases, cracks between the plank flooring lead directly into the unit below.
“The flooring plane does a lot of the heavy lifting when remediating mills to adhere to residential codes and expectations of sound separations in multi-family housing,” says Bill Devin, business unit manager, acoustics division at REGUPOL America, a global leader in acoustical solutions. From the very beginning, REGUPOL worked in close collaboration across all teams involved with the Cable Mills project to create spaces free of unwanted sounds and vibrations.
For best acoustic remediation practices, Devin suggests REGUPOL sonus curve 25mm (1-inch), a dimpled product made from 92% post-consumer recycled tire rubber installed dimple side down with polyethylene sheeting. “It acts like a rubber gasket with isolating rubber strips around the perimeter.” After it is in place, contractors pour 3-inches-plus of concrete. This acts as a new subfloor resting on rubber bearings which serve as a rubber sound isolator.
“The dimple structure leaves air pockets, which reduce the amount of contact with the surface area of the timber subfloor,” Devin says. This allows the concrete to have more deflection and increased acoustical performance. “The floor is (basically) sitting in a pool of acoustic isolating rubber. Because it’s not rigidly connected, this floating floor helps guarantee the peace and quiet expected of high-end residential real estate. It also allows for amenities such as fitness centers, and office and retail as mixed-use development, without disturbing tenants.”
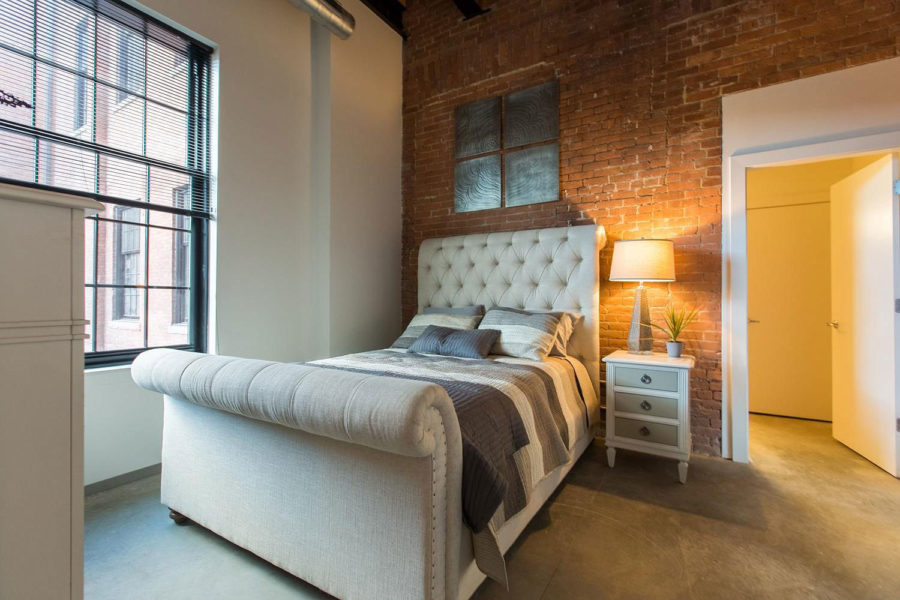
Photo courtesy of Cable Mills
This system adds 3 inches in height and added weight of almost 45 pounds per square foot. Fortunately these sturdy structures were engineered to hold heavy machinery and goods and therefore typically do not require structural reinforcements. After floors are rehabbed in this way, residents may choose a hard surface like hardwood or tile flooring, without disturbing neighbors with their footfall.
Oversized windows and openings coupled with exposed brick construction are iconic but not acoustically desirable. One way to address airborne sounds coming from outside disturbances and prevent noise pollution is double-pane windows. They provide added energy efficiency while sealing units off to outdoor airborne noise.
Finally, developers often leave exposed ceilings and bricks inside and build dividing walls in the interior spaces to house mechanical, electrical, and plumbing components. Architects can further address acoustic strategy and reduce mechanical noise by using larger ducts, suggests Sayali Wazalwar, acoustics researcher for GBBN Architects. “That decreases the air velocity in ducts going through the diffuser, and that makes less noise.”
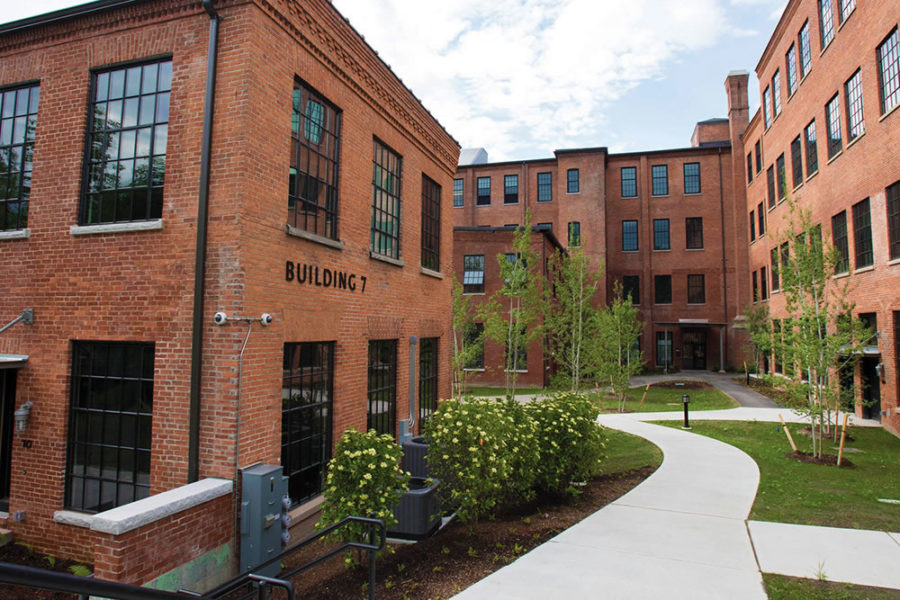
Photo courtesy of Cable Mills
Technical equipment in buildings is essential for providing air, water, heat, and electricity and is usually housed in dedicated mechanical rooms in basements, roofs, or other floors. However, sound and vibration nuisance must be considered when planning for building services. Airborne and structure-borne sound isolation can be accomplished using elastomers installed under machine foundations, equipment frames, or floating floor constructions. REGUPOL vibration and REGUFOAM vibration isolation materials help mitigate machine vibration. They provide damping, decoupling, mass, and absorption plus offer the necessary properties to create precisely customized solutions for sensitive applications.
By weaving these historical buildings back into the fabric of a community it knits a thread of history. This practice also boosts aspects of community resilience by providing safe, clean abundant housing and eliminating environmental hazards. Old mills may contain hazardous materials such as asbestos and lead paint that will be remediated by developers. “And then they’re no longer a threat to residents of the building or the community,” Maenpaa says. One final safety benefit, Maenpaa adds, is that because they are not accessible, fire departments will often let old, abandoned mills burn if they catch fire. Giving them new life as a pillar of the community reduces fire risks for a municipality.
Renovation and reuse are some of the most economical choices developers can make, rather than constructing a new building. “A ton of embodied energy was exhausted when they built them,” reminds Maenpaa of mill buildings. Developers may realize as much as a 20% cost savings over new construction because there’s no demolition, and they’re not paying to bring in more materials.