Story at a glance:
- R-value is one of the most important things to consider when choosing insulation, but it isn’t the only factor.
- Air permeability, vapor permeability, moisture tolerance, fire resistance, installation requirements, and cost all play a role in deciding which insulation to choose.
- The sustainability of various insulation products can be evaluated by looking at embodied carbon, durability and longevity, potential for recycling or reuse, and more.
When most people think about insulation, R-value—or the material’s thermal performance—is often the first thing that comes to mind. And while R-value is an important factor to consider when choosing insulation, it is by no means the only factor to consider.
This article is an introductory guide to the factors to consider when choosing insulation for a project.
What to Consider When Choosing Insulation
There are seven key factors to consider when choosing insulation: R-value, air permeability, vapor permeability, moisture tolerance, fire resistance, installation requirements, and cost.
R-Value

Photo courtesy of Rmax
Perhaps the most well-known factor associated with insulation, R-value represents a material’s ability to slow the transfer of heat between building components. A higher R-value indicates that the material is more effective at reducing the flow of heat into or out of a building, while a lower R-value indicates a higher degree of heat exchange.
Local climatic conditions greatly influence what R-value insulation a project needs. The DOE separates the continental United States into seven unique climate zones, each of which has specific insulation R-value recommendations. The suggestions listed below are those issued by Home Depot.
- Zone 1. Attics (R30 to R49); 2×4 Walls (R13 to R15); 2×6 Walls (R19 to R21); Floors (R13); Crawlspaces (R13)
- Zone 2. Attics (R30 to R60); 2×4 Walls (R13 to R15); 2×6 Walls (R19 to R21); Floors (R13); Crawlspaces (R13 to R19)
- Zone 3. Attics (R30 to R60); 2×4 Walls (R13 to R15); 2×6 Walls (R19 to R21); Floors (R25); Crawlspaces (R19 to R25)
- Zone 4. Attics (R38 to R60); 2×4 Walls (R13 to R15); 2×6 Walls (R19 to R21); Floors (R25 to R30); Crawlspaces (R25 to R30)
- Zone 5. Attics (R49 to R60); 2×4 Walls (R13 to R15); 2×6 Walls (R19 to R21); Floors (R25 to R30); Crawlspaces (R25 to R30)
- Zone 6. Attics (R49 to R60); 2×4 Walls (R13 to R15); 2×6 Walls (R19 to R21); Floors (R25 to R30); Crawlspaces (R25 to R30)
- Zone 7. Attics (R49 to R60); 2×4 Walls (R13 to R15); 2×6 Walls (R19 to R21); Floors (R25 to R30); Crawlspaces (R25 to R30)
Building code requirements often loosely correspond with these recommendations, though projects located in areas with high energy-efficiency requirements (like California) or projects pursuing a particular green building program certification may require insulation with a higher R-value than what the DOE suggests, especially when it comes to the insulation used in wall assemblies.
When choosing insulation it’s important to know whether the listed value represents the R-value per-inch of material or the total product; the R-value of spray foam and blown-in insulation is typically measured per-inch while the R-value of fiberglass batts, mineral wool panels, and rigid foam boards is generally the sum of the product itself.
Air Permeability
Insulation may be classified as either air permeable or air impermeable, with the former referring to those materials that facilitate the passage of air and the latter describing those materials that prevent the passage of air. Air permeable insulation includes materials like fiberglass, mineral wool, blown cellulose, and expanded polystyrene (EPS); air impermeable insulation materials include polyurethane spray foams as well as rigid foam boards made from either polyisocyanurate or extruded polyethylene (XPS).
Air permeable insulation is not in and of itself a bad or a poor choice, but it does require the addition of a continuous air barrier to help prevent energy loss via convection. Air impermeable insulation can be used as a building’s primary air barrier. Knowing this, it might seem as though air impermeable insulations like spray foam are always the better choice—in reality, climate and air-sealing strategies play a large role in dictating whether air permeable insulation or air impermeable insulation is necessary.
A building that employs extensive exterior air-sealing techniques, for instance, may not require air impermeable insulation, as there is significantly less opportunity for convective heat loss. Retrofitting an existing building may require the addition of air impermeable insulation to adequately address any existing leaks in the building’s envelope.
Vapor Permeability
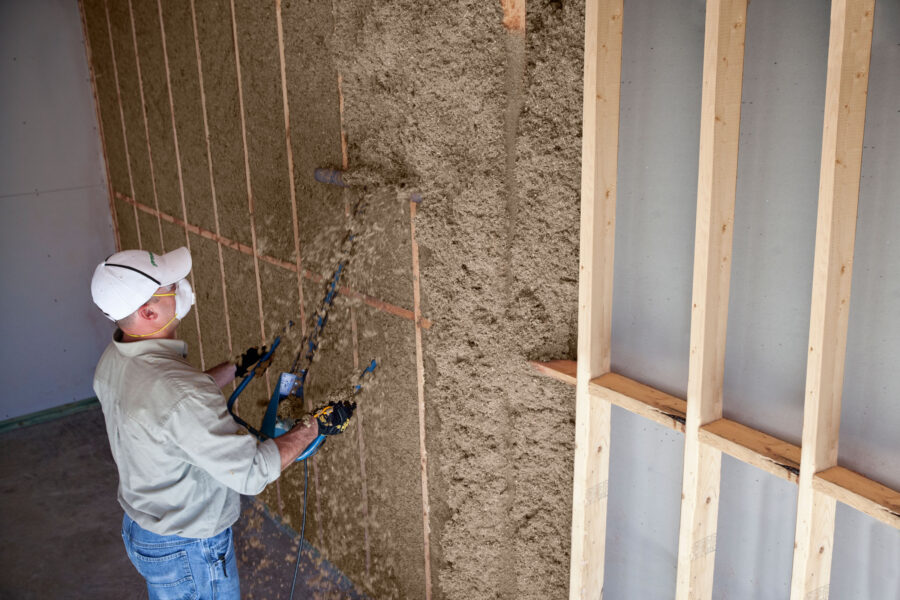
Photo courtesy of Greenfiber
Similarly, vapor permeability describes how well water vapor passes through an insulation material; vapor permeability is measured in perms. Insulation may be considered “vapor open” if it measures at above 10 perms, meaning water vapor easily passes through it. A material that measures at or below 10 perms is considered to be vapor retardant, meaning water vapor passes through it at a reduced rate.
The International Residential Code separates vapor retardant materials into three classes:
- Class I. Materials in this class have a very low vapor permeability rated at 0.1 perms or less; includes materials like unperforated aluminum foil and sheet polyethylene.
- Class II. Materials in this class have a low vapor permeability rating that is greater than 0.1 perms but less than or equal to 1.0 perms; this includes the bitumen-coated kraft facing on insulation batts and unfaced expanded/extruded polystyrene.
- Class III. Materials in this class possess a medium vapor permeability rating that is greater than 1.0 perms but less than or equal to 10 perms; includes materials like gypsum board, unfaced fiberglass insulation, and cellulose insulation.
Vapor retardant insulation may seem like the obvious choice, but there are instances where vapor permeable insulation is warranted. Projects in hot, humid climates, for example, require a certain amount of vapor permeability to allow interiors to dry out and prevent mold growth; permeable and semi-permeable insulation like mineral wool, fiberglass, and cellulose can then be useful in moving water vapor out of wall and roof assemblies where moisture may accumulate.
Vapor permeable, plant-based materials like cellulose insulation have also become increasingly common as more architects, engineers, and construction professionals prioritize green building strategies, leading to more focus being placed on the inclusion of robust air and vapor barriers.
Moisture Tolerance
Moisture tolerance refers to how well a material holds up when exposed to moisture. Considering moisture tolerance is important primarily when choosing insulation that will be in contact with the ground (e.g beneath a concrete slab) or installed on the outside of a building’s envelope.
Rigid foam expanded polystyrene and extruded polystyrene are two of the most common types of insulation used for under-slab applications due to their high moisture resistance, though polyisocyanurate insulation can also be used when protected by a foil facer.
Perhaps surprisingly, dense-pack cellulose and straw bale insulation also have admirable moisture tolerance thanks to their status as hygric buffers—that is, materials capable of absorbing, distributing, and releasing moisture without suffering degradation. These materials shouldn’t be used for under-slab or outdoor applications, but they can be extremely useful in wall and roof assemblies.
Fire Resistance
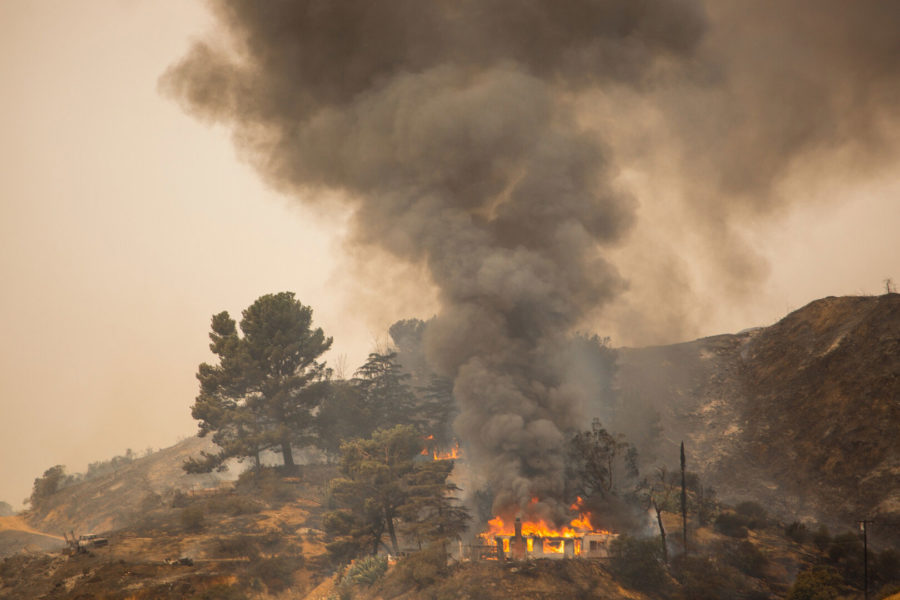
As wildfires and other severe climate events become more frequent, it becomes increasingly important to design with disaster resiliency in mind. Photo courtesy of ROCKWOOL North America
As wildfires continue to increase in both frequency and severity, the fire resistance of all building components—including insulation—must be carefully considered. Similar to other construction materials and building assemblies, the fire resistance rating of insulation is determined by its flame spread index and smoke development index.
Depending on how well it performs, insulation may be rated as either Class A, Class B, or Class C by ASTM or the National Fire Protection Association.
- Class A. Materials in this category have a flame spread index between 0 and 25 and may not exceed a smoke development index of 450; insulation with a Class A fire rating is considered non-combustible and will not contribute to a fire spreading.
- Class B. Materials in this category have a flame spread index between 26 and 75 and may not exceed a smoke development index of 450; insulation with a Class B fire rating has a moderate level of fire resistance and a very limited contribution to fire spread.
- Class C. Materials in this category have a flame spread index between 76 and 200 and may not exceed a smoke development index of 450; insulation with a Class C fire rating has a low level of fire resistance and a limited contribution to fire spread.
Most modern building codes require exposed insulation to possess either a Class A or Class B fire rating. Some insulation materials, like mineral wool, are inherently non-combustible and thus automatically achieve a Class A rating; materials like cellulose, on the other hand, are inherently combustible and so require the addition of certain chemicals to improve their fire resistance.
Installation Requirements
The installation requirements of various types of insulation should be factored into the initial decision-making process. Proper installation is crucial to insulation’s long-term performance, and some insulation is much easier to install than others.
Fiberglass batts and stone wool panels, for example, are considered to be two of the easier types of insulation to install, though the latter can be a bit tricky to maneuver by oneself due to its density. Blown-in insulation is also something a homeowner or general contractor can install with relative ease, though all air-sealing work and testing should be completed ahead of time.
Rigid foam panels represent something of a middle ground when it comes to ease of installation, as they are relatively easy to maneuver and can be cut to size with a simple utility knife or saw, but require careful fitting and sealing between all gaps/seams to prevent air leakage. For this reason, professional installation is typically recommended in order to ensure peak performance.
Polyurethane spray foam insulation, on the other hand, should always be installed by an experienced professional and requires that environmental conditions like ambient and surface temperature be within a certain range. Professional installers will also have the necessary protective equipment to ensure that the installation is both safe and effective. The installation of dense-packed cellulose insulation is also something that is best left to the professionals, as the process necessitates specialized machinery and requires adequate pressure be maintained in order to achieve the proper density.
Cost
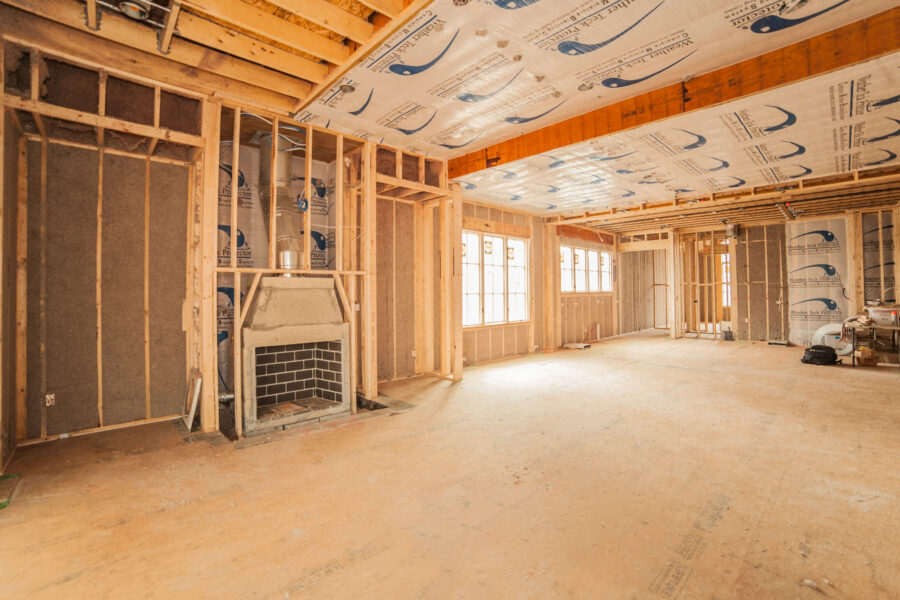
Photo courtesy of Greenfiber
Finally, the cost of insulation—both the material itself and any associated installation costs—may very well be the deciding factor on projects where budgeting is of great concern.
Generally speaking fiberglass insulation is often one of the cheapest options, regardless of where a project is located, whereas materials like mineral wool and polyisocyanurate tend to be on the more costly. EPS and XPS rigid foam panels tend to cost more than fiberglass but usually less than polyisocyanurate and stone wool. Other materials—like spray foam and cellulose—can vary widely in price depending on location and availability.
Upfront costs of insulation aren’t the only important expenses to consider when choosing a material; mineral wool may come with a higher price tag than fiberglass, but its higher R-value per inch can help a building drastically reduce its operational expenses, potentially making it more cost effective in the long run.
When is Insulation Considered Sustainable?
Given the rapid rise of green building practices in recent years, let’s explore how to evaluate various insulation products for sustainability. Insulation materials are typically considered sustainable when they possess some combination of the following qualities:
Low Embodied Emissions
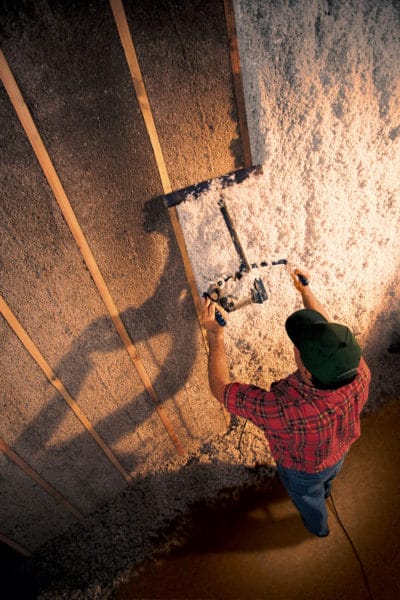
Greenfiber’s wall insulation starts as a plant material, is made into paper, and reused as insulation. Photo courtesy of Greenfiber
The embodied emissions of insulation essentially represents its net total emissions and includes all GHGs released during the production and installation of the material. Exact values can be found using Builders for Climate Action’s Building Emissions Accounting for Materials (BEAM) estimator tool, but more or less adhere to the following ranking:
- Very high. Polyurethane spray foam and XPS foam both have a very high global warming potential as they are manufactured using blowing agents like hydrofluorocarbons, of which are very good at trapping heat; these harmful agents are released into the atmosphere during manufacturing and throughout the product’s lifetime.
- High. Despite also using blowing agents in their manufacturing, polyisocyanurate and EPS foam insulation are considered to be less damaging than spray and XPS foam; this is because both use pentane as their primary blowing agent, a pure hydrocarbon that does not trap heat nearly as well as HFCs.
- Medium. Fiberglass is typically considered to be middle of the road when it comes to embodied GHG emissions, as fiberglass plants use furnaces to melt silica sand into glass fibers; these furnaces produce carbon dioxide, nitrogen oxide/dioxide, sulphur dioxide, chloride, fluoride, and various VOCs.
- Low. Though it is marketed as one of the more eco-friendly insulation options, stone wool actually has a higher global warming potential than one might expect; this is because mineral wool plants operate similarly to fiberglass plants and use large furnaces to melt down volcanic rock and/or slag, which in turn produces large amounts of carbon dioxide, nitrogen oxides, and VOCs; in recent years, however, mineral wool plants have begun working to make the manufacturing process less intensive.
- Very low. Plant-based insulation materials like wood-fiber cellulose and straw bales have the lowest embodied carbon of any insulation thanks to their ability to sequester carbon.
It is important to keep in mind that the upfront emissions produced during the manufacturing of insulation are in part offset by the long-term energy savings they provide after installation; the high R-value of polyiso, for example, significantly reduces a building’s heating and cooling requirements, which in turn translates to fewer operational emissions.
Use of Renewable & Nontoxic Ingredients
The materials and ingredients used to create insulation products also influences their overall sustainability. Wood-fiber cellulose and straw bale insulation, for example, are typically considered green insulation options thanks to their being made from natural, renewable resources instead of petroleum-based plastics like EPS, XPS, polyurethane spray foam, and polyisocyanurate insulation.
Use of renewable resources does not, however, automatically translate to sustainability, as resources may be cultivated, harvested, or otherwise obtained in an environmentally destructive manner. What’s more, many insulation products made from natural materials also contain chemical additives or treatments—intended to improve fire, pest, or moisture resistance—that may pose a threat to human and environmental health.
One way to verify whether insulation contains harmful compounds is to check for declare labels that disclose the types and amounts of ingredients present in the product. This includes Environmental Product Declarations (EPD) and Health Product Declarations (HPD) as well as the International Living Future Institute’s (ILFI) Red List Free label, the latter of which indicates that the insulation does not contain any of the “worst in class” chemicals known by the ILFI to cause human and/or environmental harm.
Durability & Longevity
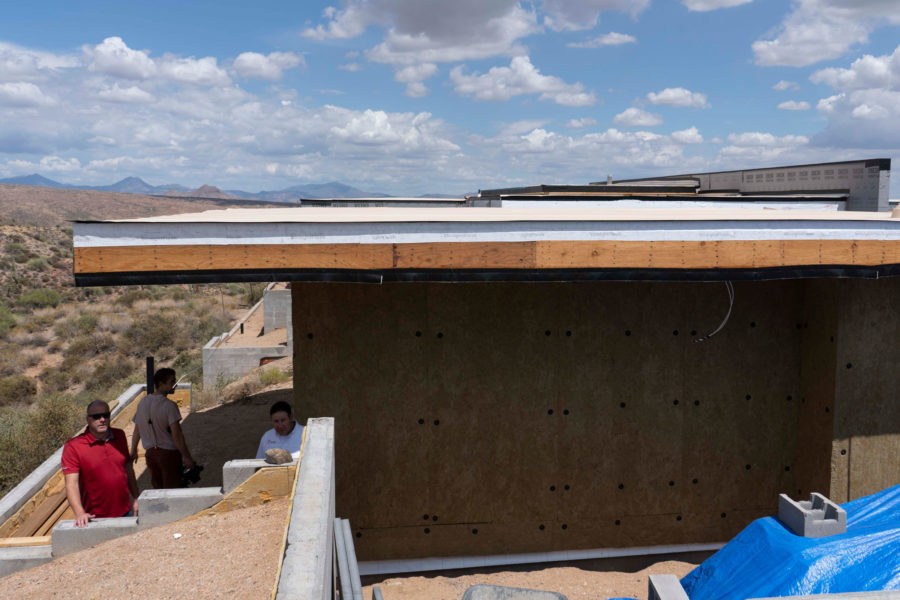
Mineral wool insulation is extremely durable and long-lasting. Photo courtesy of ROCKWOOL North America
Durable and long-lasting insulation ultimately helps to reduce both the need for new resource extraction and the GHG emissions incurred as a result of processing/manufacturing said resources into new insulation products. Materials like mineral wool and fiberglass, for example, have an average lifespan of 80 years, whereas cellulose typically needs to be replaced after 20 to 30 years.
High Recyclability or Compostability
No material lasts forever, though, and sometimes it is necessary to replace old insulation with new insulation. But if a material can be recycled or reused at the end of its operational lifespan instead of being thrown away, its lifetime environmental footprint is reduced. Most insulation can be recycled in some capacity, though some materials are easier to recycle than others and require less processing before reuse.
Some companies even have insulation take-back programs that make recycling even easier for consumers; ROCKWOOL’s Rockcycle initiative, for example, collects stone wool material from construction, renovation, and demolition sites to be reused in new ROCKWOOL products. Mineral wool insulation is particularly well suited to these sorts of take-back programs, as the material can be recycled again and again without experiencing a loss in quality—a characteristic that makes up for stone being a non-renewable resource.
Straw bales, wood-fiber cellulose, and other plant-based insulation materials have the potential to be composted once they reach the end of their operational lifespan, but only if they have not been treated with chemicals and do not contain man-made glues, adhesives, or binding agents.
Types of Insulation Materials
Now that we’ve a better idea of what factors to consider when choosing insulation, let’s take a look at some of the most common types of insulation and how they compare.
Fiberglass
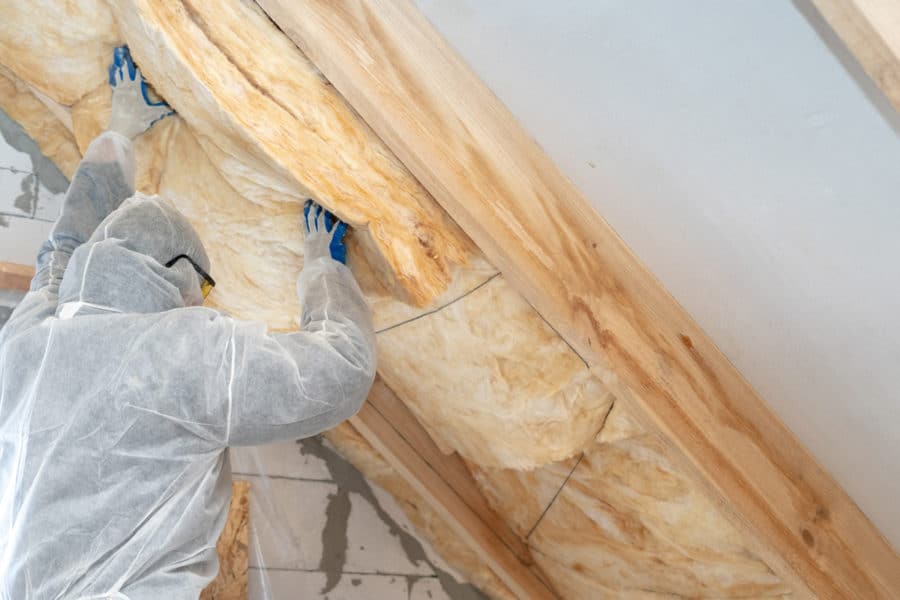
Usually dulled out in batts that are installed in pieces or rolls that are rolled out, fiberglass remains as one of the most common forms of insulation. Photo by Brizmaker
Fiberglass is one of the most common forms of insulation due to its adaptability, affordability, and effectiveness. Fiberglass insulation is made by melting silica sand (amongst other ingredients) into glass; that glass is then spun into thin fibers and mixed with resins to create batts, rolls, or boards.
Due to its commonality, the mass production of fiberglass has made it one of the cheaper options for thermal insulation material. The R-value of fiberglass insulation typically ranges between 2.2 to 2.7 per inch of thickness—which isn’t exactly terrible, though it is low when compared to other options.
Because it is made from inorganic materials, fiberglass insulation does not serve as a food source for insects or pests (although rodents have been known to use fiberglass in their nests). Fiberglass is also inherently non-flammable, meaning it won’t readily contribute to the spread of fires. Fiberglass insulation is both air and vapor permeable; as such, it will require the addition of an air/vapor barrier to prevent the unwanted transfer of air and moisture into or out of a building.
Fiberglass is one of the most DIY-friendly types of insulation to install, but does require the use of gloves and safety goggles to prevent skin and eye irritation; a respirator or dust mask is also recommended to avoid breathing in any tiny glass particles shed during the installation process.
Mineral Wool
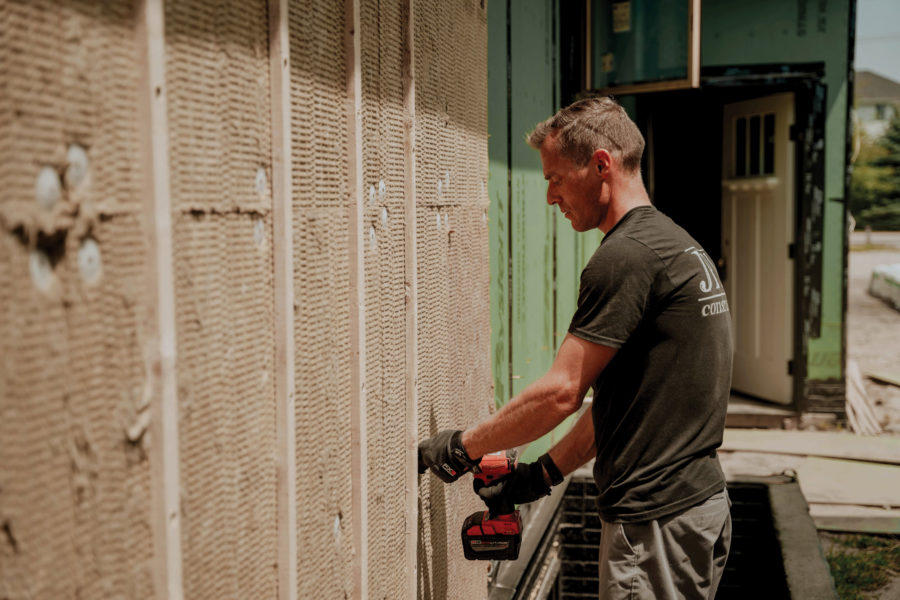
Photo courtesy of ROCKWOOL North America
Mineral wool—also known as stone or rock wool—is a type of insulation made by melting volcanic rocks (e.g. basalt, bauxite, dolomite, et cetera) or slag in a furnace and then spinning the molten material into fibrous strands.
Mineral wool insulation shares certain similarities with fiberglass, but is altogether heavier and denser; as such, the per-inch R-value of stone wool is higher, averaging between 3.0 and 3.3. Despite being dense, however, mineral wool is still highly porous, meaning it is permeable to both air and water vapor. As previously mentioned, mineral wool is an inherently non-combustible material, making it ideal for projects in wildfire-prone areas.
Stone wool insulation also has the advantage of being extremely durable. “It’s right there in the name. Our products are made from stone—the most abundant natural resource on earth and fully recyclable,” Sophia Rini, director of public affairs and communications of ROCKWOOL, previously told gb&d. “You might hear us talk about harnessing the natural power of stone; that’s because our stone wool insulation carries many of the same properties as the raw material. They are lasting, durable, and resilient.”
ROCKWOOL is a leading provider of stone wool insulation products and offers a variety of batt, board, and granulate/loose-fill solutions. Mineral wool can be installed in DIY-fashion, but it is typically recommended that installation is conducted by experienced contractors or professionals. Similar to fiberglass, stone wool insulation should be installed wearing gloves, safety goggles, and a dust mask/respirator.
Cellulose
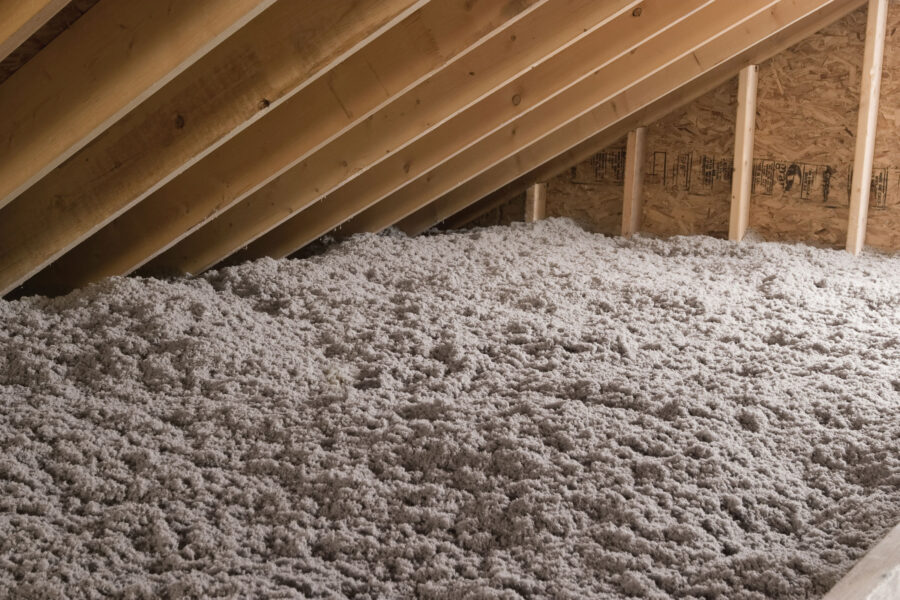
Photo courtesy of Greenfiber
Cellulose thermal insulation material has grown in popularity in recent years due to its highly sustainable nature. Made primarily of recycled, fiberized paper products like newspaper, cellulose is available as either loose-fill or dense packed insulation. It has a typical R-value of 3.2 to 3.8 per inch thickness and its relatively simple manufacturing process makes it more affordable than other options (depending on availability).
While naturally flammable, cellulose insulation can be—and typically is—treated with chemicals like borax or boric acid to increase its fire resistance while also making it less desirable to pests and mold. Cellulose insulation is both air and vapor permeable, but generally does not require the addition of a vapor barrier as it is capable of absorbing and releasing moisture without suffering water damage.
As a whole cellulose insulation is considered to be one of the most sustainable options on the market, and companies like Greenfiber have embraced that concept, taking steps to help the environment by using less energy consumption in the manufacturing process.
“Greenfiber uses a low-energy manufacturing process that results in materials with the least-embodied energy of most major insulation products. The production process generates little to no waste or byproducts because we leverage recovered material to start with,” Jason Todd, director of market development and building science at Greenfiber, previously told gb&d.
Straw Bales
Cellulose is not, however, the only plant-based insulation on the market; straw bales can also be used to prevent unwanted heat transfer between wall assemblies. While not particularly common anymore, straw bale insulation has long been used in the Midwest, with straw-bale construction being a staple of Nebraska-architecture since the late 1800s.
Straw bales typically have an R-value ranging between 0.94 and 2.38 per inch, with the exact value dependent on how tightly the bale is packed. This range is, admittedly, relatively low when compared to the per-inch R-value of something like stone wool or polyisocyanurate insulation, though straw bales make up for this in terms of sheer thickness; the average bale is 18-inches wide, meaning straw bale walls have a total R-value averaging between 30 and 36.
The density of straw bales also gives them a higher resistance to fire than one might expect, as the tightly-packed straw creates a low-oxygen environment, reducing the risk of combustion; fire resistance is further improved by the addition of lime plaster to the bales’ exteriors. Together, these qualities can help straw bale walls last for up to twice as long as walls built and insulated with traditional materials.
And because the plants commonly used for straw—rye, oats, wheat, and rice—are easy to grow, widely available, contain no toxins, and actively absorb and store carbon as they grow, straw bale insulation is considered to be very sustainable, affordable, and easy to source. It is also one of the more DIY-friendly types of insulation.
Compared to more conventional types of insulation, straw bales are much more susceptible to pests and readily absorb water, increasing the risk of mold, mildew, and premature degradation. This means walls containing straw bale insulation must be extremely well-designed to ensure adequate ventilation and prevent moisture buildup.
Polystyrene
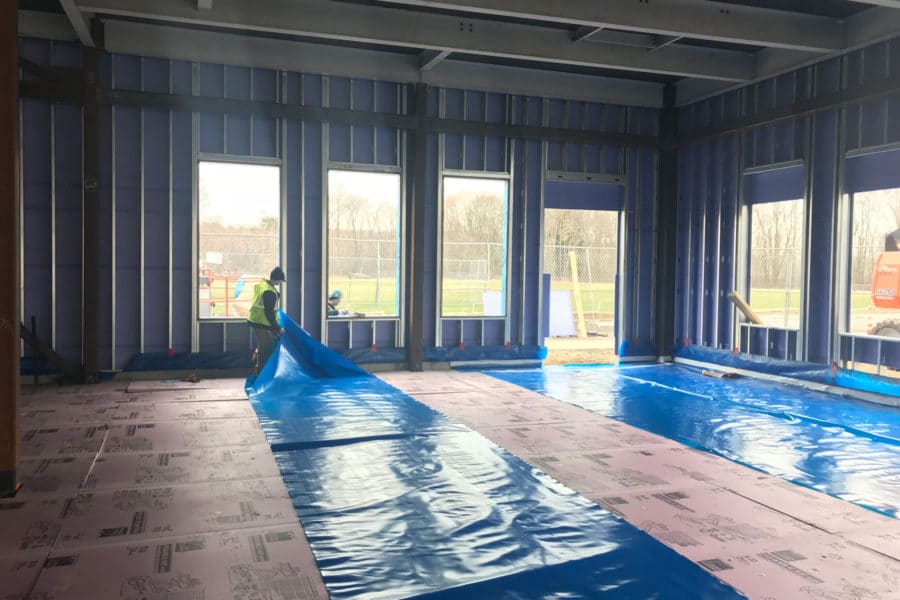
Polystyrene boards are lightweight and water-resistant, and their low water absorption helps to prevent mold. Photo courtesy of ISI Building Products
There are two common types of polystyrene insulation: expanded polystyrene (EPS) and extruded polystyrene (XPS).
- Extruded polystyrene. XPS is a strong, lightweight, and water-absorption-resistant type of closed-cell rigid foam insulation that typically possesses an average R-value of R5 per inch (this R-value will gradually drop as the gasses within the cells escape over time); XPS is manufactured using blowing agents, heat, and a specialized extruding machine.
- Expanded polystyrene. EPS rigid foam boards are similar to XPS foam boards but are lighter, thicker, and have an average R-value of R4 per inch; the manufacturing process for EPS involves the use of blowing agents, steam, and molds to expand the polystyrene into the desired form.
Both types of polystyrene insulation have similar properties, although XPS foam has a higher water vapor diffusion resistance than EPS foam, meaning it is not as permeable to air or water vapor, making it the better option for basements, foundations, and other below-grade applications. When properly installed and maintained, polystyrene insulation has an average lifespan of 30 to 50 years—a quality derived in part from its use of petroleum as a core ingredient.
This petroleum-based composition is, however, also one of the major drawbacks of polystyrene insulation. Like all plastic products, polystyrene does not biodegrade and gradually releases microplastics throughout its life cycle—and while both XPS and EPS foam insulation can be reused, their recycling options are limited. Polystyrene insulation also requires the addition of flame retardants in order to meet fire code requirements; some of these flame retardants are toxic and pose a threat to human health.
Polyurethane
Like polystyrene, polyurethane insulation is derived from crude-oil compounds, meaning it is considered a plastic polymer product; polyurethane is available in both rigid boards and spray foam. Polyurethane insulation is made by combining polyols and diisocyanates (chiefly MDI and TDI); this mixture is then heated and pressurized to create a dense, rigid foam.
As a plastic product polyurethane foam insulation is extremely durable and typically lasts upwards of 50 years before needing to be replaced. There are two types of polyurethane foam insulation—open-cell and closed-cell—which differ in a few important ways:
- R-value. Open-cell polyurethane foam has an R-value of about 3.6 per-inch, whereas closed-cell polyurethane averages closer to 6.5 per-inch.
- Permeability. Open-cell polyurethane foam is more permeable to both air and vapor than closed-cell, though the latter is not completely impermeable.
- Cost. Open-cell polyurethane is typically cheaper than closed-cell polyurethane foam.
Due to its chemical composition polyurethane spray foam is considered a flammable material—one that, upon ignition, will burn rapidly and produce thick smoke, toxic gasses, and intense heat. The installation of both types of polyurethane spray foam should be conducted by experienced professionals wearing the proper protective gear.
Plant-Based Polyurethane
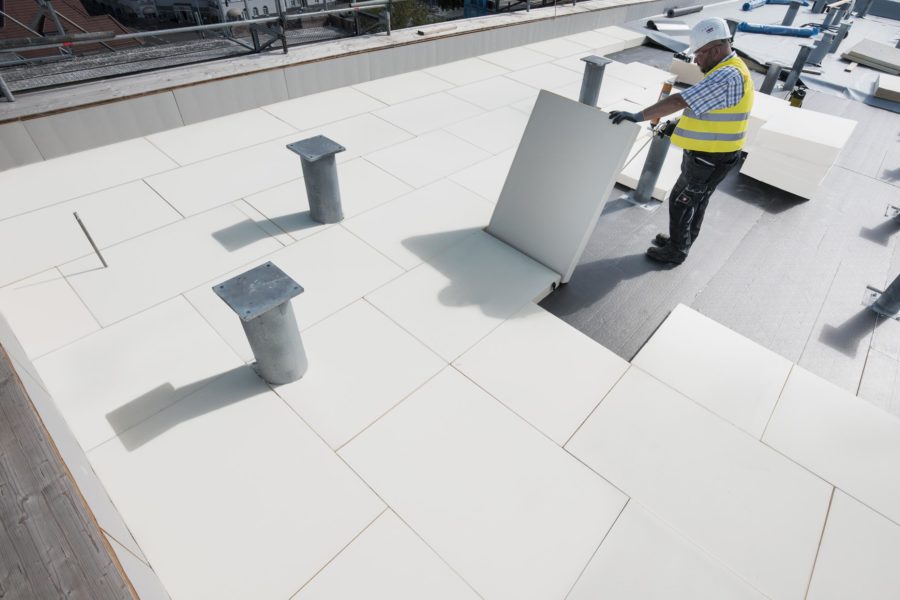
Climate-neutral materials like the raw materials in high-performance polyurethane insulation help drastically reduce the carbon footprint of buildings. Photo courtesy of Covestro
Plant-based polyurethane rigid foam (PPRF) is one of the leading sustainable alternatives to traditional polyurethane rigid foam insulation. Unlike its predecessor, PPRF does not contain chlorofluorocarbons—a group of compounds that contribute to anthropogenic climate change—making it much better for the environment.
Plant-based polymers are also easier to extract than petrochemical-based polymers and subsequently require less energy to manufacture, thereby reducing overall carbon emissions. Bio-based polyurethane rigid foam may be produced from a variety of plants and biomass sources. Covestro—a leading producer of polyurethane and polycarbonate raw materials—has helped pioneer advancements in the use of biomass as an alternative raw material for polyurethane insulation.
In 2021 the company started offering a new toluene diisocyanate—a core building block in polyurethane foam—produced in part from organic wastes like used oil and grease. The following year Covestro helped develop a breakthrough technology for producing the base chemical aniline (crucial to the production of methylene diphenyl diisocyanate, another chemical used in the creation of insulating foams) entirely from biomass.
While plant-based polyurethane uses different ingredients than conventional polyurethane insulation, it performs more or less the same when it comes to R-value, air permeability, and vapor permeability.
One of the major drawbacks of plant-based polyurethane, however, is its cost; PPRF is significantly more expensive than conventional polyurethane foam insulation, averaging between $18 and $19.15 per kilogram. PPRF is also a relatively new material—one that is still being tested and improved upon. As such it can be difficult to find a local supplier, which can increase a project’s overall construction time and costs.
Polyisocyanurate
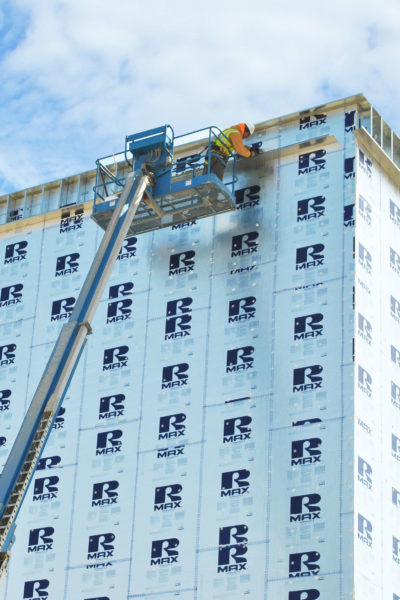
Polyiso remains the first-rate choice for wall applications, with an R-value of 6.5 per inch and a service temperature of 250º Fahrenheit. Photo courtesy of Rmax
Polyisocyanurate foam, also referred to as PIR or polyiso, is a kind of thermoset plastic insulation produced as a closed-cell, rigid, continuous foam board. Polyiso has the highest per-inch R-value of any insulation on this list, making it an ideal choice for high-performance projects looking to reduce energy consumption.
“With an R-value of 6.5 per inch, polyiso’s thermal properties surpass other rigid foam plastics by 20 to 70%, making it a clear choice for continuous insulation—a must for any sustainable project, given that HVAC costs often make up the vast majority of a building’s energy bill,” Greg Fantin, vice president of marketing at Rmax, previously wrote for gb&d.
Rmax is one of North America’s leading providers of polyiso insulation solutions and offers a range of products for both above- and below-grade applications. This impressive R-value does, however, come with an unfortunate caveat—if exposed to extremely low or extremely high temperatures, the R-value of polyiso insulation can actually drop by as much as 28%.
Because polyiso is a type of closed-cell thermoset plastic, it is inherently water-resistant, will not absorb water (though it can deteriorate over time if left exposed to the elements), and is both air and vapor impermeable. Polyisocyanurate insulation is typically protected by a facer, of which can be made from a variety of materials; foil facers are the most popular and have an extremely low perm rating (less than 1), essentially acting as an all-in-one air and vapor barrier.