Story at a glance:
- There are many different types of concrete floor coatings. Choosing the right commercial concrete floor coating or proper residential concrete floor coating for your project is crucial.
- Concrete floor coatings come in many forms, including epoxy coatings, acrylics, and polyaspartic coatings.
- Coatings help to protect concrete floors for years to come, preventing damage, loss of shine, and even accidents.
Whether you’re updating your garage or designing a commercial space, concrete is a solid choice. But untreated concrete can be slippery, hard to clean, and easily damaged. Adding a concrete floor coating eliminates those issues while enhancing the safety and appearance of your floor for years to come.
In general, the global protective coatings market size is expected to reach USD 19.46 billion in 2028 and register a revenue CAGR of 5.5%, according to a report by Reports and Data.
But where do concrete floor coatings fit in?
What are concrete floor coatings?
After your concrete floor is installed, a protective coating should be poured over the floor to seal the material and protect it from damage.
These coatings are usually considered to be epoxy, polyurethane, polyaspartic, or acrylic and can be used to customize your floor to meet your specific needs.
Because floor coatings protect your concrete for years, it doesn’t have to be resealed as often, making it a sustainable investment or helping you to not have to tear up a floor and begin again.
Benefits of Concrete Floors
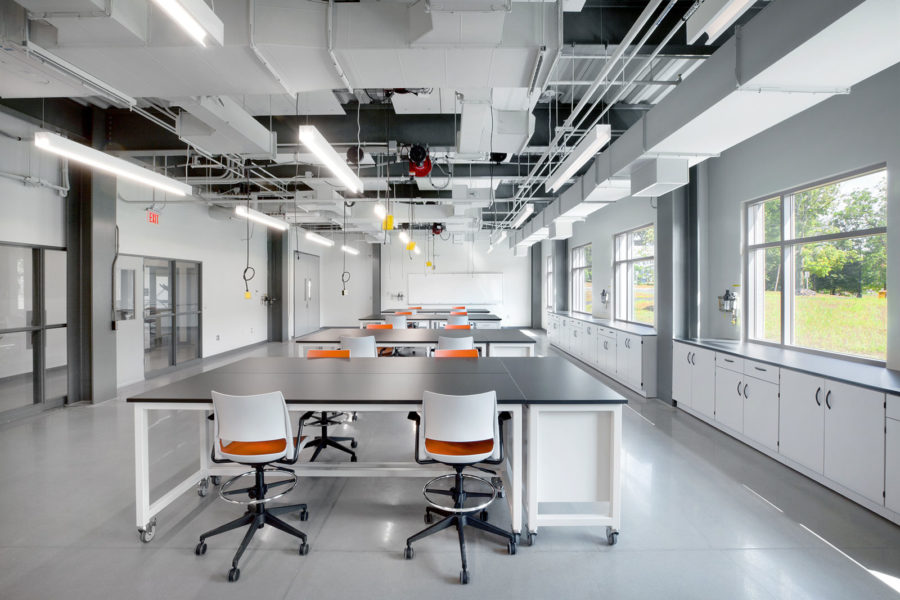
Urbahn Architects designed the 1,900-square-foot teaching lab to invoke an industrial aesthetic, including exposed ceilings and structural elements and polished-concrete floors. Photo by Ola Wilk
Concrete floor coatings are recommended for both residential and commercial spaces because they improve the look of the floor and extend the lives of the investment.
Concrete floor coatings can also improve safety and make floors easier to clean.
While there are many benefits to adding a concrete floor coating, these are five big reasons to seal the deal.
Durability
In high traffic spaces your floor has to hold up to continuous wear and tear. Concrete floor coatings can help your floor last for years in a residential or commercial space. Imagine accidentally dropping something heavy on your new concrete floor only to see the slab crack. Floor coatings provide a barrier to absorb impact and protect the concrete underneath.
Improved Appearance
Adding a coating to concrete transforms a dull material into a beautiful, unique floor. There are endless options to change the color, shine, or look of concrete with the right coating. Custom floor coatings can mimic the look of high-end marble or add a pop of brightness to an otherwise dim space.
Easy to Clean
Perhaps nothing is worse than staining new flooring. Because untreated concrete is so porous it absorbs liquids and traps small dirt particles that are almost impossible to clean. Concrete floor coatings prevent debris and spills from leaking into the concrete. No special cleaning supplies are needed; with the right coating your floor should only need a quick mopping to look sparkling clean.
Enhanced Safety
Both residential and commercial projects can experience improved safety with floor coatings. When concrete becomes wet, it’s extremely slippery. Concrete floor coatings increase traction and prevent falls. For those managing the safety of commercial spaces, concrete floor coatings are easier to clean and therefore harbor less bacteria than untreated concrete.
Protection
Floor coatings provide a barrier from scratches and dents while protecting the concrete underneath from damage. Depending on what you choose, floor coatings can prevent the concrete from deteriorating due to water, chemicals, or oils. Because floor coatings don’t have to be resealed very often, they are a great investment that can protect your floor and save you money.
Common Areas for Concrete Floor Coatings
Concrete floor coatings can easily improve common areas where you might experience a lot of foot or vehicular traffic—like a retail space, warehouse, or even parking garage.
Smart projects often incorporate coatings to maintain and protect structures and surfaces long after they’re completed. Some coatings provide waterproofing as well as concrete surface protection.
Here are some common areas where concrete for coatings are needed:
- Garages
- Warehouses
- Retail spaces
- Manufacturing facilities
- Showrooms
- Schools and universities
- Hospitals and health care facilities
Types of Concrete Floor Coatings
As previously mentioned, there are many different types of concrete floor coatings available on the market—from epoxy to polyurethane to hybrids, polyaspartics, and more.
“It’s important that the coating type you choose is meeting your intention and your requirements,” said Mosby Lawrence, waterproofing manager at NEOGARD, in a previous interview with gb&d.
Here’s a more detailed look at the types of concrete floor coatings.
Epoxy
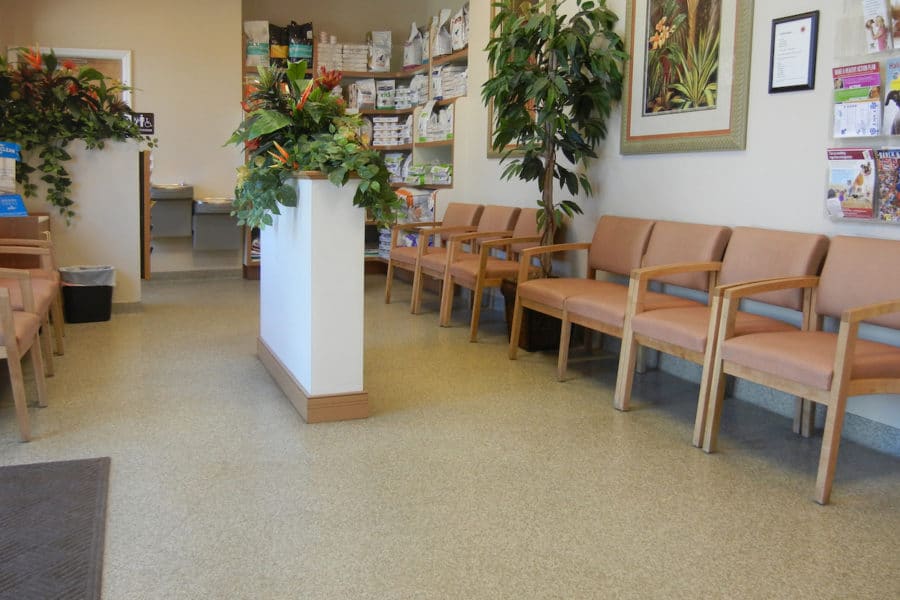
Photo courtesy of Everlast Epoxy
Epoxy broadcast systems have been used for decades as an affordable, easy to apply option with concrete surface protection and enhanced durability for ramps, bridge decks, and parking garages.
Lawrence says hybrid systems, especially polyurethane/epoxy, are becoming more popular as another of the top types of coatings. Their durability makes them a great option for high-volume, heavy traffic parking garages.
“Even if you don’t want to use hybrid throughout the whole garage, you can use it in high wear areas such as ramps, exits, entrances, and turning areas,” he previously told gb&d. “This will increase the durability of the entire system.”
Polyurethane
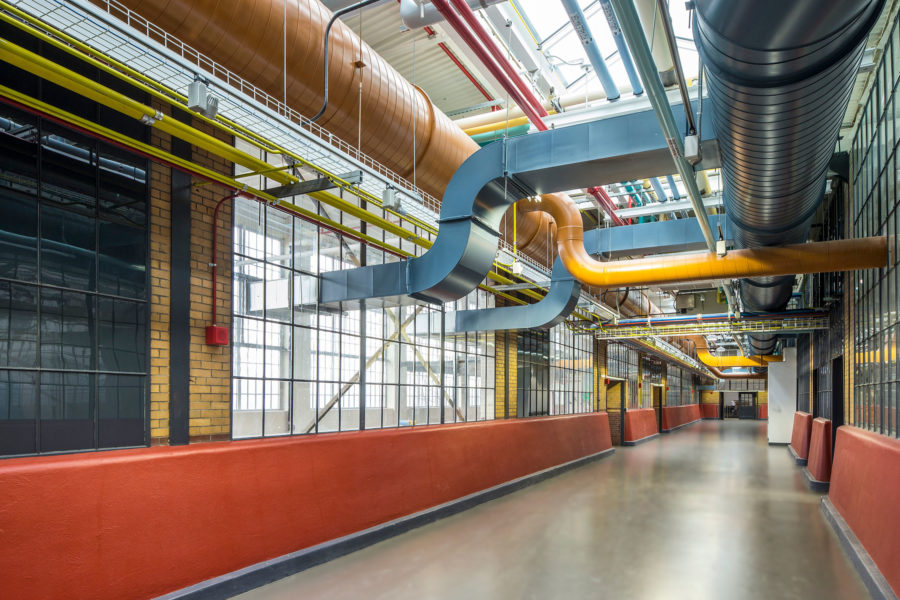
The Energy Innovation Center’s central “racetrack” floor is enhanced with ultra-low VOC polyurethane floor coatings. Photo courtesy of Covestro
Low-VOC, high-performance polyurethane-based concrete floor coatings are widely available in the market today, and they look and perform just as good as traditional coating systems, Steven Reinstadtler, a manager at Covestro, previously told gb&d.
“These coatings have proven performance and are widely used in commercial and industrial spaces by some of the most forward-thinking leaders in the environmental building movement,” Reinstadtler says.
He says while cost may have been a deterrent from using them in previous years, you save money in the long run.
“It’s true that, gallon-for-gallon, polyurethane floor coatings still carry about a 30% price premium over conventional epoxy or acrylic floor coatings. This percentage represents a major improvement over a few years ago when the premium was 50%, and the price gap is expected to narrow even further, but still, cost always matters.”
He continues. “While the pricing of conventional products might seem attractive at first glance, once you factor in durability over time—the life cycle cost—the argument for using a higher performance option becomes more evident. To that end, ultra-low VOC polyurethane floor coatings are not only better for the environment, but they also last three to four times longer than many typical floor coating products. If we’re looking for something beyond a band-aid solution for our concrete floor spaces that considers the future, the math is simple—high-performance polyurethane floor coatings offer roughly 300% more value for only a 30% increase in price. When an architect or specifier is considering their fiduciary responsibility to their client, it is important to consider the initial costs, as well as the owner’s longer-term operation and maintenance costs.”
Acrylic Coatings
An acrylic floor coating is a water-based option that is typically considered to be not as durable as epoxies or polyurethane floor systems, but often cost less polyurethane floor coatings. Its high-gloss finish is more decorative than functional, making it a solid solution for low-traffic areas that don’t need a ton of protection.
Polyaspartic Coatings
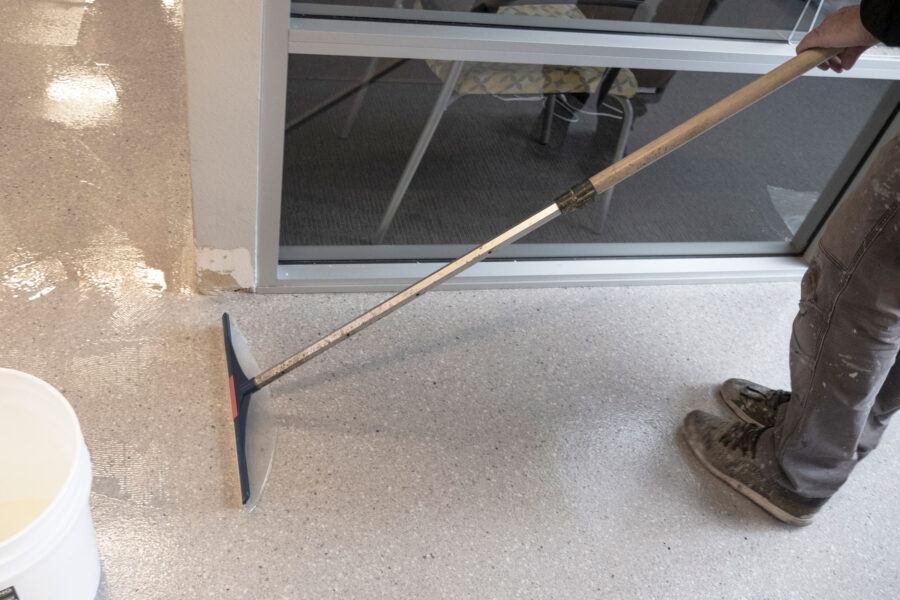
Photo courtesy of Westcoat
Polyaspartics are materials that are considered to be a subset of polyureas.
Polyaspartic floor coatings are often two-part systems made of a resin and a catalyst that kickstarts the curing process. While the polyaspartic coatings of old were found to be limiting, modern polyaspartic floor coatings are increasingly used as alternatives to epoxy and polyurethane coatings, according to corrosionpedia.com.
Cementitious Coatings
Cementitious urethane floor topping is designed to withstand aggressive chemical and thermal attack while providing abrasion resistance, according to TMI Coatings.
In 2009 Arkema launched Kynar Aquatec FMA12 for coatings used on cementitious and other substrates where breathability and/or greater elastic properties were needed. Kynar Aquatec CRX was developed for applications requiring greater hardness, abrasion resistance, and chemical resistance since it can be cross-linked with a second component. Coatings formulated with Kynar Aquatec can be applied in the field to a variety of substrates—including metals, plastics, wood, concrete, stucco, EIFS, and previously painted surfaces.
Vinyl Ester Coatings
Vinyl ester resins are considered to be a cross between polyester resins and epoxy resins. They are best for corrosion-control and containment applications. Vinyl ester can be used for concrete and steel tank linings or as a concrete floor topping.
Chemify.com reports that the resin’s shrinkage factor, similar to polyester resin, is a main disadvantage.
Preparation for Coating
Before applying a coating to a concrete floor, you’ll need to ensure the space is clean, dry, and without any debris, moisture, or damage like cracks and holes.
Depending on the floor, you may need to sweep, clean, etch, or even patching the concrete surface to ensure a smooth and even application.
Application Process
Westcoat’s Tidalstone standard thin film system consists of their EC-12 epoxy primer. This is primarily designed for concrete applications.
After the concrete has been properly prepared to International Concrete Repair Institute guidelines of surface prep, they apply their EC-12 primer—a very nice, tenacious, moisture-tolerant priming agent.
Cost Considerations
Costs can range widely depending on the concrete floor coating you choose. Project teams should also consider how the size of the surface area, the type of coating, and the level of preparation required affects the overall cost.
Maintenance and Care
Depending on the coating, maintenance is minimal.
By utilizing an epoxy or resinous flooring like Tidalstone you will both save and extend the life of the concrete.
“A lot of times an epoxy flooring system is simply used to help preserve the integrity of the concrete. That way you’re not having to do these costly repairs because the last tenant, for example, did not have a coating down and that caused the materials or chemicals or exposure to water to rapidly expose the concrete to things that may now require it to be completely removed. That’s a much bigger environmental impact because now we have to cut out the concrete, remove the concrete, pour new concrete. If we utilize a protective coating, we can help eliminate and preserve the life of that concrete so it can go 100 years,” Westcoat Product Manager Todd Cook previously told gb&d.
Regular Cleaning
Depending on the coating, you should be able to easily and regularly spot clean your epoxy concrete floor with a soft cloth and a touch of Windex.
Floors that use polyaspartic and polyurethane finishes as final seal coats have really good chemical resistance, Cook says, so they can handle cleaning agents and exposure to tougher fluids and chemicals that might be found in, say, veterinary hospitals or a laboratory environment.
On the flip side, he says, “A light office space is going to have pedestrian traffic—they could get away with dust mopping. Bigger floors that might see more chemical exposure may have more stringent requirements—they might have auto scrubbers, flooring machines, things of that nature.”
Apply a new topcoat.
If you’re using Westcoat’s Tidalstone system, after it’s been primed they utilize their EC-102 Polyaspartic—UV-resistant, polyaspartic, fast-drying topcoat material.
“This will provide a high-service, UV-stable material,” Cook told gb&d. “By broadcasting into the EC-102 we have a UV stable base, as opposed to using standard epoxies or other materials that might be subjected to yellowing or ambering.”
Schedule periodic maintenance.
Schedule regular check-ins of your flooring to ensure it still has the look and durability you want. Westcoat’s Tidalstone Thin Film system and their High Build systems can last in the 10 to 20 years of service life.
“These are very durable, high-performance coatings, but like anything they require a little bit of maintenance and upkeep. Every five years or so depending on use and exposure, you would lightly clean the surface and abrade it.
“You could reapply a clear coat of SC-65 and that would extend that service life even further. Essentially that final coat is the sacrificial coat; it’s the layer that takes the burden off the whole system, like a clear coat on a car or a wax. It helps prevent wear. As long as it’s maintained it can last a very long time.”
How to Choose the Right Coating
With so many coatings, it can be confusing to know which to choose for your residential or commercial project.
Coatings like Westcoat’s solar reflective Texture-Crete topcoat can be applied over both solar reflective and non-solar reflective systems. It can also bond to concrete walkways and pool decks without waterproofing systems.
Here is a step-by-step guided to choosing the right coating for your project.
Consider the application.
Evaluate the surface condition.
Research the different types of coatings.
Consider the color and finish.
Think about maintenance.
Set a budget.
Hire a professional.
Get samples.
Conclusion
At the end of the day it’s important to consider your options and understand your needs before choosing the right concrete floor coating.
“A lot of us forget best practices can include small things like … choosing the right system. Frankly, that’s one of the most important aspects here—taking the time to evaluate what you need for your facility,” Cook says.
Whether it be an office, school, laboratory, hospital, vet clinic, whatever—Westcoat wants to have that dialogue with the design team or facility manager ahead of time so they can give the proper recommendation.
“So many times we see in our industry that a design team chooses the lowest bid or a system recommendation that isn’t appropriate for the space. That’s not sustainable. Now you’ve chosen an inferior system that was not suitable for chemical exposure or high traffic,” he says.
“If you pause and reflect and specify and utilize the correct system from the beginning you’ll have a system that’ will most likely hold up very well, be a lot easier to maintain, and be a suitable alignment based on the requirements of the facility and attributes required.”
Laura Rote contributed to this article.