Story at a glance:
- PIM software from Newforma streamlines emails and production schedules so teams can find project information quickly.
- Choosing eco-friendly, durable products is easy when you look for Declare Labels.
- Protecting the outside of your building goes beyond coatings; it starts with the initial inspection.
Construction delays, obliterated budgets, poor communication, subpar materials. These are just some of the issues that plague projects all over the world, but those who’ve been in the industry a long time know it doesn’t have to be that way.
With thoughtful planning and the right resources, most projects can avoid major setbacks and mistakes from ever happening. These are some of the top construction tips and tricks we’ve gathered from the experts over the years.
1. Get organized.
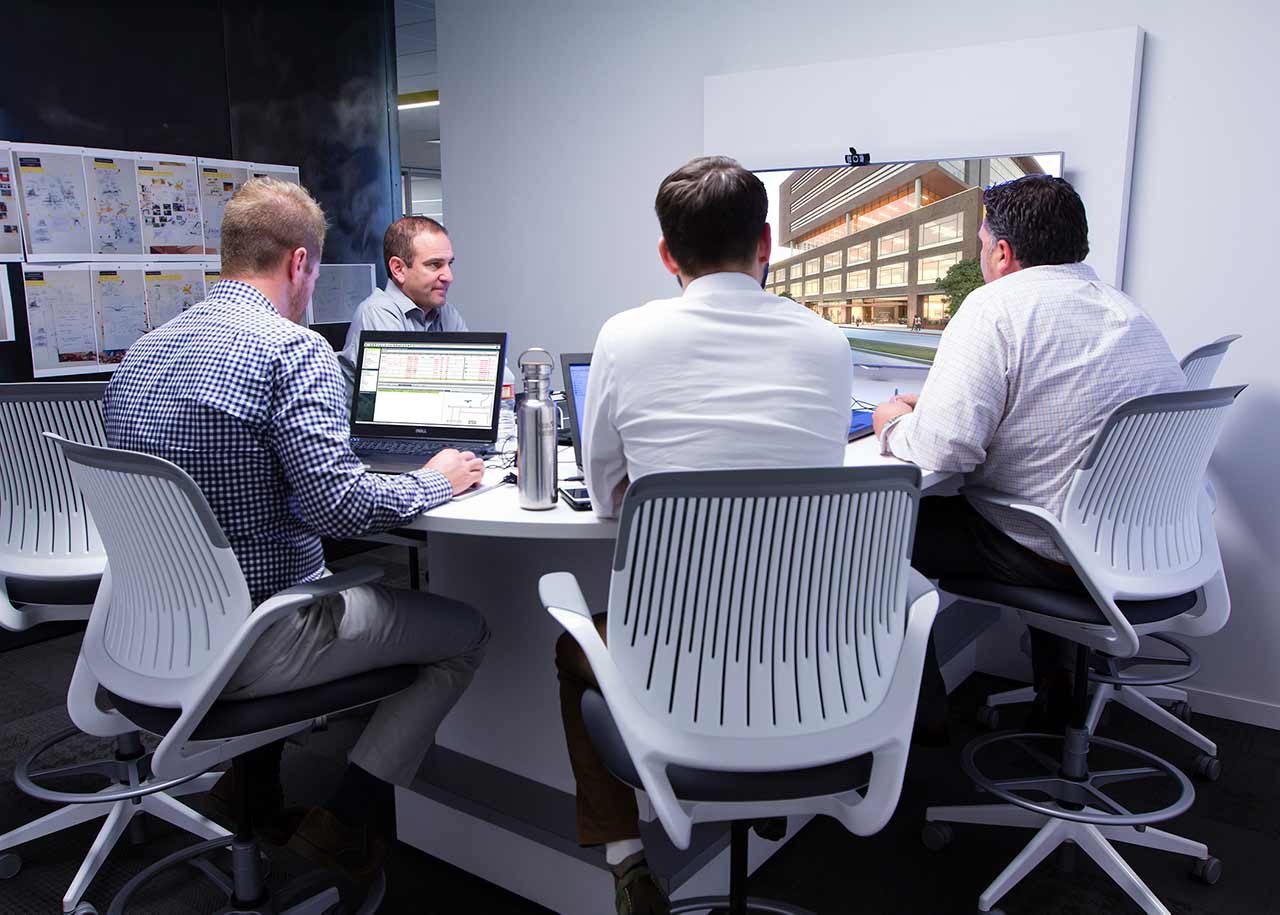
Corgan team members at work, using Newforma software. Photo courtesy of Newforma
The list of construction tips and tricks might easily start with streamlining services and allowing service management software to do a lot of the work for you. Companies like IFS offer optimized planning, remote assistance, and take an integrated approach to services.
You can also improve project workflow with project information management (PIM) software like that of Newforma. Newforma Project Center helps design teams organize and find project information quickly and easily.
Architects and engineers often have complex folder structures containing terabytes of data generated per project that become difficult to search and manage. “Newforma’s server is looking at all of the content of those folders, indexing the information, and then providing a way for users to search that material,” Aaron Kivett, solution consultant at Newforma, said in a previous interview with gb&d. Newforma offers email management, risk mitigation, and more.
2. Use BIM.
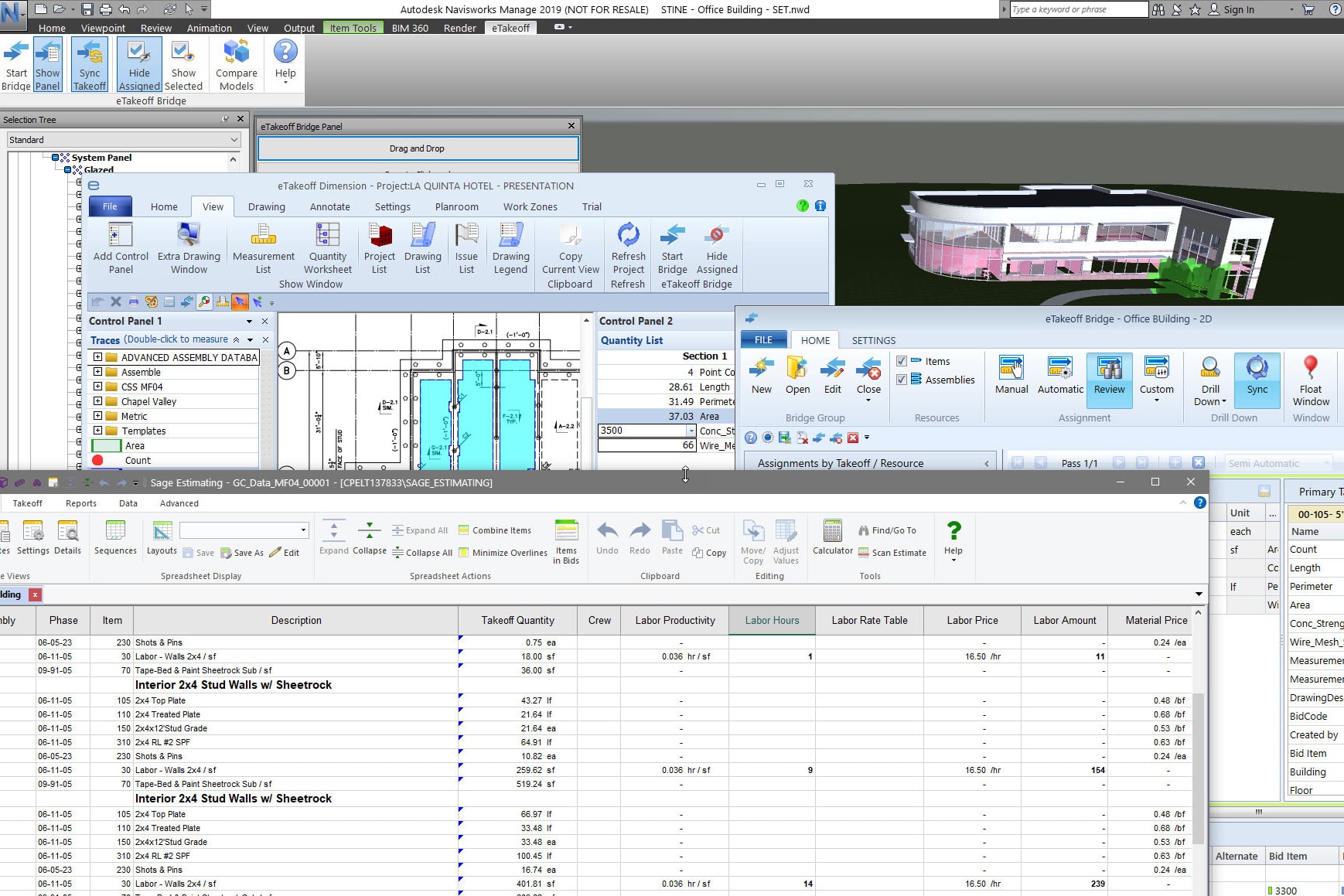
Building Information modeling in action. Photo courtesy of Sage
As the experts at Sage know, BIM helps to eliminate a lot of common construction and design headaches, including issues surrounding cost, schedule, constructability, and rework. BIM also facilitates collaboration with your entire project team so you can do more work faster.
According to a gb&d article by Sage’s Dustin Anderson, BIM saves time and reduces repetitive work. “It gives you access to model information that you can put into your estimate quickly, so you can spend less time on model takeoff. For example, it allows you to link construction objects from a model directly to assemblies, like walls, in an estimating database. This provides you with time-saving shortcuts, such as taking off all 3-5/8 metal stud walls in a single step,” he writes in the article.
3. Determine your materials’ sustainability.
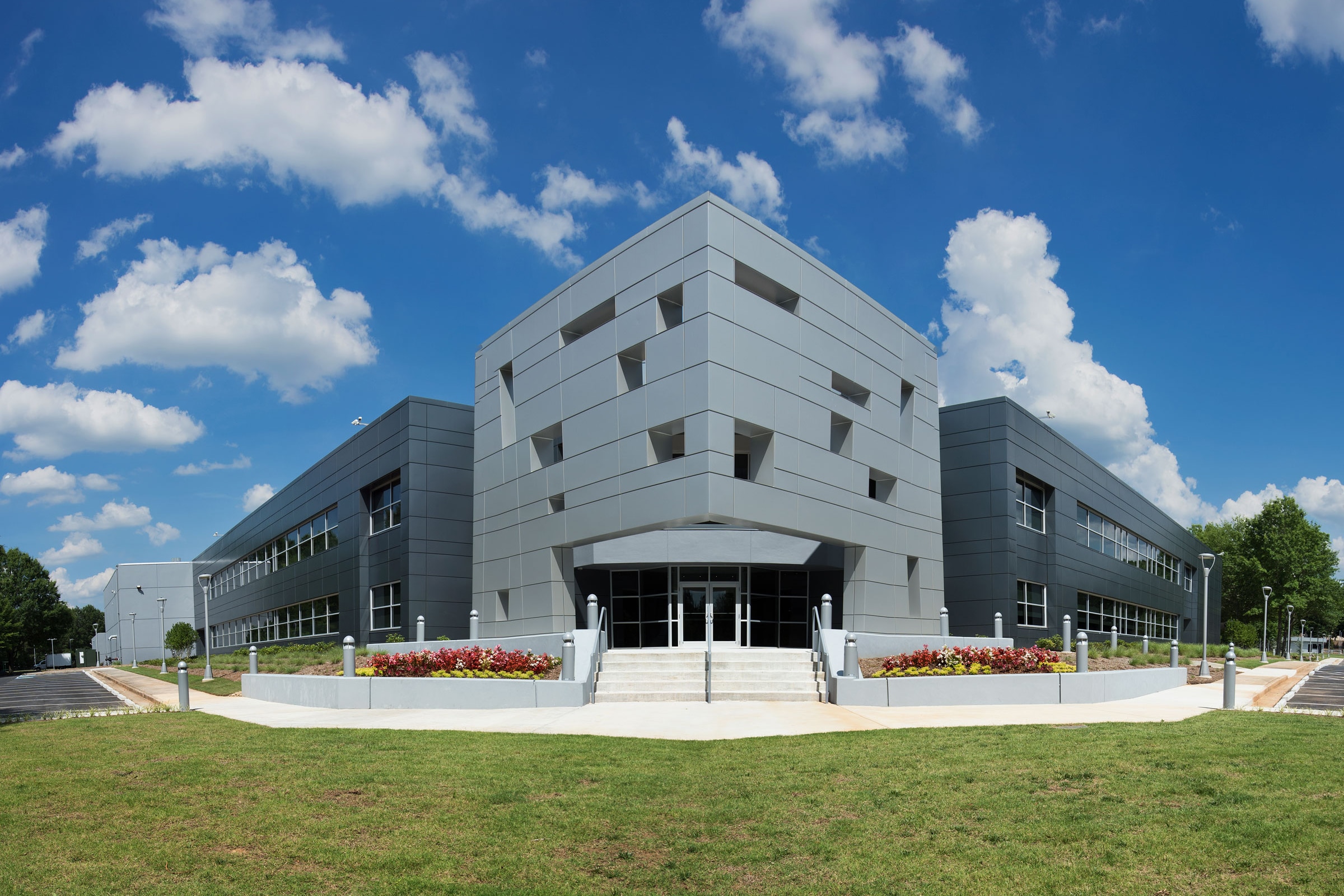
Two colors of Intercept—Silversmith and Gray Velvet—were installed at Acuity Brand Lighting’s Engineering and Technology Center in Decatur, Georgia, to help create a cutting-edge work environment. Photo courtesy of CENTRIA
Are you really incorporating sustainable building materials and products for your project? Check their credentials and look for Declare Labels.
Developed by the International Living Future Institute (ILFI), a Declare Label reveals a product’s source location, the materials that make up the product, and how the product is treated at the end of its life.
“Declare Labels provide lots of details, including the final assembly location of a product and end-of-life options,” writes Steve Marziale, product engineer at CENTRIA, for gb&d. “ILFI then publishes a full list of the product’s ingredients on a Declare Label, all provided by the manufacturer. This includes ingredients that come without restrictions and an analysis of what are called Red List chemicals (if they are present in the product).”
4. Plan for disaster.
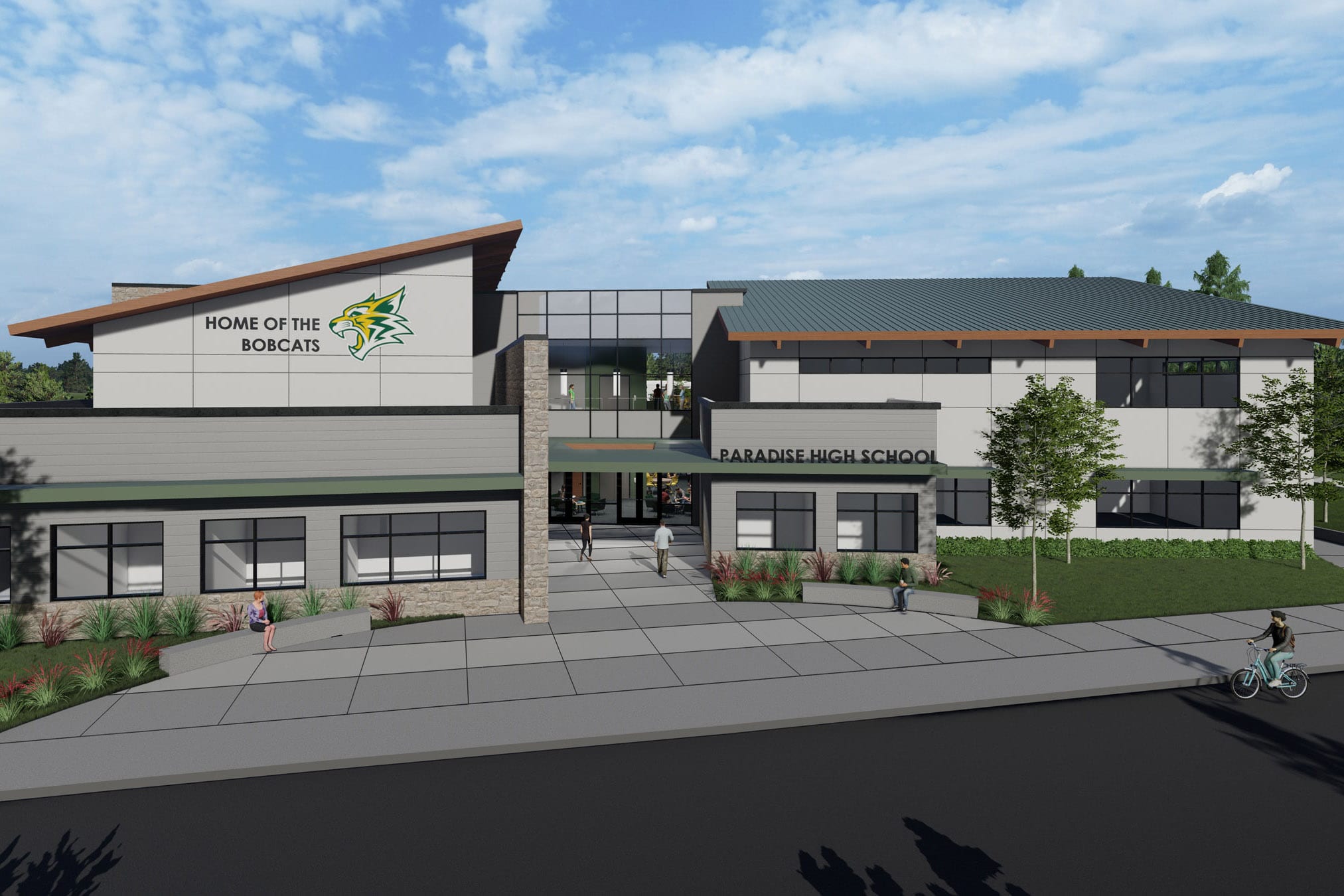
The new Paradise High School Classroom and Administration Facility. Image courtesy of Studio W Architects
Being prepared for the worst is one of experts’ top construction tips and tricks—and it can save you a lot of heartache later on. This includes having things like conditions assessments—something Studio W and the Paradise Unified School District in California know all too well.
“Studio W was initially hired in 2017 to complete a conditions assessment and develop a master plan to assist Paradise Unified School District,” Brain Whitmore writes in a submitted article for gb&d. “We went through the facilities assessments, set the conditions of all of their sites—architecturally, structurally, electrically, mechanically, and so forth—and developed a list of project needs and prioritized projects based on the funding at that moment. The district wanted to increase, enhance, and improve the physical condition of their schools.”
It was all before a massive fire tore through the region, destroying much of the district’s facilities.
“We would encourage every school district to go through this process, just like what we did with Paradise before the fire, so they have an up-to-date assessment. Having allowed Paradise Unified School District to know exactly what they had and how they might rebuild after the disaster. Having a master plan already drawn up saved them a lot of time because a lot of their priorities did not change even after the fire; they still wanted enhanced education facilities and modernized athletics, for example.”
5. Protect concrete slabs and floors with a moisture barrier.
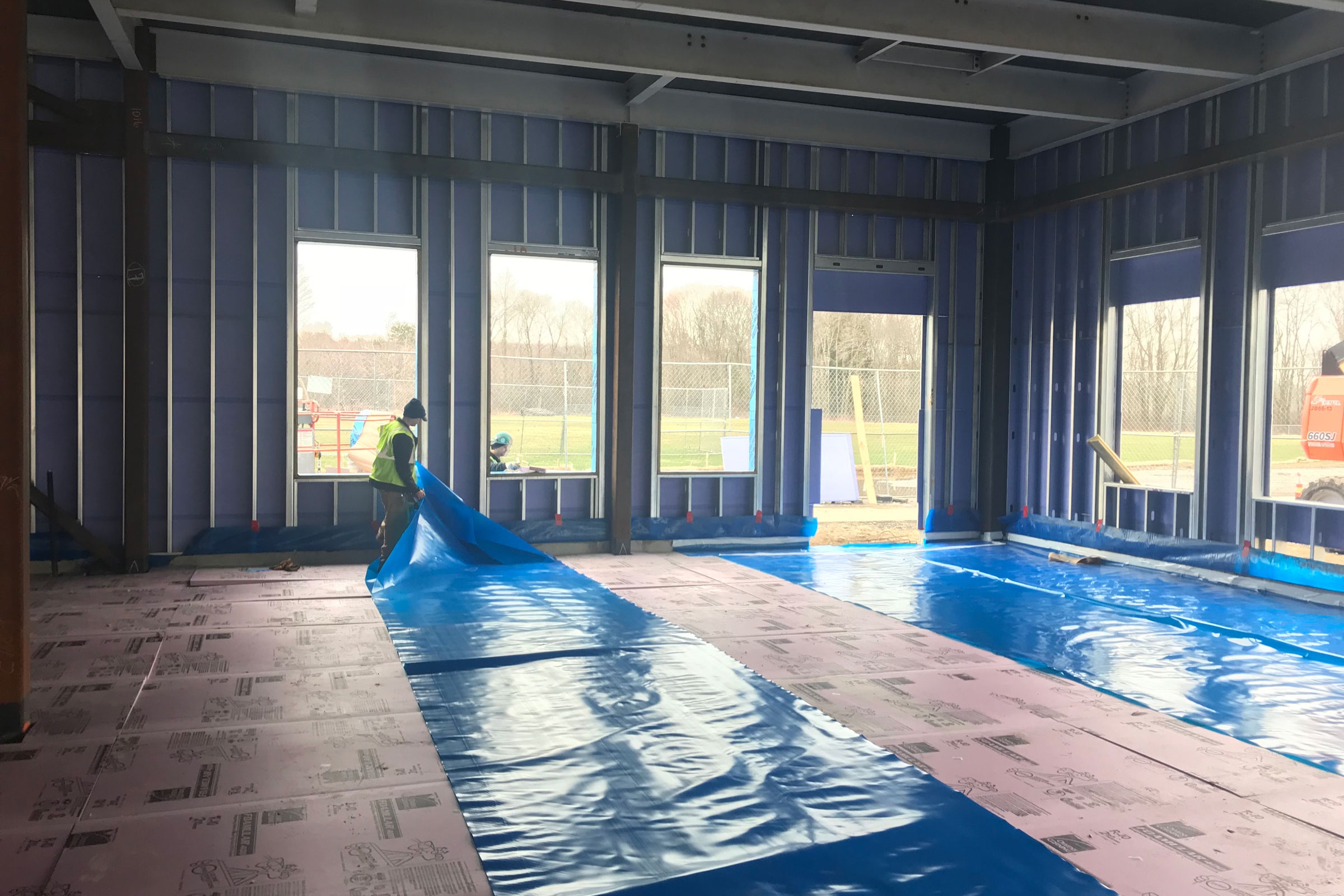
ISI Building Products’ Viper II 15-Mil being installed in conjunction with foam board insulation. Photo courtesy of ISI Building Products
Your foundation is vital, but what good is a strong foundation if it’s not protected from moisture? According to the pros at ISI Building Products, below slab water vapor remediation after-the-fact is a complicated and costly fix. They say choosing and properly installing the correct below slab water vapor protection is imperative to your finished floor and overall health and safety.
Industry organizations like American Concrete Institute (ACI) and the American Society for Testing and Materials (ASTM) have produced specific guidelines and testing standards for under-slab water vapor retarders and barriers.
For example, ASTM E 1745 (Standard Specification for Plastic Water Vapor Retarders Used in Contact with Soil or Granular Fill under Concrete Slabs) is a testing standard used for determining a product’s performance. ASTM E 1745 classifies materials as A, B or C based on the products puncture resistance, tensile strength and water vapor permeance. Class A vapor retarders and barriers carry the highest puncture resistance and tensile strength, with Class C being on the lower end of the scale. The water vapor permeance requirement is currently set at 0.1 perms for all three classifications making the separating factors puncture resistance and tensile strength.
6. Assess carbon.
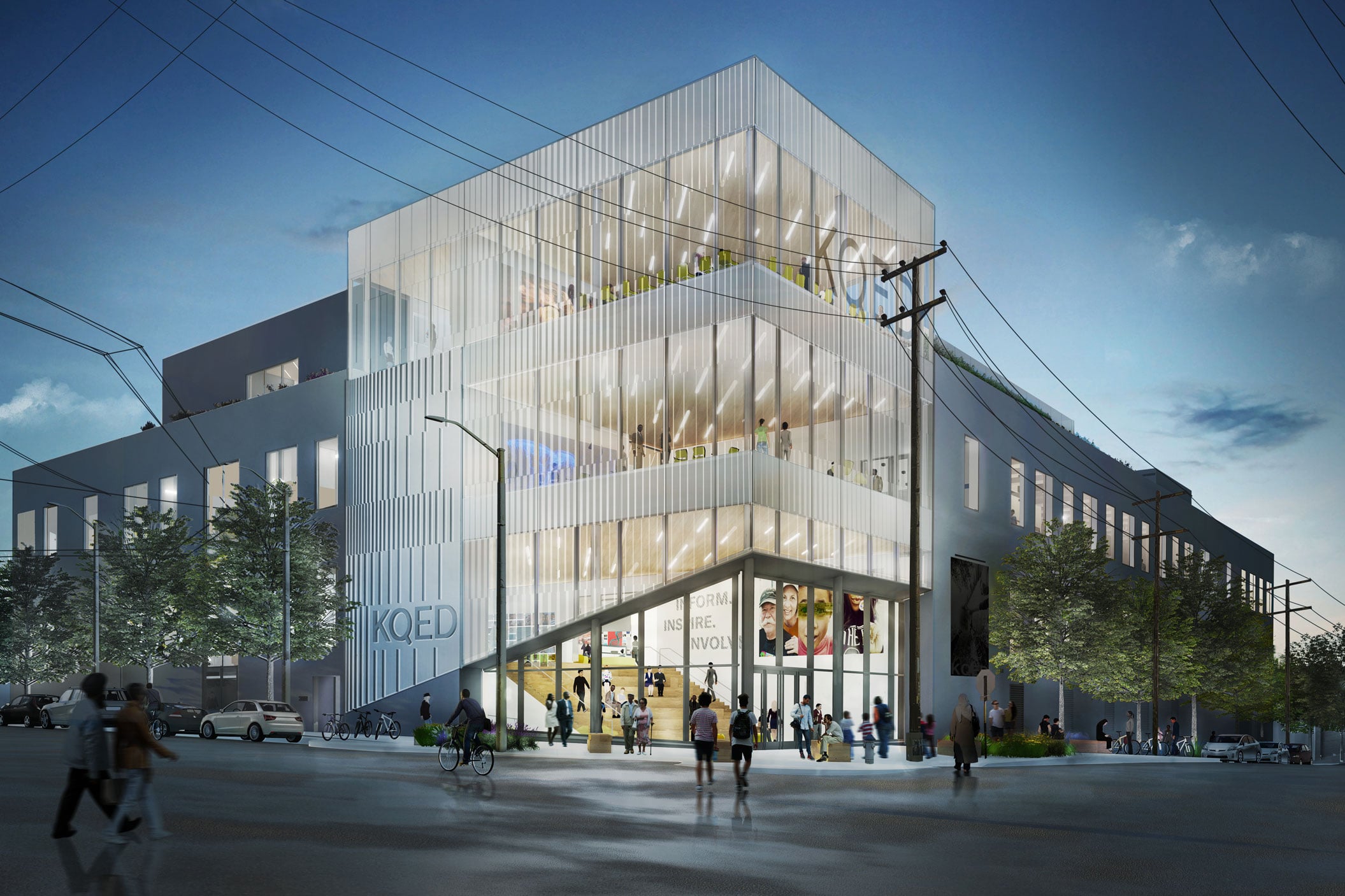
EHDD’s redesign transforms KQED’s headquarters into a hub for civic engagement and contemporary journalism. A dynamic new entry reinforces the public media station’s commitment to transparency and accessibility. Photo courtesy of EHDD
For another of our construction tips and tricks, you can use a carbon assessment tool like EPIC, recently introduced by EHDD. It allows EHDD designers—and eventually, their clients—to set carbon targets and identify the most impactful measures early in the project process.
“We see this as complementary to life-cycle assessment and product optimization tools like Tally and EC3, which are crucial later in design,” writes Brad Jacobson in an earlier contribution to gb&d.
Currently in beta testing, the EPIC tool “brings together operational and embodied carbon impacts and potential sequestration measures, on a level playing field and measured over a project life cycle so we can see more clearly where we get the biggest, and most immediate, bang for the buck,” Jacobson says.
7. Opt for a sustainable plumbing system.
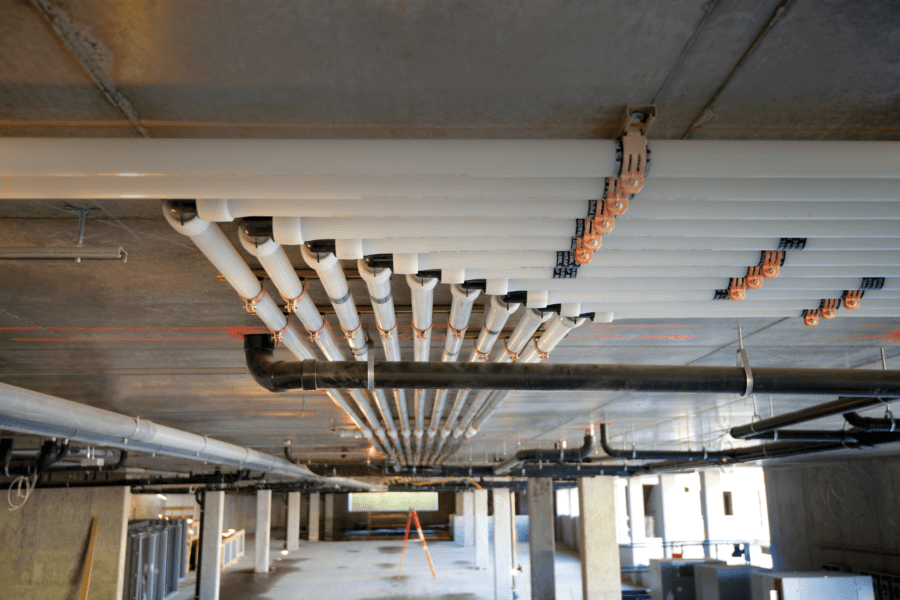
With an offering in sizes up to 4 inches, using PEX in commercial applications is challenging traditional copper, steel, and CPVC piping materials that have dominated the commercial building industry for the past century. Photo courtesy of Uponor
Save money in the long run with an efficient plumbing system. Devin Abellon, PE, business development manager for engineering services at Uponor, says PEX Pipes are more sustainable than copper and other piping materials because cross-linked polyethylene pipes are a flexible, durable, and cost-effective polymer piping product for domestic water, hydronic distribution, and radiant heating and cooling applications for both residential and commercial applications.
In 2016 the Journal of Cleaner Production published a report based on the life cycle assessment comparing the economic and environmental performances of PEX and copper pipes over the life cycle of a student housing project in Lancaster, Pennsylvania. The results of the analysis indicated using PEX instead of copper piping systems would considerably reduce the total cost of the building up to 63% over its life cycle while reducing the carbon dioxide emissions by approximately 42% and lessening the negative effect of environmental impacts to land, water, and air.
8. Protect your exterior.
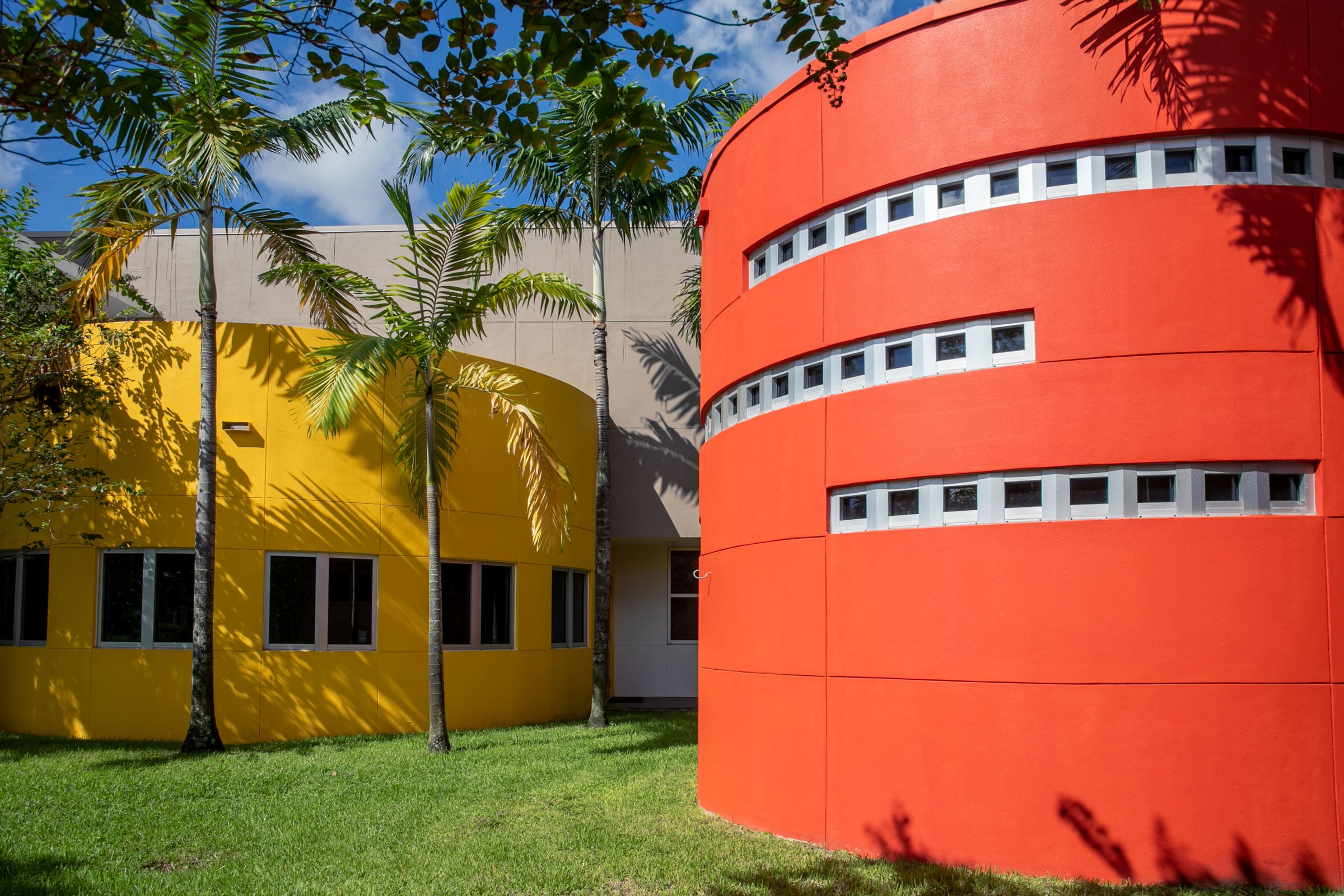
With the help of Restore Construction Group and APV Engineered Coatings, the Children’s Ability Center will be able to keep its colorful facade for years to come. Photo courtesy of APV Engineered Coatings
Of course, what’s on the outside counts, too, when it comes to construction tips and tricks. Preparing buildings with the proper protective coatings can preserve them for many years to come, according to APV Engineered Coatings. But their experts say not everyone does this correctly, and careful pre-inspection of a project makes a big difference when it comes to mastering the top construction tips and tricks.
“Together with our certified contractor, we act as inspectors on the job,” Erin Brown-Neff, director of marketing and business development for APV Engineered Coatings, previously told gb&d. “We go to the job site, see the unique situation on the project, and use NACE, SSPC, or ASTM Standards to specify how the surface should be prepped.”
Rex Dean, global director of façade restoration at Stuart Dean, says they first determine the type of substrate that needs coating and the existing coating system—if there is one. They then test the surface for adhesion to see if a new field-applied coating system will anchor to the current coating. When that’s done, surfaces are tested for environmental contaminants like chlorides, sulfates, and nitrates—which are removed if they’re present. Next up: the creation of an “anchor/surface profile.” That can be achieved by hand abrasion, mechanical tool abrasion, and blast abrasion.
Ultimately, if you’ve done a thorough pre-job assessment and selected a knowledgeable contractor that works directly with the coating manufacturer, issues should be minimal-to-nonexistent, Brown-Neff says.
“When a customer is incorporating NeverFade® into the spec, they’re sourcing a product that is going to increase the life cycle of the facade, so we want to make sure they’re getting what they’ve asked for.”
Submit your construction tips and tricks to lrote@gbdmagazine.com to be considered for a future article.