Story at a glance:
- BSA LifeStructures is a national, integrated design firm that shares their keys to successful early planning in construction.
- BSA LifeStructures provided in-house architecture, MEP planning, and landscape design at Notre Dame’s McCourtney Hall.
- The McCourtney Hall project achieved LEED Gold versus its initial target of LEED Silver.
Programming and planning efforts are typically exercises to get everyone on the same page concerning programmatic priorities and budget limitations. Yet this phase should also be approached through a lens of sustainability.
If done correctly, the process will allow the focus to be on the benefits of avoiding overbuilding (program efficiency), creating functional adjacencies (shared spaces), planning for efficient systems (sustainable and green), and return on investment as well as setting standards for materials, equipment, and the environment.
Here’s what to consider in the early planning in construction process before your next health care project.
Don’t overbuild.
You’ve heard it said before; Lean is green. Avoid overbuilding.
The benefits of not overbuilding a research space include energy savings and material savings that you’ll be able to apply in upgrading your lab spaces.
Rightsizing a building can be emotional. There’s a delicate but necessary balance between diplomacy—managing needs versus wants—and planning that is backed by evidence.
Utilization studies should inform the basis of occupants’ space requirements, both today’s needs and future needs. Lab planning professionals account for planning standards, class schedules, research grants and focuses, and projects of growth or retraction. A gap analysis that’s part of a utilization study will reveal areas of underutilization and crowding.
At Miami University in Ohio, space planners were able to achieve enough real savings through utilization data to specify linoleum flooring in the research labs. Not only is the linoleum sustainable, but it can also help prevent fatigue in researchers who can be on their feet for most of the day.
Create functional adjacencies.
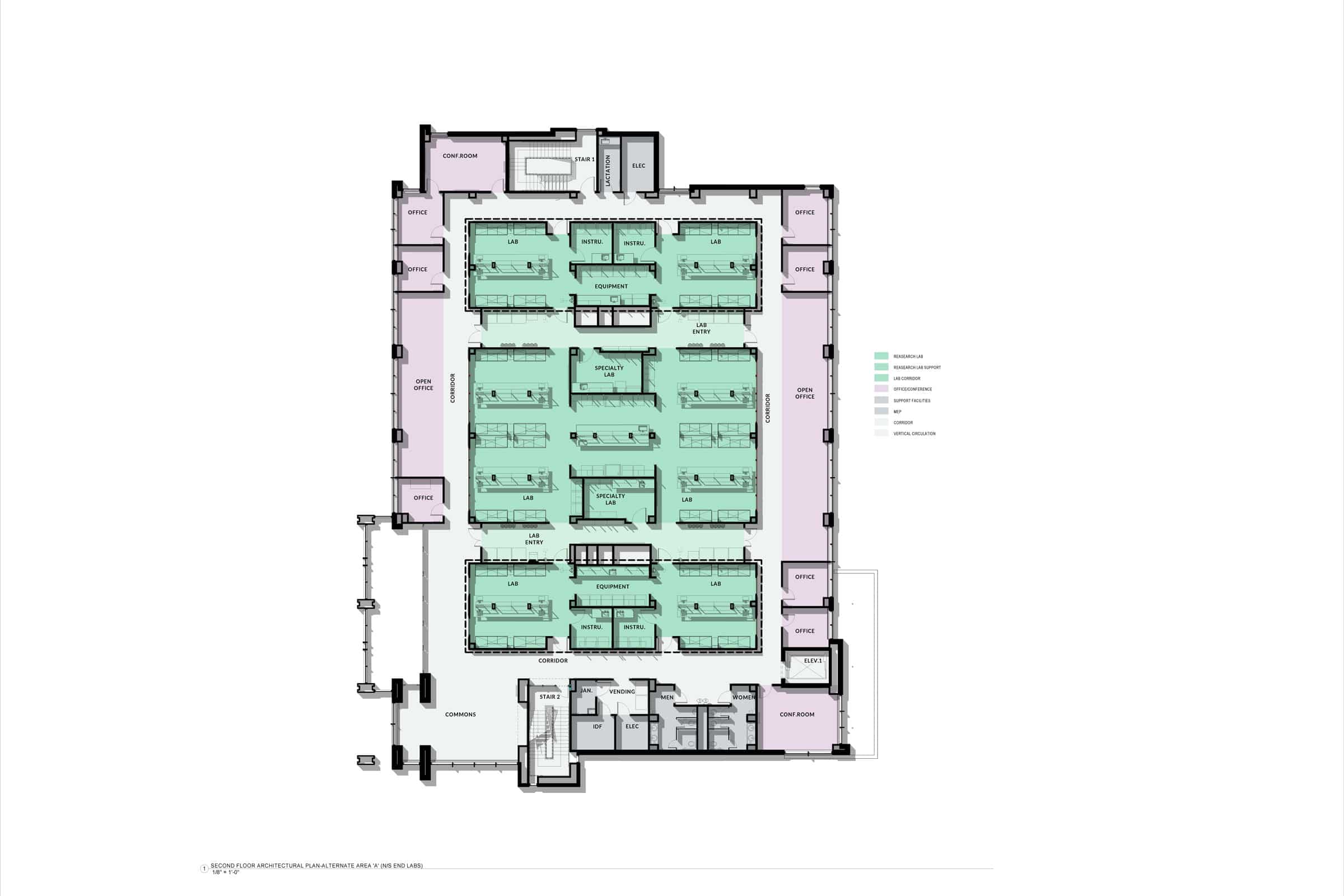
At Purdue University, centrally located support labs maximized efficiencies and lowered the carbon footprint. Plan courtesy of BSA LifeStructures
Opportunities for shared spaces also rightsize space allocations and reduce redundancies.
At the Institute for Drug Discovery on the campus of Purdue University, shared support facilities were designed in the center of the floorplate to maximize the adjacencies for the most-frequent users.
The resulting savings in square footage lowered the carbon footprint, created lean processes in the research environment, kept additional materials out of the landfill during construction and created more green space on the campus.
In a similar fashion, the shared core facilities at Purdue’s new engineering complex, Lambertus and Dudley Halls, led to optimal plan configurations for efficiency, daylight capturing, and collaboration.
Study areas were located next to faculty offices and allowed natural light to be delivered deep into the building to circulation areas. This space-planning model influenced the design of the floorplan throughout the building. Some iterations differed, yet the base idea held function.
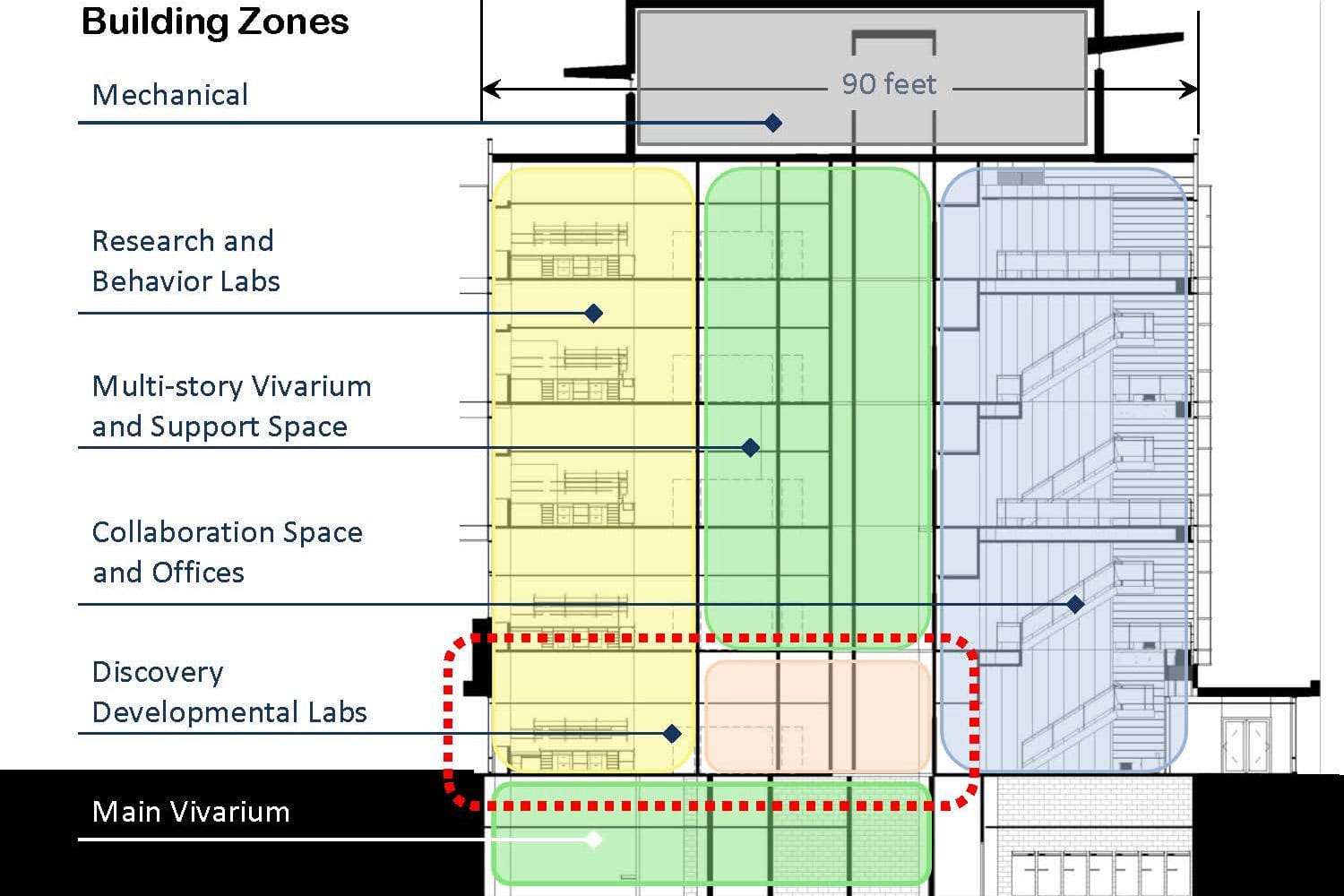
The vertical vivarium at the Stark Neurosciences Research Institute resulted in energy efficiencies. Image courtesy of BSA LifeStructures
Vertical adjacencies allow for animal holding rooms adjacent to the laboratories and main supporting spaces. Principal investigators and researchers have immediate access to animals without leaving their lab area. The mechanical system’s vertical configuration is extremely efficient, saving on operational costs.
Set standards for materials, equipment, and the environment.
Establishing room design criteria is also a vital facet of pre-planning.
Room criteria sets the stage for selecting sustainable materials and finishes and for meeting MEP requirements.
Although standards and codes must be followed, they sometimes allow for interpretation.
For example, when you’re choosing between epoxy flooring and rubber flooring, rubber offers sustainability. It’s renewable, low-VOC, anti-slip, bacteriostatic, and you can clean it with water rather than chemicals. That said, rubber is not always appropriate or allowable.
Remember the building systems.
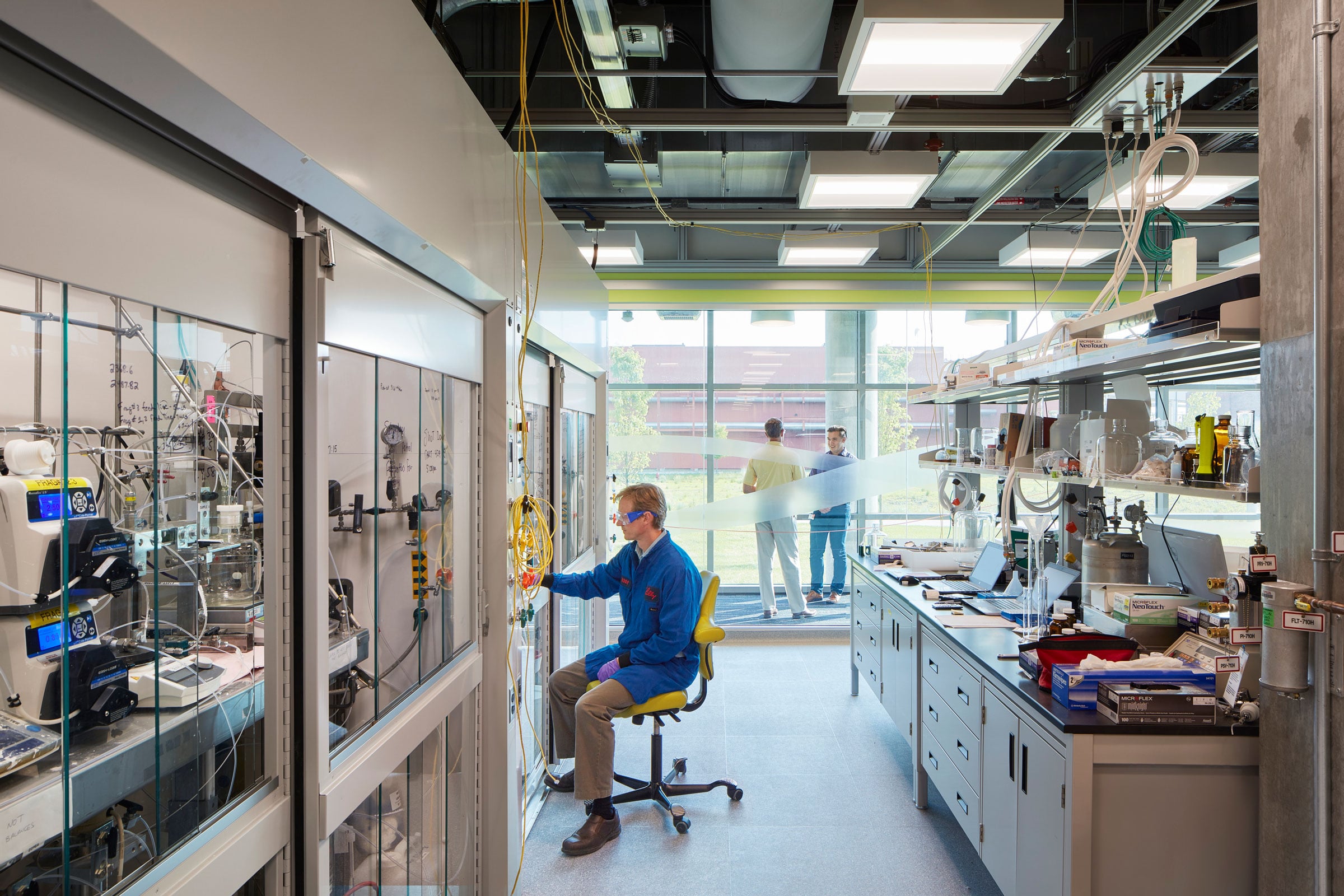
A modular approach to mechanical design resulted in an annual savings of nearly $1 million in reconfiguration costs. Photo by Mark Herboth Photography
R&D facilities are often reconfigured to keep pace with changing research.
At an unnamed Fortune 500 corporation, reconfiguring 42 lab arrangements over three years cost $2.7 million. At the firm’s new Innovation Development Center, preassembled modules were designed to provide all major MEP infrastructure throughout the labs. The modules were the MEP infrastructure “fingers” throughout the space, providing water and lab gasses, electrical bus duct, telecom cables, and exhaust ductwork.
Technicians can quickly connect hood ventilation lines in a variety of locations, and 10% of the hoods were reconfigured within 18 months. It would’ve cost $750,000 if this new facility had been designed as the previous one was—and that doesn’t include the design, demolition, and reconstruction that would have been necessary. Modular design allowed these configurations to occur in a matter of days at no additional cost. Prefabrication also accelerated the construction schedule, reducing costs by more than $70,000 and saving more than 3,000 onsite labor hours.
Case Study: McCourtney Hall at University of Notre Dame
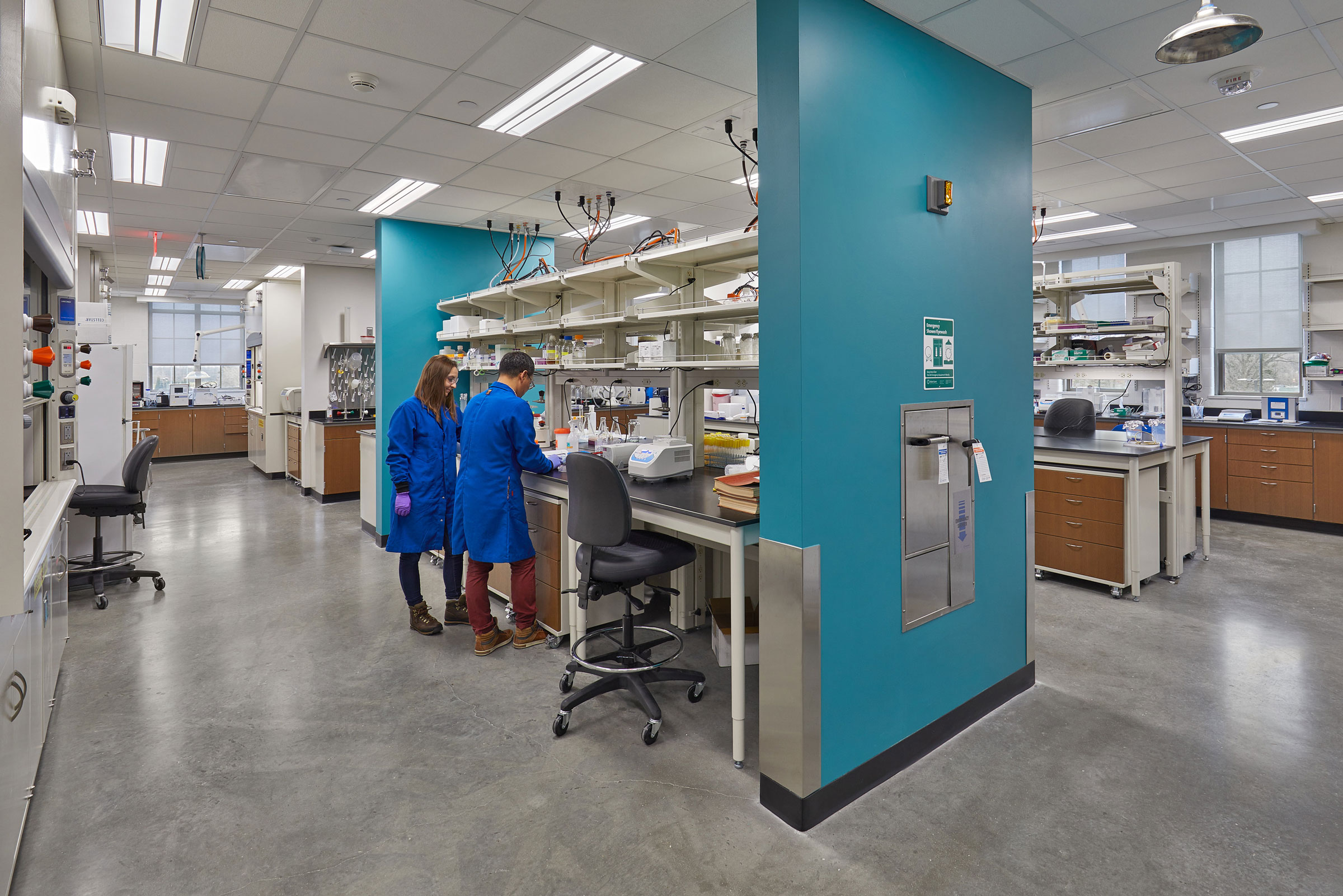
Inside Notre Dame’s McCourtney Hall. Photo by Frederick | Julius Photography
McCourtney Hall at the University of Notre Dame exemplifies how early planning helped establish a high-profile, flexible, collaborative lab space.
The building houses combined labs for the colleges of science and engineering and supports analytical sciences and engineering, chemical and biomolecular engineering, and drug discovery. This particular building is meant as a high-profile home for advanced research. It encourages collaboration between different fields and inspires novel research while providing a foundation for original research that might not have occurred in a more traditional, siloed setting.
McCourtney Hall is approximately 200,000 square feet, one-half of which consists of open lab and team spaces. It has a collaborative core for offices and informal interaction. Initially 40% of the building was reserved as shell space but is now nearly entirely built out. The project cost $61 million to build, or about $280 per gross square foot. The building occupies four floors with a basement level and a mechanical penthouse on top.
Interdisciplinary design made this project possible. From its beginning, there were four major goals: architectural impact, LEED certification, systems flexibility, and energy conservation.
For architectural impact, the idea was to make a statement on campus while establishing a modern laboratory presence. Early planning in construction of this project initially included a minimal target of LEED Silver. The systems needed to support a broad range of cutting-edge research and adapt to research needs over the next 50 to 100 years. This building needed to have a long life. Conserving energy was essential for this high-energy usage building type. This was achieved via a focus on responsive controls that deliver energy and services when and where they’re needed. BSA LifeStructures provided in-house architecture, MEP planning, and landscape design to provide a holistic, cohesive design that met these four goals.
Early planning and architectural drivers help support those project goals. McCourtney Hall is a foundational building in establishing a presence in a newly developed area of campus, as part of the master plan. One idea was to blend the exterior design with the campus’ style, which is akin to Collegiate Gothic. The building needed to provide a program to meet the needs of two different schools, while encouraging cross pollination and collaboration in research between them.
It also needed to make a statement to help put Notre Dame on the map and attract top research talent. McCourtney Hall is the cornerstone of what Notre Dame envisions as a new R&D quad. Early on engineers helped establish the new campus utility distribution loop to this quad, one that utilizes the campus’ geothermal development.
From an exterior architecture standpoint, the university challenged the design team to create a building that looked like it has been around for 100 years and was then renovated to become a modern lab. The design team adapted this collegiate Gothic style to accommodate the modern laboratory program. The gables conceal the fans and hide the heavy HVAC equipment needed to support the lab.
Shape collaboration.
Early on in the design, the team created a concept of neighborhoods to support collaboration between engineers and scientists from Notre Dame’s various schools. This plan was partially inspired by the L shape of the building and its presence as the new R&D quad. These neighborhoods consist of shared space, shared core labs and dedicated spaces. The neighborhood concept also incorporates labs as modules that can be easily slotted into any shell space and reconfigured as needed, allowing researchers to plug and play.
The building’s shape, the knuckle, became a unifying design feature and as a collaboration destination. The knuckle includes a public zone where researchers can gather, offices for graduate students, and where conference rooms are located. The buildings wings serve as non-public zones, except for the first floor. Labs closest to the knuckle are more standardized for the sharing of space and equipment; labs further from the knuckle are specialized. This space planning served as a project roadmap for initial design and construction as well as future lab module buildouts of the shell space. A mini atrium within the second-floor knuckle connects the second and third floors. Interior finishes evoke a raw, industrial feel, while not distracting from the building’s research mission. The flexibility concept that’s so central to the neighborhoods extends to interior ideas such as movable screens that allow users to reconfigure these common areas to fit their needs.
The MEP systems in McCourtney Hall were designed to optimize flexibility and efficiency while supporting the neighborhood design theme. Early collaboration between engineers, architects, and planners made this possible. Ductwork, for example, is manifolded in size to allow supply and exhaust flexibility anywhere in the building.
The flexible approach led to a fume hood plan with a maximum number of connected fume hoods for the entire building, regardless of their specific location. The team conducted a wind study as part of the early planning in construction to help locate and size the exhaust stacks for safe exhaust of hazardous chemicals.
Variable frequency drives allow operation along many operating points for all air handling unit fans, exhaust fans and pumps. Low-pressure drop coils and filters help reduce fan power ad energy use. The use of mechanical controls creates a highly responsive system, using energy and air only when and where it is needed. A variable air volume exhaust is present, a fume hood occupancy setback. A supplied air temperature reset exists that enables the HVAC system to be turned down, should an emergency warrant it, but still provide service to critical spaces.
The plumbing infrastructure uses centralized systems to allow easier maintenance and enable easier relocation of services as lab needs change. One of the central design features that allows this laboratory flexibility are the ceiling interface panels. The services are provided at easy connection points in the ceiling for quick connection and relocation. The flexibility is also supported by typical locations for emergency stations and sinks. Energy efficiency abounds here as well. Localized vacuum systems, variable-speed air compressors, low-flow water fixtures and metering on a nitrogen tank measured by a central monitoring system are examples.
On the electrical side, the design of McCourtney Hall allows moving and relocating pieces of equipment to accommodate changes in laboratory equipment needs, enable plug and play functionality, and improve maintainability through a main-tie-main service, draw out switchgear and use of raceway ceiling interface panels and busway within labs. There is also an emergency system designed to provide resiliency to support critical research. An emergency generator and redundant electrical system to reduce disruptions in the electrical supply is also present.
The building’s lighting system is entirely LED, 40% better than code at the time the project was built. Daylight and occupancy sensors carefully control energy usage, while allowing users to override the controls as needed.
LEED with pre-planning.
How did all of this early planning in construction affect LEED? The project achieved LEED Gold versus its initial target of LEED Silver.
The project achieved resource savings of 26% for energy and 30% for water. Given this project’s focus on control and verification, there are a number of credits that were important to achieve, including the lighting and thermal comfort credits and outdoor air delivery monitoring. Enhanced commissioning, measurement, and verification to make sure those systems are functioning well after constructed—and as designed—was critical.
Lean is green, and green pre-planning is essential. Early planning that brings designers, engineers, contractors and owners to the same table results in energy and material savings that translate into upgraded lab spaces equipped to serve researchers today in in the future.