Story at a glance:
- Exterior wall cladding materials have expanded to include the unexpected, from innovative terra-cotta to MCM.
- Brick continues to be a popular cladding material for its durability and inherent thermal properties.
- Many architects choose wood for its aesthetics, including sustainably sourced wood that’s specially modified.
Exterior wall cladding materials have evolved beyond the perhaps more expected brick or wood. While brick and wood continue to be beloved, architects and designers are also turning to solutions like metal composite material and exciting terra-cotta solutions.
Here are some of the most popular exterior wall cladding materials and why architects today might consider these options.
What is Exterior Cladding?
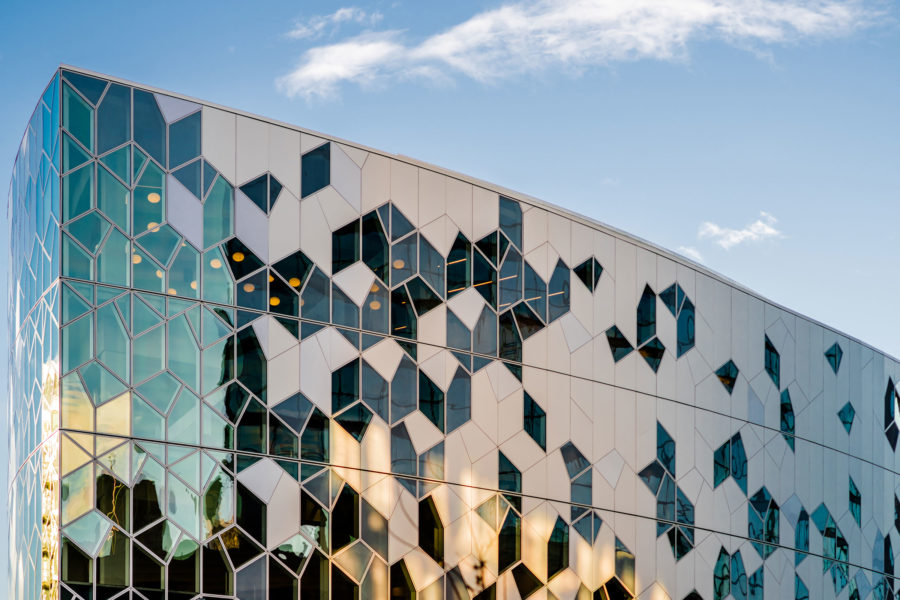
Interspersed with the glass and natural wood accents, ALPOLIC MCM creates a lace-like effect across the building’s facade. Photo courtesy of MCA-ALPOLIC Division
In the fundamental sense cladding can be described as the external material used to both beautify and protect a building’s exterior from the elements. Historically wood, stone, and brick have been some of the most popular forms of cladding, but modern technological advancements have expanded the possibilities when it comes to protecting a building’s envelope.
What’s the Difference Between Cladding and Facade?
Before we review the different types of cladding, let’s take a moment to talk about how exterior cladding differs from facade.
- Cladding refers exclusively to the material that protects a building’s entire exterior while also providing some measure of aesthetic and design value.
- Facade refers solely to the building’s exterior appearance—particularly the side that faces the street; this includes cladding as well as any other design elements like windows, cornices, pillars, gables, etc.
What are the Most Popular Types of Cladding Materials?
Here is a guide to some of the most popular types of cladding materials, as well as their advantages and disadvantages.
Terra-Cotta
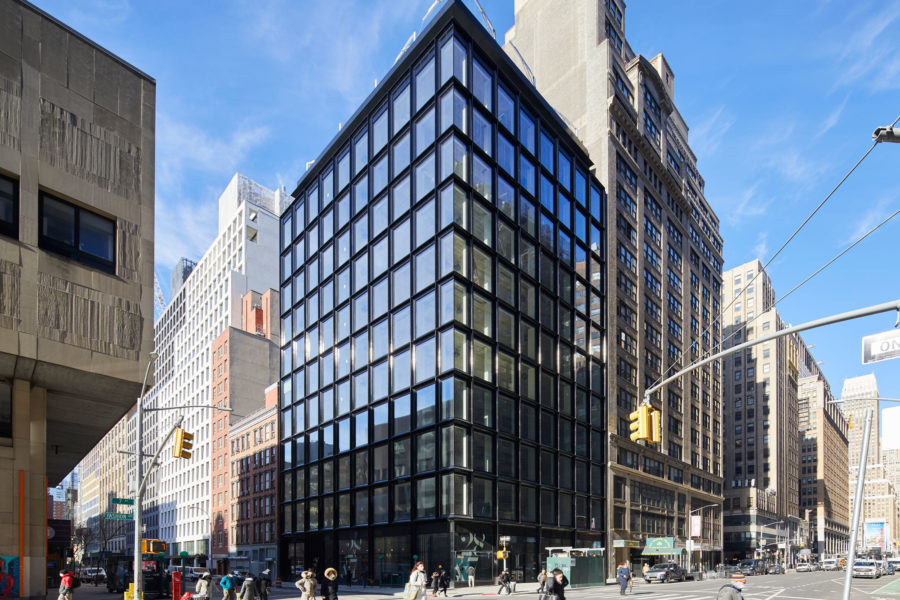
The facade at 28&7 was manufactured in a zero-waste, low-energy process, designed by Shildan Group with a custom glossy black glaze that visually highlights the structural grid. Photo by Dave Burk, courtesy of SOM
Skidmore, Owings & Merrill (SOM) chose a surprising black glazed terra-cotta from Shildan Group for its 2022 project, 28&7, in Manhattan. The 28&7 facade draws inspiration from the neighborhood—an area rich in 19th- and 20th-century masonry buildings, with a cladding selected for both its customizable and sustainable properties.
“We knew from the get-go that we wanted a black building,” said Michael Kirchmann, CEO and cofounder of GDSNY and a former SOM architect, in a previous article for gb&d. He said the black punctuates the building’s prominent corner in a way that gives it even more presence.
SOM had worked with terra-cotta before, collaborating with Shildan Group on another NYC project that incorporated white glazing. When it came time for 28&7, the team knew they wanted something special. They returned to Shildan to push the envelope even more. “We were looking for extra depth and extra reaction to the light—and to do that in a way that was contrasting with the context, which is a very neutral buff tone masonry,” SOM Design Partner Chris Cooper previously told gb&d.
Shildan Group has seen a demand for three-dimensional shapes and an expansion of where terra-cotta can be used—including on curtain walls, according to Shildan Group President Moshe Steinmetz. “No more of those boring, rectangular aluminum extrusions but really introducing cladding to those volumes to make a building much more interesting,” he told gb&d.
Pros of Terra-Cotta Cladding
- Sustainable. Terra-cotta is made from clay, a natural material, and can be recycled after it is broken, making it an environmentally friendly option.
- Non-combustible. Clay is a naturally non-combustible material that does not burn, which can help prevent or significantly lessen fire damage.
- Durable. Like most clay building materials, terra-cotta is extremely durable and can last for upwards of 100 years; it also has a high compression strength and can withstand weather and temperature changes without damage.
Cons of Terra-Cotta Cladding
- Oxidation. Due to the iron found in many types of clay, terra-cotta is prone to oxidation when exposed to the open air, which can cause it to change color over time.
- Improper glazing. In order for terra-cotta to be made waterproof, it must first be glazed; if the glazing process is done improperly, it can lead to leaks and water damage.
Brick
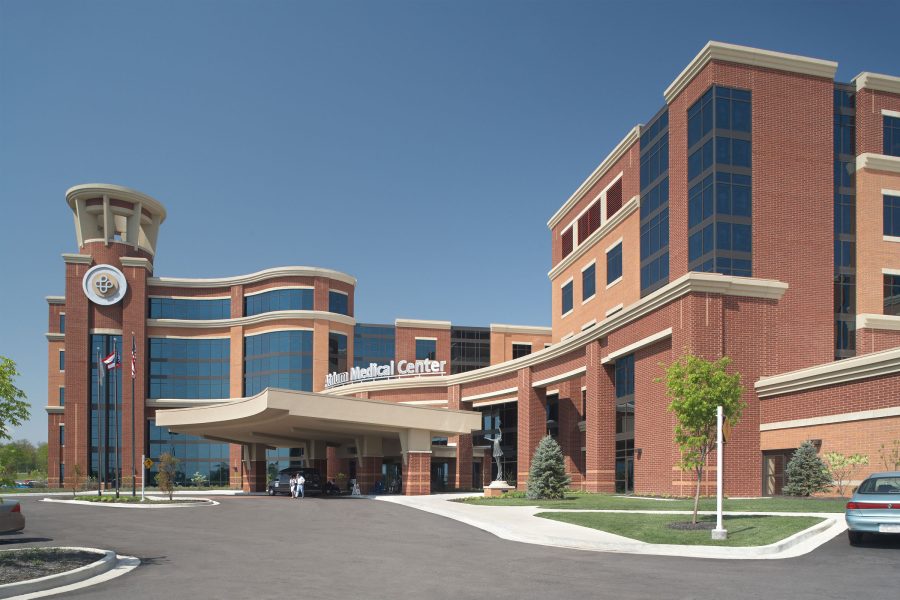
The design for Atrium Medical Center in Ohio incorporates monarch oversized brick from Belden Brick. Photo by Maguire Photo
Brick is one of the oldest cladding options on the market and remains a timeless material suitable for a range of aesthetics and project types. Because it is made from inorganic materials and fired at extremely high temperatures, brick cladding is incredibly resilient, is both weather- and storm-proof, with minimal maintenance requirements.
As long as it is properly cared for, brick can last for well over 50 years, with many brick-built structures lasting upwards of 100 years. “The brick will last the life of the building without a whole lot of extended maintenance,” Brian Belden, executive chairman and vice president of sales and marketing for Belden Brick, previously told gb&d. “And if you look at the energy that’s used to create a brick versus other products over the life of the product itself, it really stands out as a good value.
Beyond its incredibly durability, brick cladding remains a sustainable material in that it has high potential for reuse and thus supports a circular economy. “Not only is brick almost entirely recyclable, but it’s a building material that can be retained when a building undergoes a full renovation,” Tim Leese, director of marketing for Glen-Gery, wrote in a previous article for gb&d. “Building codes further support reuse as an exterior cladding material in other buildings when the bricks retain their original properties and have their structural capacity intact.”
Brick also makes for more energy-efficient projects, as bricks have inherent thermal properties because the clay from which they are made is a high-density material. Leese says brick can absorb and store heat energy in both the summer and winter to better cool and heat a home, in turn helping to minimize large peaks and dips as a home’s temperature fluctuates, instead averaging out extremes. Building with bricks also allows for virtually no emissions, he adds.
Brick cladding’s resilience, versatility, and range of colors, textures, and shapes make it a suitable choice for almost any project. Nowadays, it’s not uncommon to find brick-clad offices, educational institutions, residential buildings, and even health care facilities. ““A lot of the challenges health care facilities face with climate change is deferred maintenance with a lot of their facilities and infrastructures,” Greg Heppner, a senior principal at SmithGroup architecture firm, told gb&d in a previous article. “If brick is a component of that design and contributes to that quality then it could be an advantageous material to use.”
Pros of Brick Cladding
- Durable. As long as they are properly installed, most bricks have a lifespan of 100+ years; they have an extremely high compression strength and are largely unaffected by the elements.
- Thermal insulation. Bricks are capable of absorbing and storing heat, which makes them great at helping to regulate interior temperatures without the need for excessive electric heating and cooling.
- Low maintenance. Thanks to their strength and material composition, bricks are a low-maintenance cladding option; in most cases, occasional mortar touch-ups and a yearly cleaning is all that’s needed to keep brick cladding in good condition.
Cons of Brick Cladding
- High upfront cost. Bricks are one of the more expensive cladding options due to both the material costs and labor costs; in order for brick cladding to remain waterproof and prevent moisture build-up, professionals must be hired to perform the installation.
- Moisture retention. Despite their weatherproof nature, bricks are still a porous material that can soak up water; in areas with heavy rainfall, excess moisture retention can lead to water damage.
- Cracking. Due to their practically non-existent flexibility, bricks are liable to crack over time, especially if they are subjected to regular vibrations, such as those from heavy machinery or even traffic; this also means brick cladding is not earthquake proof.
Wood
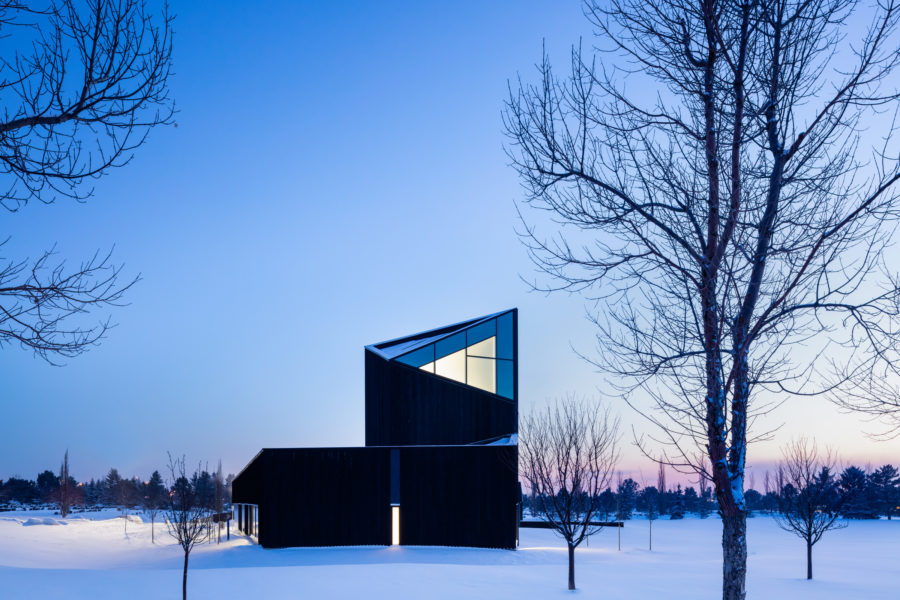
Delta Millwork’s Accoya wood was used for most of the siding on the South Haven Remembrance Center in Canada. Photo by Ema Peter Photography
For exterior cladding it’s important to use woods that are “stable,” according to Delta Millworks CEO Robbie Davis. That means they maintain their straightness and flatness when there are changes in temperature, humidity, and exposure to the elements like sun, rain, hail, and so forth.
Davis previously told gb&d Delta’s exterior woods—including its specially modified products like Accoya and Kebony, its shou-sugi-ban line that involves a Japanese charring process, cedar, and its newest thermally modified Mojave collection (available in oak, hemlock, radiata, and Ponderosa pine)—are far superior in quality to those typically sold at home centers. You’ll spend a bit more upfront, he said, but it will save you significant money, time, and headaches down the line.
All of Delta’s wood is sustainably sourced, and a good portion of its domestic product comes from tree farms in British Columbia. That means there’s no clear-cutting involved, less long-distance shipping, and a smaller carbon footprint than those produced by many other wood harvesters in America and abroad.
Testing, too, is a vitally important part of the Delta process. Each product is subjected to artificially emulated extremes—high in the dry mountains of Colorado, for example, or near the humid coast of California—with an accelerated weathering machine to make sure treated wood and coatings can easily endure the harshest real-world conditions. That way, there are no surprises once it’s installed, and clients can be assured of its future performance.
Pros of Wood Cladding
- Aesthetically pleasing. Wood cladding ranks right up alongside stone as one of the most aesthetically pleasing exterior claddings, one that offers a warm, inviting appearance and provides a sense of closeness to the natural world.
- Good insulator. Wood cladding is a natural thermal insulator, allowing it to trap and retain heat, thereby reducing dependency on heating and cooling systems, which in turn boosts energy-efficiency; wood cladding is also good at insulating against sound.
- Environmentally friendly. When harvested sustainably, wood cladding is an incredibly eco-friendly cladding option, as it can be reclaimed and will biodegrade once it no longer has construction value.
Cons of Wood Cladding
- High maintenance. Compared to something like concrete or stone, wood cladding is fairly high maintenance; in order to retain its durability, wood cladding must be regularly stained, painted, or oiled.
- Susceptible to moisture. Due to wood being a naturally porous material, one that absorbs and retains water, wood cladding is prone to warping, mildew, and rot, especially in regions that experience high humidity or rainfall.
- Insects. As with any wood product, wood cladding may be damaged by an array of insects that feed on wood, such as termites, carpenter bees, and woodboring beetles.
Thermally Modified Wood
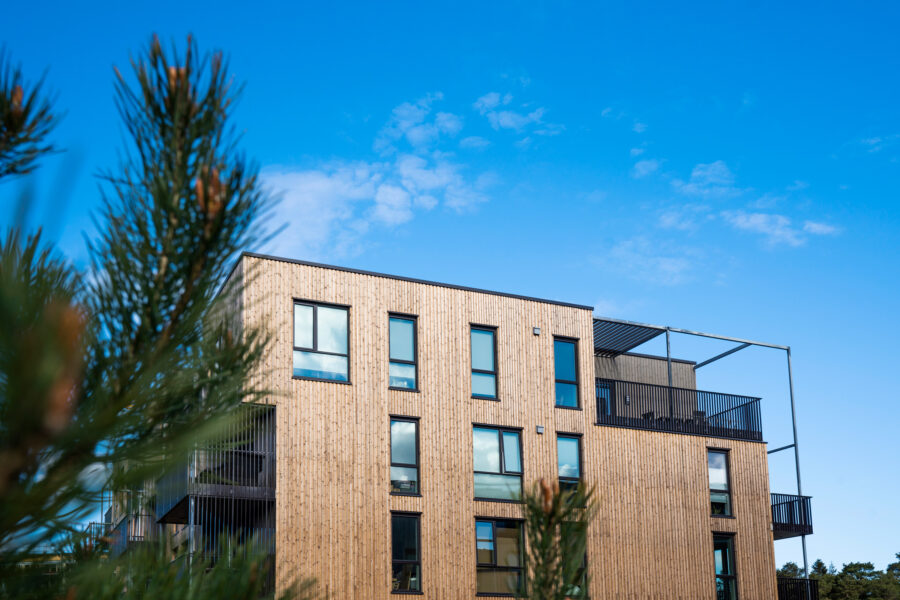
Thermally modified wood is mixed and matched at this sustainable apartment building in Norway. Photo courtesy of Thermory USA
But if the desirable inherent properties of wood cladding aren’t enough, consider implementing specialized thermally-modified wood cladding instead.
Thermal modification refers to the process by which certain organic compounds are removed from the wood’s cell-walls using a controlled heat procedure known as pyrolysis. In doing so, the wood becomes more durable and is made permanently resistant to decay and water damage. Thermory USA—one of the leading manufacturers of thermally modified wood cladding—has fine-tuned this process even further by using steam to improve control and thoroughly inspecting each board to reduce waste production.
Thermory also takes care to ensure that they are harvesting all of their wood sustainably. “We are careful with how we source our wood,” Thermory’s part-owner Kevin DeMars previously told gb&d. “We have taken great care to understand how different forests and environments renew. We source from several locations around the world and make sure to leave all forests healthy and thriving. We never source from rainforests.”
Pros of Thermally Modified Wood Cladding
- Low moisture absorption. The thermal modification process reduces the wood cladding’s ability to absorb and retain moisture, making it humidity-resistant and ensuring that it won’t warp or mildew over time.
- Durable. After the thermal modification process is complete, wood cladding has a higher resistance to rot and is better able to withstand harsh weather conditions.
- Aesthetically pleasing. Thanks to the drying process, thermally modified wood takes on deeper, richer color that mimics the color of many wood species found in tropical climates.
Cons of Thermally Modified Wood Cladding
- Decreased strength. While thermally modified wood is more durable than regular wood cladding, it is not as strong; due to the high temperatures associated with the modification process, thermally modified wood loses approximately 30% of its bending strength.
- More expensive than wood. Seeing as thermally modified wood cladding requires an extra step before it can be used in construction, it is more expensive than buying traditional wood cladding.
- Burns quicker. Due to its decreased moisture content, thermally modified wood burns faster than regular wood cladding, making it more susceptible to extreme fire damage.
Metal Composite Material (MCM)

Photo courtesy of ALPOLIC
MCM is a cost-effective cladding solution more architects are turning to, as lightweight sheets can be fabricated into complex shapes, finished in a wide array of colors and designs, and provide a steadfast cladding option that, combined with insulation and air water barriers, creates a high-performance building envelope, according to Michael Bowie, technical support specialist at MCA-ALPOLIC Division.
“Introduced to the world more than 50 years ago, American manufacturing and architectural use of MCM has taken hold over the last three decades,” Bowie previously wrote for gb&dPRO. “First incorporated into gas station canopies, painted aluminum composite material (ACM) offered a lightweight, uniform look for the biggest petroleum brands who needed easy fabrication, reliability, and custom matched finishes for their corporate identity colors.”
He said the panels can be prefabricated in the shop and installed faster than alternative products for the building envelope. “These systems could require less structural investments, like reduced steel needs because of the lighter load in the wall assembly. Though only one-fourth to one-third as much metal as comparable one-eighth inch sheet metal, composites impressively retain their rigidity and strength.”
Pros of MCM Cladding
- Lightweight. Generally speaking, MCM cladding only weighs half as much as solid sheet metal, making it easier to transport and install, which can help reduce overall construction costs.
- Strong. Despite being lighter than steel, MCM cladding is still 90% as strong as solid metal, which means it won’t compromise a building’s structural integrity; MCM also offers improved stability and vibration resistance.
- Versatile. Compared to solid sheet metal, MCM is incredibly versatile and may be shaped into a nigh-unlimited number of complex shapes, allowing for more dynamic designs.
Cons of MCM Cladding
- Denting. While MCM cladding is generally able to withstand severe weather without much issue, it can be dented or scratched by hail or the windblown debris accompanying hurricanes and tornadoes.
- Faulty seals. If MCM cladding is not properly sealed, it can allow water to enter the building, leading to potential moisture damage, mildew, or mold growth.
Ceramic
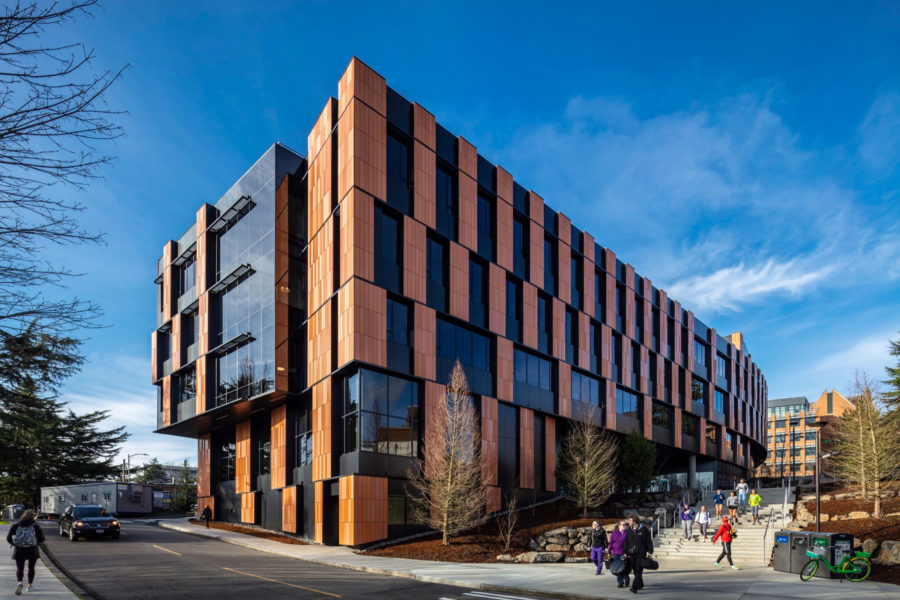
The Bill & Melinda Gates Center for Computer Science & Engineering. Photo courtesy of IMETCO
Experts are also seeing a growing demand for ventilated facades in the architectural community. Why a ventilated facade? Simply put, a ventilated building envelope—defined as cladding designed with an internal air chamber—allows for both increased thermal and acoustic performance, reducing energy costs for heating and cooling, and with less ambient noise making its way in, improving the lived experience inside the structure.
Properly designed ventilation can increase the resiliency of a structure by keeping building materials dry at all times, while using thick ceramic tiles help the structure resist against direct environmental loads such as wind, rain, and heat. Combined with a rainscreen, a time-tested building practice, ceramic facades can last generations.
Innovative Metals Company (IMETCO), a leading US manufacturer of premier metal products for the building envelope, has experienced this demand firsthand. “Lighter, easier to install, safer for buildings (with no contribution to fire risk), and endlessly customizable, this cladding system sets a new industry standard,” Juan Gurrea, export manager at Gresmanc, previously told gb&d. “And it can be combined with various materials or seamlessly integrated into IMETCO’s innovative IntelliScreen rainscreen systems.”
Pros of Ceramic Cladding
- Low maintenance. When installed as exterior cladding, most ceramic panels are either incredibly low maintenance (occasional washing) or no maintenance at all.
- Natural insulator. Similar to terra-cotta, ceramic cladding is great at insulating both heat and sound, which in turn creates a more comfortable interior with smaller heating and cooling loads.
- High durability. When it comes to weather, ceramic cladding is capable of handling everything from wind and rain to snow and ice; as long as it is properly maintained, ceramic cladding has an expected lifespan of 50+ years.
Cons of Ceramic Cladding
- Prone to cracking. Despite being able to withstand a variety of elemental factors, ceramic cladding is still susceptible to cracks and breakage when exposed to intense vibrations or forceful impacts.
- Expensive. As is the case with most ceramic products, ceramic cladding is usually more expensive than other cladding options due to the extra steps involved in its creation and installation.
Vinyl Siding
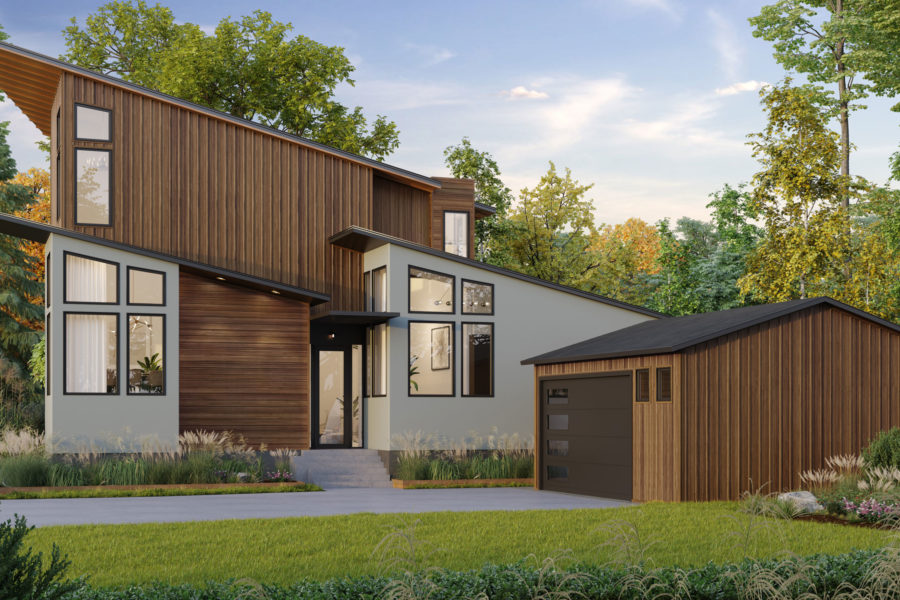
The Cedar Renditions aluminum siding line was developed with a variegated wood-grain design that offers a modern, streamlined look on 6-inch panels. Rendering courtesy of Westlake Royal Building Products
Perhaps unexpected, vinyl siding continues to be a popular—and increasingly sustainable—choice. “Vinyl siding is probably the most sustainable product from a complete life cycle perspective of any exterior cladding,” Steve Booz, vice president of marketing at Westlake Royal Building Products, said in a previous interview with gb&d. “The resources to manufacture it are lower, and certainly the longevity and the recyclability of the material make it one of the most full-circle sustainable solutions out there.”
Westlake Royal Building Products’ TruExterior product line is made from 70% recycled content—specifically fly ash, which is a by-product recovered from coal combustion—combined with polymer for a high level of dimensional stability and durability.
“Customers want a product that is going to last a lifetime,” Booz said. “That’s why our siding products at Westlake are engineered with advanced materials that offer a wood-like aesthetic without the moisture absorption or maintenance issues associated with real wood products. When moisture penetrates materials like wood and then dries out, it can lead to cracking, warping, and mold growth. And customers just don’t have time to deal with those issues.”
Pros of Vinyl Siding
- Quick installation. Thanks to its lightweight nature and the fact that it comes in long panels, vinyl siding has a very quick installation time, especially when done by experienced professionals.
- Inexpensive. Averaging between $3.00 and $10.00 per square foot, vinyl siding is one of the cheapest cladding materials you can find, which can help save on initial construction costs.
- Low maintenance. Once it has been installed, vinyl siding requires very little maintenance; any dirt, dust, or grime that accumulates on its surface can typically be removed with a simple pressure-washer.
Cons of Vinyl Siding
- Cracking. When exposed to extremely cold or freezing temperatures, vinyl siding has a tendency to become brittle and has even been known to crack.
- Poor UV resistance. Compared to most cladding options, vinyl siding has an extremely low UV-light tolerance, which means it is likely to fade or change color over time.
- Easily damaged. While this isn’t true for all vinyl siding, a vast majority of vinyl siding options are easily dented, which can result in more frequent replacements; this is especially true for buildings located in regions that often receive hail and experience high winds.
Precast Concrete
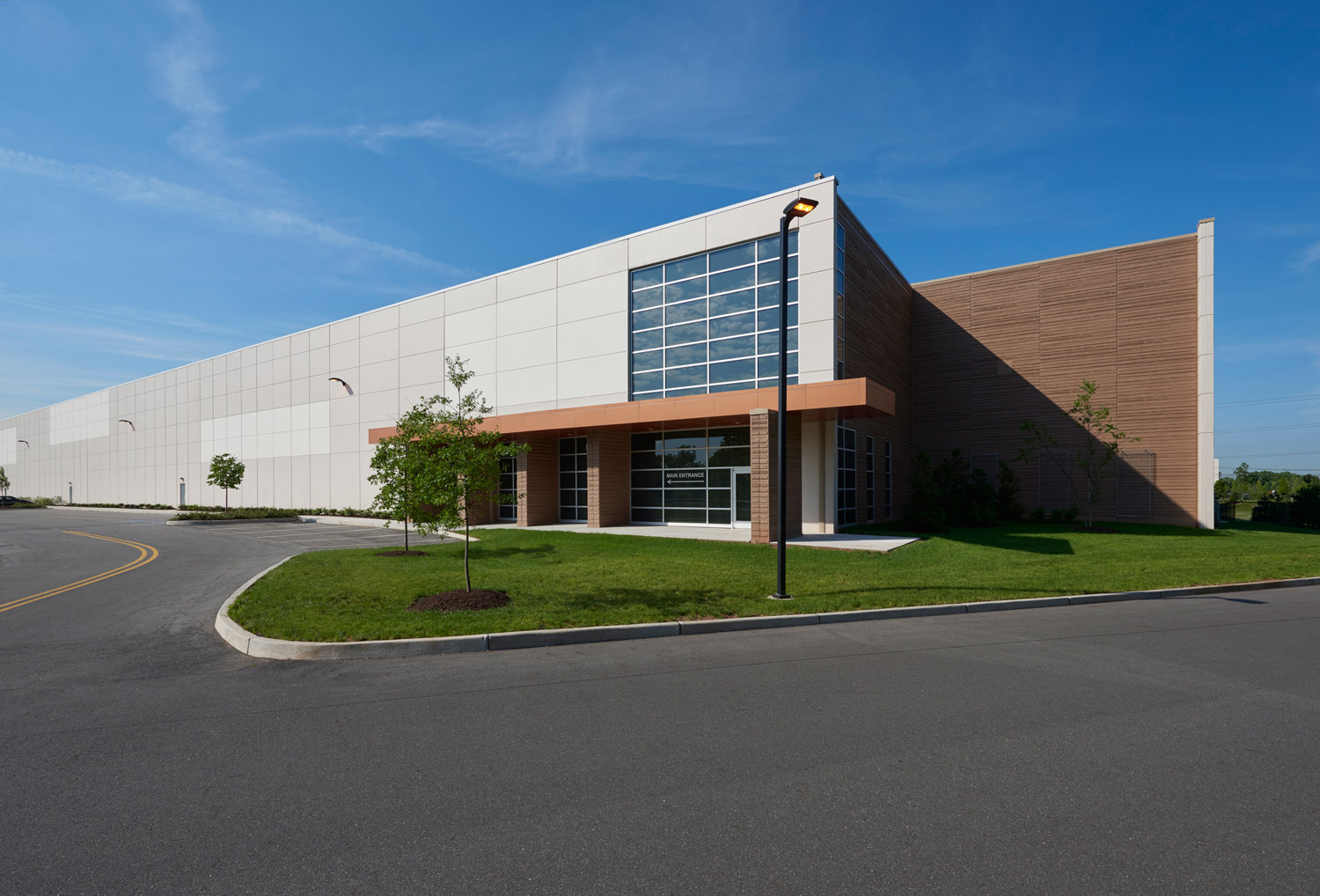
The South Washington Park in Piscataway, New Jersey shows that its possible to have a building made with precast concrete look as it were made with wood as well. Photo courtesy of Fabcon
While concrete has long since been used as a cladding material, it was only very recently that options expanded beyond the drab concrete block to include precast concrete panels, or large slabs of pre-manufactured concrete. Precast concrete panels are quick to install, incredibly strong, and are typically of a higher quality and are more structurally-sound than cast-in-place concrete.
What’s more, precast concrete isn’t limited to the grays you’ve come to expect from concrete. “We can create practically endless colors through the combination of materials we use,” Rich Mantel, material engineer for Fabcon Precast, previously told gb&d. “We can combine four different ‘primary’ colors of pigments (light red, dark red, yellow, and black) in any ratio to create many different matrix colors.”
Precast concrete cladding can also be made to mimic a variety of textures, such as stone masonry or wood grain, without sacrificing the qualities that make concrete so desirable. When supplying precast concrete panels to the South Washington Park buildings in Piscataway, New Jersey, for example, Fabcon utilized a horizontal wood plank form-liner to create a striated texture that added an overall sense of depth to the panels.
Pros of Precast Concrete Cladding
- Extremely resilient. Once cast, precast concrete cladding is stronger and more resilient than concrete cladding cast on-site; precast concrete is capable of withstanding corrosion, severe weather, and impacts with ease.
- Low maintenance. If sealer is applied after precast concrete cladding is installed, it only needs to be hosed down once a year to keep it clean; in the event that a sealer is not applied, precast concrete should be power-washed every 4 to 6 years to get rid of dirt and grime buildup.
- Quality control. Due to being manufactured in a controlled setting, precast concrete cladding is extremely uniform in quality, which helps ensure that the finished structure is safe, durable, and structurally-sound.
Cons of Precast Concrete Cladding
- Higher upfront costs. While precast concrete may not be as expensive as, say, stone, it is more expensive than traditional concrete blocks.
- Can be difficult to transport. Large precast concrete panels are often bulky, heavy, and awkward to transport, which can cause delays and increase a project’s overall construction time.
- Difficult to modify. Once precast concrete cladding cast, it is almost impossible to modify; should any changes need to be made after the fact, it can require a complete restructuring or re-casting of the panels themselves.
Stone
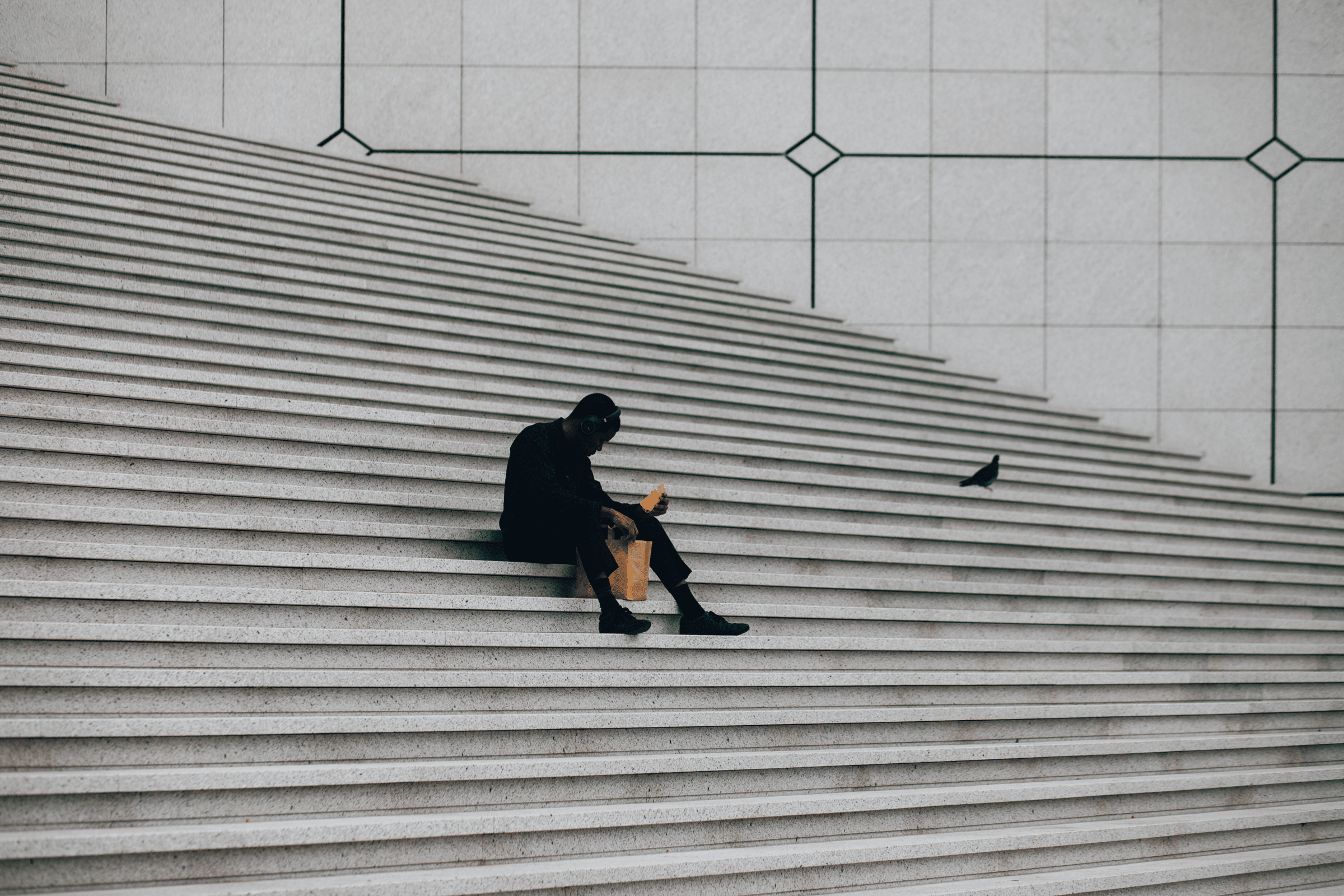
The Grande Arche de la Défense in Paris won the Pinnacle Award of Excellence for Commercial Exterior from the Natural Stone Institute. Photo courtesy of Polycor
As one of the oldest building materials, it’s no surprise that stone cladding continues to persist as a favored element in a wide variety of commercial and residential designs, especially when so many different types of stone are available.
Polycor, a Canada-based company, is one of the leading suppliers of building-grade stone in North America and places a key focus on sourcing high-grade stone in various colors so as to eliminate the need for dyes or resins. Polycor’s Bethel White granite, for example, is quarried in Vermont and is the whitest granite on the market. It was used to restore The Grande Arche de la Défense in Paris after the structure’s original marble failed.
Stone cladding is also favored for its low environmental impact. “Stone has an extremely low embodied carbon footprint because it was formed by the planet itself,” Hugo Vega, Polycor’s vice president of commercial and institutional sales, previously told gb&d. “It’s right under our feet.”
Add on to that stone’s incredibly long lifespan and the fact that quarrying stone doesn’t necessitate the use of chemicals or produce toxic waste and it’s easy to see that stone is one of the most environmentally friendly cladding choices there is.
Pros of Stone Cladding
- Extremely durable. It’s no secret that stone is incredibly strong and lasts for an extremely long time, two qualities that allow it to withstand virtually any weather conditions, fire, and even some natural disasters.
- Low maintenance. Most stone used for exterior cladding purposes requires little upkeep; occasional power-washing and mortar retouching is typically all that’s required to keep it in good condition.
- Sustainable. As a 100% natural product, stone requires very little preparation before it can be used in construction, which reduces its overall waste production and energy consumption.
Cons of Stone Cladding
- Expensive. The main disadvantage of stone cladding is its price, as real stone is both expensive to purchase and requires a team of professional stonemasons to install, which raises your overall labor costs.
- Poor installation. If your stone cladding ends up being installed incorrectly, it can lead to cracking, which can in turn allow moisture to accumulate and cause problems with mold or mildew.
- Heavy. While the dense weight of stone aids in its durability, it also requires a strong structural substrate and may even necessitate the installation of additional structural support features, which can further increase construction costs.
Artificial Stone Veneer

Artificial stone veneer cladding installed on a lodge. Photo courtesy of Cultured Stone
That being said, natural stone isn’t the only way to achieve the stone aesthetic—there’s also artificial stone veneer. “As a manufactured product, architectural stone veneer opens up a world of almost unlimited product variety, and adding stone elements remains one of the top architectural trends for both exterior and interior applications,” Sarah Lograsso, director of marketing and product design for Cultured Stone, told gb&d in a previous interview.
Cast in molds based on real stones, Cultured Stone’s artificial stone veneer is created using a concrete mixture and then hand-painted with iron oxide pigments to mimic the color and texture of natural stone. The resulting product is incredibly convincing and retains many of the desirable qualities of stone (high durability, weather resistant, etc.) at only a fraction of the weight.
This means artificial stone veneer can accommodate design choices that wouldn’t necessarily be possible—or economical—with full bed-depth stone.
Pros of Artificial Stone Veneer
- Durable. Most artificial stone veneer claddings are designed to last anywhere from 20 to 75 years and are capable of weathering storms, fire, and wind without sustaining significant damage.
- Lighter than stone. Considering manufactured stone veneer isn’t as dense as stone and is therefore lighter (roughly one-fourth the weight), it can be affixed to a wider range of non-structural building components.
- Easy installation. Thanks to their lightness and availability in large sheets, artificial stone veneers are fairly quick and easy to install, which helps cut down on total construction time.
Cons of Artificial Stone Veneer
- Prone to fading. Unlike natural stone, artificial stone veneer is liable to fade over time when exposed to UV light, which can detract from the building’s aesthetic value.
- Repetition. Due to the fact that artificial stone veneer is mass produced using molds, you’ll inevitably end up with repeating patterns; in this regard, manufactured stone veneer isn’t nearly as unique as true stone.
- Moisture problems. If artificial stone veneer is not installed properly, it can allow moisture to accumulate behind the cladding, which can then lead to mold growth, wood rot, and even structural damage.
Metal Panels
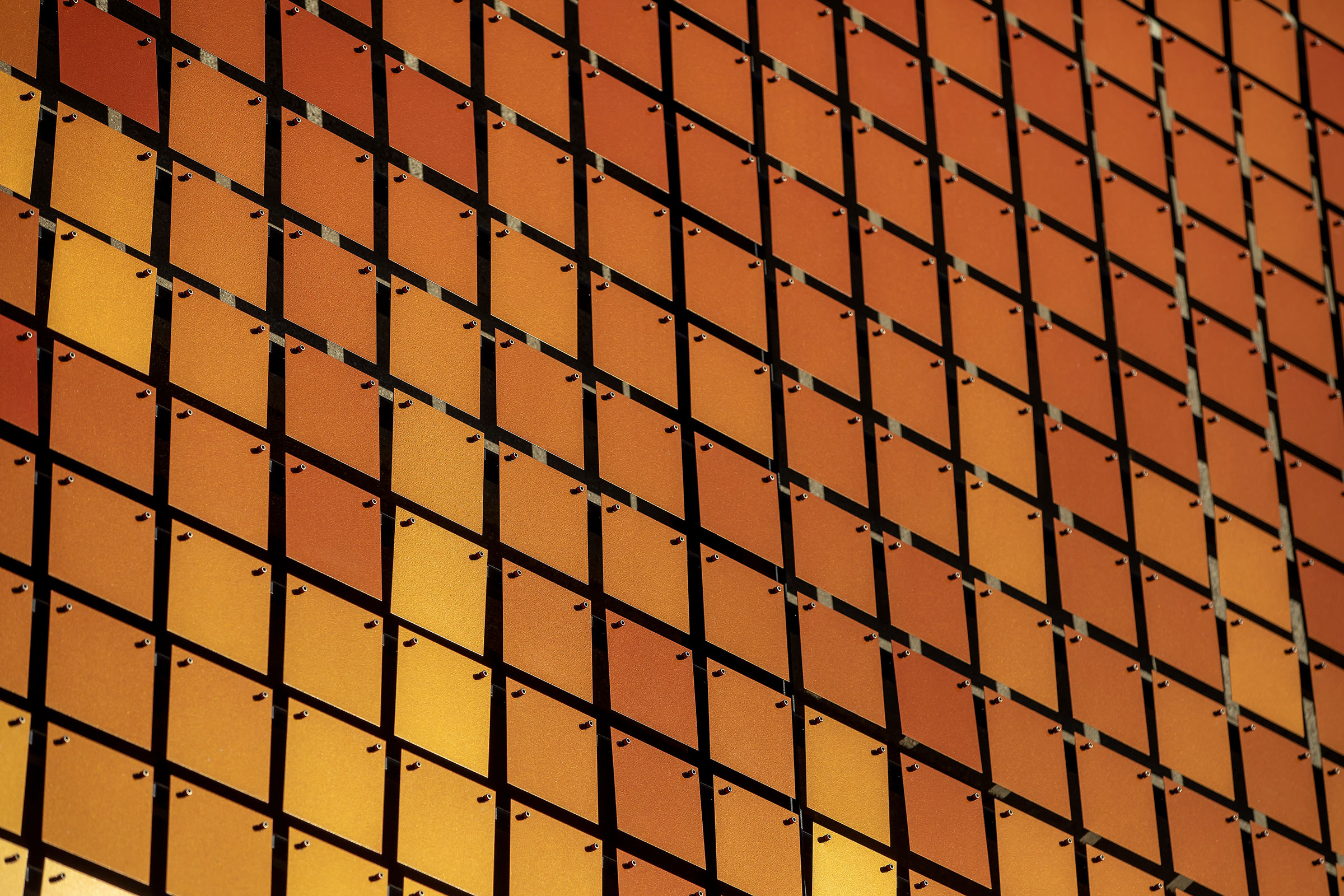
The Footprint Center in Phoenix emphasizes sustainable design strategies, including a metal panel facade. Photo by Christy Radecic
Lastly, let’s take a look at a relatively new cladding material that has quickly taken the architectural world by storm: metal panels. “You look at any type of project that has been done over the years—some of the most complex projects out there—and metal panels are used,” Devin Norton, the senior project designer for HOK, previously told gb&d. “It can be bent, and it can be molded and panelized to any shape for the most part.”
This versatility has allowed metal panels to fill a niche that conventional cladding materials simply can’t. “Glass has certain restrictions. A metal panel has a lot more flexibility. Just like you can’t do certain things with concrete. A metal panel can take any type of shape,” Norton says.
We see this in HOK’s revitalization of the Footprint Center stadium in Phoenix, Arizona, which made use of metal panel cladding capable of moving with the wind—the end result being a mesmerizing ripple effect that makes the building much more dynamic than it used to be.
Petersen is one of the leading producers of metal panel cladding and the company behind the PAC-CLAD brand, which carries a variety of high-performance, UV-blocking panels capable of withstanding extreme weather and reducing a building’s cooling loads.
Pros of Metal Panel Cladding
- Recyclable. On average, metal panel cladding lasts anywhere from 30 to 50 years; once it’s reached the end of its lifespan, metal cladding can be 100% recycled, thereby reducing the amount of material waste.
- Low maintenance. Typically metal panel cladding requires very little maintenance once it has been installed, which can help save money on cleaning and repairs down the line.
- High durability. Modern metal panel cladding is highly resistant to corrosion, fire damage, and most kinds of water damage, allowing it to withstand everything from storms to acid rain without much issue.
Cons of Metal Panel Cladding
- Oil canning. Referred to as the phenomena by which the flat parts of metal panels appear wavy or distorted, oil canning can result from a number of factors, including improper handling/storage, over-driving the fasteners, stressors during production, etc.
- Susceptible to rust. If it is not appropriately treated before installation, metal panel cladding (particularly the edges) can rust over time, especially in areas that receive frequent, heavy rainfall.
- Delamination. Once the polymer coating on metal panel cladding starts to age and wear out, it can start to delaminate and peel away from the panel’s surface.
Laura Rote contributed to this article.