Story at a glance:
- Because they are made primarily from clay devoid of organic matter, terra-cotta and brick are both naturally fire resistant building materials.
- Concrete and cement-based products like stucco are also inherently non-combustible thanks to their use of naturally fire-resistant materials like limestone and silica sand.
- Other common fire resistant building materials include mineral wool, gypsum, and fire rated glass.
As wildfires continue to become more frequent and severe, architects and other AEC professionals have a responsibility to design spaces that buy occupants as much time as possible to safely evacuate should a fire break out.
One way to do this is by choosing and specifying non-combustible, fire resistant materials throughout a building’s interior and exterior.
In this article we’ll explore what it means for a material to be considered fire resistant and take a look at seven common examples.
What are Fire Resistant Materials?
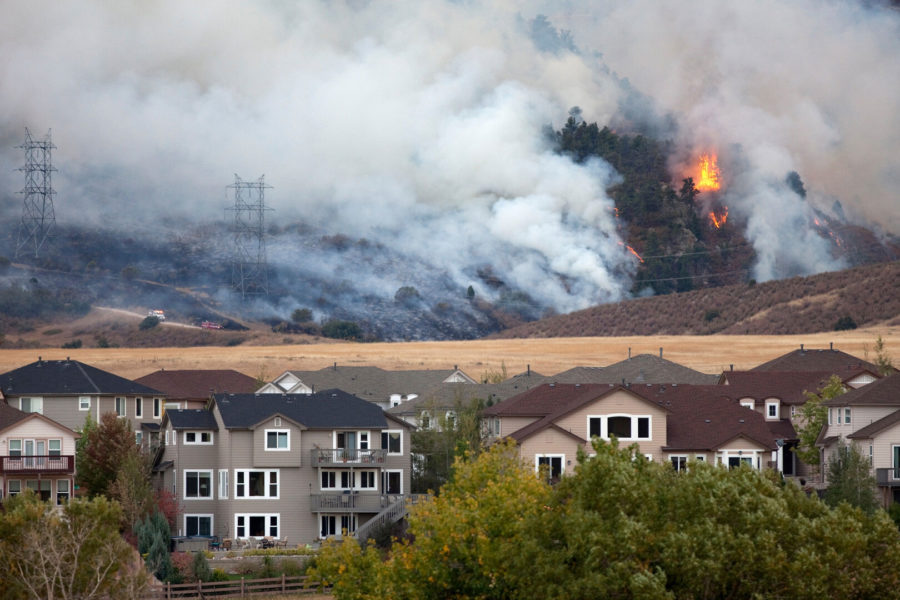
Photo courtesy of ROCKWOOL North America
Fire resistant building materials are generally considered to be inherently non-combustible and naturally resist burning when exposed to flames. Fire resistance is defined as being “so resistant to fire that for a specified time and under conditions of a standard heat intensity it [the material] will not fail structurally or allow transit of heat and will not permit the side away from the fire to become hotter than a specified temperature.”
Naturally fire resistant materials will almost always receive an automatic Class A fire rating from the American Society for Testing and Materials (ASTM). Fire ratings are based on a material’s flame spread index—or how quickly flame spreads across a material’s surface—and smoke development index, or how much smoke a material generates as it burns. A Class A rating is the highest possible rating and means the material has a flame spread index between 0 and 25 and a smoke development index between 0 and 450.
Building with naturally fire resistant materials is extremely important from a safety standpoint and is integral in providing occupants with enough time to evacuate in the event of a fire.
Fire Resistant vs Flame Retardant
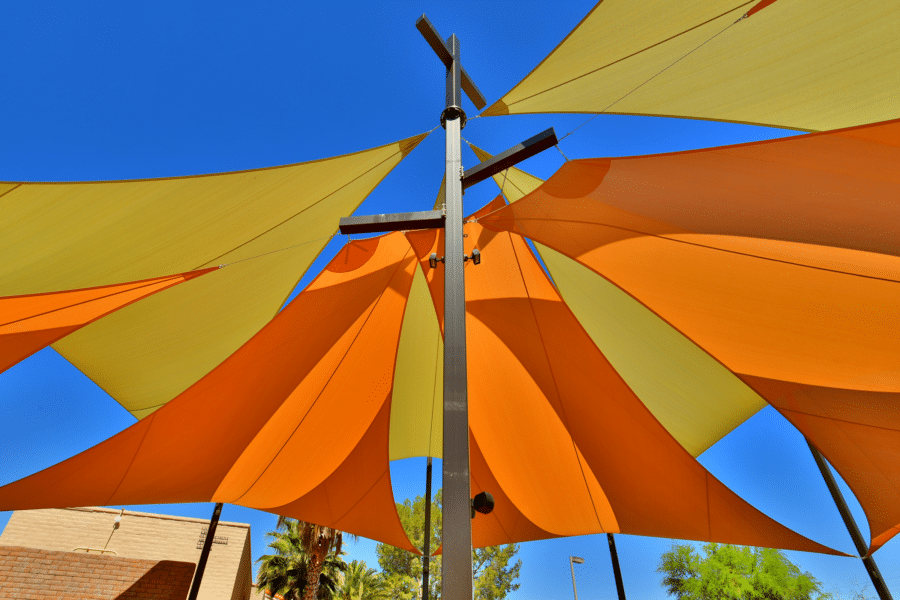
Photo courtesy of GALE Pacific
Before we move on to our examples, let’s take a moment to discuss the differences between fire resistant and flame retardant, as the two terms are often used interchangeably despite referring to two very different things.
- Fire resistant. As previously mentioned, fire resistant materials are those which possess a natural ability to withstand fire, typically as a result of their chemical makeup.
- Flame retardant. A flame retardant material, on the other hand, is one that has been treated with chemical flame retardants—many of which contain bromine—to improve its overall resistance to fire and ability to self-extinguish.
Any naturally combustible material can, in theory, be treated with chemical retardants to reduce its susceptibility to catching on fire. This includes organic raw materials like lumber, products that contain organic materials (such as cellulose insulation), as well as combustible synthetic materials like polyethylene.
Many architectural fabrics, for example, are made from inherently combustible polymers that have been engineered to be flame retardant. This is done by either applying a surface treatment or by integrating flame retardants into the fibers themselves; the latter method is more effective and is practiced by GALE Pacific, one of the world’s leading manufacturers of architectural fabric products.
“When we produce fiber, the flame retardant additive spins through an extrusion die head and goes all the way through the fiber, effectively locking in the additive,” Andrew Nasarcyzk, research and development manager at GALE Pacific, previously wrote for gb&d.
7 Fire Resistant Building Materials
Now that we’ve established what it means for something to be considered fire resistant, let’s take a look at seven such materials.
1. Terra-Cotta
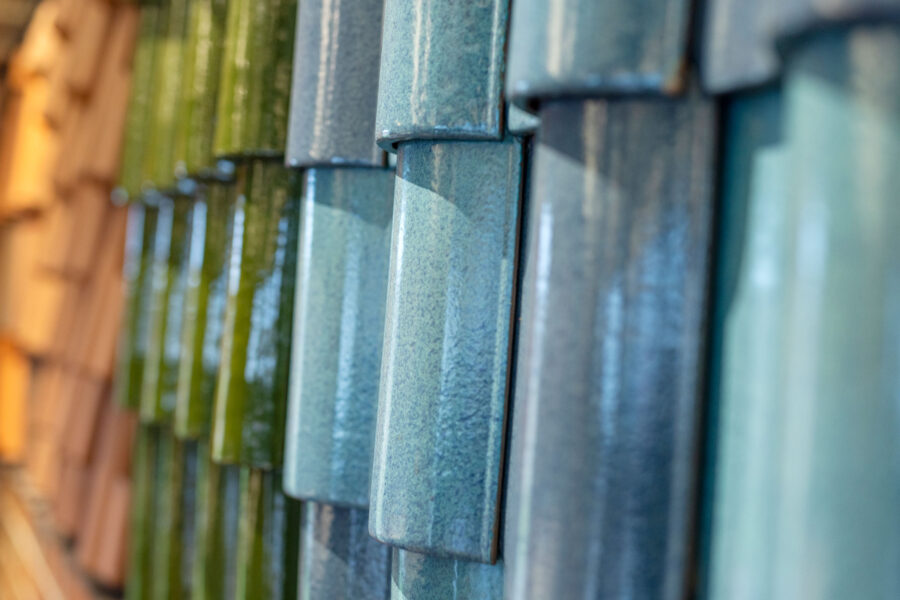
Photo courtesy of Ludowici
Terra-cotta—a phrase that translates to “baked earth” in Italian—is a clay ceramic material that has historically been used in a variety of artistic and architectural applications. In construction, terra-cotta is most commonly used for roofing, flooring, and cladding tiles, though the material has also been used as infill between steel structural components as a means of fire-proofing.
As it is made from inorganic materials, terra-cotta is inherently non-combustible and will not catch fire, allowing it to be used as a barrier or protective sheath that helps protect against or reduce fire damage. “One of the other great benefits of terra-cotta tile is its inability to burn,” Rob Wehr, vice president of business at Ludowici, wrote in a previous article for gb&dPRO. Ludowici is one of the world’s leading manufacturers of terra-cotta tiling solutions, specializing in the creation of durable, fire- and weather-resistant roofing tiles.
The manner in which terra-cotta is manufactured also contributes to its high fire resistance, as after the clay is filtered, mixed, and molded, it is fired at an extremely high temperature—typically between 1,100℉ and 2,100℉—to harden and vitrify the clay. Combined, these characteristics make terra-cotta an excellent choice for projects in wildfire prone areas, especially when used as part of a wall or roofing assembly.
“The objective is creating a roofing assembly that resists burning and hot embers and can hold these off as long as possible,” Dan Harris, vice president of sales and marketing at Ludowici, told gb&d in a previous article. “With Ludowici’s noncombustible clay as a part of a Class A fire-rated roof assembly, the roof structure is better protected and gives those inside a burning building more time to evacuate.”
It should be noted, however, that terra-cotta tiles do not make a roof assembly wholly immune to fire, as windblown embers can still ignite the roof’s underlayment should they find their way through gaps in the tiles. For this reason, it is recommended that a Class A underlayment be installed underneath terra-cotta tiles for added protection, especially in wildfire-prone areas.
2. Brick
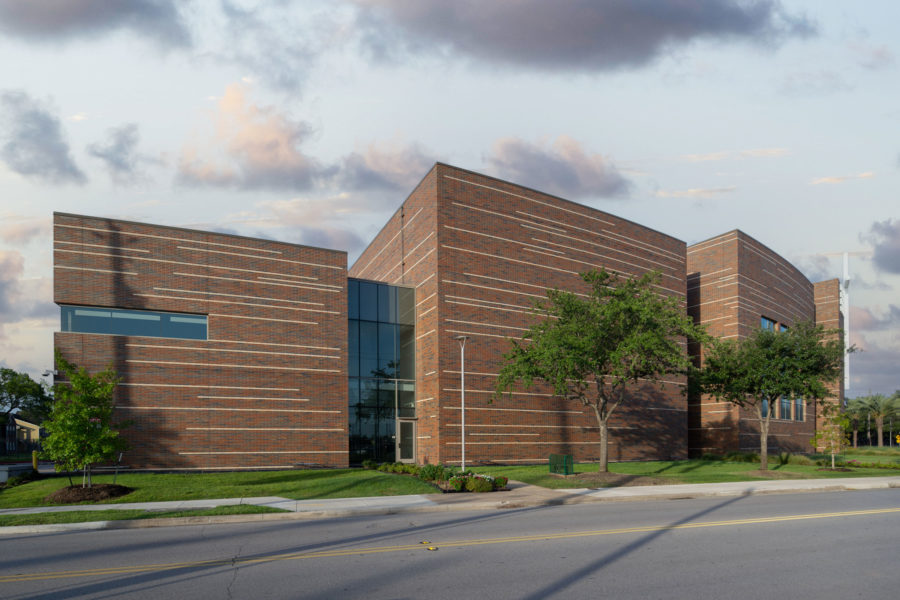
Photo courtesy of Acme Brick
Similar to terra-cotta, brick is another clay-based building material with inherent fire-resistant properties thanks to its manufacturing process and use of inorganic building materials, the former of which involves firing in a kiln at very high temperatures.
“When you think about fire protection, brick is fired at around 2,000 degrees Fahrenheit, which means brick is classified as a non-combustible material,” Stan McCarthy, senior vice president of sales at Acme Brick, previously told gb&d. Established in 1891, Acme Brick is the one of the world’s largest (and oldest) manufacturers and distributors of bricks and masonry-related products.
Once fired brick becomes an extremely durable material that, in addition to boasting a Class A fire rating, possesses a high resistance to the elements in general. “Studies have shown that structures built with brick offered dramatically more protection from windblown debris than other cladding products,” says McCarthy.
It’s important to note, however, that while bricks are extremely resistant to fire, the mortar that holds brick walls together typically possesses a lower fire resistance than the bricks themselves. Of course, mortar is still classified as a non-combustible material (it is made from clay, sand, cement, and lime, after all), but conventional mortar begins to crack and expand once temperatures crest the 500℉ to 600℉ range, potentially leading to the collapse of a wall even if the individual bricks are undamaged.
3. Concrete
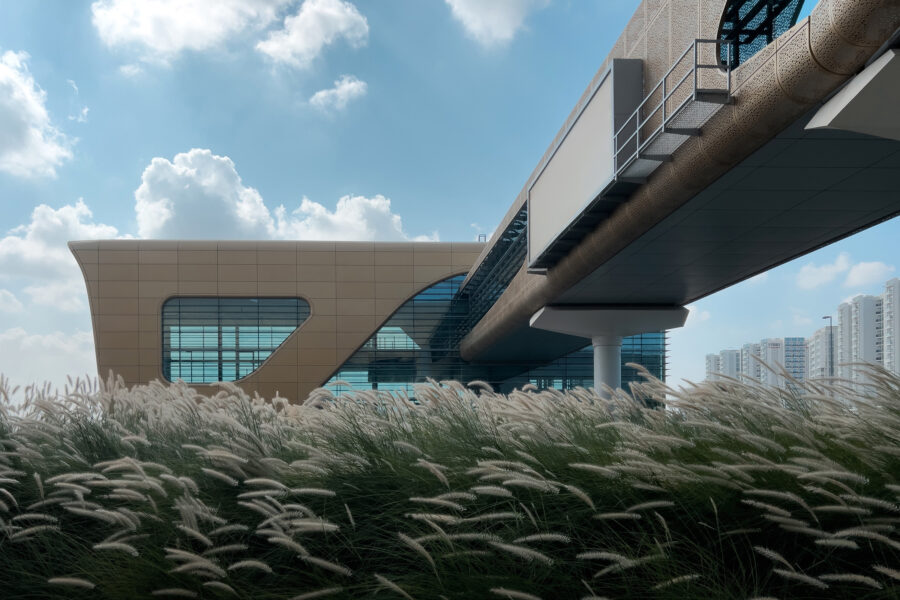
Concrete project in Dubai. Photo courtesy of the Global Cement and Concrete Association
Concrete is an incredibly strong, durable, and versatile material that can be used to construct everything from buildings and bridges to roads and dams—qualities that have led it to becoming one of the most widely-used resources in the world. Made from Portland cement, water, coarse aggregates (e.g. gravel), and fine aggregates (e.g. sand), concrete is an inherently non-combustible material with a slow rate of heat transfer that will not burn or produce toxic fumes when exposed to fire.
For this reason, all concrete is considered to be fire resistant with a Class A fire rating—but not all concrete possesses the exact same fire-resistance properties. The type of aggregates used to manufacture concrete, for example, can change how well it prevents fire damage; as a general rule, carbonate aggregates like dolomite and limestone tend to be the most efficient, as they both have a high heat capacity.
One of the most effective ways to use concrete in modern construction is insulated concrete forms (ICFs). Strong, quick to manufacture, and relatively simple to put in place, ICFs are created by pouring concrete into flame-retardant insulated polystyrene foam forms; once the concrete sets, the forms are left in place rather than removed, giving the wall improved insulating qualities over traditional wood-frame walls.
In addition to being extremely energy efficient, ICFs are also highly fire-resistant, capable of withstanding intense heat (up to 2,000℉) for a period of four hours without suffering structural damage. The very nature of ICFs means they do not allow flames to pass directly through walls, nor do they transfer enough heat to start a fire on the wall’s cool side for a period of 2 to 4 hours, reducing the likelihood of fire damage and/or loss of life.
4. Mineral Wool
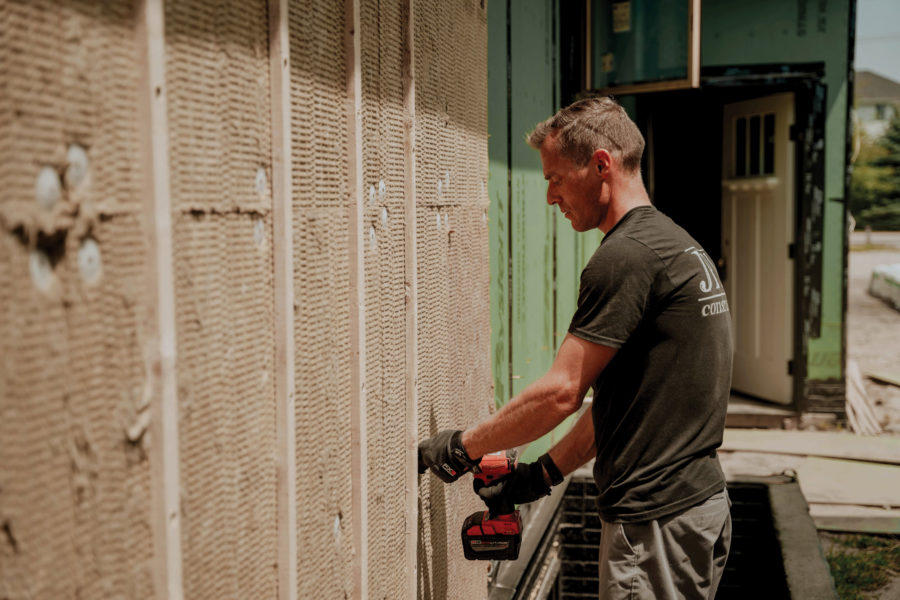
Photo courtesy of ROCKWOOL North America
Primarily used as thermal and acoustic insulation, mineral wool—also referred to as stone or rock wool—is a material made by melting volcanic rocks (e.g. basalt, bauxite, dolomite, et cetera) or slag in a furnace and then spinning the molten material into fibrous strands. Because it is made from inorganic materials, stone wool is inherently flame resistant.
“It’s naturally non-combustible (tested in accordance with ASTM E136) and able to withstand temperatures up to 2,150°F (1,177°C),” Brendan Knapman, head of product management for ROCKWOOL, previously wrote for gb&dPRO. “It limits the spread of fire, slows the transfer of heat across the wall assembly, and will not contribute to smoke development with added design flexibility for ASTM E2707 or NFPA 285 assemblies including unlimited insulation thickness to meet increasingly stringent thermal requirements.”
ROCKWOOL is a leading provider of stone wool insulation products and offers a variety of batt, board, and granulate/loose-fill solutions, many of which were designed to comply with the California Fire Code, one of the most rigorous fire codes in the country. ROCKWOOL was the first insulation provider to make it onto California’s Office of the State Fire Marshal’s Building Materials Listing Program and currently offer eight stone wool insulation products that have been independently tested in accordance with ASTM E84 for flame spread and smoke development and ASTM E136 for non-combustibility.
Beyond helping to slow the spread of fire, mineral wool is also an extremely effective insulation material, one that possesses an average R-value between 3.0 and 3.5 per-inch of material. Combined, these qualities make stone wool a highly suitable insulation material for buildings that must comply with stringent fire codes as well as rigorous energy-efficiency codes. “Selecting stone wool insulation is an ideal solution for the challenges of building a high-performance home in a WUI [Wildland Urban Interface] zone. It makes it possible to achieve aggressive goals for energy efficiency as well as fire resilience,” writes Knapman.
5. Gypsum
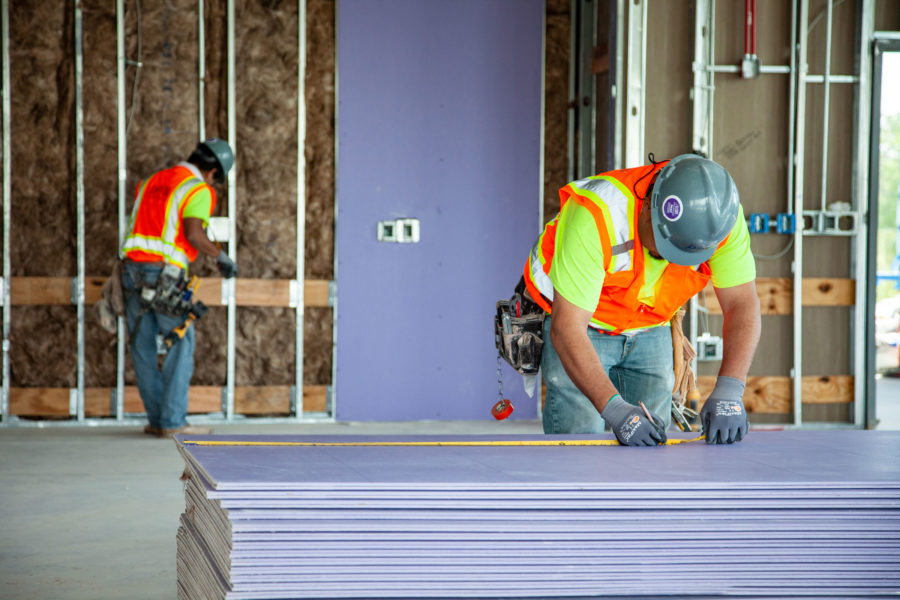
Photo courtesy of National Gypsum
Gypsum is a soft mineral composed of calcium, sulfate, oxygen, and water that is commonly used in construction to produce drywall/sheetrock, wall and ceiling plasters, gypsum blocks, and as an additive in cement. Products and building assemblies that include gypsum enjoy a high degree of fire resistance, a quality that comes from the material’s chemical composition.
“Chemically speaking, gypsum is very unique,” Brett Fleury, product marketing manager for performance flooring at USG—a leading manufacturer of high-quality building materials—previously told gb&d. “Two molecules of water are chemically bound to the gypsum. When the gypsum is heated to a high temperature, the chemically bound water absorbs the rising heat, thus serving as a heat sink during a fire test.”
The high water content of gypsum means it is non-combustible, helping it to slow the spread of flames and provide occupants with ample time to evacuate; a standard drywall panel, for example, will typically resist fire for up to one hour, though certain types of gypsum drywall are engineered to last upwards of two hours.
National Gypsum is a leading provider of gypsum board and drywall solutions, one that is constantly looking for new ways to improve upon their products’ inherent fire resistance. “Whenever we vet new ingredients or new chemistry, we test them internally and do multiple qualifying trials before introducing them to the marketplace,” Matt Gallagher, gypsum systems product manager for National Gypsum, told gb&d in a previous interview.
“Product fire resistance properties and achieving the respective fire system ratings are very important to National Gypsum because this ensures life safety for building occupants. We are constantly testing and re-testing within an Underwriters Laboratory (UL) approved testing facility to demonstrate how our products can be used in fire-rated assemblies.”
6. Stucco
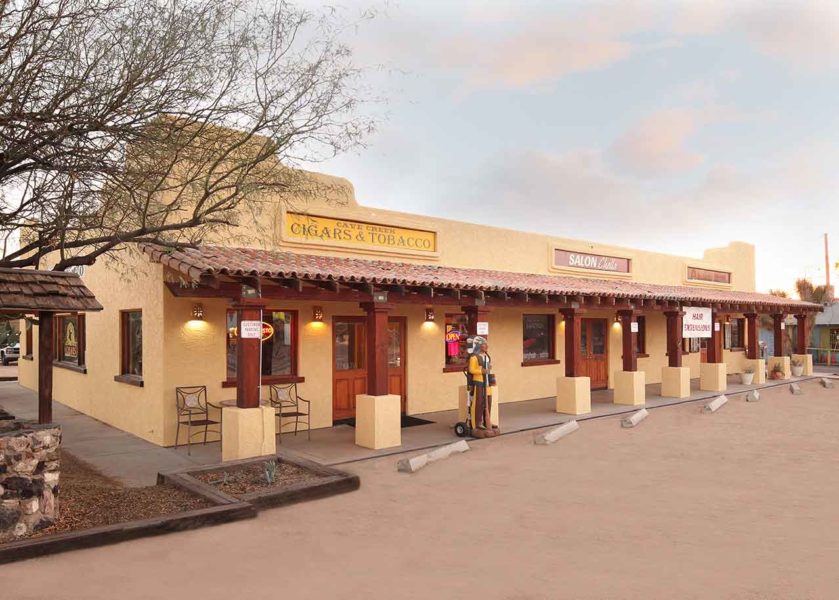
Photo courtesy of APV Engineered Coatings
A staple of the Spanish Colonial, Mission Revival, and Pueblo architectural styles, stucco is a naturally fire-resistant material primarily used as an exterior finish, though it may also be used indoors as well. Stucco is traditionally made from non-combustible materials like Portland cement, lime, sand, and water and is applied as a wet plaster that hardens to a dense-yet-permeable solid as it dries.
The nature of stucco means it can be applied over a range of surfaces including brick, concrete, metal, and even wood framing; when used as an exterior finishing solution, most modern stucco is applied in three coats overtop a metal mesh used for reinforcement. When installed correctly against other fire-resistant materials, a one-inch layer of stucco regularly achieves a one-hour fire rating.
Due to its permeability, however, stucco does have regional limitations as to where it may be applied. The material’s ability to absorb moisture means it is not ideal for installation in areas with high humidity, as this can lead to mold and mildew growth; stucco may also become brittle when exposed to extremely cold temperatures, making it a poor choice in the northeastern and northern Midwest states.
Stucco is best suited to hot, dry climates—like the American Southwest—where it helps improve energy efficiency in addition to a building’s overall fire resistance.
7. Steel
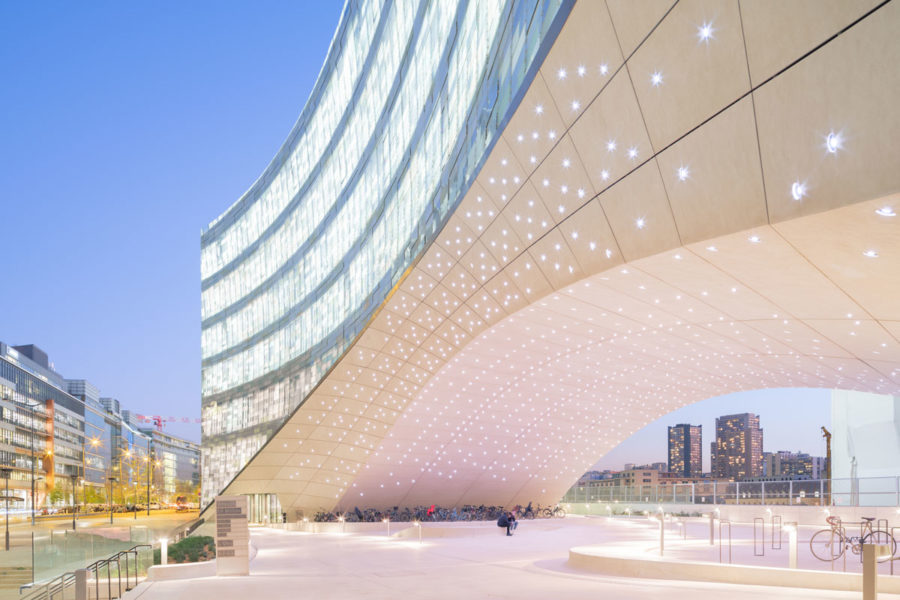
The new Le Monde Group Headquarters, designed by Snøhetta and SRA Architects, features a vaulted steel arch and a translucent, dynamic facade with more than 20,000 pixelated glass elements. Photo by Jared Chulski
When it comes to commercial and large-scale, multifamily residential buildings, steel is one of the most commonly used fire resistant building materials, as its high compressive strength makes it ideal for use in structural framework applications. Because it is made from iron, carbon, and small amounts of various elements, steel is considered non-combustible and thus boasts an inherent fire resistance.
It should be noted that steel’s overall fire resistance is relatively low when compared to other materials on this list. The strength of steel remains more or less unchanged when exposed to temperatures below 600℉, though it loses approximately 50% of its strength once temperatures crest the 1,000℉—something that becomes a problem when you consider that most building fires average between 1,000℉ and 2,000℉.
For this reason, structural steel elements are often protected by an additional layer of other fire resistant materials like gypsum and concrete or painted with intumescent coatings that help insulate against extreme temperatures and reduce the likelihood of structural failure.