Story at a glance:
- Low-carbon concrete refers to any concrete that is produced with a lower carbon footprint than conventional concrete.
- Concrete manufacturers can reduce their carbon emissions by as much as 70% by switching to renewable energy, reducing cement content, and implementing carbon capture and utilization technologies.
- CHRYSO, Holcim, and Prometheus Materials are among the leading providers of innovative low-carbon concrete solutions.
Concrete is the second most used substance in the world, coming in only behind water—and it’s not hard to see why. Concrete is an incredibly strong, durable, and versatile material that can be used to construct everything from buildings and bridges to roads and dams, making it a pivotal component of modern infrastructure.
Unfortunately concrete is also one of the most carbon-intensive materials there is, with the cement and concrete industry accounting for approximately 7 to 8% of the world’s carbon dioxide emissions, according to the Global Cement and Concrete Association (GCCA).
If humanity hopes to continue manufacturing concrete without putting the planet in jeopardy, we must find ways to reduce concrete’s carbon footprint—that is, we need low-carbon concrete.
What Makes Traditional Concrete Carbon-Intensive?
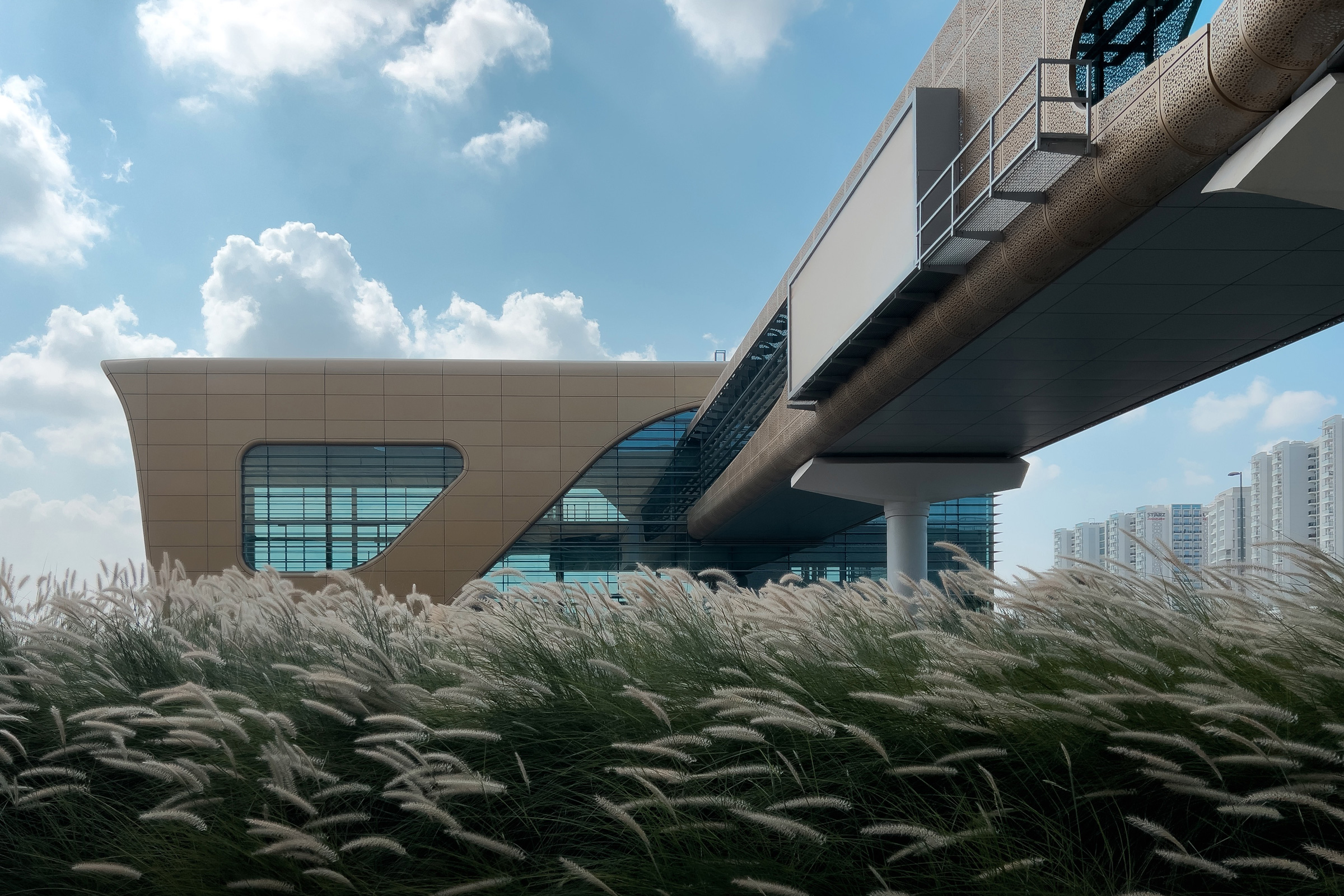
Traditional concrete is an incredibly carbon-intensive material due to both the burning of fossil fuels and natural chemical reactions that take place during the production of cement. Photo courtesy of the Global Cement and Concrete Association
Before we can understand what makes low-carbon concrete, well, low in carbon, we first need to understand why traditional concrete is such a carbon intensive material. “The construction industry is a significant contributor to greenhouse gas emissions,” Lisa Barnard, sustainability and customer engagement program manager for CHRYSO & GCP, told gb&d in a previous interview. “And traditional concrete has long been a major contributor to carbon emissions due to the energy-intensive production of cement.”
Cement is a key ingredient in concrete and is created by heating limestone—a type of carbonate sedimentary rock—in kilns to produce clinker, which is then ground down to a fine cement powder. “The production of cement contributes an estimated 85 to 95% of concrete’s carbon footprint. CO2 is produced during a chemical reaction that takes place when cement is being manufactured,” says Barnard.
Aside from these reactionary emissions, the high-heat kilns used to produce cement generate additional CO2 emissions. “Because a lot of those kilns don’t use high-quality energy sources; they’re using coal or dirty coke that create the most emissions,” Dan Getz, structures global practices director at HKS, a leading international architecture and engineering firm, told gb&d in a previous article.
What is Low-Carbon Concrete?
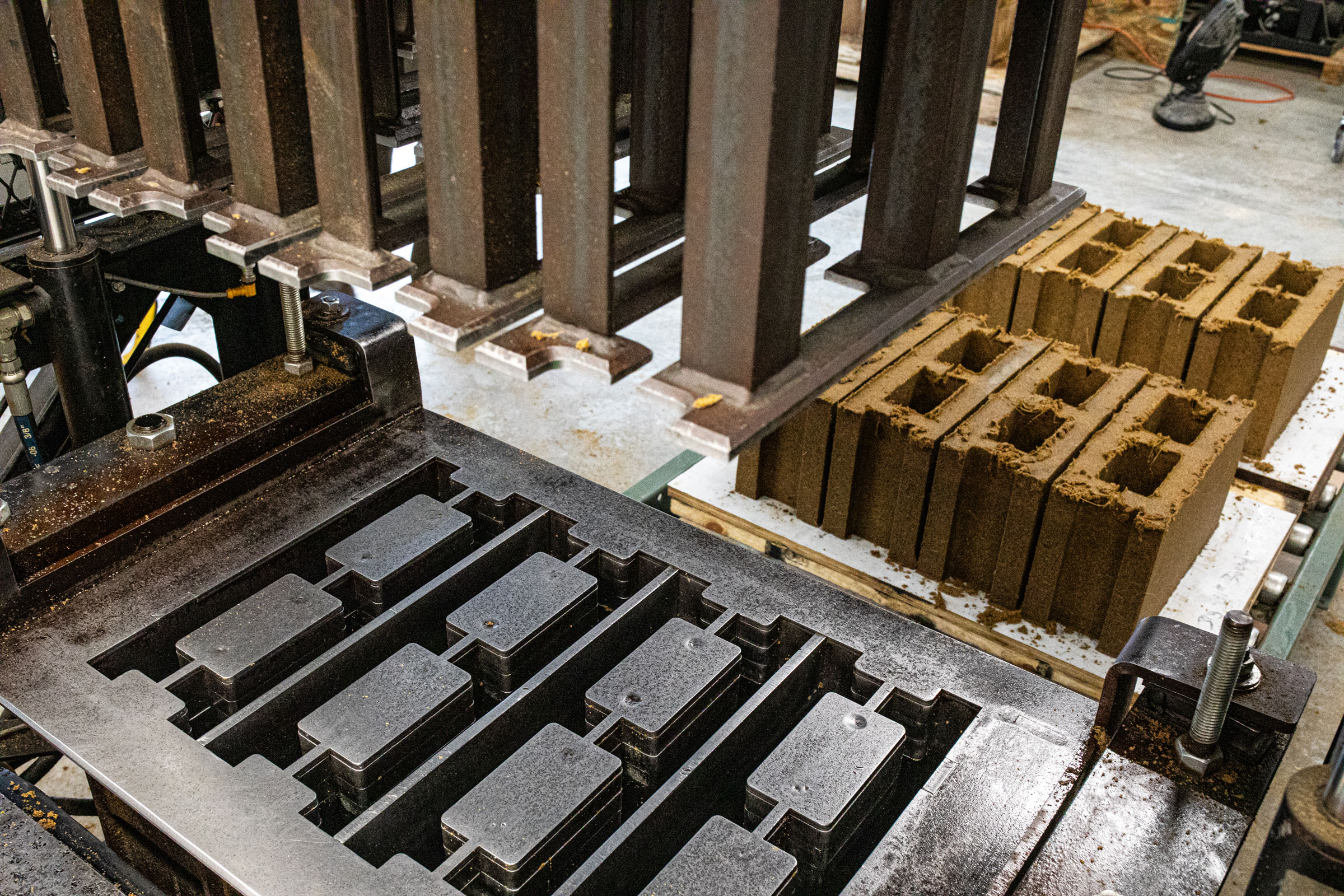
Low-carbon concrete refers to any concrete that is produced with fewer carbon emissions than conventional concrete. Depending on the methods used, low-carbon concrete may be responsible for 70% fewer emissions than traditional concrete. Photo courtesy of Prometheus Materials
Low-carbon concrete refers to any concrete produced with a lower carbon footprint than conventional concrete—which, admittedly, is a bit of a broad description, but that’s largely because there are so many ways to reduce the CO2 emissions of cement and concrete. Aside from this reduced carbon footprint, low-carbon concrete is designed to behave identically to its carbon-intensive counterpart.
Low-carbon concrete is an integral component of the GCCA’s 2050 Net Zero Roadmap, an ambitious climate pledge that aims to decarbonize the cement and concrete industry in order to produce carbon neutral concrete by the year 2050.
“The GCCA Roadmap targets CO2 reductions through greater efficiencies in cement, clinker, and concrete production, the rollout of renewable energy, the expansion of CCUS, better building design and construction, and maximizing the natural carbon absorbing benefits of concrete in the built environment,” Thomas Guillott, chief executive at GCCA, previously wrote for gb&d.
How is Low-Carbon Concrete Produced?
There are four key ways concrete manufacturers can lower the carbon footprint of their products: transitioning to cleaner energy sources, incorporating recycled/alternate materials, installing onsite carbon capture technologies, and via carbon utilization.
Depending on how these methods are implemented, concrete’s carbon footprint can be reduced by as much as 70%.
Switch to a Cleaner Energy Source
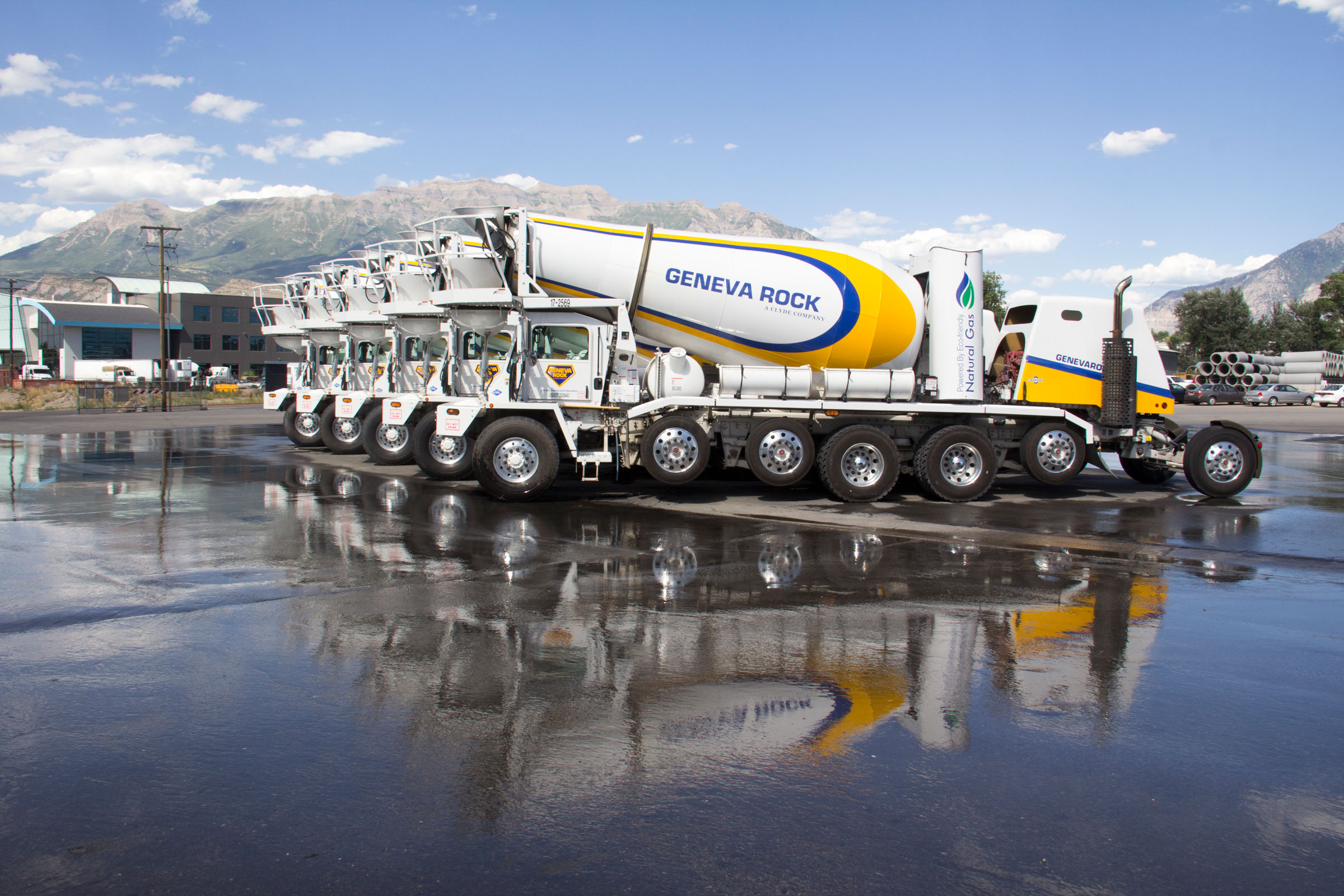
The burning of fossil fuels during the production of cement, mixing, and transportation of concrete is responsible for over half of all concrete-related emissions. Switching to cleaner energy sources—in terms of both plant and fleet operations—can help drastically reduce concrete’s CO2 emissions. Photo courtesy of Geneva Rock
Approximately 50% of the carbon emissions associated with concrete production are a result of burning fossil fuels like coal and oil, which supply kilns with the heat needed to fuse limestone, clay, and other materials into clinker.
Switching to cleaner fuel sources to power these kilns can reduce carbon emissions by a significant margin. Testing is ongoing to determine which clean energy sources are the most effective replacements, with biomass, wind, and solar being some of the most promising. Holcim—a leading building material supplier—for example, has made a commitment to power all of their US operations with 100% renewable energy by the year 2030. The company’s Fort Totten ready-mix concrete plant in Washington, DC was recently equipped with a solar array capable of generating between 1,300 and 1,500 MWh per year of renewable energy.
Clean energy can also help reduce the carbon emissions associated with the mixing and transportation of concrete to construction sites. Geneva Rock Products—one of the foremost concrete and asphalt providers in the state of Utah—for example, has taken steps to reduce their carbon emissions by investing in clean energy technologies. The company invested over $8 million in a compressed natural gas (CNG) fueling station and a fleet of 25 CNG Ready-Mix concrete trucks.
“The new cleaner running CNG fleet has significantly lower emissions than its diesel counterparts: 50% less fine particulate matter and 90% less carbon monoxide,” Nathan Schellenberg, vice president of specialty construction at Geneva Rock Products, previously wrote for gb&dPRO. “The impact of this investment is the equivalent of removing 8,000 cars per year from Utah roads.”
Use of Alternative & Recycled Materials
Because cement is the most carbon-intensive component of concrete, many carbon-reduction efforts seek to replace all or a portion of that cement with alternative or recycled materials. “Sustainable concrete often replaces a portion of Portland cement with alternative materials like fly ash, slag, or natural pozzolans,” Michael LeMonds, chief sustainability officer for Holcim US, previously told gb&d. “These substitutes reduce CO2 emissions and resource consumption.”
These materials—typically referred to as supplementary cementitious materials (SCMs)—not only help curb emissions but also prevent byproducts from other industries from entering the waste stream. Fly ash, for example, is produced by coal-fired steam generating plants and is considered an environmental hazard because it contains organic pollutants and toxic metals, while slag is a waste byproduct of the steel industry that can introduce heavy metals into the soil and water. When used in place of cement, however, these materials are effectively sequestered for the long term.
Onsite Carbon Capture & Storage
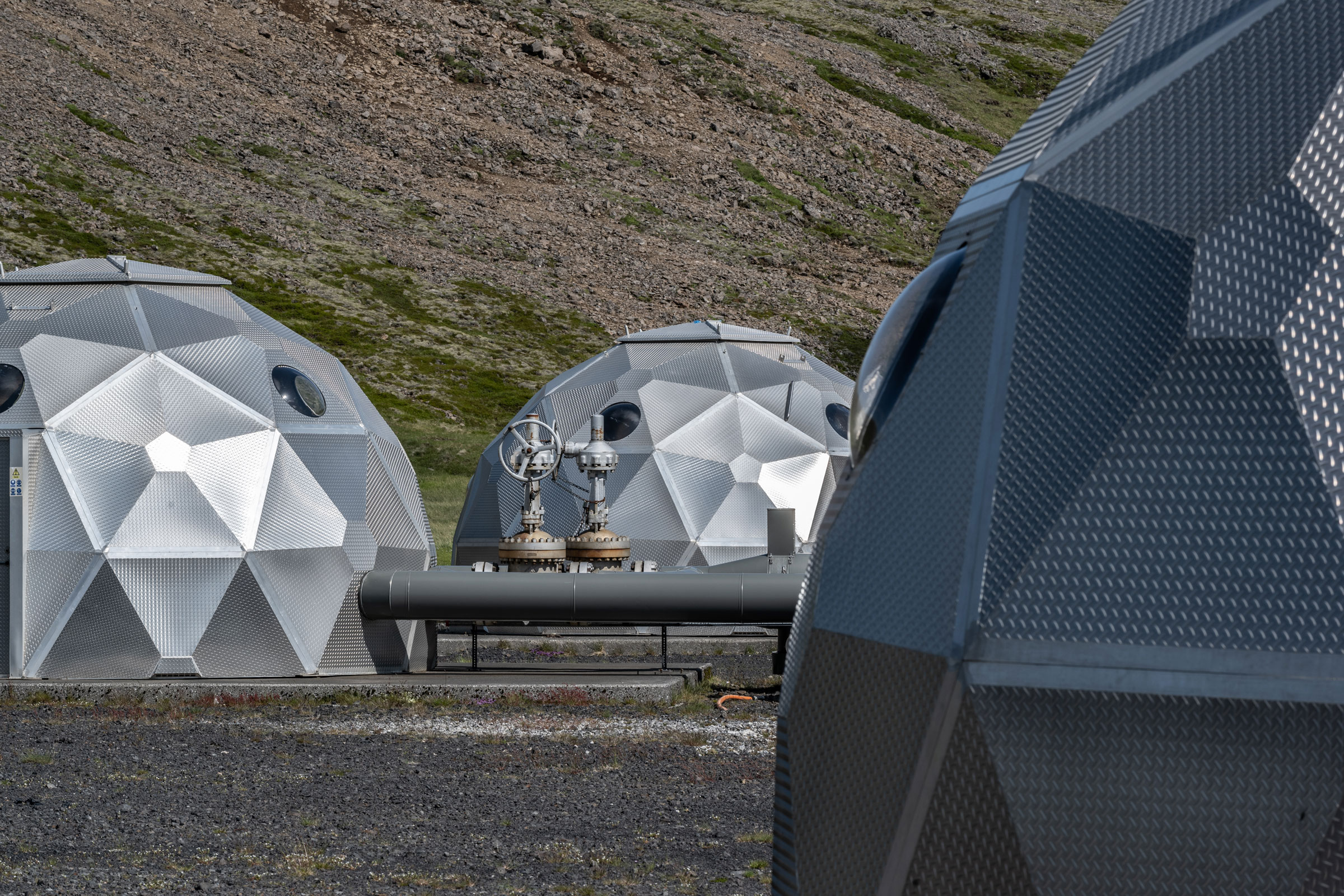
Cement and concrete plants can reduce their carbon emissions by capturing carbon as it is produced, compressing it into liquid form, and then storing it in geological formations. Photo courtesy of Carbfix
The environmental impact of concrete can also be reduced through the installation and use of on-site carbon capture technologies at cement plants. Carbon capture equipment is designed to separate CO2 from the other emissions and impurities produced during cement production, similar to how a filter might remove differently-sized particles from the air.
After the CO2 is captured and separated it is then compressed into a liquid form to make it easier to store and transport. Once compressed into liquid form this captured carbon can then be transported to a storage site, where it is typically injected into geological formations—like saline aquifers, deleted oil reservoirs, or basalt deposits—and left to mineralize to form carbonate rock.
Carbon Utilization
Carbon capture utilization (CCU) refers to the practice of using carbon captured during concrete’s manufacturing process either directly (i.e. not altered at the chemical level) or indirectly (i.e. transformed) in the production of other products like carbonated beverages and fertilizer.
Recent innovations in CCU, however, have provided concrete manufacturers with a new method for reducing their carbon emissions—storing captured CO2 within the very concrete they’re producing. Companies like CarbonCure Technologies, for example, have devised methods for injecting captured carbon into fresh concrete during the mixing process, where it then mineralizes and becomes permanently embedded within the concrete.
This CCU technique not only helps sequester carbon but also allows the concrete to maintain its compressive strength, enabling concrete producers to safely reduce their products’ overall cement content without negatively impacting performance, thereby reducing carbon emissions even further.
Low-Carbon Concrete Product Examples
As the demand for low-carbon concrete increases, more and more companies are beginning to experiment and find new ways to lower the carbon footprint of their products. CHRYSO, Holcim, and Prometheus Materials are just three of the leading providers of low-carbon concrete solutions, as we’ll see below.
CHRYSO®Quad
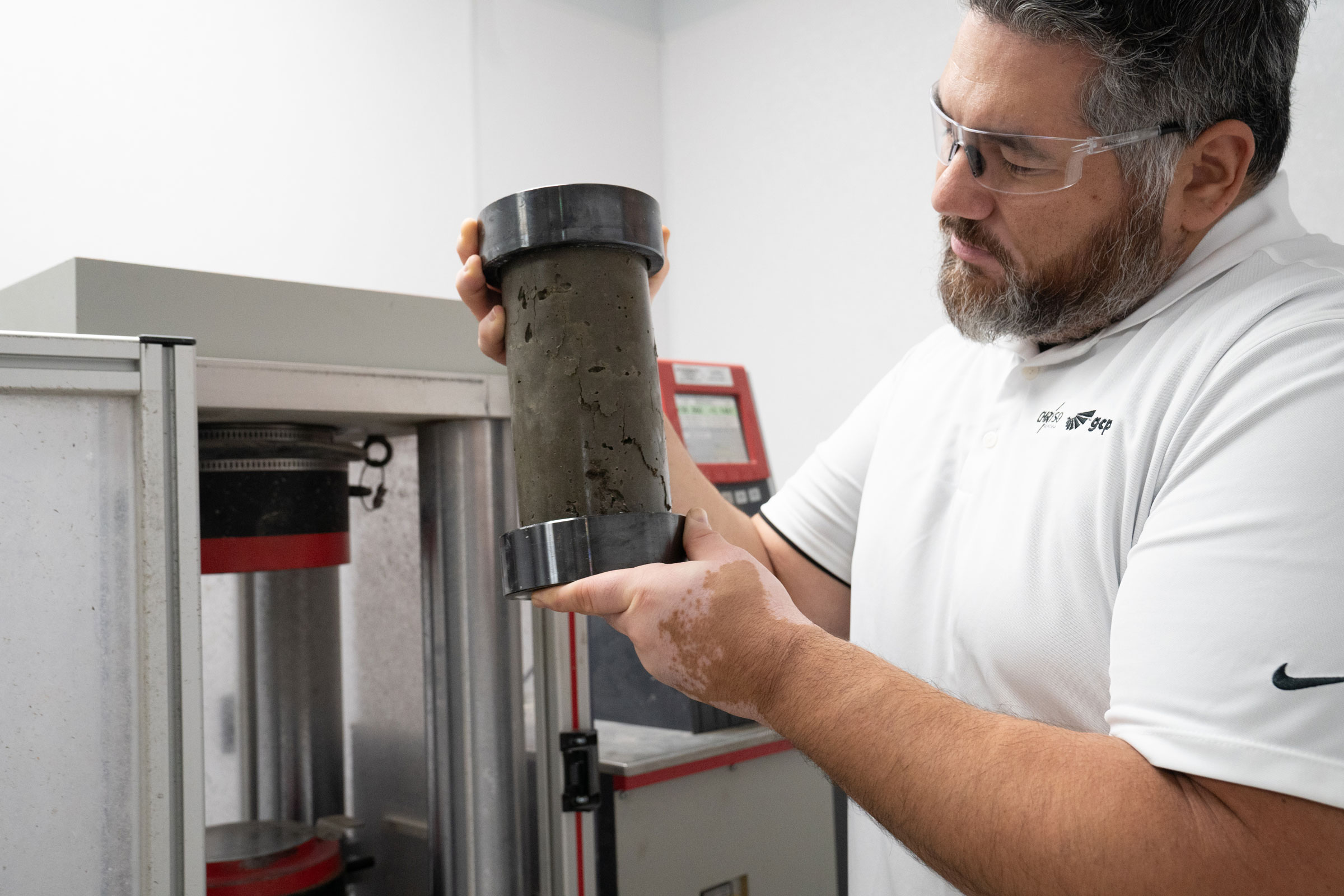
CHRYSO Quad helps reduce concrete’s carbon footprint by allowing lower quality, locally sourced aggregates be used in the manufacturing process, reducing transportation-related emissions. Photo courtesy of CHRYSO and GCP
Developed by CHRYSO and GCP, CHRYSO Quad is a unique concrete solution that allows locally sourced, lower quality complex aggregates—e.g. harsh manufactured sands, sands with lower gradation, and swelling clay contaminated aggregates—to be used in the concrete manufacturing process.
“The system is designed to enhance the use of complex aggregates such as harsh manufactured sands,” Barnard wrote in a previous gb&dPRO article. “Using lower quality, more complex sands, and aggregates, which are locally sourced, without compromising the concrete quality significantly contributes to reducing supply lead time, costs, and improving the concrete CO2 footprint through reduction in transportation impacts.”
Analyses from CHRYSO estimate that the use of locally-sourced materials results in anywhere from a 0.4 to 9% reduction in CO2 emissions.
ECOPact
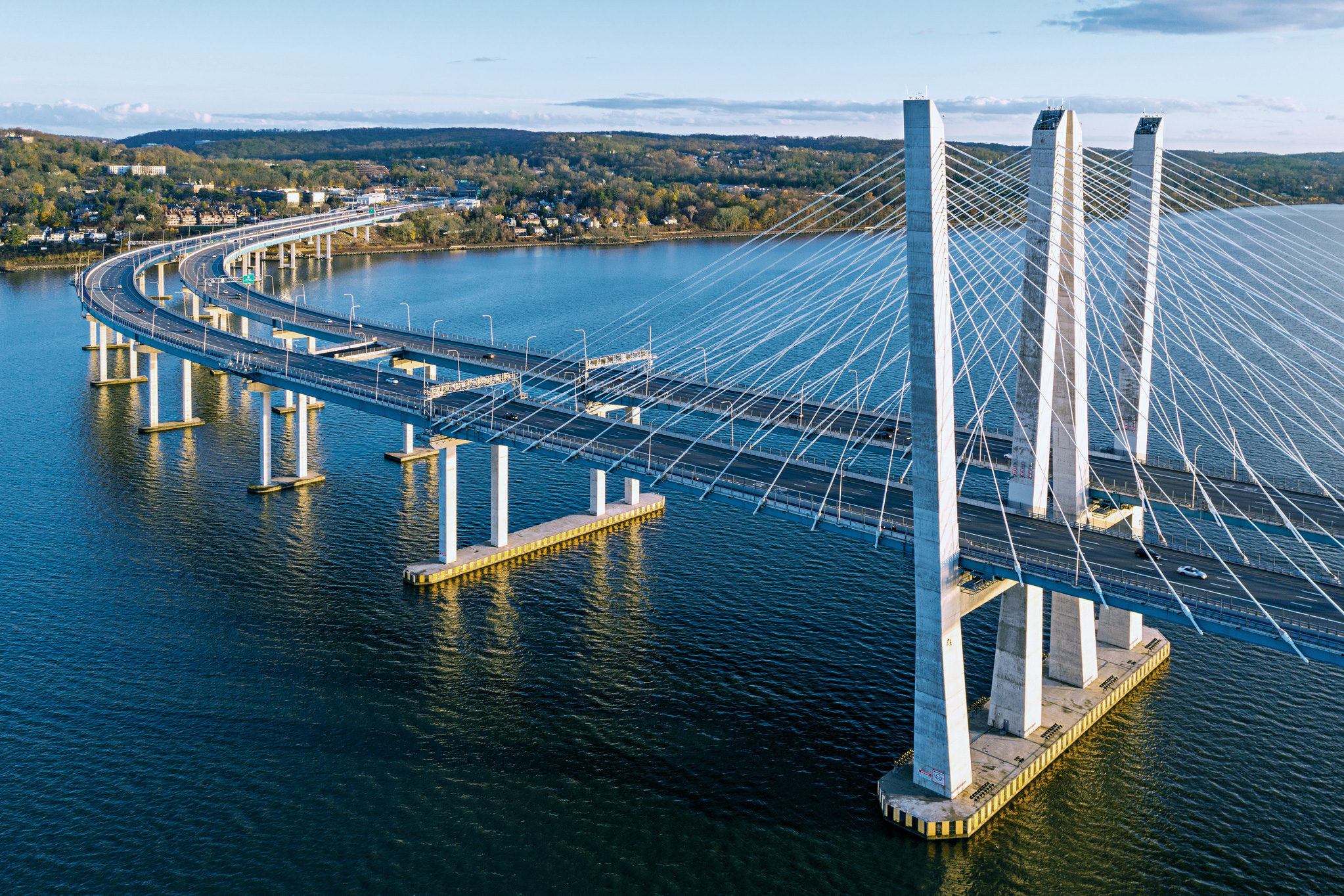
Holcim’s ECOPact line of products guarantees a minimum 30% reduction in embodied carbon and boasts the same strength as traditional concrete. Photo courtesy of Holcim US
Developed by Holcim, the ECOPact line of products is considered the concrete industry’s broadest offering of low-carbon concrete solutions for sustainable construction. ECOPact is available in a range of low-carbon levels starting at 30% lower embodied carbon and going all the way up to an impressive 90% carbon reduction with ECOPact Max.
ECOPact guarantees equal or better performance than conventional concrete and can be used in a variety of structural applications. “While many sustainable concrete solutions aim to reduce carbon footprints, the difference between them lies in the proprietary mix designs, performance attributes, and the extent of carbon reduction,” says LeMonds. “The uniqueness of ECOPact lies in its optimized blend of performance, durability, and sustainability.”
ECOPact’s high strength and top-tier performance is provided by an innovative combination of admixture technology and supplementary cementitious materials. The product line is produced locally, is recyclable, and can be specified to include recycled construction demolition materials
EnviroMix® SE
Also developed by CHRYSO and GCP, EnviroMix is a novel class of concrete strength enhancers that allows for a reduction in cement content without jeopardizing performance. The EnviroMix line includes EnviroMix SE, EnviroMix, and EnviroMix ULC, all of which offer varying levels of carbon reduction.
“Our EnviroMix® SE is an inventive strength enhancer offering for concrete that reduces the cement factor by approximately 10%,” Barnard told gb&d. “By using less cement, a major source of carbon dioxide emissions, the environmental footprint of concrete can be significantly reduced.”
The standard EnviroMix offers up to a 50% reduction in CO2 per square meter of concrete, while EnviroMix ULC promises over a 50% carbon reduction per square meter.
ProZero
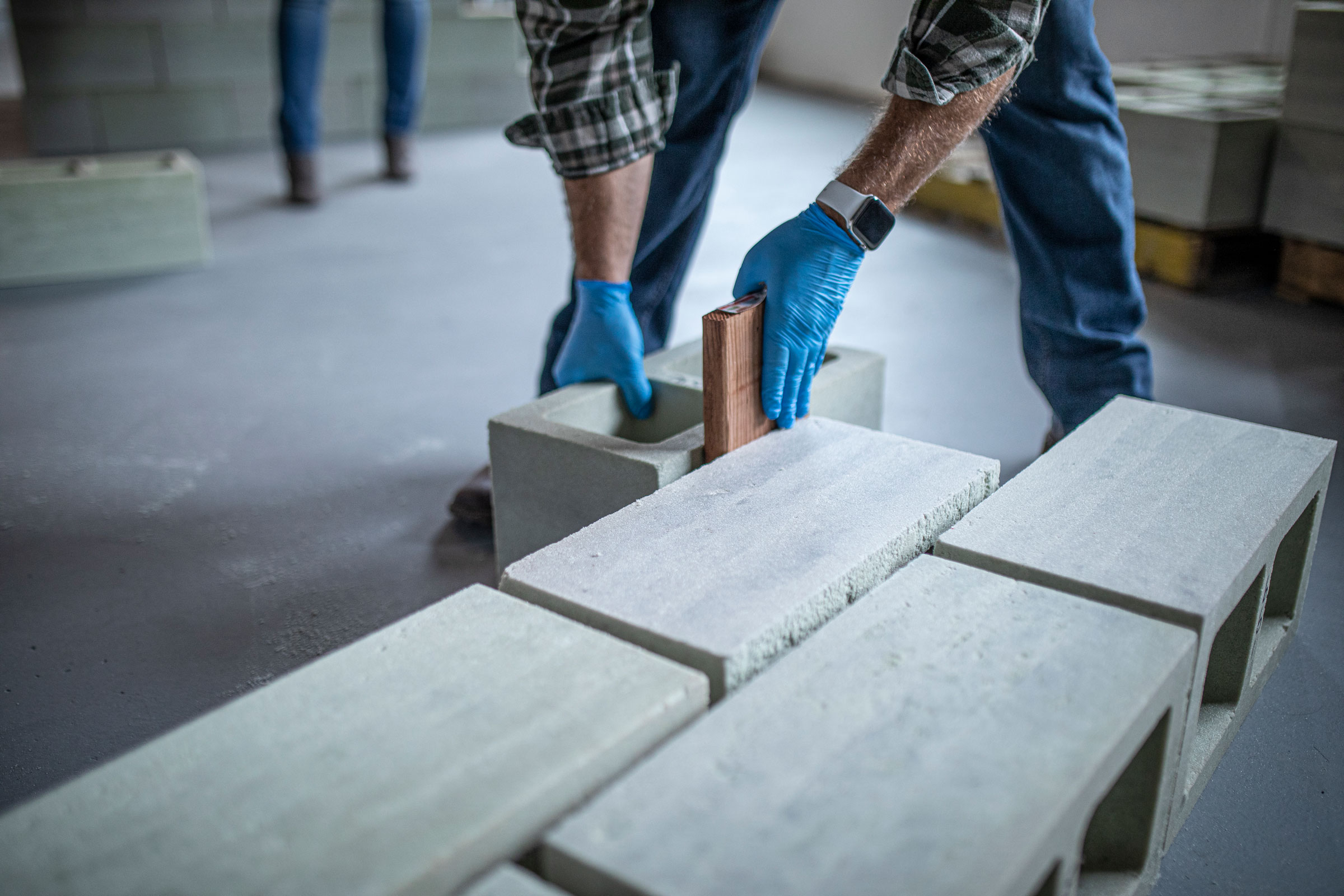
ProZero is an innovative carbon neutral concrete solution that replaces traditional limestone-based cement with a bio-cement made from biomineralized microalgae. Photo courtesy of Prometheus Materials
Prometheus Materials developed ProZero as a response to the growing demand for eco-friendly, low-carbon concrete—but rather than take an incremental approach to carbon reduction, Prometheus Materials aimed for full carbon neutrality by completely eliminating the need for limestone-based cement.
ProZero is a zero-carbon bio-concrete produced by stimulating microalgae to create biomineralized calcium carbonate—the same process that creates coral reefs and seashells—that is then dried and used as the basis for bio-cement. In this manner ProZero avoids the carbon-intensive operations involved in manufacturing traditional cement. Microalgae also absorbs carbon as it grows, meaning ProZero sequesters carbon throughout its operational lifespan, reducing its carbon footprint even further.
In addition to being a more sustainable concrete product, ProZero is also 15 to 20% lighter, possesses comparable compressive strength, and far exceeds the flexural strength of conventional concrete. “This degree of flexural strength will open up quite a few new market opportunities that traditional concrete just can’t fulfill,” Loren Burnett, president, CEO, and cofounder of Prometheus Materials, previously told gb&d.