Story at a glance:
- Polyaspartic floor coating is a cost-effective alternative to epoxy and polyurea due to its longer lifespan, increased durability, and chemical resistance.
- A range of facilities can benefit from the installation of polyaspartic flooring thanks to its varied properties and design options.
First developed in the early 1990s, polyaspartic floor coatings have become increasingly popular in residential, commercial, and industrial spaces thanks to their high durability and many desirable qualities, such as a fast curing time, UV resistance, and easy maintenance.
Polyaspartic floor coatings are also favored for their reduced usage of toxic volatile organic compounds (VOCs) and relatively quick application times, both of which make the coating a healthier and more sustainable option.
But what exactly are polyaspartic floor coatings in the first place?
What are Polyaspartic Floor Coatings?
In the fundamental sense, polyaspartic floor coatings are what’s known as two-part concrete-coating systems, meaning they consist of both a primer/base-coat and a clear topcoat—pigments and/or flakes can also be added to the base-coat for customization purposes.
“Polyaspartic” refers to the coatings’ composition—all polyaspartic materials (or “esters”) contain aliphatic polyurea, a type of elastomer derived from the reaction of an aliphatic diamine and an aliphatic polyisocyanate. Polyaspartic esters are extremely durable but are also capable of absorbing impacts without breakage, making them an ideal component for floor coatings.
Advantages of Polyaspartic Floor Coatings
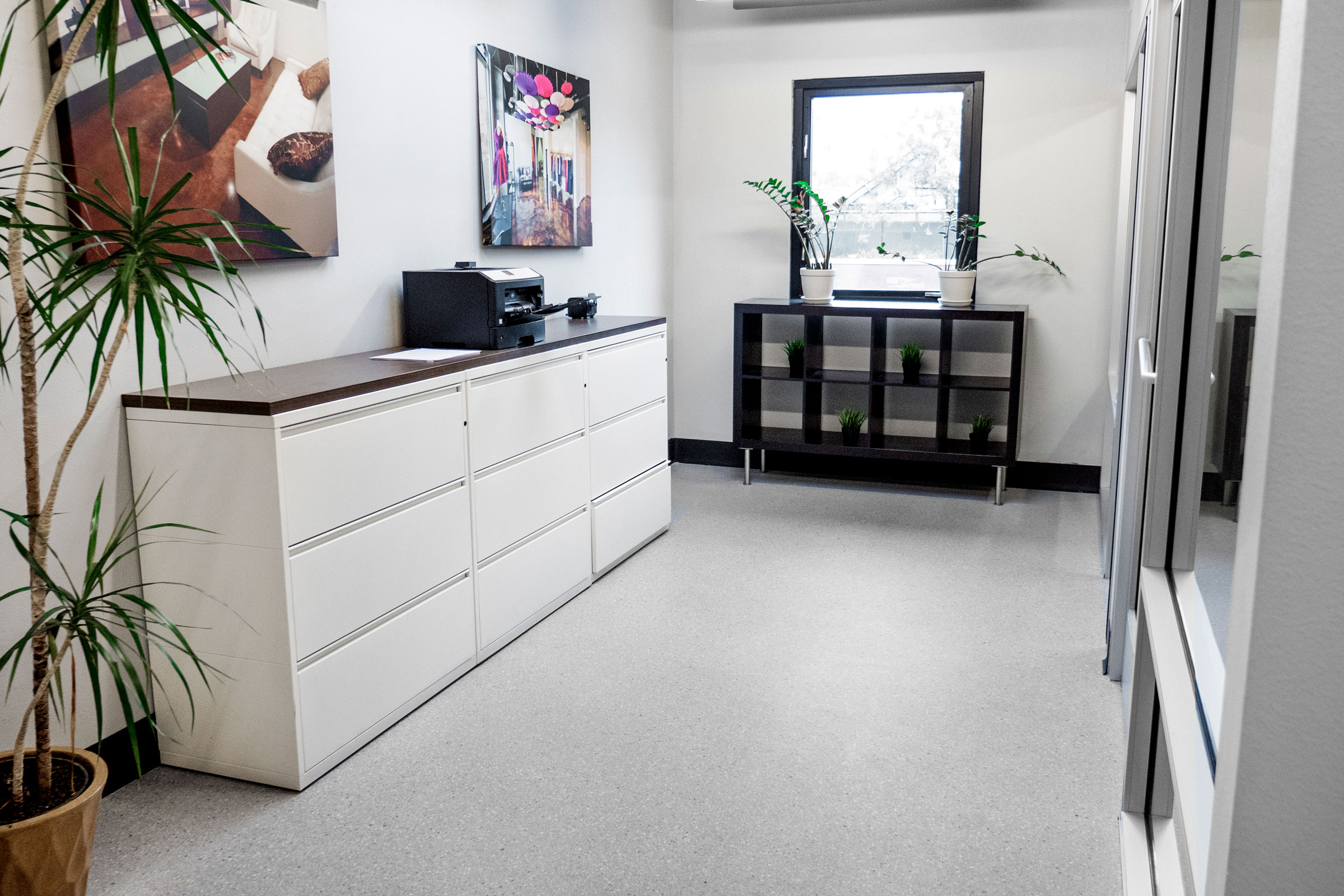
Polyaspartic floors offer many design options to compliment a range of commercial, residential, and industrial settings. Photo courtesy of Westcoat
What makes polyaspartic floor coatings so desirable? Let’s take a look at a few of their main advantages in the sections below.
Durability
First and foremost, polyaspartic floor coatings are extremely durable—on average, polyaspartic floors last for upwards of 20 years and are capable of withstanding heavy foot traffic, abrasives, and forceful impacts with ease. This is largely due to the fact that polyaspartic esters are capable of flexing, meaning they actually absorb and redistribute force rather than cracking or shattering under it.
Fast Curing Time
Another benefit of polyaspartic floor coatings is their fast (but not too fast) curing time. Once applied, polyaspartic floors are capable of handling foot traffic in as little as four to six hours and vehicle traffic in 24 hours. This is much quicker than, say, epoxy floors, which typically take anywhere from three to seven days to cure completely—but still slower than polyurea coatings, which have a tendency to dry out quickly.
Chemical Resistance
Thanks to the usage of aliphatic amine-terminated polyurea—a strong-bonded polymer—polyaspartic floor coatings have a fairly high chemical resistance to neutral and basic pH solutions, making them an ideal choice for facilities that utilize strong cleaning products or who handle certain alkaline chemicals.
UV Resistance
Polyaspartic floor coatings that contain aliphatic isocyanates and their derivatives have a high resistance to light and UV damage, which means they won’t fade or yellow over time when regularly exposed to the sun—a marked improvement over both epoxy and polyurea coatings. This makes polyaspartic coatings extremely well-suited to use in outdoor spaces or in buildings with large atriums/skylights.
Low VOC Emissions
One of the most important advantages associated with polyaspartic floor coatings is their status as low-to-zero volatile organic compound (VOC) products. When it comes to floor coatings and sealants, VOCs are typically found in the solvents they use to ensure a high-quality, long-lasting finish; over time these sealants evaporate and release VOCs into the air, making occupants more susceptible to organ damage, central nervous system damage, and certain cancers.
Fortunately most polyaspartic coatings don’t make heavy use of solvents, making them either low-VOC (50 g/l or less) or zero-VOC (5 g/l or less).
Versatile Design Options
An often overlooked benefit of polyaspartic floor coatings is their versatility when it comes to design—a feat made possible through the addition of color pigments, vinyl paint/quartz chips, or certain metallic pigments. This versatility means polyaspartic floors can be made to match, complement, or accentuate their surroundings.
Easy Maintenance
After installation polyaspartic floors are very easy to maintain—simply sweep up dust and larger debris as needed with a soft-bristled broom or microfiber mop and clean the surface every one to two weeks with a neutral or basic pH cleaner. Try to avoid the usage of highly acidic cleaners, as these can weaken the molecular bonds that hold polyaspartic esters together and compromise the coating’s structural integrity.
Slip Resistance
Due to their slightly textured finish, polyaspartic floors are fairly slip-resistant—much more so than epoxy floors—which makes them an ideal choice for areas with high foot-traffic. To reduce potential slippage even further, anti-slip additives can be added to the coating before application.
Antibacterial
Lastly, polyaspartic floor coatings are considered to be antibacterial—or at the very least, bacteriostatic—due to the fact that they contain no welds, seams, or grout lines for bacteria to gather in.
Polyaspartic coatings can also be modified to exhibit antimicrobial properties through the addition of certain additives, which makes them much more resistant to bacteria, mold, and fungi. Ultimately these qualities make polyaspartic floors ideal for hospitals and labs that require extremely clean, sterile environments.
Common Problems with Polyaspartic Floors
Of course, no coating is perfect, and polyaspartic floors have their fair share of potential issues. Some of the most common problems include:
Moisture Problems
One of the most frequent issues associated with polyaspartic floors is moisture, specifically the moisture content of the concrete on which the coating is being applied. If the moisture content of the concrete is too high, the polyaspartic coating will not be able to penetrate far enough into the concrete to bond properly. When this happens the coating simply sits on top of the concrete, which can result in decreased durability, longer curing times, and peeling.
In order to avoid moisture-related problems, a moisture content test should be conducted before installation—if the concrete has a high moisture content, a moisture barrier can be put down before applying the polyaspartic coating.
UV Sensitivity
We know what you’re thinking: Isn’t UV-resistance one of the benefits of polyaspartic floor coatings? To which we’d reply, yes, but not all polyaspartic coatings are made to be UV-resistant. If you fail to specify that your project needs to be able to withstand UV light, you may end up with a UV-sensitive polyaspartic coating that is liable to fade over time.
Acidic Chemical Damage
While the specific composition of polyaspartic coating allows it to withstand a wide variety of chemicals, it is susceptible to damage from highly acidic chemical compounds, such as those found in some industrial-strength cleaners. This is due to the fact that the amino acids used to bond polyaspartic molecules together are easily weakened by acidic compounds, which in turn weakens the coating itself—this can then lead to cracking, peeling, and other damages that may negate the coating’s desirable qualities.
Temperature Sensitivity
Finally, certain types of polyaspartic floor coatings are notoriously temperature-sensitive at the initial application phase and may not cure properly below 55℉/13℃. In indoor spaces with adequate climate control systems, this shouldn’t be a problem—but it can make applying the coating more difficult during the winter, especially if applied outdoors.
Fortunately, there are many types of polyaspartic coatings available, some of which are engineered for low-temperature application.
Polyaspartic Floors vs Epoxy
Chemically speaking, both polyaspartic coatings and epoxy coatings are resin-based polymers—epoxy, however, contains epoxide and forms through a compound’s reaction with epichlorohydrin and an acidic hydroxy group, while a polyaspartic forms through the reaction of an aliphatic diamine and an aliphatic polyisocyanate.
Chemical Resistance
Thanks to their chemical makeup, both epoxy and polyaspartic floors are fairly chemical-resistant, though some water-based epoxy coatings offer little-to-no chemical resistance at all. Both coatings’ chemical resistance, however, can be improved through the addition of certain additives.
Design & Customization
In terms of customization, polyaspartic and epoxy floors are fairly well-matched, albeit in different ways: Polyaspartic floors can be flaked—something epoxy doesn’t handle very well—but epoxy floors typically support a wider range of color options. As a result polyaspartic floors are more common in commercial centers and garages, while epoxy floors have become popular in homes themselves.
Durability & Application
Polyaspartic coating is, however, more durable than epoxy, with the former boasting an average lifespan of 20 years, whereas the latter typically only lasts 10 to 15 years, as epoxy is neither as flexible nor as abrasion-resistant. Polyaspartic coating also offers better UV resistance than epoxy does and cures at a much faster rate, being able to sustain vehicle-traffic after only 24 hours—epoxy, on the other hand, typically requires a full seven days to finish curing.
Cost
Where epoxy has polyaspartic coating beat, however, is price. Typically, epoxy costs between $4 and $7 per square foot, whereas polyaspartic usually costs between $6.00 and $9.00 per square foot.
Polyaspartic Floors vs Polyurea
Due to the fact that polyaspartic coatings are a type of polyurea coating, the differences between the two are slight, but still important—it may be easier to think of polyaspartic coating as an upgraded version of polyurea coating.
Polyaspartic coating is slightly more durable than polyurea, has a better resistance to UV light, and is easier to apply because it has a longer pot life, meaning it doesn’t dry out as fast. Polyurea’s extremely quick drying time also weakens its bond with the concrete, reducing its life expectancy to only 15 years compared to polyaspartic coating’s 20-plus years.
Of course, polyurea coating is also cheaper than polyaspartic coating, averaging out to between $2 and $7 per square foot.
How are Polyaspartic Floor Coatings Applied?
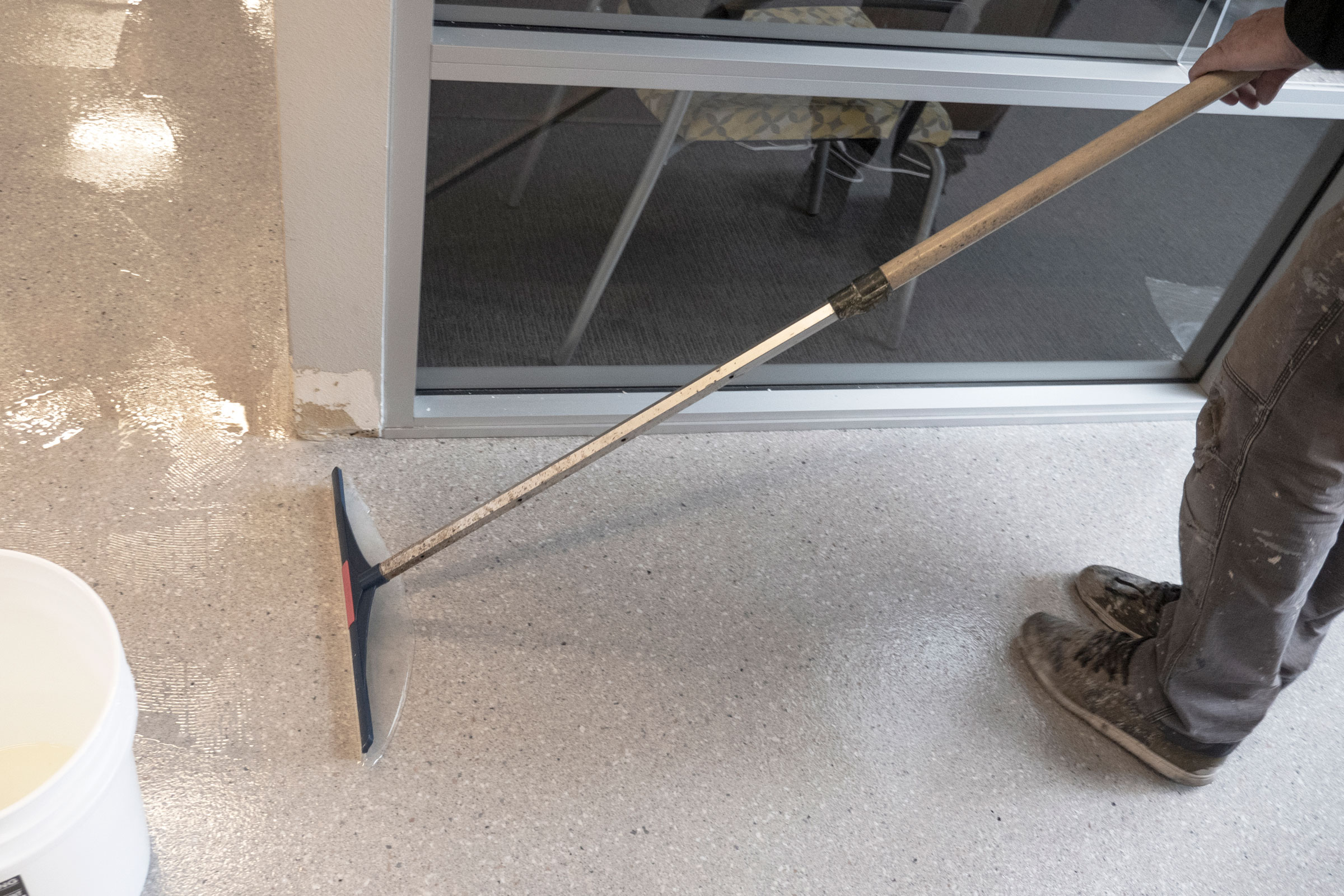
Polyaspartic floor coatings are fairly simple to apply and finish curing in as little as 24 hours. Photo courtesy of Westcoat
Regardless of whether you’re planning on applying polyaspartic coating yourself or if you’re leaving it to the professionals, it’s always a good idea to familiarize yourself with the process so that you know what to expect. In the general sense, polyaspartic coatings are applied as follows:
Step 1: Surface Preparation
Before polyaspartic floor coating can be applied to concrete, the concrete’s surface needs to be prepared. This entails a thorough cleaning of the concrete itself, followed by grinding the concrete to remove any imperfections or inconsistencies, which helps ensure that the polyaspartic coating will adhere and set properly.
Step 2: Inspection
After the surface is prepared, an inspection of the concrete is conducted to verify that it is ready for coating. If any damages are found during the inspection process, they should be repaired before moving forward with polyaspartic coating’s base-coat application.
Step 3: Primer & Base Coat Application
Once the floor has been inspected a primer and base coat of polyaspartic coating is applied (if any pigments are being added, it is during this stage). Most professionals use either the dip-and-roll method, ribbon-and-roll, or spray-and-roll method to lay down the initial primer and base-coat.
In some cases, epoxy may be used as the primer layer.
Step 4: Flaking (Optional)
After the base-coat has been laid down, flakes or chips may be added for aesthetic purposes to create a speckled look. In most cases, flakes—be they quartz, paint, or vinyl—will add around 8 mils to the floor’s thickness, but do not otherwise impact the coating’s functionality.
Once the flakes have been added, any excess is scraped off with a floor scraper and loose chips are vacuumed up.
Step 5: Topcoat Application
With the flakes in place, the final layer of clear polyaspartic coating can be poured and spread out evenly using a roller. This topcoat layer is typically between 6 mils and 18 mils—a thinner topcoat layer may create a slightly more textured surface if flakes have been applied underneath.
Step 6: Curing
After the final coat of polyaspartic coating is applied, the curing (or setting) process begins. For polyaspartic floors to cure in a timely manner, they should be kept at temperatures of 77℉/25℃ or above and left untouched for four to six hours, at which point they can handle light foot-traffic. Allow a full 24 hours for curing before allowing vehicle-traffic on polyaspartic floors.
What Facilities Benefit from Polyaspartic Floor Coatings?
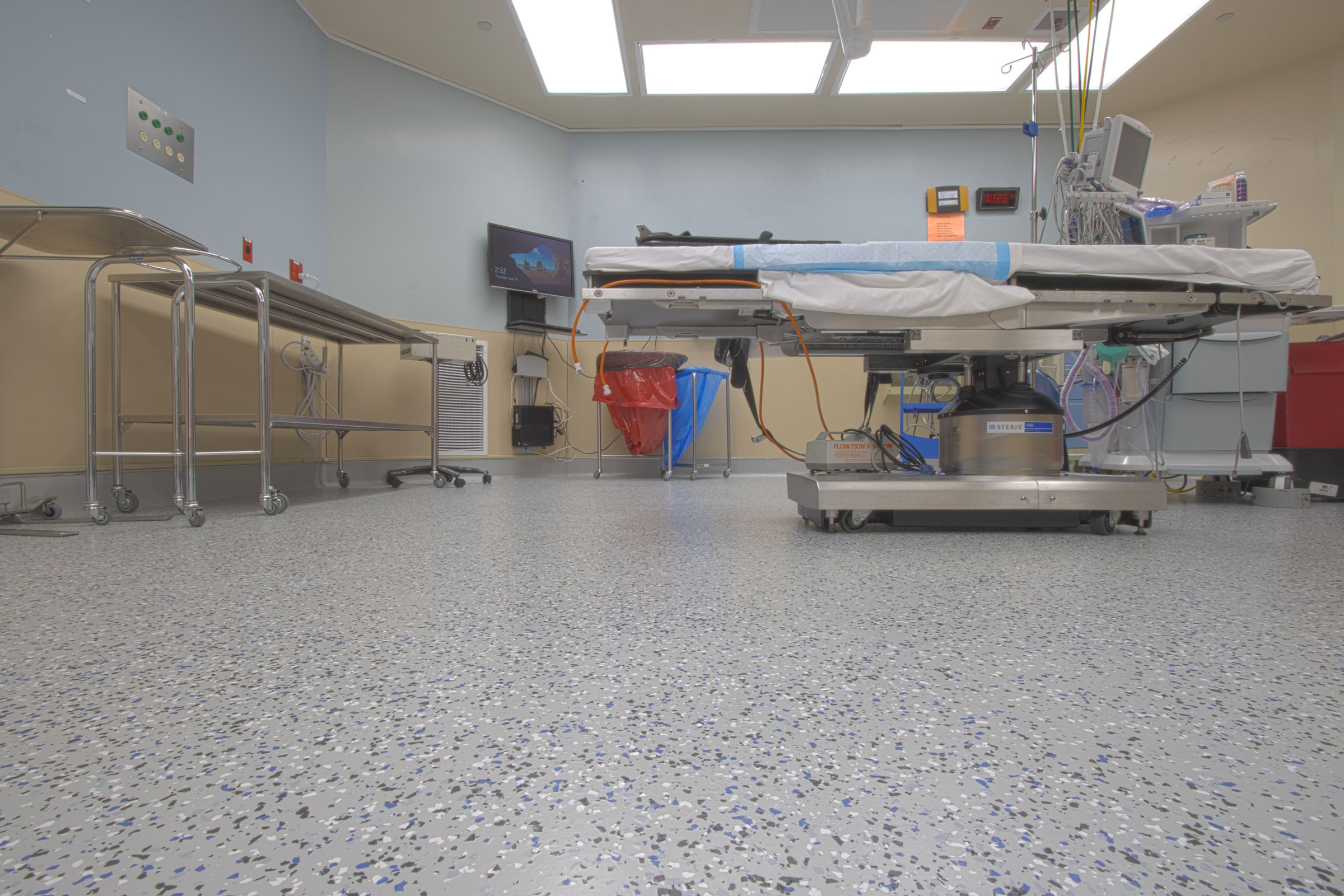
Polyaspartic floors are ideal for use in medical facilities due to their antibacterial qualities. Photo courtesy of Bona
Due to their impressive qualities and numerous advantages, polyaspartic floor coatings are the ideal choice for a range of different facilities, including:
Industrial Facilities
First and foremost, industrial facilities—such as warehouses, manufacturing plants, etc.—can benefit greatly from the installation of polyaspartic floors. Due to their quick installation time, polyaspartic floors reduce the amount of production time lost, which in turn cuts back on profit loss. Polyaspartic coatings are also durable and scratch-resistant, which means companies don’t need to worry about heavy machinery damaging their floors.
Commercial Spaces
Polyaspartic floors are also commonly used in commercial spaces like showrooms, malls, and shopping centers, as their high-durability allows them to handle high foot-traffic with ease. Add to the fact that polyaspartic floors are easy to maintain, won’t yellow over time, and are aesthetically-pleasing and it’s no wonder that they’ve become so popular in these commercial areas.
Health Care Facilities
Hospitals and other health care facilities can benefit from the application of polyaspartic floor coatings due to their antibacterial properties—which help reduce mold and bacteria growth, thereby preventing sickness—and ability to withstand the strong cleaning agents necessary to maintain a hygienic environment.
Furthermore, health care facilities will appreciate the lower-levels of toxic VOCs produced by polyaspartic floor coatings, which in turn improves air quality and reduces the likelihood of developing certain cancers.
Residential Spaces
As one of the most popular locations for polyaspartic floors, residential spaces—particularly garages—benefit from the installation of polyaspartic coating due to its high chemical/stain resistance. Oil and other vehicle-related fluid spills are common in these types of spaces, but polyaspartic floors won’t stain as long as any and all spills are quickly cleaned up.
Homeowners can also count on polyaspartic floors to be low maintenance and durable, reducing the amount of time and energy spent on repairs.
Sports Facilities
You might be surprised to learn that sports facilities can also benefit from polyaspartic floors, in large part thanks to their slip-resistant nature—a crucial component in preventing unnecessary injuries on both the court and in the stands. Polyaspartic floors are also highly resistant to staining, which is a necessary feature in places where food and beverages are often spilled.
Finally, sports facilities have plenty of design options when it comes to polyaspartic floors, making it that much easier to keep in line with the stadium’s color scheme and aesthetics.
Food and Beverage Facilities
Lastly, food and beverage facilities can benefit from the application of polyaspartic floor coatings due to their antibacterial, slip-resistant, and chemical-resistant properties. Polyaspartic floors help food and beverage facilities prevent the spread of foodborne illnesses, reduce the risk of workplace accidents, and limit damages incurred through the use of corrosive cleaning products.
Cost of Polyaspartic Floor Coatings vs Other Coatings
Discerning readers will have already noticed that “affordable” isn’t listed as one of the advantages associated with polyaspartic floors—and it’s true that, on average, polyaspartic coatings cost more than epoxy and polyurea floor coatings. A complete cost comparison is included below (keep in mind that exact prices will ultimately depend on your location and the company performing the installation):
- Polyaspartic: $6 to $9 per square foot
- Epoxy: $3 to $7 per square foot
- Polyurea: $2 to $7 per square foot
These higher costs, however, are typically warranted due to the fact that polyaspartic floor coatings are of a higher quality and have longer lifespans compared to other coatings, meaning they won’t need to be replaced as frequently.
How to Maintain & Care For Polyaspartic Floor Coatings
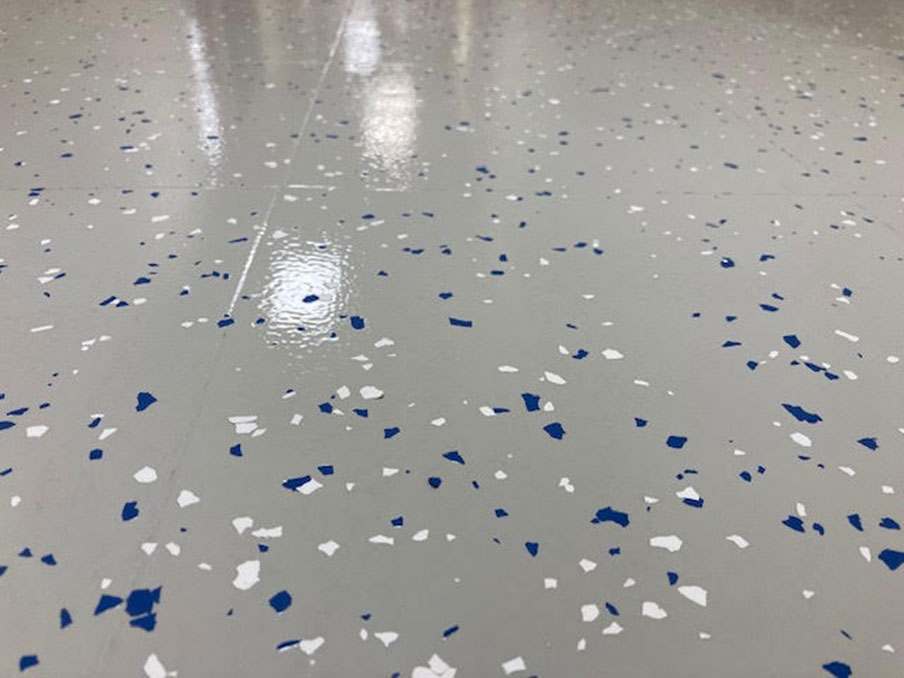
Polyaspartic floors can last for upwards of twenty years as long as they are properly maintained. Photo courtesy of Bona
In order to get the most out of a polyaspartic floor, there are a few things you should know about the maintenance and care process.
Regular Cleaning
In general it’s recommended that polyaspartic floors be cleaned at least once a week to keep them in good condition. Of course, what constitutes “regular cleaning” largely depends on the needs of the facility itself—a hospital, for instance, may require their polyaspartic floors be cleaned every day, whereas a residential garage may not need to be cleaned as frequently.
In any case it’s a good idea to sweep or vacuum up dirt, dust, and debris at least once a week and deep clean with a neutral pH floor cleaner once every one to two weeks to keep a polyaspartic floor from building up a layer of grime.
Avoid Harsh Chemicals
While it’s true that polyaspartic floors are better than most at handling strong chemicals and corrosives, regular exposure to these products will decrease the coating’s lifespan—especially if those chemicals are highly acidic, as explained in previous sections.
Address Spills Promptly
To minimize damages incurred from accidental exposure to chemicals, corrosives, and acidic products, any spills should be addressed and cleaned promptly to keep polyaspartic floors in good condition and prevent unwanted staining.
Regular Inspections
Lastly, proper maintenance includes regular inspections—in most cases, it’s a good idea to have your polyaspartic floor professionally inspected once every five years to ensure that there aren’t any serious issues that may jeopardize the coating’s functionality.
Where Can You Buy Polyaspartic Floors?
If you’d like to implement polyaspartic floor coating in your next project, you have several options when it comes to buying the necessary materials:
- Flooring companies: If you’re looking for the most professional and efficient installation, a flooring company that specializes in polyaspartic floors is your best bet—just keep in mind that the labor costs associated with this option will be higher.
- Contractors: Alternatively, you could have contractors install your polyaspartic floor, an option that is typically cheaper than hiring a dedicated flooring company—this option is, however, slightly more risky when it comes to installation quality.
- Online: If you’re looking to apply polyaspartic coating yourself as part of a personal project, you might consider purchasing the supplies online—companies like Rust-Oleum and Sherwin Williams both sell high-quality polyaspartic products.
FAQs
How long do polyaspartic floors last?
As long as they are properly maintained, polyaspartic floors are capable of lasting 20-plus years before needing to be replaced. Ultimately, however, a polyaspartic floor’s lifespan will depend on a couple of factors beyond routine maintenance, such as how the floor is used and what sort of traffic it is subjected to on a regular basis.
In a commercial setting—such as in a mall—polyaspartic floors can easily last upwards of 20 years, even if they receive a lot of foot traffic. Polyaspartic floors that are installed outdoors as, say, a driveway, may not last quite as long due to exposure to the elements and regular vehicle-traffic.
Are polyaspartic floors slip-resistant?
Yes—polyaspartic floors are fairly slip-resistant as is and can be made to be even more-so by adding anti-slip additives, making them ideal for shopping centers, schools, warehouses, and other such facilities that see a lot of foot-traffic.
Are polyaspartic floors sustainable?
Due to their long lifespans, quick application time, and the fact that they are produced using fewer amounts of hazardous materials than other floor coatings, polyaspartic floors are considered to be relatively sustainable.
In Conclusion: Are Polyaspartic Floors Worth It?
Despite the higher costs associated with installation, polyaspartic floors are a worthwhile investment due to their quick curing times, long lifespans, and low maintenance. Thanks to their reduced usage of VOC-producing solvents, polyaspartic coatings don’t release toxic compounds into the air over time, leading to improved occupant and employee health.
What’s more, their wide range of design options means polyaspartic floors can be customized to suit a variety of facilities—schools, hospitals, shopping malls, stadiums, etc.—while still meeting their unique requirements.
Regardless of whether you’re looking to remodel your garage or if your company is looking to put down new flooring, a polyaspartic floor will provide the durability you need without compromising your efforts to design sustainably in the process.