You may have recently heard the term “resilient design” being used more frequently within the construction and architectural industries. And with extreme global weather events and consumer concerns regarding sustainability, discussion around best building practices and resilient construction and materials has only increased.
So what does building resiliently mean exactly? The Resilient Design Institute defines resilient construction as “the capacity to adapt to changing conditions and to maintain or regain functionality and vitality in the face of stress or disturbance.” It is the improvement of existing homes or attention to durability in new construction to help a structure last longer and be able to withstand more intense conditions.
Resilient Construction: Demanded by Homeowners and Climate Alike
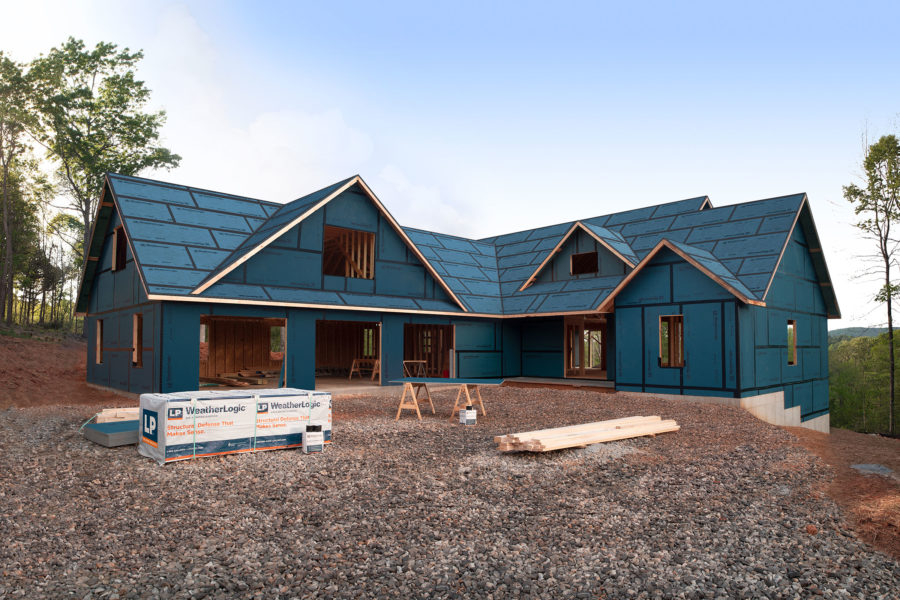
Photo courtesy of LP Structural Solutions
Resiliency has extended beyond a hot topic or trend into an expectation for many current and prospective homeowners. As cofounder of Instruction Construction, Mark LaLiberte points out: “Homeowners are expecting change. They are expecting higher quality products that will protect their homes. And it is up to the builders to rise to the occasion and build in these improvements that lower risk and improve customer satisfaction.”
Healthy, resilient homes now rank at a higher priority than location in the minds of homeowners. This only increases in younger generations, which tend to be more conscious when it comes to sustainability. There has been a trend in homeowners who desire to stay in one home for longer periods of time, since it can be a more sustainable option than frequent moves. Therefore, demand for resilient homes has risen for both new and old homes.
Beyond general consumer demand for sustainability, though, weather often requires that a home be built with resilient materials. From destructive hurricanes to fierce tornadoes, catastrophic events are happening with alarming frequency. According to recent NASA reports, global temperatures are rising, and ice sheets have been melting—both of which may be contributing factors to changing weather patterns. In 2020, there were $20 billion weather events that amounted to about $74 billion in damage. With these changes, resilient construction is increasingly important as builders seek extra durability to prevent damage and protect their builds.
A Portfolio Approach to Resiliency
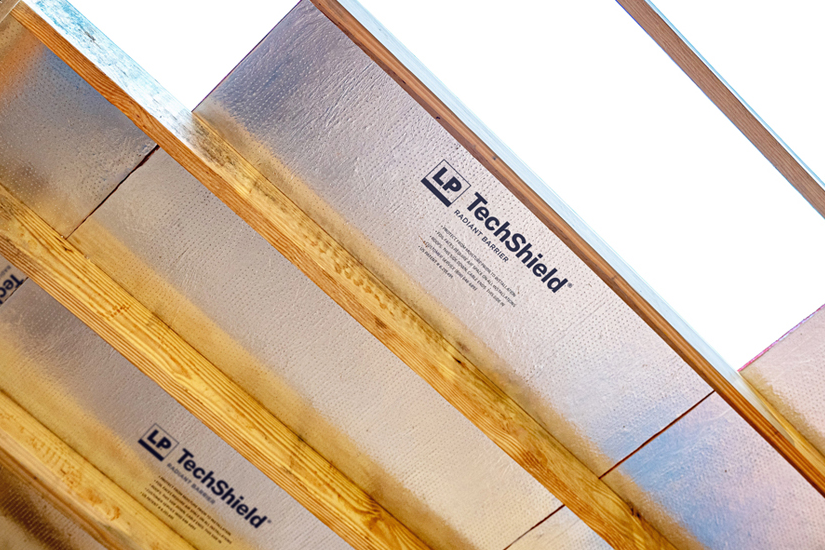
Photo courtesy of LP Structural Solutions
To support longer-lasting builds, many companies have tailored their products to act as a defense line against extreme climates. As a company, LP Building Solutions approaches weather-related challenges in a holistic way. From radiant barriers to air and water barriers, we offer a portfolio of solutions that can collectively go a long way in protecting homes in all climates, including high temperatures, extreme rain, and beyond.
In hot climates the most obvious aspect of the environment that builders have to combat is heat and, more specifically, the radiant energy to which structures are exposed in warmer climates throughout the country. The features of LP® TechShield® Radiant Barrier prevent the majority of radiant energy from entering into the attic space. The aluminum surface of LP TechShield panels has a very low emissivity, meaning that as the panel heats up only about 3%–5% of that energy is emitted or radiated off the surface into the interior attic space. Blocking this radiant heat can significantly reduce attic temperatures by up to 30° F.
Moisture intrusion is another major concern for builders and homeowners alike. While many builders resort to flexible timing and weather contingency clauses to successfully navigate wet weather construction, they are still often at the mercy of the materials they use. LP Building Solutions has been long committed to engineering building materials that specifically stand up to moisture-related challenges. For example, LP WeatherLogic® Air & Water Barrier works to help keep water and air out with an integrated, water-resistive overlay when sealed with seam and flashing tape. From sub-flooring, air and water barriers to siding materials, our products are engineered to ensure that your projects stay protected during and after construction.
Rebuilding After Natural Disasters
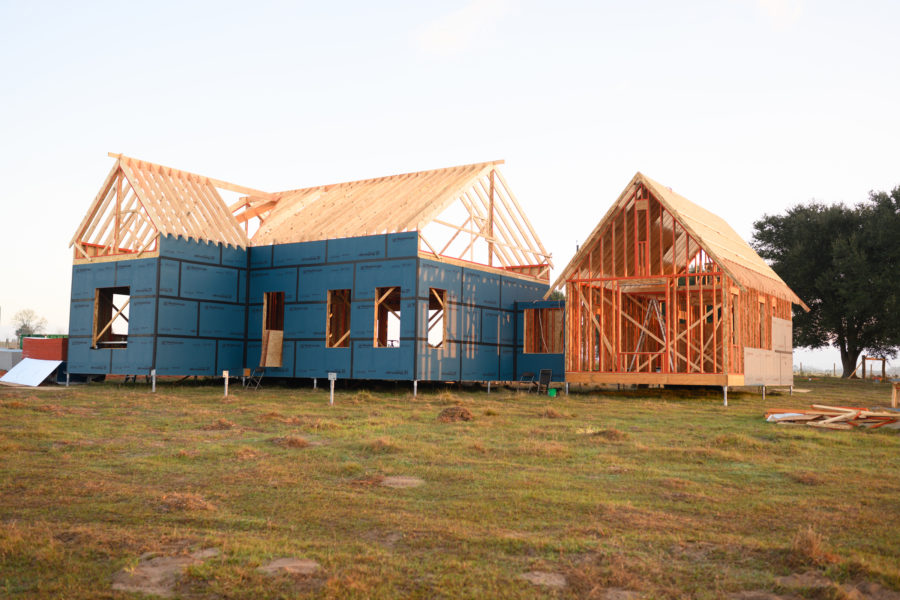
Photo courtesy of LP Structural Solutions
Part of resilient construction is rebuilding previously damaged structures using new products and systems to prevent future damage due to natural disasters. Since 1980, billion-dollar weather disasters have more than doubled in frequency. With the increase in hurricanes, tornadoes, wildfires, and more, rebuilding after natural disasters has become top-of-mind for many building professionals, especially those in areas prone to natural disasters.
As the need for rebuilding and repairing property damage arises with every natural disaster, designing structures that can withstand future weather events is crucial. Rebuilding communities after natural disasters is often a long process, but it can be done well when building professionals approach it with the perspective of resilient rebuilding. This means not simply getting structures back up as soon as possible but making intentional choices to prevent further damage.
Using sustainable materials when rebuilding is a key way to contribute to the well-being of the area that has been damaged. And while resiliency and sustainability aren’t interchangeable terms, they do go hand-in-hand. As demand for resilient building materials rises, so does demand for sustainable construction, which is the practice of reducing or eliminating environmental impact.
When rebuilding, property damage pros can shift to a value-added, solutions-based mindset to build more resilient structures, leading to increased durability and long-term efficiency. Rebuilding after natural disasters can be a big task, and though it varies per build here are some important steps to take after an event:
- Get power.
- Remove moisture as soon as possible.
- Remove damaged gypsum/drywall and insulation to open walls.
- Reduce potential mold growth by clearing out flooring and furniture.
- Apply proper mold inhibitor in/on walls and surfaces.
- Dispose of all damaged materials properly.
Resilient Building’s Impact on the Industry
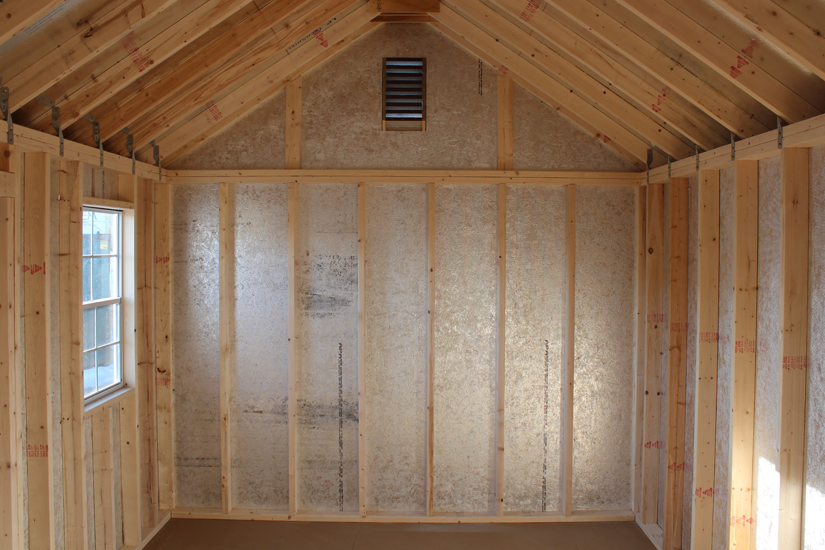
Photo courtesy of LP Structural Solutions
Resilient construction materials mitigate risk and can prevent long-term issues. Although durable products are a valuable resource for builders looking to construct high-performance, weather-resistant buildings, ultimately other factors will also come into play. Beyond products, builders should think critically about building methods to best support the products they are installing. Here are some things to keep in mind:
Wall Design
Sound isn’t typically top-of-mind the way that air sealing and moisture might be during a build, but considering how sound might travel from room to room can prevent consumer concerns from arising later on.
Home Ventilation
Increase fresh air accessibility and prevent a building envelope that doesn’t let air in properly.
Renovation
Resilient building isn’t only for new builds; consider updating older homes to improve efficiency.
As awareness of building quality increases in homeowners and natural disasters continue to be a concern, builders will have to adapt to the elevated expectations in the marketplace. This may mean increasing standards in the installation process itself. Accuracy will be more important than ever to assure the best possible performance.
National building codes set the standard for safe, affordable construction of all buildings and specify the minimum requirements for safeguarding people and property. However, national building codes do not currently address resilient construction. But as the country endures natural disasters and the aftereffects of wind and flooding, revisions to the building codes may influence resilient design and building. As the impacts of climate change accelerate, the need to rapidly assess and integrate the economic benefits of building resiliently, both in the public and private sectors, is imperative.
Knowing how to build and maintain a resilient structure is crucial in the current industry. Both protective materials and preventive techniques can help you achieve a longer-lasting durable build that meets consumer concerns and withstands harsh weather.