Story at a glance:
- Embodied carbon is the term for the carbon emissions of a material released during its extraction, transport, and manufacture plus the carbon emission associated with its disposal.
- Embodied carbon can represent up to 90% of all the carbon emissions associated with a building.
- Designers and builders have a large number of options to lower embodied carbon in their structures including low-carbon concrete and green steel.
The building sector, contributing almost 40% of global carbon emissions, has come under increasing scrutiny to reduce this percentage by reforming its traditional practices and using low-carbon materials.
Given that up to 90% of the carbon emissions associated with any particular building over the course of its lifetime will have already been released in the form of embodied carbon even before construction begins, one obvious strategy to lowering the sector’s total contribution of greenhouse gases is to focus on ways to slash embodied carbon.
Let’s examine more closely the multiple avenues open to designers and builders to reduce embodied carbon. But first, what exactly is embodied carbon?
What is Embodied Carbon?
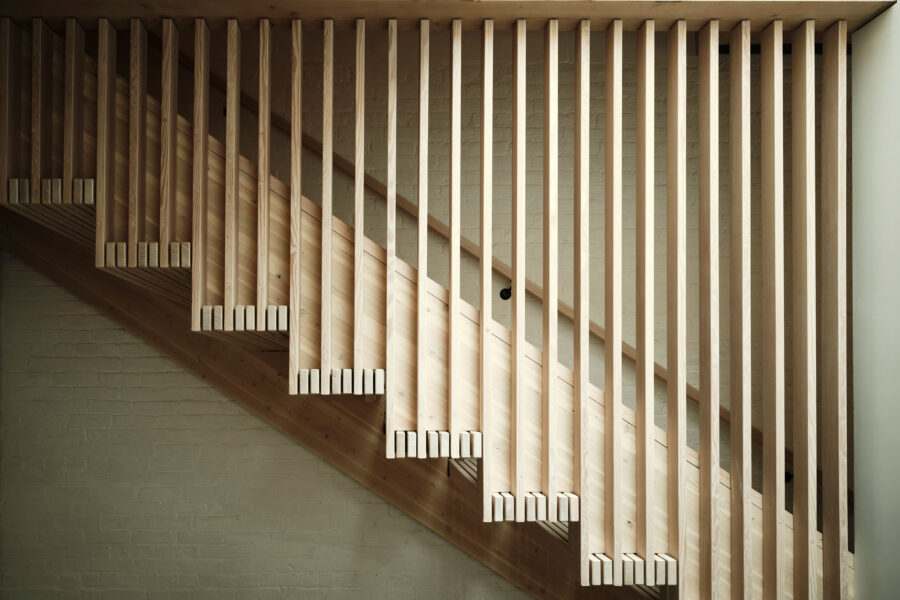
Glue-laminated Douglas fir forms the central stairwell that connects the three floors of Aaron Schiller’s Brooklyn Mass Timber House. Photo by Frank Frances
Embodied carbon is the term used to describe the carbon emissions associated with the extraction, manufacturing, transport, construction, and disposal of everything that goes into building a structure. Today concrete, steel, and insulation are the three highest carbon culprits in the building sector.
Another way of explaining embodied carbon is to set it against operational carbon emissions. We can say the embodied carbon inherent in building materials is all the carbon emitted during the life cycle of a structure other than the carbon released during the daily operations occurring inside the building. Examples of the latter include heating, cooling, and lighting.
Roughly half of all the carbon emissions associated with new buildings will be embodied carbon by 2050, according to a report by the United Nation Environment Programme.
How is Embodied Carbon Calculated?
Conducting a life cycle assessment (LCA) of each stage of a material’s fabrication is the only way to quantify the amount of carbon emissions embodied in a material.
Mathematically, embodied carbon is expressed as the global warming potential for that material during a specified time frame (usually 100 years). It’s written in carbon dioxide equivalent units. This means all greenhouse gases other than carbon dioxide—like methane or nitrous oxide—that are generated during the material’s production are included in the embodied carbon value for a specific material.
The findings of an LCA could be presented as Environmental Product Declarations (EPDs). These may be used as the metric for various environmental impacts of building products, including their embodied carbon emissions.
Tips for Reducing Embodied Carbon
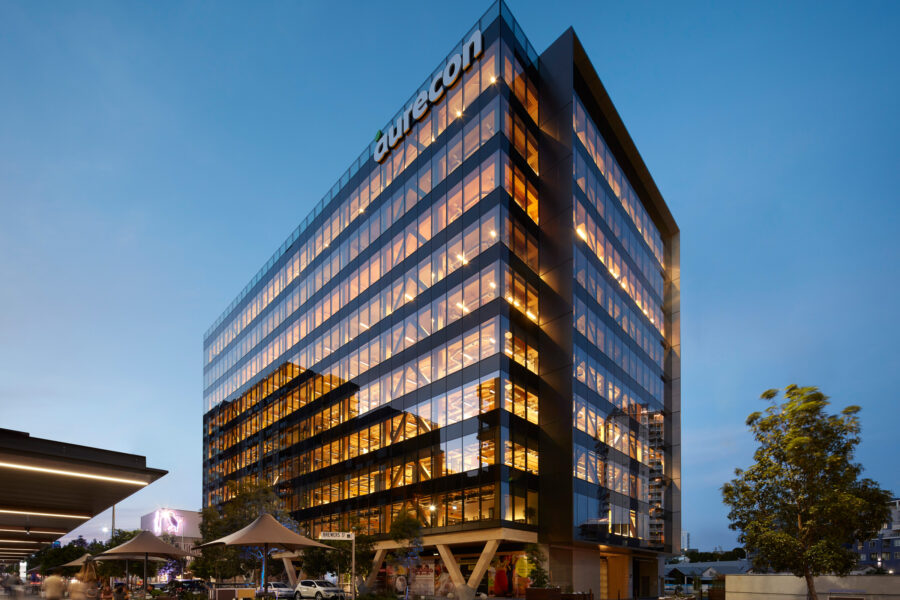
Designed by Bates Smart, the 25 King Office building makes heavy use of mass timber, both for its low embodied carbon and biophilic qualities. Photo by Tom Roe
Designers and builders can lead the way in reducing the environmental impacts of embodied carbon in four distinct areas of their work.
1. Design Efficiency
A mass timber building reduces embodied carbon by 26%, according to an article from Science Direct. Implementing passive house principles regarding a structure’s mechanical systems also cuts down on its embodied carbon.
2. Materials Selection
Choosing low-carbon alternatives can reduce embodied carbon in the final build by up to 74%. For instance, replacing cement with slag or fly ash can lower embodied carbon up to 33% with a possible cost reduction, according to research from the Rocky Mountain Institute (RMI). Choosing polyisocyanurate or mineral wool batt instead of extruded polystyrene foam as insulation can cut embodied carbon by 16%.
3. Renovation and Retrofits
RMI also reports that repurposing an existing building may result in a 75% savings in embodied carbon. And designing with easy fabrication and defabrication in mind for potential office fit-outs will not only save money; it will also lower embodied carbon.
4. Achieving Green Certifications
Designers and builders who wish to achieve LEED or similar certifications can do so more easily when embodied carbon is minimal. Given the likelihood of changes in future building codes to require embodied carbon reductions, implementing low-carbon materials and practices now will ease the transition to those reforms.
Low-Carbon Solutions for Buildings
In a recent report the real estate firm JLL predicts that there will be a 70% shortfall in low-carbon office buildings by 2030 as demand exceeds supply. It’s more urgent than ever to develop low-carbon solutions that reduce embodied carbon.
Here are a few ideas not already mentioned in this article. For more, see the International Living Future Institute guide.
Real Projects that Reduce Embodied Carbon
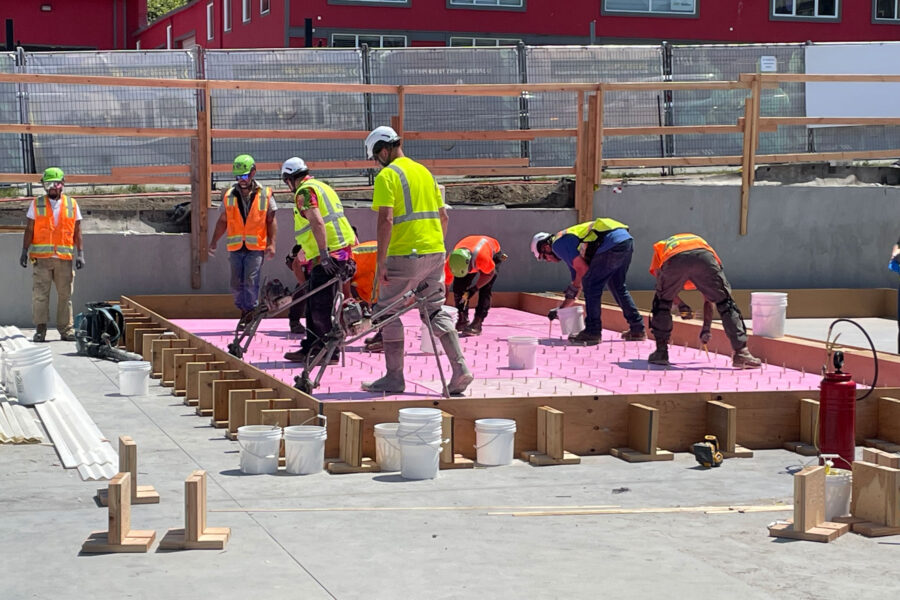
Foam is put down for sandwich panels during construction of the Seattle Storm facility. Photo courtesy of Sellen Construction
For inspiration in reducing embodied carbon in their new builds, designers and builders have the following real projects to emulate.
Seattle Storm Facility
Low-embodied carbon concrete specialists at CHRYSO & GCP helped design the Seattle Storm facility in Seattle, Washington using its industry game-changing technologies that contributed to its LEED Gold certification.
The project’s concrete producer, Stoneway Concrete used Lafarge slag cement, Ashgrove type IL cement, and chose CHRYSO & GCP’s admixture and fiber technologies to help exceed the specified embodied carbon limits and overall performance.
“Stoneway collaborated with CHRYSO & GCP to identify the best low carbon mixes for the intended application,” Lisa Barnard, sustainability and customer engagement program manager for CHRYSO & GCP, previously wrote for gb&d. “Overall the project exceeded a 40% reduction compared to typical average mixes in the region.”
Arizona State University Building
ASU’s Interdisciplinary Science and Technology 7 is another great example. To construct a building with 40% less embodied carbon, ready-mix producer Martin Marietta AZ, concrete contractor McCarthy Building Companies, and admixture supplier GCP came together to find the concrete mix that would meet the objective.
“Ready-mix concrete is sometimes viewed as a commodity, but the delivery of a product that has wide scale application—especially one with architectural aspects to it—requires a significant mind shift,” says McCarthy Building Companies Senior Project Manager Carlos Diaz. “It takes months to determine the right mix—making sure the suppliers and chemical partners are working together to find the best admixtures and supplementary cementitious material (SCM) for the application.”
“Everyone involved in the project came together to discuss different mix design scenarios and how to use locally available resources,” says Joel Lopez Martinez, Martin Marietta AZ quality control manager. “Using high fly ash mix design for the 6,000 PSI mix is beneficial as it reduces permeability to water and produces a densified product. GCP’s admixtures played a big part in the success of this mix design, as in help with water reduction by using WRDA 64 and increasing concrete workability by using ADVA 195.”
Better Buildings Low-Carbon Pilot
The US Department of Energy has piloted the Better Buildings initiative showcasing the efforts made around the country to lower embodied carbon. So far, there are 65 projects and counting to review for ideas and guidance.