Story at a glance:
- Environmental product declarations are documents based on life cycle assessments that quantify a product’s environmental impact throughout its life cycle.
- An environmental product declaration helps companies identify weak spots in their sustainability initiatives and makes it easier for customers to make more informed choices.
- Interface, Kingspan, Autex Acoustics, CHRYSO & GCP, and Excel Dryer are just a few of the companies prioritizing environmental product declarations.
When it comes to making informed material choices in green building projects, few documents are more useful than environmental product declarations, a type of environmental declaration that uses life cycle assessment data to provide insight into a product’s lifelong environmental impact.
In this article we’ll provide an introductory glimpse into the world of environmental product declarations—including their importance, how they work, and how to review them—and take a look at a few companies prioritizing environmental product declarations.
What is an Environmental Product Declaration?
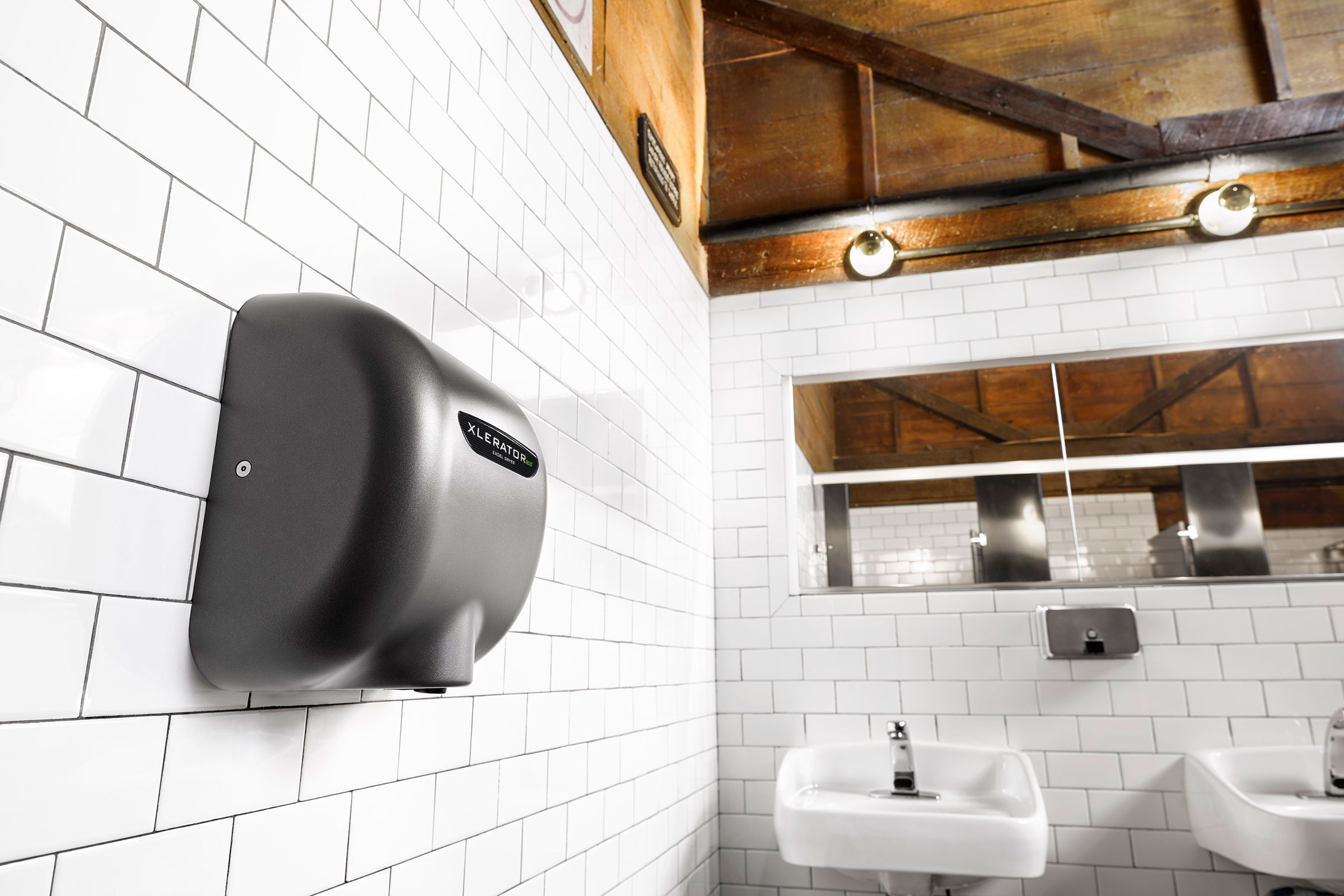
EPDs are Type III environmental declarations that provide accurate, science-based information regarding the impact of a product throughout its entire life cycle. Photo courtesy of Excel Dryer
An environmental product declaration, or EPD, is a voluntary Type III environmental declaration that serves to objectively quantify the environmental impact of a product throughout its life cycle, from cradle to grave.
“EPDs are designed to meet the global market demand for science-based, transparent, quality-assured information about product environmental performance,” Anna Mullens, vice president of marketing for the ICC Evaluation Service (ICC-ES), previously wrote for gb&dPRO. “An EPD is a third-party verified summary of the primary environmental impacts—including greenhouse gas emissions—from a product’s extraction, transportation, and manufacturing.”
Common impact categories included in an EPD include global warming potential (GWP), eutrophication potential, acidification potential, ozone depletion potential, smog formation potential, et cetera.
“EPDs are like a nutrition label for building materials,” Stacy Smedley, senior director of sustainability at Skanska USA, previously told gb&d. “Think about being on a low carb diet, going to the grocery store, and shopping for cereal. You’re going to pick up those boxes and read the nutrition labels to check the amount of carbohydrates per serving size. It’s exactly what we’re doing with carbon and building materials through EPDs.”
EPDs cannot be generated on their own but are instead derived from data gathered as part of a product’s life cycle assessment (LCA) following the ISO 14040 series of standards. The full LCA report itself, however, is not included in the published document, nor are any sensitive commercial details. To ensure fair, accurate, and unbiased reporting, EPDs must be verified by an unaffiliated third-party before publishing.
Why are Environmental Product Declarations Important?
EPDs are an important tool for a number of reasons, particularly for consumers, as the transparency they provide allows designers and specifiers to make more informed purchasing decisions. Because EPDs are third-party verified, the information they contain is considered to be extremely trustworthy, complete, and accurate, removing any possibility of greenwashing or skewed reporting.
But EPDs are more than just informative decision-making documents—they also help make whole-building sustainability calculations more accurate and provide product manufacturers with a better understanding of the strengths and weaknesses of their sustainability initiatives.
“It’s critical that we look beyond simply compiling documentation and start using EPDs as a tool to allow us to reduce our carbon footprint in the building industry,” John Dalton, fire protection technical services manager for GCP, previously told gb&dPRO.
EPDs can also help projects earn points toward certification with various green building rating systems when it comes to material transparency. The LEED Gold certified MSU Romney Hall, for example, made use of 42 products with EPDs, earning it “an exemplary performance status for the sourcing of products and materials from manufacturers who have verified improved environmental life cycle impacts of their products,” Jim Beal, principal owner of Cushing Terrell—the design firm behind Romney Hall’s renovation—wrote in a previous gb&d article.
The EPD Process
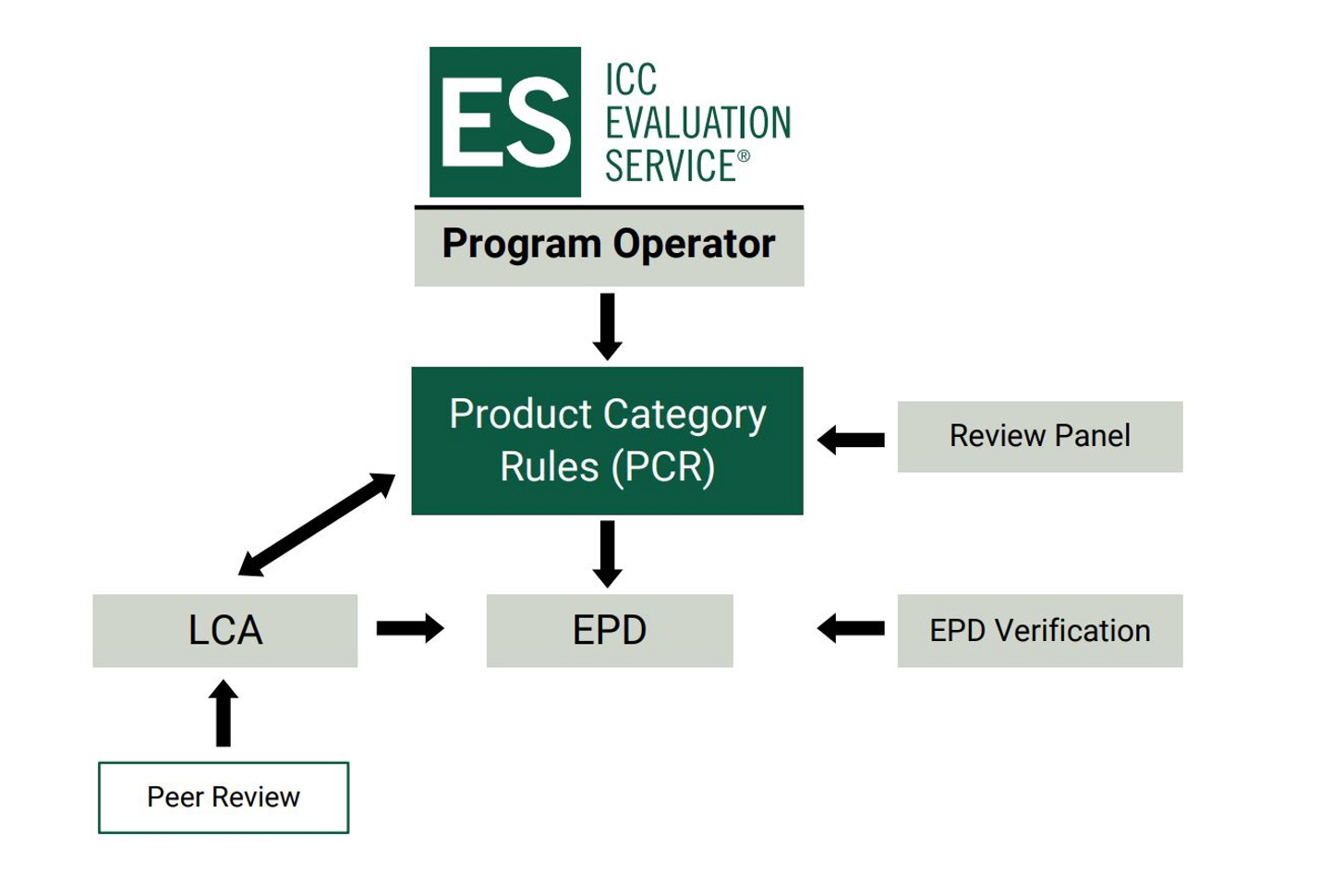
The EPD process results in a transparent declaration of a product’s environmental effects. Chart courtesy of ICC-ES
To create an EPD, a company must do the following as per the International EPD System’s (IES) guidelines:
Define
The first step in creating an EPD is to define the product using the appropriate Product Category Rules (PCR). PCRs are specific guidelines and requirements that describe how a product’s LCA must be conducted and the manner in which the results must be disclosed. The overarching purpose of a PCR is to facilitate ease of comparison between products within the same category.
If a suitable PCR does not exist for the product category in question, a new one must be developed based on the process outlined under the IES’ PCR Development protocol.
Develop
Once a product has been appropriately defined, an LCA must be developed. This can be done in-house by the organization or with the assistance of a consultant specializing in LCAs and environmental product declarations. As previously stated, the LCA study must be conducted in compliance with those methodologies, principles, and practices established by ISO 14040, as well as ISO 14044.
Compose
After the LCA study has been conducted, the results and any other required information as mandated by the General Program Instructions (GPI) and PCR will need to be compiled and an EPD report composed. The IES has specific requirements regarding the EPD report formatting and the necessary information it must include, though there is some room for flexibility on a case by case basis.
Verify
The International EPD System recognizes two forms of verification procedures—individual and verification via EPD process certification—both of which result in a third-party verified EDP.
- Individual verification. An approved individual verifier or an accredited certification body must conduct a verification of all LCA-based data and any additional information (as required by a valid reference PCR or GPI).
- Verification via EPD process certification. Describes the verification of an internal organizational process designed to develop EPDs based on the GPI and reference PCRs; EPD process certification may only be carried out by an accredited certification body.
Regardless of which procedure is used, the verifier or accredited certification body in question must possess knowledge and experience related to the product type, industry, and relevant standards of the product whose EPD is being developed. The IES curates a list of approved independent verifiers and accredited certification bodies on their website.
Register & Publish
Once verified, the EPD is ready to be registered and published. To do this the organization developing the EPD must register the EPD in the EPD Portal along with the following documentation:
- EPD in PDF format (if not in English, an English executive summary must be included in the main content)
- English verification report as provided by an individual verifier and/or a certificate of EPD Process Certification
- Product description (in English)
- A picture of the product or service being declared
- List of any products included in the EPD (if relevant)
- Company logo (only required for first-time EPD registration)
How to Review EPDs
When reviewing and comparing EPDs it’s important to know what to look for and how to interpret the information they contain. As a general rule an EPD will always include five types of information:
- General information
- Product information
- Information detailing the LCA methodology
- Results of the LCA
- Interpretation/analysis of the LCA results
Actually searching for and comparing EPDs can be a daunting task—that’s why international construction and development company Skanska co-created the Embodied Carbon in Construction Calculator (EC3), a free open-source tool that allows users to find and compare EPDs with ease.
Simply input the project address and material quantities and EC3 will search more than 100,000 EPDs, making it easier than ever to locate and compare low-carbon products. “When you’re procuring materials, it helps you make the best decisions around embodied carbon,” Heidi Creighton, former national head of sustainability for Skanska USA Commercial Development, now principal of Creighton Sustainability Advisors, previously told gb&d.
5 Companies Prioritizing Environmental Product Declarations
Now that we have a better understanding of what environmental product declarations are and how they work, let’s take a look at five companies prioritizing transparency and sustainability in their business practices.
1. Interface
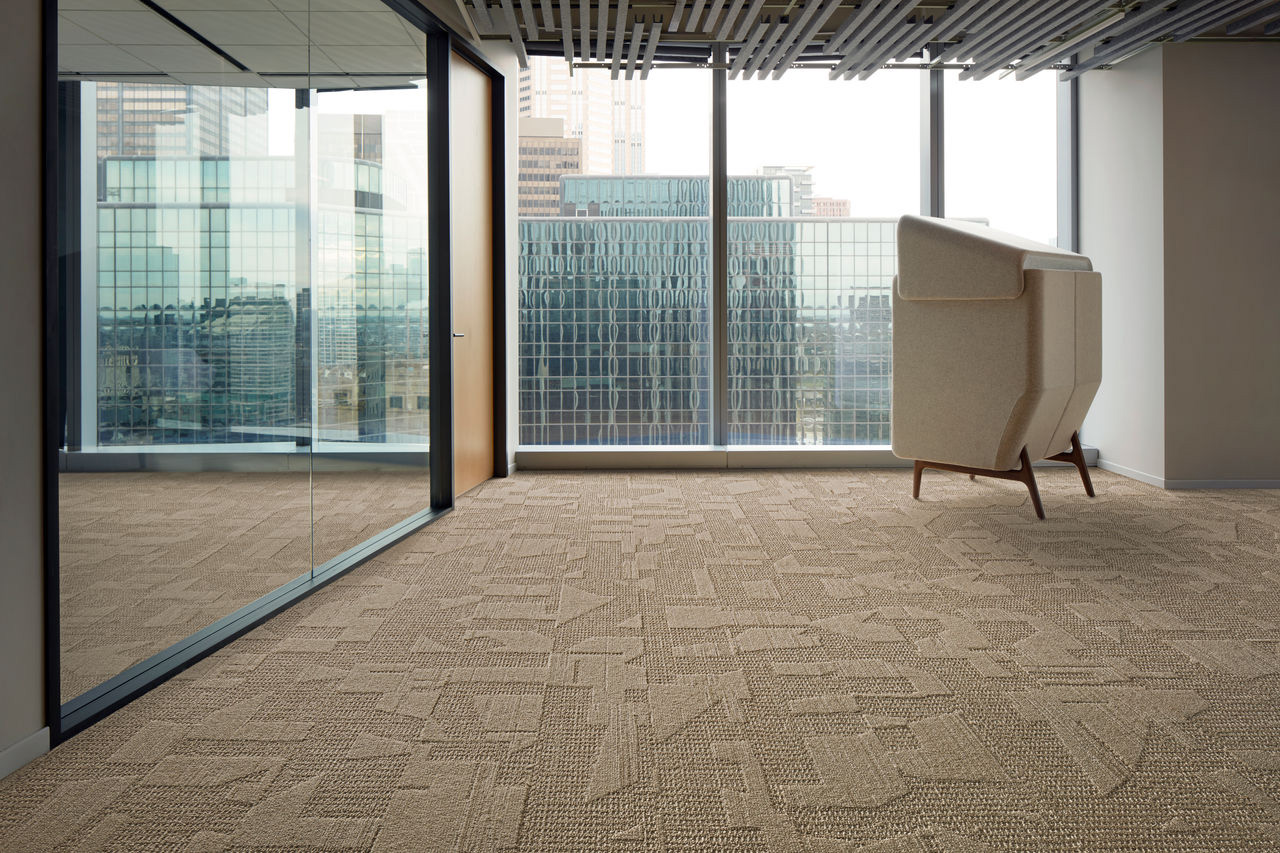
Interface’s new Etched & Threaded collection is made from recycled nylon fibers from Aquafil. Like almost all Interface products, the carpet tiles in the collection have a product-specific EDP. Photo courtesy of Interface
As the first North American flooring manufacturer to publish a third party verified EPD, Interface is no stranger to providing their customers with product transparency. “Interface is all in on solving the climate crisis. It’s not lip service,” Erin Jende, director of marketing at Interface, previously told gb&d. “We are asking, ‘How can we most quickly move the needle?’”
Interface has published EPDs for all standard products since 2012, with 99% of all products having a product-specific EDP as of 2024. Take Interface’s newest collection of modular carpet tile, Etched & Threaded, for example. Made from Aquafil’s ECONYL—a regenerated nylon fiber derived from recycled plastic waste—and Interface’s proprietary GlasBac backing (also made using recycled content), Etched & Threaded is incredibly low-impact in terms of manufacturing, installation, and maintenance.
Aside from using recycled materials in their products, Interface also encourages its clients to responsibly dispose of their flooring at the end of its operational lifespan; all of their modular carpet tile is designed to be easily repurposed or recycled through their ReEntry process, further reducing its lifelong environmental impact.
2. CHRYSO & GCP
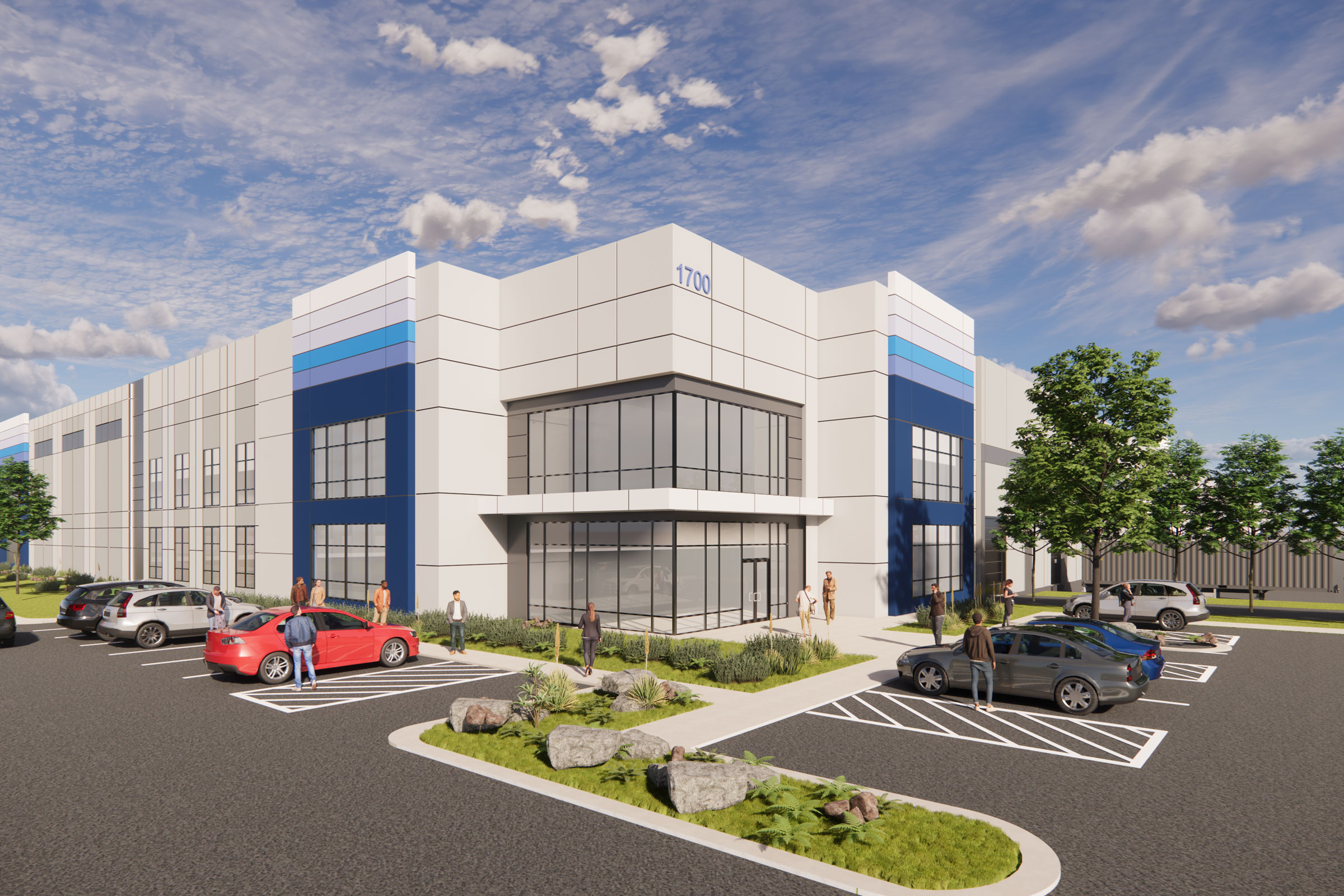
IDI Logistics chose GCP’s MONOKOTE fireproofing system for their new warehouse in part due to its EPDs. Photo courtesy of IDI Logistics
CHRYSO and GCP Applied Technologies—both business units under the Saint-Gobain family of companies—are two leading providers of construction chemicals and materials that have adopted EPDs into their business practices.
“We use LCAs and EPDs both internally and externally for product development and transparency,” Lisa Barnard, sustainability and customer engagement program manager for CHRYSO & GCP, told gb&d in a previous interview. “In the journey toward carbon neutrality it is important to provide accurate and robust data. To that end we work with third-party providers to assist our customers in the development of their own LCA and ultimately mix specific concrete EPDs using our admixture specific data.”
GCP’s MONOKOTE® line, for example, encompasses a range of gypsum based cementitious fireproofing products designed to meet commercial and industrial fire protection requirements. The entire line is covered by an ASTM-certified EPD that offers ample insight into the products’ environmental impacts.
And with more and more customers prioritizing sustainability in their purchasing decisions, this commitment to transparency pays off. “We like MONOKOTE as a fireproofing solution due to its EPDs,” Steve Golumbeck, IDI Logistics Chicago’s vice president of development, previously told gb&dPRO. “For us it was a win-win. MONOKOTE was the most economical, met all fireproofing criteria, and it had a better carbon footprint.”
3. Kingspan Group
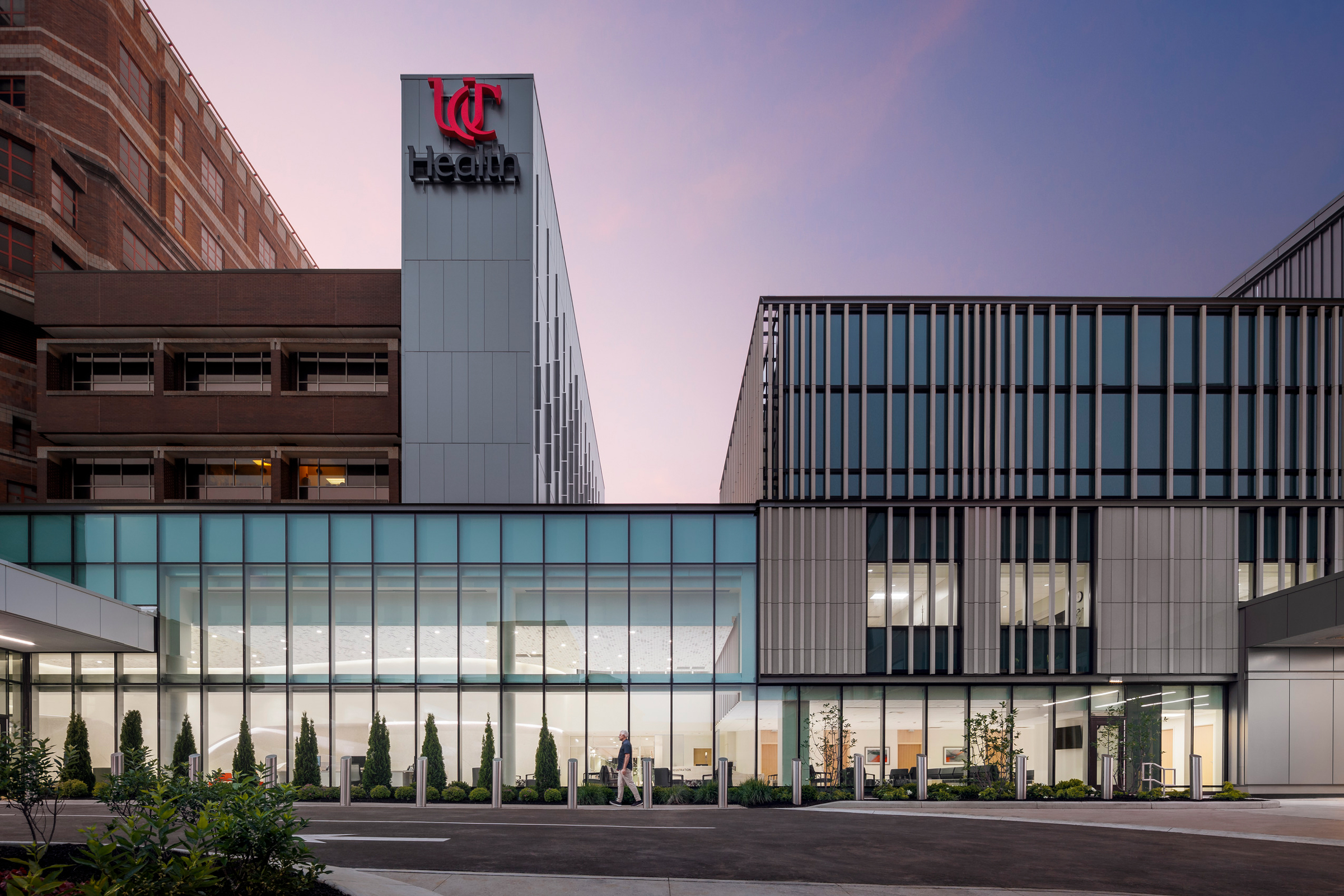
The EPDs for Kingspan’s QuadCore insulated metal panels are amongst the best in the industry and have a very low GWP. CannonDesign used QuadCore Optimo for this emergency room renovation in Cincinnati. Photo by Brad Feinknopf Photography
Few companies have demonstrated a stronger commitment toward sustainability than the Kingspan Group, a premier building materials manufacturer that specializes in daylighting solutions, insulation, and architectural facades. While Kingspan has not yet published EPDs for all of its products, the EPDs it does have are some of the most impressive in the industry. As of 2024 Kingspan has published six EPDs that were third party verified by SCS Global: four for their QuadCore line of insulated metal panels (IMPs), one for their laminated metal panels, and another for their polyisocyanurate (PIR) IMPs.
Kingspan’s QuadCore IMPs are produced offsite in a highly controlled environment using a large amount of recycled content. “The panels are manufactured with a target of zero waste heading to a landfill,” Brent Trenga, director of sustainability for Kingspan Insulated Panels North America, told gb&d in a previous article. This carries over to the panels’ end-of-life treatment as well, for both the foam insulation and steel are low carbon materials that may be recycled once they reach the end of their operational lifespans.
QuadCore IMPs have some of the lowest GWP figures in the industry, with the commonly used 3” IMP thickness—and specifically those produced at Kingspan’s Caledon plant in Ontario—having a GWP of only 2.59 KgCO2/ft2.
EPDs and greater transparency are just one component of Kingspan’s Planet Passionate sustainability program, a 10-year plan to decarbonize their entire operational footprint and transition the company’s manufacturing sites over to at least 60% direct renewable energy by 2030.
4. Autex Acoustics
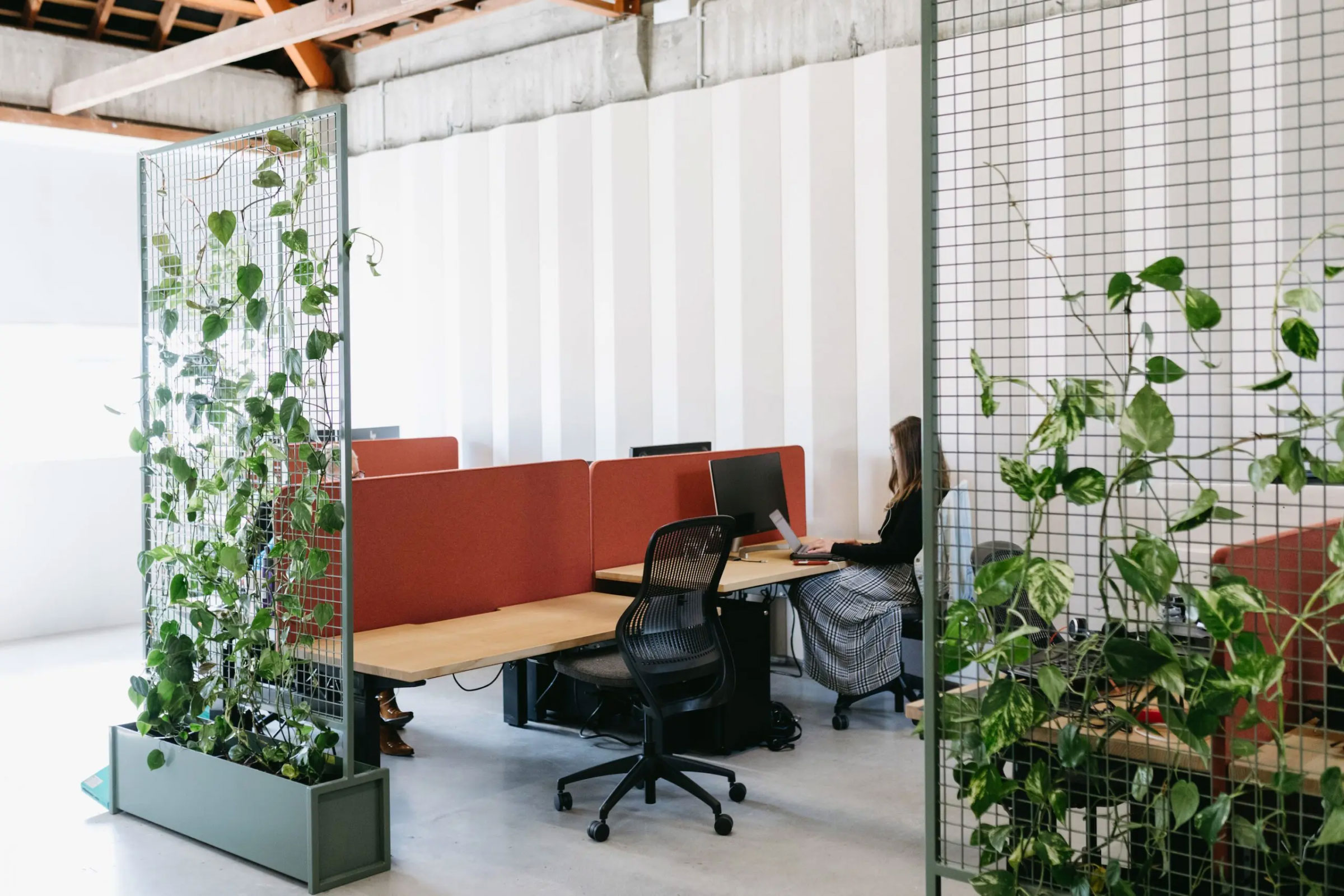
Autex’s contributions to well-designed, acoustically comfortable co-working spaces help even diverse spaces meet individual working needs. Vicinity Desk Screens and Lanes are seen here. Photo courtesy of Autex Acoustics
As one of the world’s leading manufacturers of sustainable acoustic solutions, Autex Acoustics knows just how important transparency is for maintaining a successful business. The company’s sustainability journey began in 1990 with the establishment of a zero-waste production line and has since evolved to encompass a range of environmentally-conscious methodologies—EPDs being one of them.
Autex first began publishing its EPDs in 2017—the same year they started measuring their greenhouse gas emissions—though they’ve been commissioning LCAs for more than 20 years. “This was before there was a huge push in the industry, much less the acoustics industry, to be looking at these figures and be mindful of the way we operate and how we make our own products,” Antonio Holguin, business development and sustainability lead for Autex Acoustics North America, told gb&d in a previous article.
Autex’s Vicinity series of acoustic desk screens, for example, possesses an EPD created and verified in accordance with ISO 15804. The screens are made from 100% polyester fiber and contain at least 50% post consumer recycled content (i.e. PET plastic bottles), while also being designed for disassembly, repurposing, or recycling at the end of their operational lifespan. Vicinity products are carbon neutral, low VOC, and possess no toxicity issues of concern.
Autex has further demonstrated its commitment toward transparency by generating HPDs for all of their products and ensuring that their full product lineup bears LBC Red List–Free Declare labels.
5. Excel Dryer
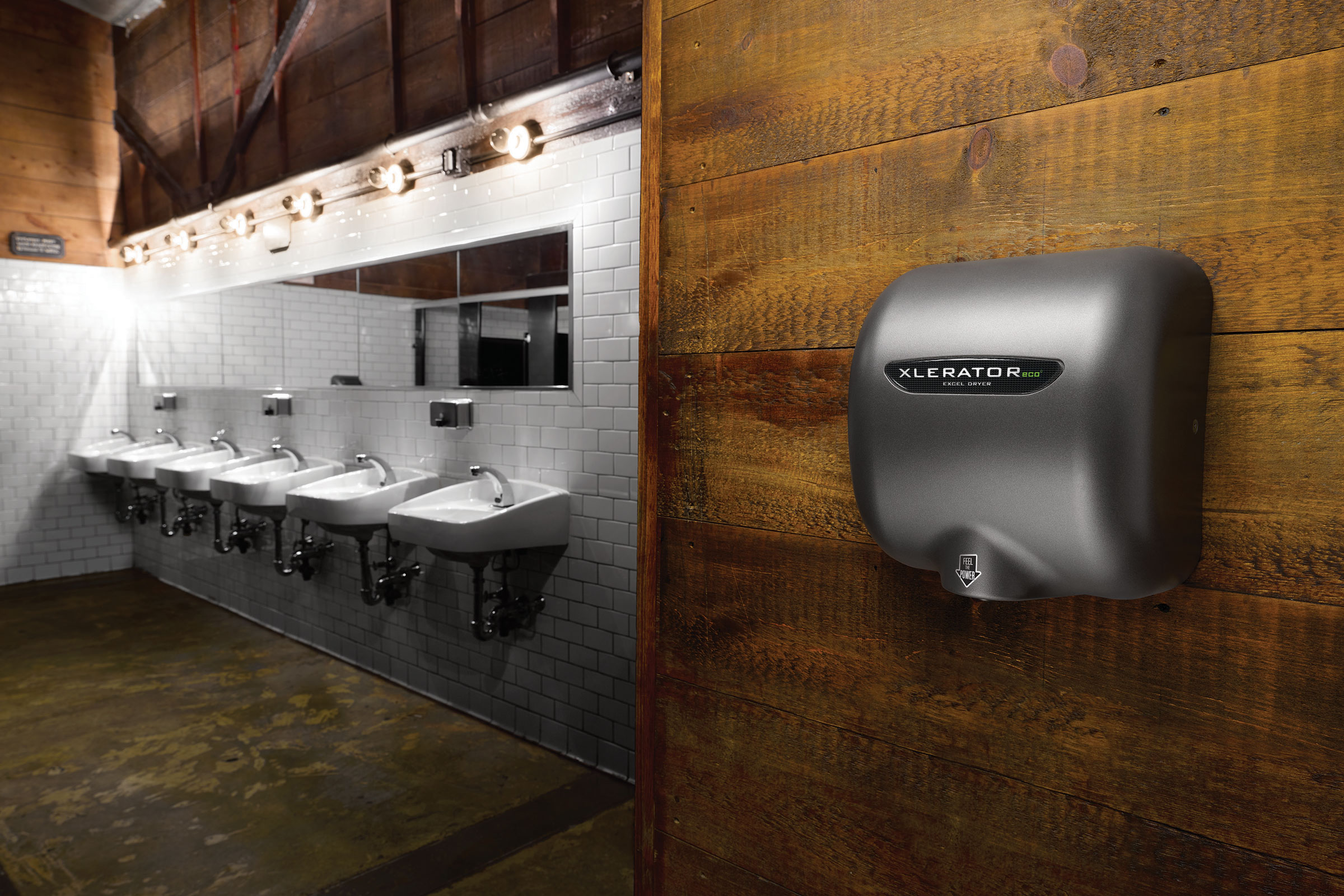
Excel Dryer has published EPDs for their entire product line of high-speed commercial hand dryers. Photo courtesy of Excel Dryer
Excel Dryer is a leading manufacturer of touchless high-speed commercial hand dryers and has long prioritized sustainability in all of their product’s designs. This is exemplified by Excel’s publishing of EPDs for their full product line of hand dryers, including the XLERATOR®/XLERATOReco®, XLERATORsync®, and ThinAir® hand dryers.
“We work hard to source the best materials from quality vendors that are as local as possible, so we are happy to share what goes into our products,” Denis Gagnon, president of Excel Dryer, previously told gb&d. “Our primary goal has always been to influence the entire industry to pursue greater transparency in matters of sustainability and health.”
During the LCA portion of the EPD process, Excel compared all four of their hand dryers to paper towels that had either a 0% or 100% of recycled content. The assessment found that each dryer’s GWP was 83% less than 0% recycled content paper towels and 81% less than 100% recycled content paper towels.