Story at a glance:
- Insulated concrete forms are a formwork system for reinforced, cast-in-place concrete walls consisting of a concrete core inside a permanent rigid foam form.
- There are three basic types of ICF systems: flat wall, waffle grid, and screen grid/post-and-beam systems.
- ICFs are considered a form of continuous insulation and greatly improve a structure’s overall energy efficiency.
Insulated concrete forms (ICFs) have been around in some form for almost 90 years. They’ve long served as strong, energy-efficient building materials. And with green construction techniques becoming more common, these innovative building blocks have seen something of a renaissance in recent decades.
In this article we break down the basics of ICFs and explore their benefits.
What is an Insulated Concrete Form (ICF)?
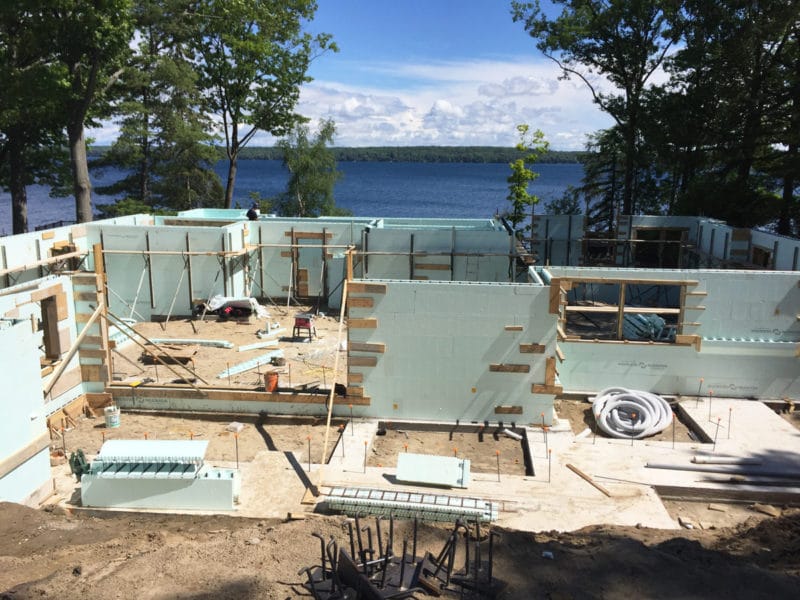
Photo courtesy of ICFMA
ICFs are a system of formwork for reinforced, cast-in-place concrete walls created by pumping concrete into hollow forms made from rigid foam insulation. Once the concrete sets the forms are left in place rather than removed, giving the wall improved insulating capabilities over traditional wood-framed walls while also providing backing for interior and exterior finish materials.
Expanded polystyrene foam (EPS) is the industry standard when it comes to ICF insulation, although extruded polystyrene options are also available. These foam panels generally range between 2 and 2¾ inches thick, though some brands offer ICFs with 4-inch panels on each side for improved thermal resistance properties. The hollow space between each set of panels is typically 6 to 8 inches wide.
Most ICFs are designed for straight wall assemblies and measure 16-by-48 inches, but certain manufacturers offer larger sizes. Tremco CPG’s DURAMAX Technology NUDURA standard forms, for example, are the ICF industry’s largest standard forms and measure 96-by-18 inches, reducing wall joints by 60% compared to other wall systems.
The tops and bottoms of ICFs are molded so they interlock with the ICFs above and below them, with some brands offering forms with reversible interlocks to help reduce waste. Many manufacturers also produce specialty ICFs—like curves, corners, end caps, lintels, and brick ledges—as well, improving their overall versatility.
Where are ICFs Used?
ICFs are used primarily for foundations and exterior wall assemblies, although they may also be used to construct floors, interior walls, roofs, and even pools. Advancements in ICF technology have greatly improved their overall versatility in recent years, expanding their design potential and allowing builders to create extremely energy-efficient structures that are also aesthetically pleasing.
Today ICFs can be found in both residential and commercial projects—including office buildings and schools—as well as military structures and disaster-proof safe rooms.
Types of Insulated Concrete Forms
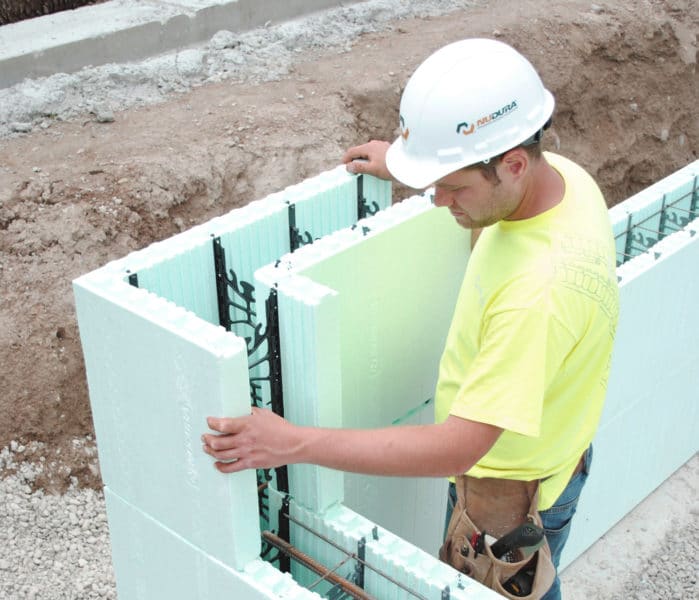
Flat wall ICFs—like these NUDURA ICFs from Tremco CPG Inc.—are the most popular type of ICF system. Photo courtesy of NUDURA
Generally speaking you’ll find three basic types of ICF systems: flat wall, waffle grid, and post and beam.
Flat Wall Systems
As the most popular type of ICF, flat wall systems create flat, monolithic reinforced concrete walls that are similar in appearance to traditional concrete walls constructed using removable forms. Because their concrete cores are of a uniform thickness, flat wall ICFs require the most concrete of any ICF system. This ultimately makes them heavier than other ICFs but imbues them with greater compressive strength overall.
The two insulation panels in flat wall systems are held together by cross ties or webs made from either polypropylene plastic or steel, with the former being the most common. These cross ties double as furring strips for attaching finishes to the interior or exterior face of the ICF.
Some ICF manufacturers utilize hinged or knockdown ties in their flat wall systems, which lets the forms fold flat for shipping—a quality that many builders love. “This allows them to fit twice as many forms in their trucks, saving time, money, and the hassle of repeat transport trips compared to other ICFs currently on the market,” Natalie Rodgers, marketing committee chair of the Insulating Concrete Forms Manufacturers Association (ICFMA) and manager of strategic learning programs at Tremco CPG, previously told gb&d.
Waffle Grid Systems
Waffle grid ICFs are characterized as having thick, closely spaced reinforced columns and beams with thin sections of concrete webbing between them. The alternating thicknesses of waffle grid ICFs mean they require less concrete and possess a greater thermal resistance rating than flat wall systems thanks to the thicker layer of EPS foam within the grid area.
These qualities do, however, come at the expense of design flexibility, with waffle grid ICFs having certain limitations when it comes to wall heights. Waffle grid systems are also only available as preformed blocks, meaning they take up more space than flat wall systems during transport.
Post & Beam Systems
Post-and-beam or screen grid ICFs are incredibly similar to waffle grid systems, with the main difference being that the spaces between the posts and beams are filled by EPS foam rather than concrete. This improves the ICF’s overall R-value but prevents the assembly from achieving any meaningful fire resistance rating.
Like waffle grid systems, post-and-beam forms also possess design limitations, restricting both wall height and number of stories. Screen grid systems are also only available as preformed blocks.
Benefits of Insulated Concrete Forms
Insulated concrete forms have become incredibly popular in recent decades. These are just a few of the benefits ICFs offer.
Energy Efficiency
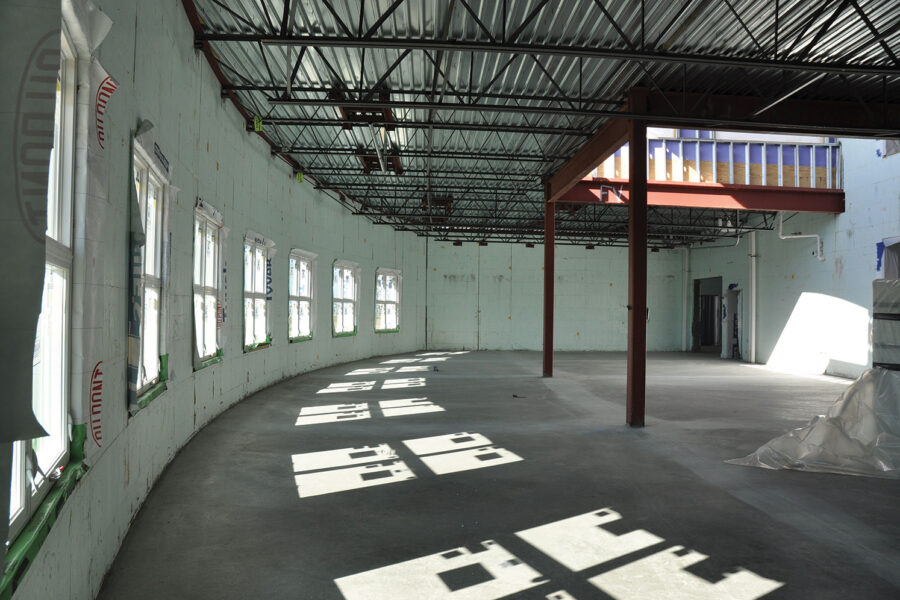
Richardsville Elementary School, built with Nudura ICFs, was the first net zero school in the US. Photo courtesy of Tremco CPG
As one might expect of a product with “insulated” in its name, ICFs are energy-efficient building materials that, when properly installed, help prevent air leaks and unwanted thermal energy transfer. ICF walls may be considered a form of continuous insulation and are functionally devoid of thermal bridges; the average ICF has an R-value of 22, although higher R-values are available depending on foam thickness.
To help illustrate just how efficient ICFs are, let’s take a look at the results of a study conducted by the ICFMA that compared a two-by-six traditionally insulated wood-framed cavity wall with a standard six-inch core ICF wall. “The wall was cooled to negative 35 degrees on one side and room temperature maintained on the other to see when the wall would reach a steady state,” Brian Corder, CEO of BuildBlock ICFs and vice chair of the ICFMA, previously wrote for gb&d. “How long would it take before they had to add energy to maintain a 70-degree room temperature?”
At the end of the study researchers found that the wood-framed wall reached steady state in approximately 60 hours, while the ICF wall took 300 hours to reach steady state. “When you have a solid mass wall that never changes temperature because it’s airtight and insulated from temperature changes, you’re significantly reducing the strain on your HVAC system,” writes Corder.
The incredible energy efficiency delivered by ICFs has made them an extremely popular choice for projects targeting net-zero—or even net-positive—status/certification. “It’s much easier to build a net zero job or system with ICF,” Cameron Ware, western division key account executive for Tremco CPG’s NUDURA ICF brand, previously told gb&d.
“You start with the envelope to reduce air infiltration. Air infiltration is a huge piece of net zero, and ICF virtually eliminates it completely. Whereas in regular construction, there’s an awful lot of caulking required to make wood or steel have zero air infiltration.” Aside from reducing energy waste, ICFs’ airtightness also helps improve indoor air quality, making for healthier interior environments.
Faster Construction & Lower Labor Costs
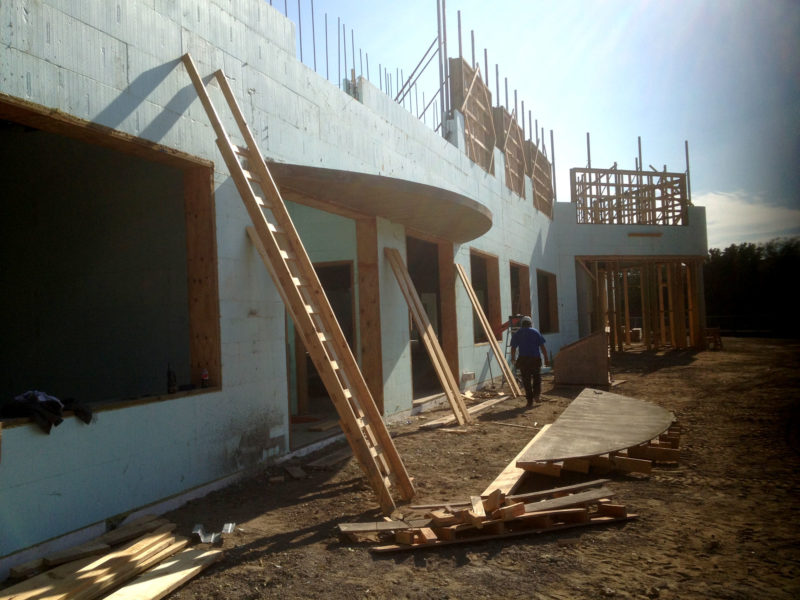
Building with ICFs can help reduce construction times and lower labor costs. Photo courtesy of NUDURA
Another benefit of ICFs—and particularly fully-assembled units—is that they help reduce onsite construction times compared to stone, brick, concrete masonry units (CMUs), and even traditional poured-in-place concrete. “Masonry work is very, very hard work. It’s easier and faster production-wise to put up ICF because the product only weighs about one pound per square foot, compared to 30 to 40 pounds per rock or CMU,” Ware says.
ICFs also enable faster construction, as they allow builders to complete multiple envelope layers at the same time. This is because ICF systems simultaneously function as a building’s structural framework, insulation, air barrier, vapor barrier, and anchorage for exterior/interior finishes. The rigid foam insulation layer is also convenient for installing electrical conduit, as channels may easily be cut, routed, or melted out of the foam face. All in all, estimates suggest that ICFs can shave off anywhere from two weeks to four months from a project’s total construction time.
ICFs can also help to reduce labor costs compared to other masonry materials, as their installation doesn’t necessitate a full team of experienced contractors. “ICFs are frequently built by DIY customers, and as long as one person is versed in ICFs, they can work with unskilled laborers and you can move from stacking walls one day to pouring the basement as quickly as the next day,” Corder wrote in a separate gb&d article.
Building with ICFs also helps circumvent potentially expensive weather-related delays, as ICF systems can be installed in almost any weather condition without issue, as they do not absorb moisture like stick-built structures.
Durability & Resiliency
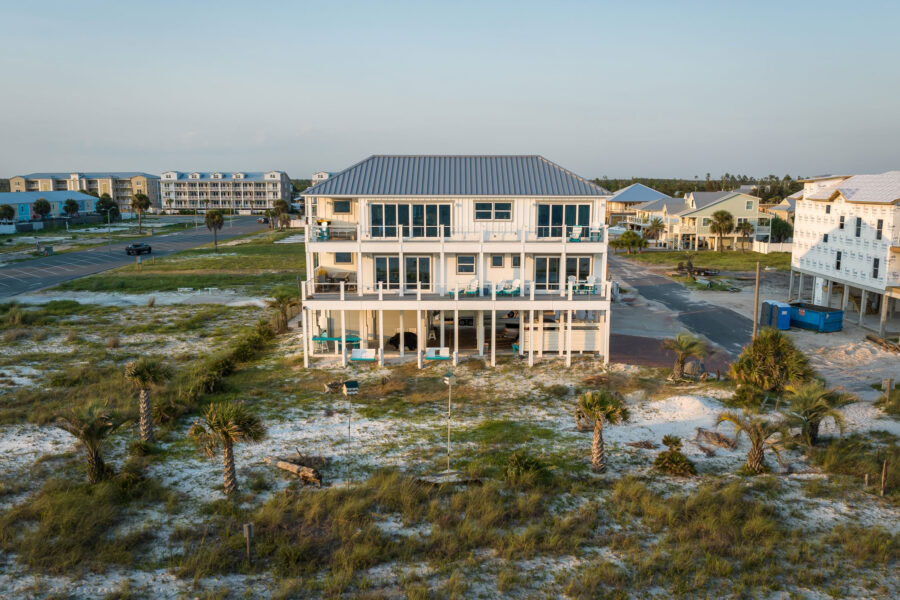
This home is one of the few houses left standing after Hurricane Michael. It was built using ICFs. Photo courtesy of Tremco CPG
Because they do not contain any organic matter, ICFs are inherently mold, mildew, and pest resistant, negating the need for potentially toxic resilience-boosting additives or coatings. Neither do ICFs require additional fireproofing, as concrete is a naturally non-combustible material, with most ICF wall assemblies boasting a three to four hour fire rating—significantly higher than that of traditional wood-framed walls.
The combination of concrete and steel in ICF systems imbues them with stiffness, strength, and ductility—the three most important qualities when it comes to withstanding earthquakes and other seismic disturbances. When paired with their high fire rating, these characteristics make ICFs an extremely smart choice for projects in wildfire- and earthquake-prone regions like the Pacific Northwest.
ICFs are also incredibly resistant to lateral wind loads, making them an ideal choice for projects in areas where tropical storms and hurricanes are common. “At a minimum, an ICF wall can withstand 150 mile per hour winds,” writes Corder. “The steel reinforced concrete inside that wall provides structural stability, even from large debris. The foam on the outside delivers a large cushioning effect, too.” Most ICFs are designed to effectively weather 250 mile per hour winds, exceeding the 195 mile per hour standard of Miami-Dade certification.
This extreme durability means ICFs—like all concrete products—have an impressively long lifespan. “Concrete is concrete. It’ll be around for 100 to 200 years, whereas wood will be replaced after 35 to 50 years,” Ken Taft, an architect with Bobby Cox Companies who’s worked with NUDURA ICFs on multiple projects, previously told gb&d.
Acoustic Control
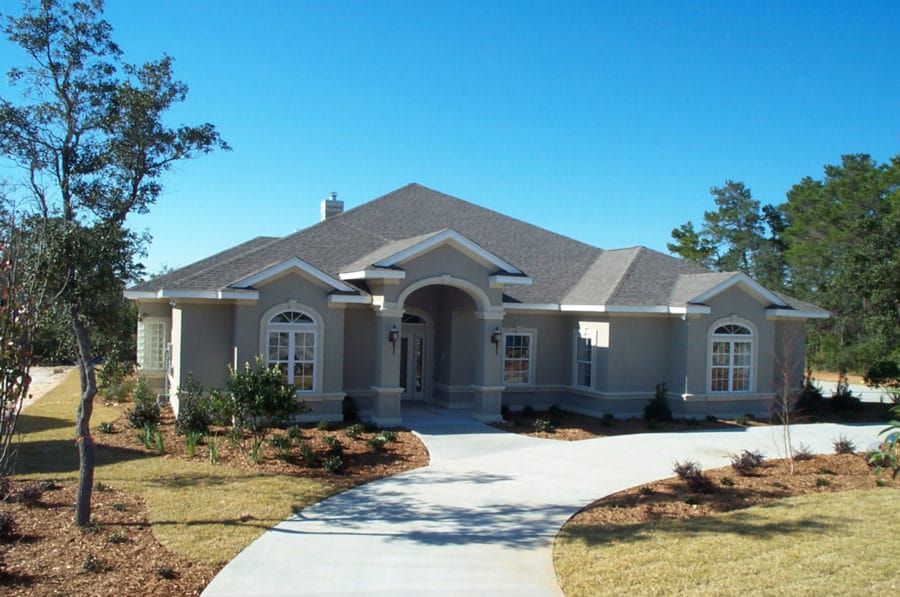
In addition to acting as a thermal insulator, ICFs also help reduce noise transmission between walls. Photo courtesy of ICFMA
An often overlooked benefit of ICFs is their high sound transmission class (STC) rating and overall positive impact on a building’s acoustics compared to traditional wood framing. “Your typical house is in the 40s or so, or even a little lower, which means you’re going to hear the guy across the street mowing his yard. You’re going to hear kids playing outside,” Ware says. “An ICF house has an STC of over 50, which means you can’t hear through it very well.” This sound dampening benefit results in a much quieter interior, free from outside distractions.
ICFs’ sound-dampening abilities are due to their being able to both block and absorb sound waves. Dense, high-mass materials like concrete are extremely effective sound barriers, while foam insulation actively absorbs sound energy, helping to prevent unwanted sound transmission between walls.