Story at a glance:
- Prefab homes are built using pieces manufactured offsite before being assembled and transported to the actual build site.
- There are four types of prefab homes: mobile/manufactured, modular and panelized, pod, and kit.
Prefab homes in the United States date all the way back to the late 1800s, though the prefab homes of 2024 look much different. The demand for prefabricated homes has skyrocketed in recent decades, with more and more options, styles, and features being offered.
The term “prefab” is often used as a catch-all for a variety of unique pre-manufactured home types. This article aims to demystify the world of prefab and provide examples as to some of the most sustainable options.
What are Prefab Homes?
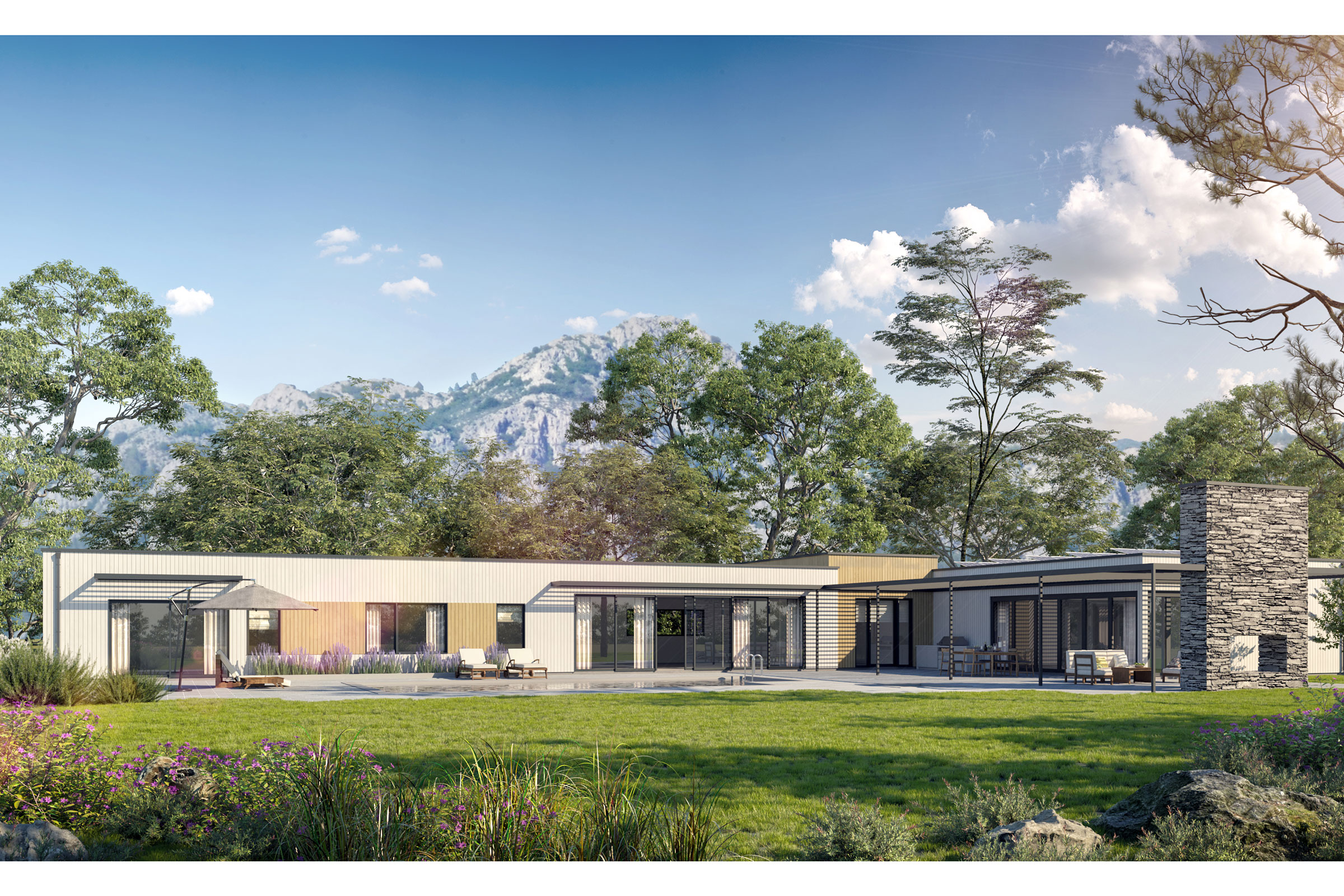
This prefabricated passive house is the brainchild of Plant Prefab and Richard Pedranti Architect. Rendering courtesy of Plant Prefab
A prefab or prefabricated home is a type of house whose pieces are all (or mostly) manufactured in an offsite factory in advance before they are assembled on the building site. This is in contrast to the traditional “stick-built” home, or those homes constructed onsite from the ground up.
Types of Prefab Homes
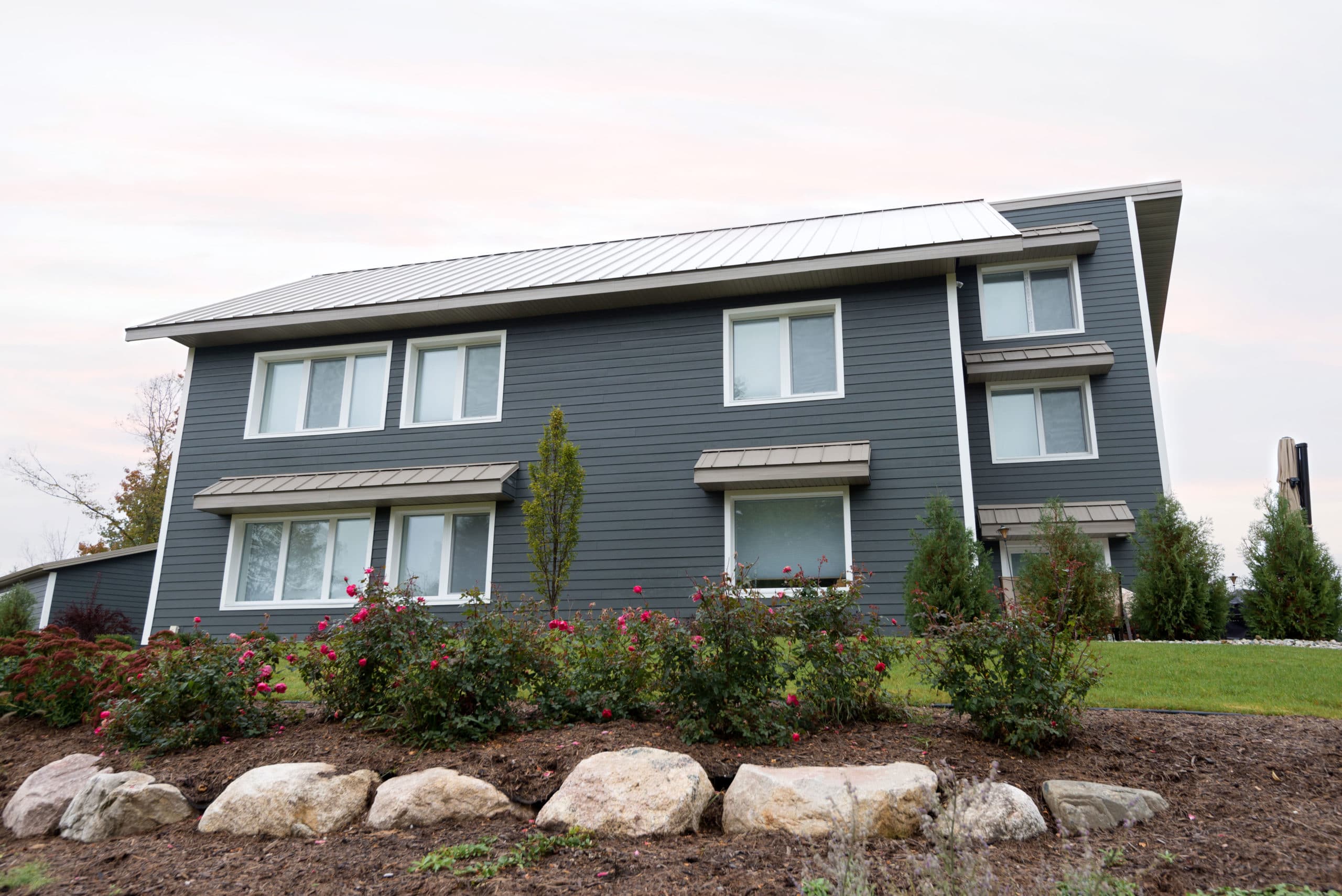
Photo courtesy of Phoenix Haus
There are four commonly recognized types of prefab homes—mobile/manufactured, modular/panelized, pods, and kits. All share certain similarities but vary somewhat in terms of their actual design and the construction methods they employ.
Mobile & Manufactured Homes
There is no inherent difference between mobile and manufactured homes other than when they were built. According to HUD, a factory-built home constructed prior to June 15th, 1976 is a mobile home, whereas all factory-built homes constructed after June 15th, 1976 are considered manufactured homes.
Federal law regulates the definition of this category of prefab home and describes them as such: “Manufactured homes are built as dwelling units of at least 320 square feet in size with a permanent chassis to assure the initial and continued transportability of the home.” Manufactured prefab homes are built in accordance with HUD building codes, feature wheels, and may be hitched to, and subsequently transported by, another vehicle.
Because they have wheels and are built on a chassis, manufactured homes are technically considered vehicles and thus fall under the DMV’s jurisdiction. These homes are licensed by the DMV and as such must also be built to the DMV code.
Manufactured homes can, however, be converted to “real property,” after which point they become subject to conventional real estate law. This process is usually fairly straightforward but ultimately varies slightly from state-to-state.
Modular & Panelized Homes
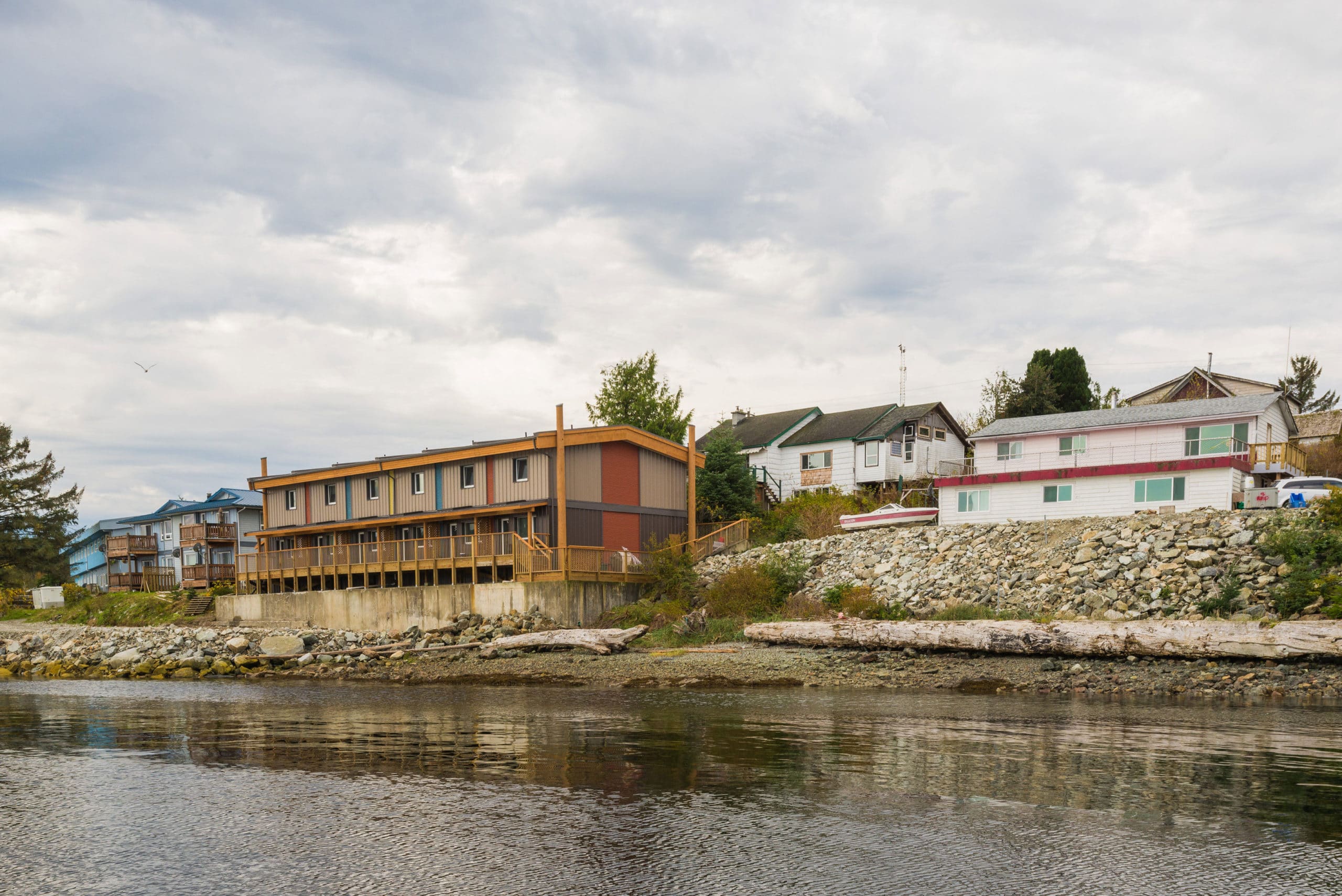
The Bella Bella Passive House on Campbell Island is constructed from multiple 32 x 14 foot prefabricated modules. Photo courtesy of Vancouver Coastal Health
Modular and panelized prefab homes, on the other hand, are not designed with mobility in mind and typically resemble the traditional “stick-built” home in both their size and features. Most modular homes are not fully assembled before delivery but instead arrive in two or more sections (i.e. “modules”) and then assembled on the build site.
Panelized prefab homes are similar to modular homes in that they are constructed offsite and transported in sections to the build site for final assembly. Rather than arrive as modules, however, panelized homes arrive as prefabricated wall panels, roof trusses, and I-joist or truss floor systems.
A prefab home may be built entirely from modules, panels, or a combination of the two. As long as the structure consists of at least 70% pre-manufactured elements, it qualifies as prefab.
Unlike manufactured homes, modular and panelized prefab homes are built in accordance with the International Residence Code (IRC) rather than HUD building codes. In most cases modular and panelized prefabs fall under the IRC’s Off-Site Construction category.
Pod Homes
A subset of tiny houses, prefab pod homes are somewhat of a combination between manufactured and modular homes. Like manufactured homes, pods are almost always built and assembled entirely offsite before being transported to the homeowner’s property. But unlike manufactured homes, prefab pods (usually) aren’t designed with wheels and thus necessitate the use of a crane to lower them onto a permanent foundation, similar to modular homes.
Because they are designed as a single unit, prefab pod homes are typically much more compact in design compared to any other subcategory of prefab homes. Like modular and panelized homes, prefab pod homes must comply with the IRC.
Kit Homes
While still technically considered prefabs, kit homes require considerably more on-site construction than any other type of prefab home. Instead of arriving entirely assembled or in a few pre-manufactured sections, kit homes arrive flat-packed with their components already cut but not put together.
Because they are ready-cut and require little-to-no further alteration, kit homes are still much easier to assemble than a conventional stick-built home and are much more user friendly, allowing homeowners to assemble the house themselves if desired.
Benefits of Prefab Homes
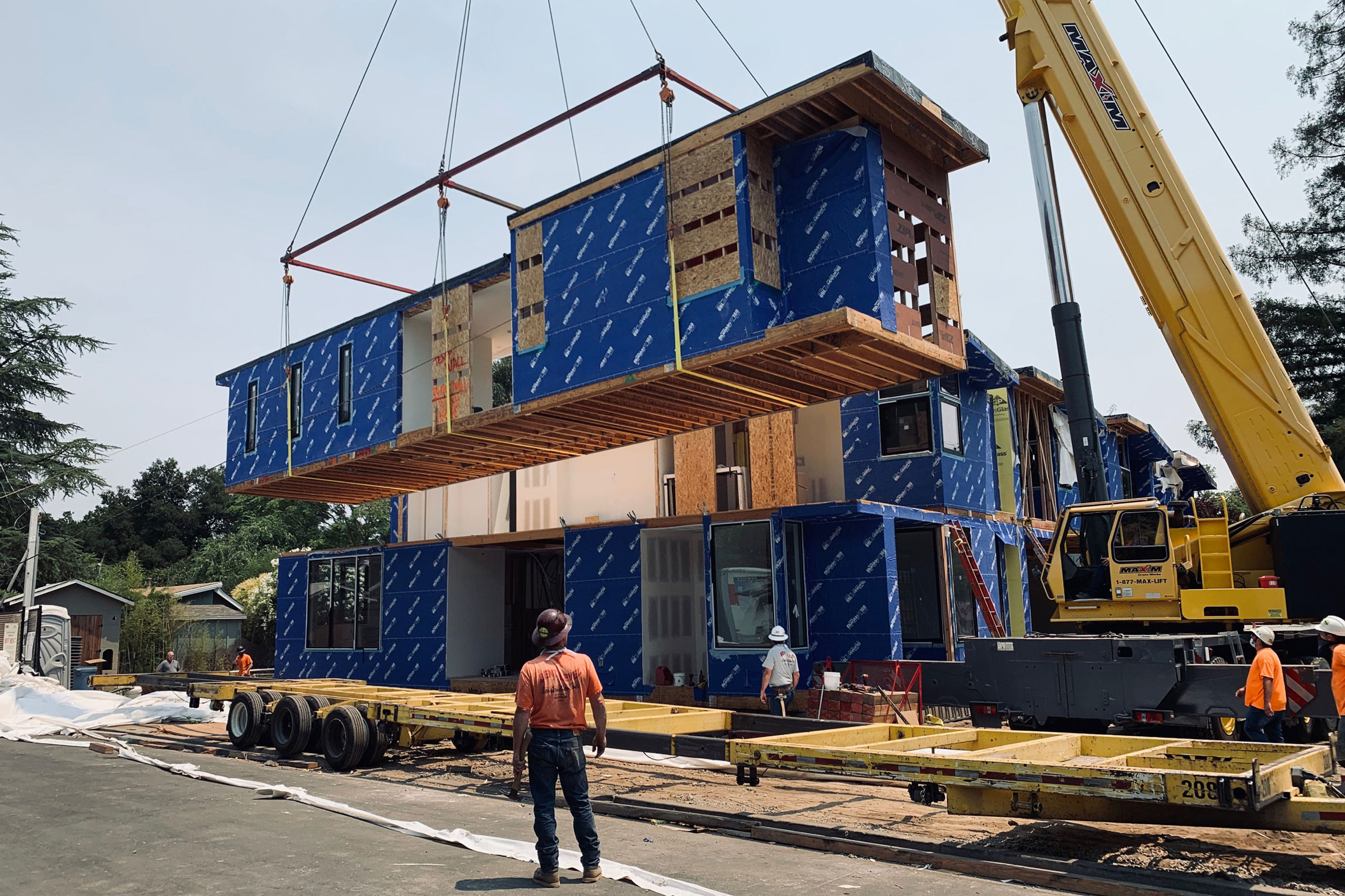
Three days is all it took for Plant Prefab to install custom-designed townhomes by Metro Architects. Photo courtesy of Plant Prefab
Prefab homes have seen a resurgence in popularity over the last few decades, in large part thanks to the range of benefits they offer.
Energy-Efficient & Low Waste
Because all of their pieces are designed and manufactured in a controlled environment to high quality standards, prefab homes tend to be extremely airtight and thus very energy-efficient constructs once assembled. There are also a growing number of prefab home manufacturers who are designing and building to LEED and Passive House standards—both of which prioritize energy efficiency and reduced carbon emissions.
The controlled environment in which prefab homes are designed and constructed also means that they produce far less waste than the average stick-built home. This is especially true of those prefab home manufacturers who use nesting software to cut and prepare building components, as these programs help lay out cutting patterns in a highly efficient manner that minimizes the amount of wasted material.
Shorter Build Times
One of the most significant benefits of prefab homes is that, because the majority of their components are assembled off site (and are therefore not affected by weather conditions), they have drastically reduced build times when compared to conventional stick-built homes. Most stick-built homes take months to construct in the field, but prefabricated homes can be built and assembled in a few weeks—and the most expertly crafted prefabs take just days to install.
Often Less Expensive
Because prefab homes waste very little material and require fewer workers to install, they tend to be less expensive overall when compared to their stick-built counterparts—in some cases as much as 20% less expensive. This ultimately depends on the design and style of the home itself, the manufacturer, and a few other factors.
Manufactured homes, for example, can be purchased for an average of $128,000—much lower than the national average for conventional stick-built homes. Modular and panelized prefab homes tend to be more costly, but still typically cost less per square foot than a standard home.
Disadvantages of Prefab Homes
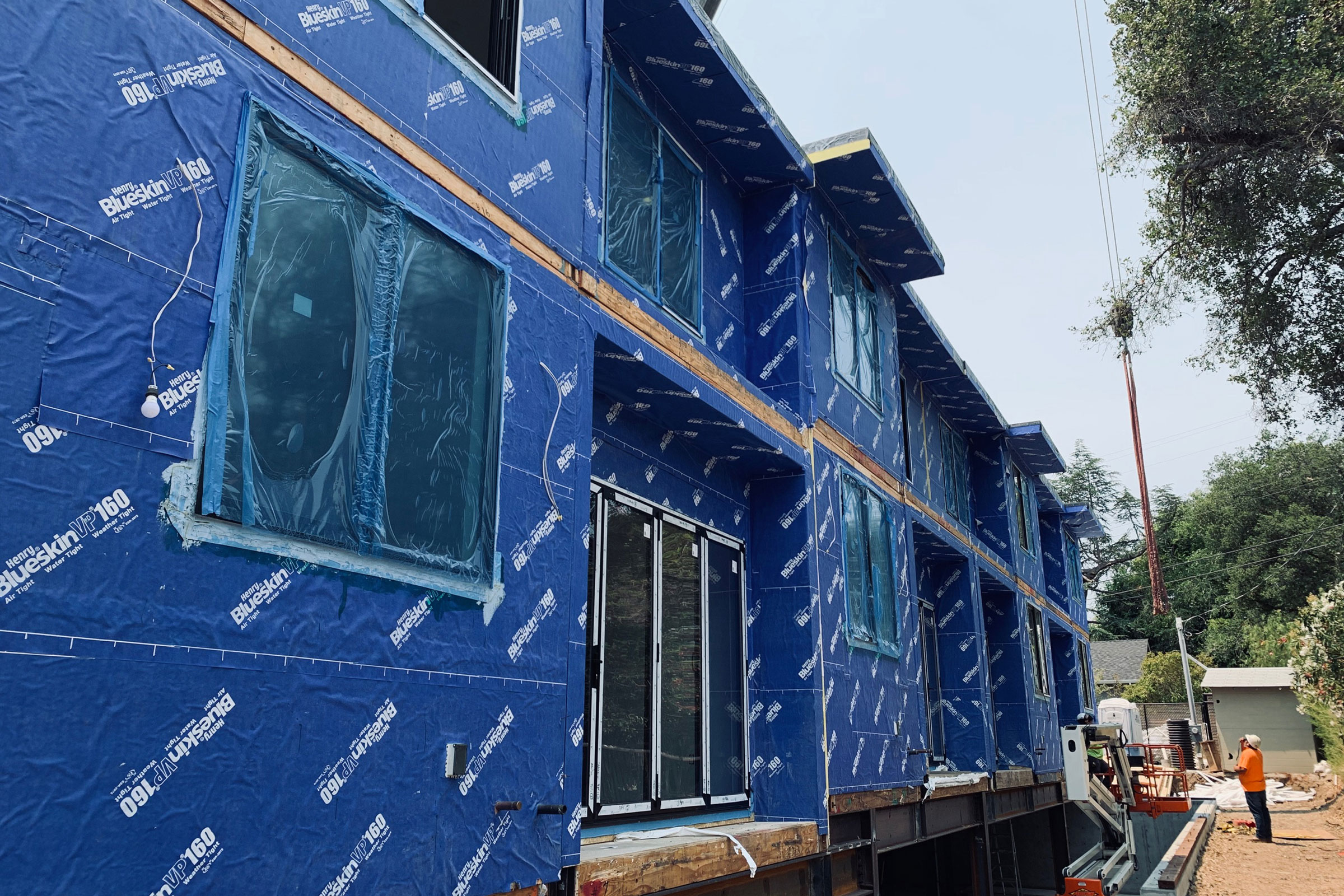
Despite their numerous benefits, prefab homes aren’t without their disadvantages, either. Most prefabs offer less design flexibility, for example, than their stick-built counterparts. Photo courtesy of Plant Prefab
Prefabricated homes have no shortage of benefits, but just like any home, they come with their fair share of disadvantages, too.
Necessitate Land Ownership
Because they are constructed offsite and transported to the build site for assembly and installation, prefab homes necessitate complete ownership of the land they sit on. If you don’t already own that land, you’ll need to purchase it before any other work can begin.
More Upfront Costs
While prefab houses tend to be more affordable in the long run than their stick-built counterparts, they often come with more upfront costs. If you buy an existing home, for example, you can generally expect to make a 20 to 25% down payment and pay off the rest as mortgage over time. Prefab homes, however, typically require you pay for the home’s construction in installments before you move in.
You’ll also need to pay for the land before building the home, as well any inspections, soil testing, and permits required by your zoning area’s applicable building codes and regulations.
Less Design Flexibility
Despite the increasing customizability of prefab homes in recent years, they still offer less design flexibility than constructing a custom-built home from the ground up, especially when it comes the materials used and overall architectural style of the home. Of course, this varies depending on the company you’re purchasing the prefab from.
8 Prefab Home Examples
Here are a few examples and the companies that offer them.
1. Plant Prefab

Plant Prefab installed a four-unit townhome development in Los Gatos, California in three days in July. The custom-designed residences by Metro Architects are a prime example of how Plant Prefab’s building system allows for faster construction that’s also more efficient than traditional methods. Rendering courtesy of Metro Architects
Based in Rialto, California, Plant Prefab is committed to providing sustainable, high-quality modular and panelized prefab homes. “We use the USGBC’s LEED for Homes program as well as our own stringent health and sustainability program, Z6, to create some of the world’s healthiest homes with the lowest possible impact on the planet,” Plant Prefab Founder and CEO Steve Glenn previously told gb&d.
Founded in 2016 Plant Prefab seeks to provide consumers with the best in prefab construction, with a major focus on achieving efficiency throughout all phases of preplanning, prefabrication, and installation. This is perhaps best exemplified by their installation of a four-unit, 11,054-square-foot modular townhouse development—custom-designed by Metro Architects—in Los Gatos, California over the span of just three days in 2020.
Because Plant Prefab’s building system takes place in a quality-controlled, offsite factory rather than onsite, the development project had a much lower impact on the existing neighborhood and allowed site and structure work to occur simultaneously. Plant’s rigorous sustainability program also helped minimize the negative environmental impact of the townhouses themselves.
Once prefabrication was complete Plant delivered each of the custom residences as four fully volumetric Plant Modules—complete with all fixtures, finishes, and appliances in place. This, combined with Plant’s use of smart utility connections, helped facilitate the 72-hour installation.
2. RPA LivingHomes
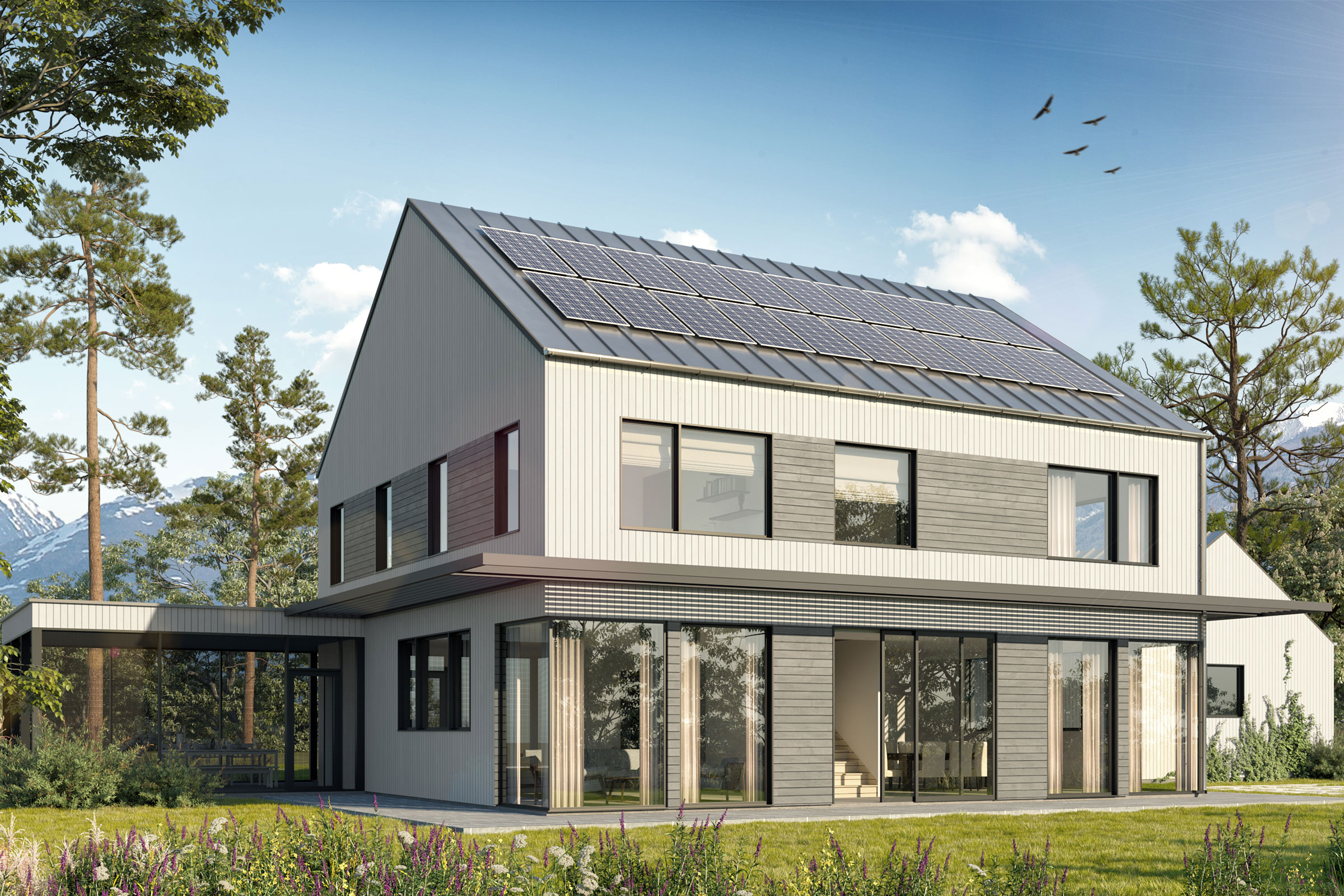
Prefabricated passive houses in three styles are the latest from Plant Prefab and Richard Pedranti Architect. Rendering courtesy of Plant Prefab
A collaboration between Richard Pedranti Architect (RPA) and Plant Prefab, RPA LivingHomes are an impressive union between Pedranti’s sustainable designs and Plant’s innovative Plant Building System, a hybrid prefab solution that utilizes a new kind of panel in combination with highly specialized modules.
“With the Plant Building System accommodating the design to prefab was not a significant challenge; we were able to translate Richard’s designs into a simple combination of Plant Panels and Plant Modules,” Glenn says. “Air distribution was collocated and restricted to the minimal number of modules and crossovers to allow for efficient and seamless installation.”
RPA LivingHomes 1 and 2 are characterized by their pitched roofs—optimized for PV panel installation—whereas RPA LivingHome 3 is distinctly Californian in design. Each home features an open floor plan and is designed to meet both Passive House and net-zero energy standards.
All RPA LivingHomes feature airtight construction, heat recovery ventilation systems, high-performance windows and doors, highly efficient mechanical systems, a dedicated fresh air system, and high value insulation. Plant Prefab’s Plant Building System allows each home to accommodate greater design flexibility, time savings, and transportation efficiency than any other prefabrication method.
3. Phoenix Haus
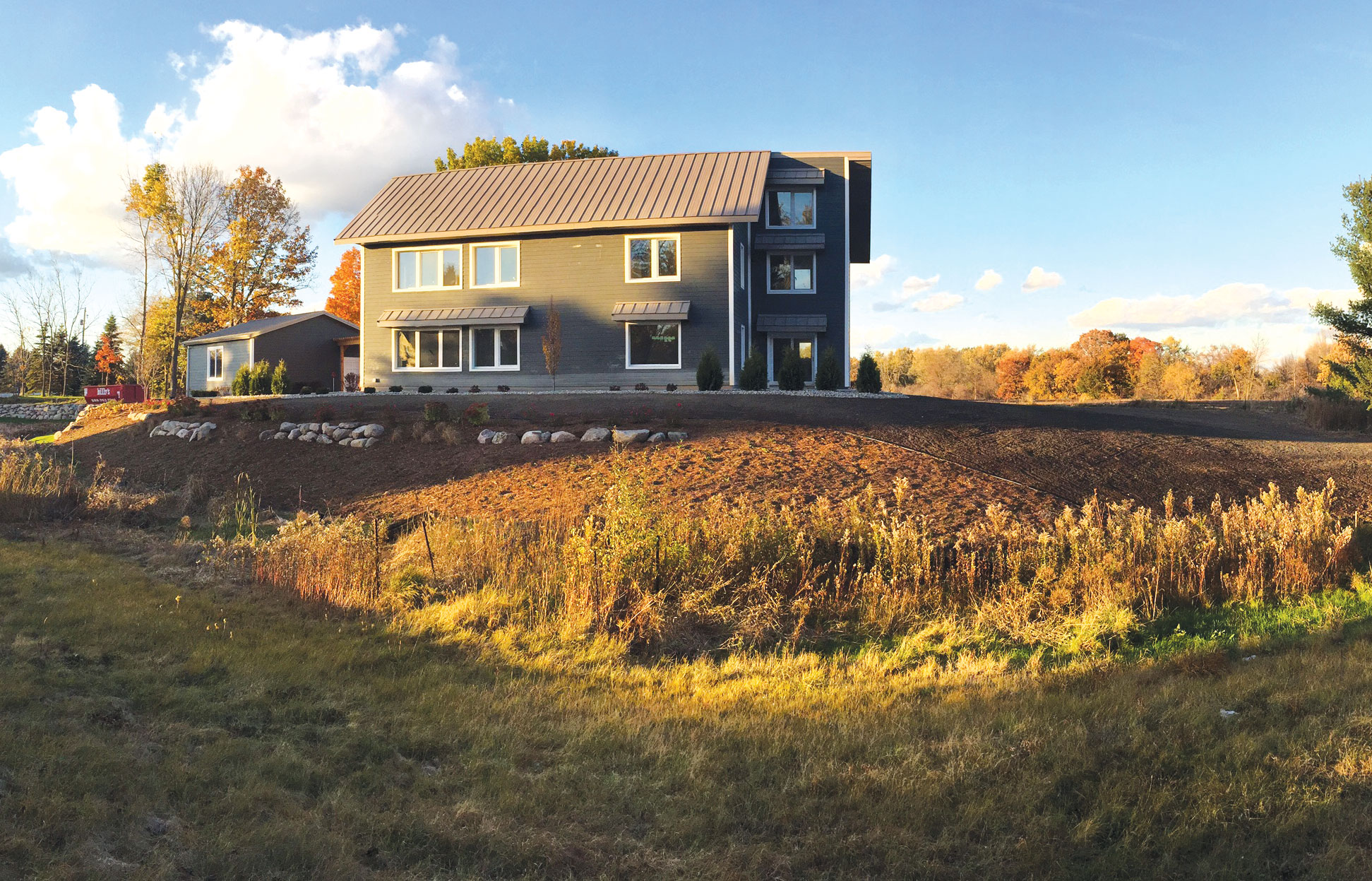
A typical Phoenix Haus prefab home is 1,200 to 3,000 square feet. Photo courtesy of Phoenix Haus
Founded in 2011 and based in Detroit, Phoenix Haus seeks to create innovative, environmentally conscious buildings and provides efficient, low-cost prefabricated homes built to the Passive House standard.
Working out of a renovated 1900s factory, Phoenix Haus’ large factory features an overhead crane, semi-automated equipment, and a loading bay designed for specialized vertical trailering. This allows the company to prefabricate both custom and pre-drawn template designs to meet the ever-growing consumer demand for passive homes.
By building to Passive House standards, homes prefabricated by Phoenix Haus tend to be more expensive than your average prefab—but the improved energy-efficiency they provide makes the investment worthwhile. “Currently, there is a 10 to 15 percent cost premium to building to the Passive House standard using prefab,” Kate McDonald, project manager at Phoenix Haus, previously told gb&d. “However, when a cost analysis is performed and this premium is amortized over the life of the structure, it turns out to be a marginal increase in the investment that starts paying you back the minute you start living in the structure.”
Phoenix Haus currently offers eight off-the-shelf yet customizable prefab home designs ranging from 1,200 to 3,000 square feet and spanning a range of architectural styles. Their H7 | 30 model also includes a 1,000-square-foot carport with a 1,000-square-foot roof-deck.
4. Square Root Architecture + Design

The second iteration of C3, Chicago’s first green prefab house, by Jeffrey Sommers of Square Root Architecture + Design. Photo courtesy of Square Root Architecture + Design
After designing C3, one of Chicago’s first sustainable modular prefab homes, Square Root Architecture + Design’s Jeffrey Sommers created C3 1.1, an improved version that drew upon the best parts of prefab and on-site construction.
Rather than relying strictly on prefabricated modules, C3 1.1 utilizes structural insulated panels (SIPS), a kind of flat-pack prefab system used to construct a highly insulated, thermally broken building envelope that provides improved protection against air and water infiltration.
This form of panelized prefab requires more onsite construction than, say, a modular prefab might, but it allowed Square Root to take full advantage of both offsite and onsite construction, greatly reducing the project’s overall expenses. “It allowed for lower shipping costs, lower craning costs, and the ability to work within the city’s requirements for on-site inspections,” Jeffrey Sommers of Square Root Architecture + Design previously told gb&d.
Once assembled C3 received both Indoor AirPlus and EnergyStar certifications and was third-party tested for a Home Energy Rating System (HERS) score of 43.
5. Ecocor
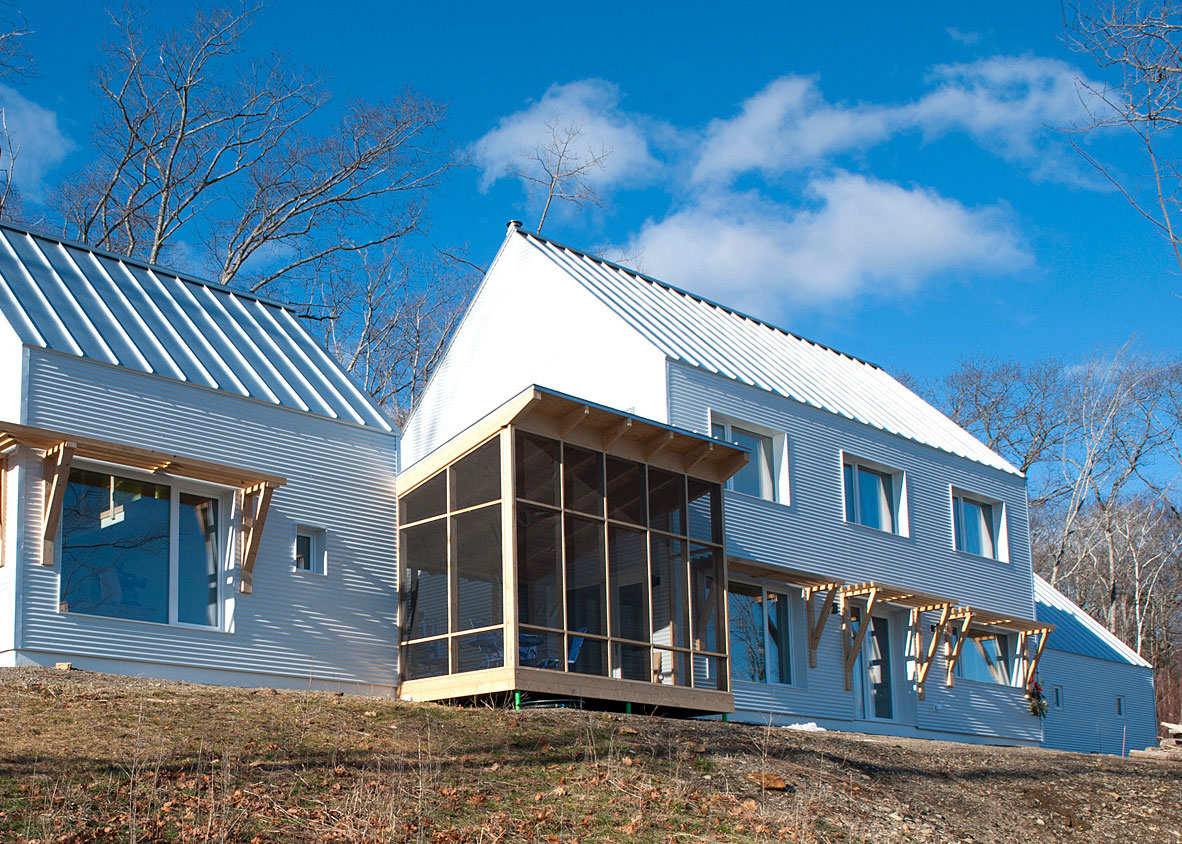
Ecocor has sustainability in mind as they build their projects by focusing on using 80-90% less waste. Photo courtesy of Ecocor
Since the company’s founding in 2010 Ecocor has been committed to designing, manufacturing, and assembling high-performance Passive House-certified buildings, cutting construction waste, drastically reducing energy consumption, and shortening time-to-occupation. It wasn’t until 2013, however, that Ecocor’s owner and technical director, Christian Corson, began experimenting with prefabrication.
Since then Ecocor has gone on to partner with Richard Pedranti to create SOLSKEN, a line of highly-sustainable, energy-efficient prefab homes built to Passive House standards and that utilize locally-manufactured materials, FSC-certified lumber, as well as zero-VOC insulations and chemical sealers—all of which Corson believes should be common practice in the industry.
“It makes no sense to ask our clients to raise their families and children in a home built out of toxic materials,” Corson told gb&d in a previous article. “At the same time, not using these materials means the people working for us, on the floor of the factory day-to-day, they stay healthy, too.”
Ecocor’s facility uses the latest technology to prefabricate panelized walls, floors, and other building components in a highly-controlled, low-waste environment—and what little waste the factory does produce is almost always reused in other projects.
6. Outward Bound Dorms
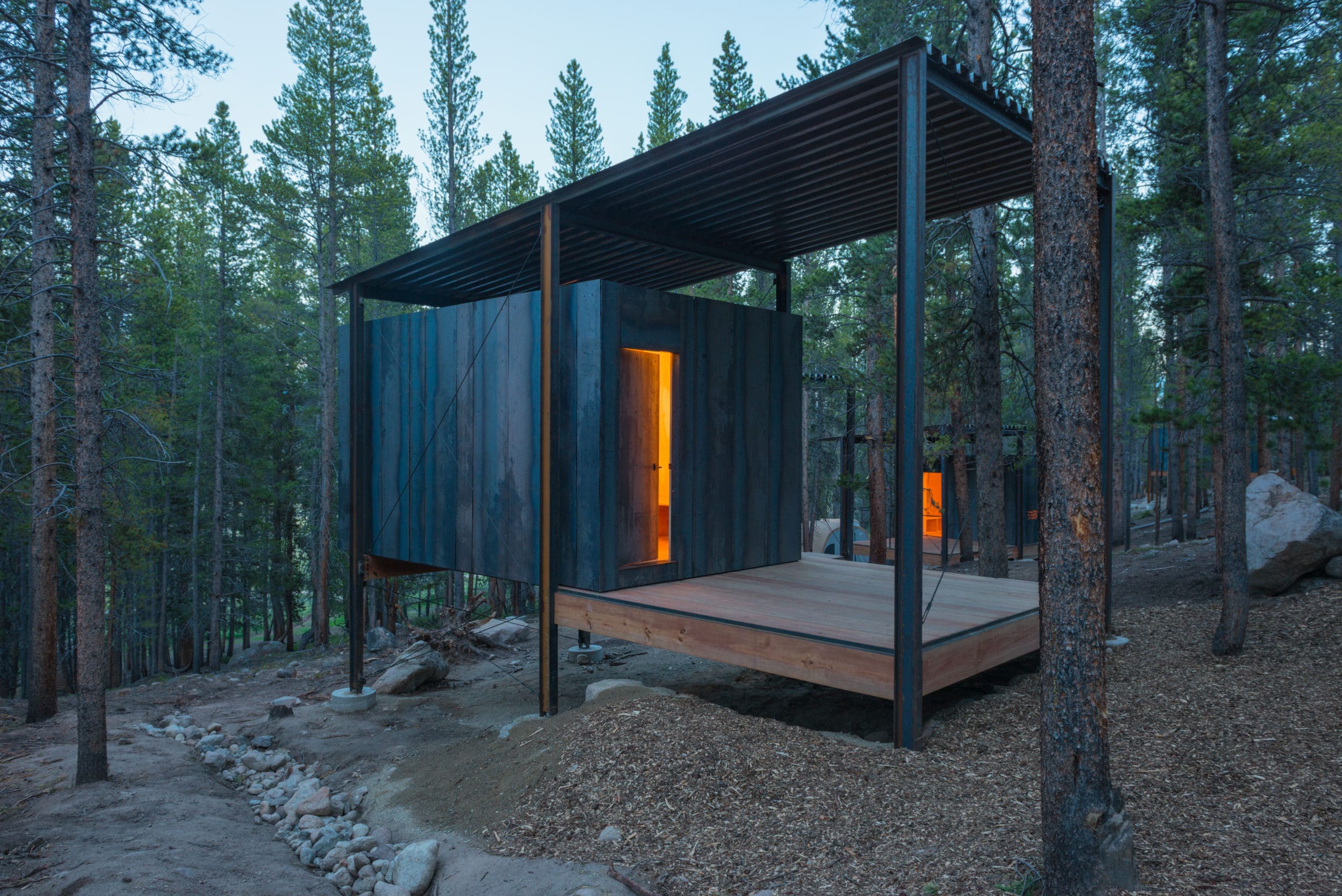
Besides being crafted to handle its snowy environs, the micro dorms were also built with materials selected for their durability and low maintenance. They were designed by Rick Sommerfeld and his design students at University of Colorado Denver. Photo by Jesse Kuroiwa
Designed by Rick Sommerfeld, founder and director of Colorado Building Workshop (the University of Colorado Denver’s design build program) and his graduate students, these 14 micro-dorms are a prime example of prefab home ingenuity.
Built for staff members of Outward Bound—an organization that delivers supervised educational expeditions in the wilderness for a variety of ages—these innovative dorms offer a sustainable, more inviting alternative to the conventional cabin. “We were looking at existing cabins, and saw that needs weren’t being met,” Sommerfeld previously told gb&d. “This type of housing didn’t provide a front porch or any type of social space for gathering.”
To remedy this each dorm features a quaint wraparound porch that faces its neighboring cabins, creating small community clusters and encouraging communal interaction. These porches are an extension of the exterior frame surrounding each cabin’s interior box, a feature that provides each dorm with greater resilience to precipitation and snow buildup.
To maximize the project’s efficiency and reduce construction time, all of the hot rolled steel and birch plywood wall pieces for the dormitories were prefabricated in Denver and then flat-packed to the build site. Nesting software was also implemented in designing the dorms’ prefab cabinetry, greatly reducing the amount of lumber waste.
7. Bella Bella Passive House
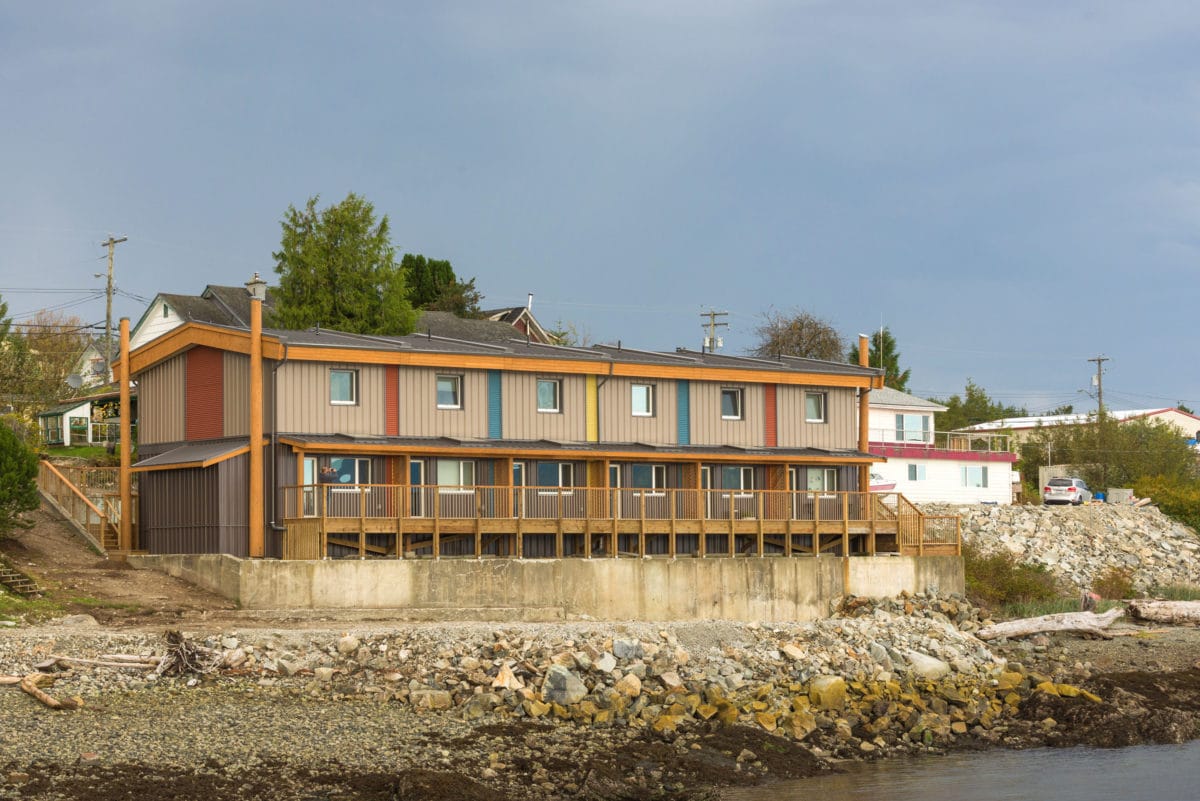
The Bella Bella house for staff of a remote hospital was built to Passive House standards, quickly and efficiently, using prefab techniques. Photo courtesy of Vancouver Coastal Health
Designed for Vancouver Coastal Health’s (VCH) R.W. Large Memorial Hospital by Mobius Architecture, the Bella Bella Passive House showcases just how beneficial prefabs can be when building in remote locations.
After a fire destroyed R.W. Large Memorial Hospital’s staff housing, it was imperative that VCH build a replacement as soon as possible—but because of the hospital’s remote location on British Columbia’s Campbell Island, a place where it might take over a year to construct a building from the ground up, doing so proved easier said than done. The island is only accessible by boat or plane, which made getting materials and a construction team to the site incredibly challenging.
To expedite the process VCH commissioned six two-story attached prefab townhouses from Mobius Architecture to be shipped in from the mainland after prefabrication. “A prefab structure taken up by barge presented a very quick and cost effective way to efficiently meet what would be needed in Bella Bella,” Glen Garrick, sustainability manager, transformation and innovation for VCH, told gb&d in a previous article. “In the end the project was completed at a cost of $2.6 million—about $500,000 less than it would have cost to construct the development onsite.”
Designed by Mobius Architecture and constructed in a Britco facility in the province, each of the project’s approximately 32 x 14 foot modules—12 in total—were carefully built and tested to Passive House standards in a closed, quality-controlled environment. Features like mineral wool, fiberglass insulation, airtight windows, heat and energy recovery ventilation units, and split-system heat pumps helped each module achieve maximum energy-efficiency.
While the modules were being prefabricated, prep work started at the actual build site—a common prefab practice that can help shorten the construction period by as much as 30%. All in all it took just nine months to complete the entire process.
8. Liv-Connected
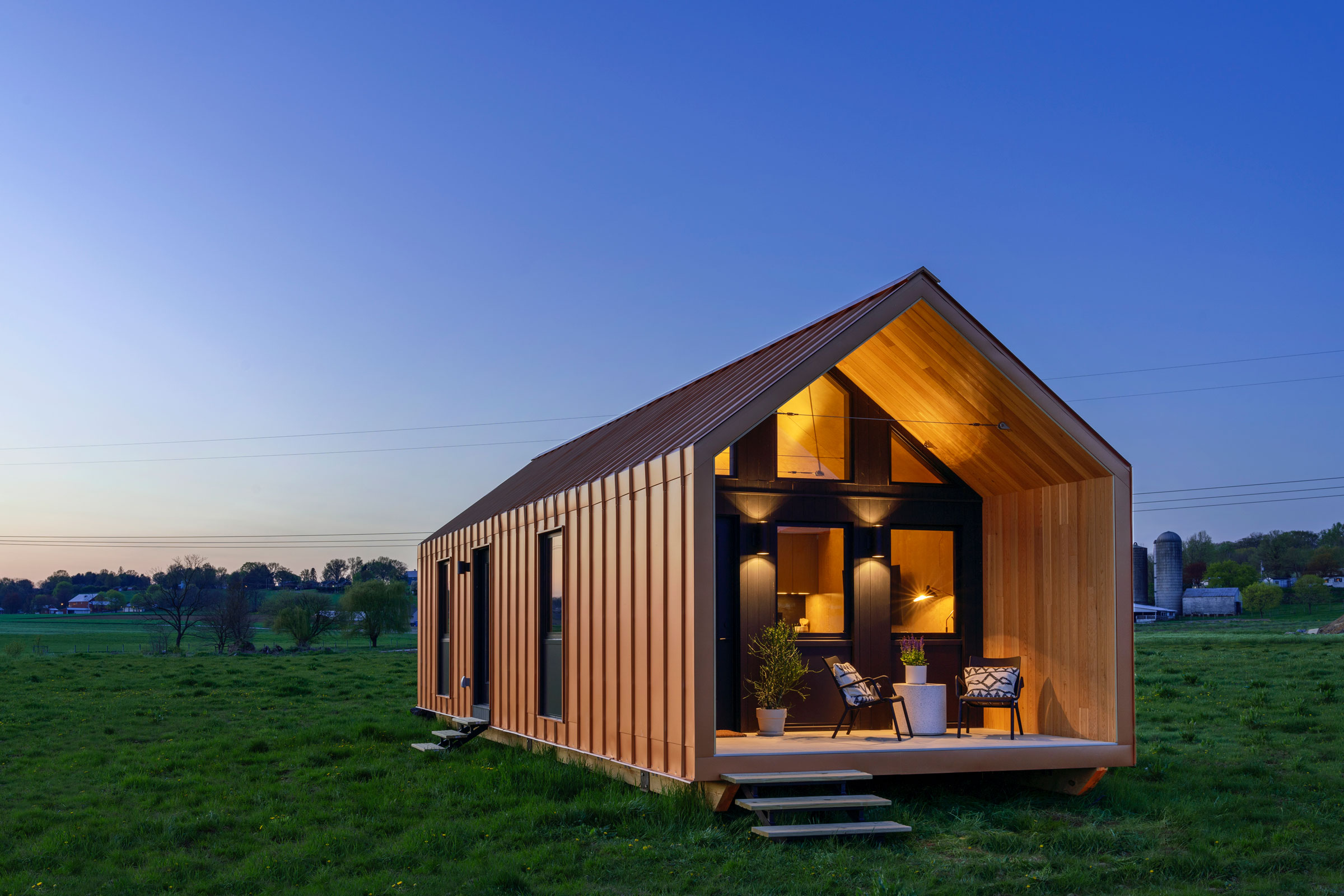
Liv-Connected manufactures design-focused homes that can be rapidly deployed and endlessly customized. Photo courtesy of Liv-Connected
Started as a disaster relief project, Liv-Connected was founded on the premise of creating a sustainable alternative to the standard FEMA trailer and providing affordable housing for thousands of people in a very short amount of time. It has since become a leading designer of rapidly-deployable prefab modular homes marketed towards the general public, with the Conexus and Via being the company’s two base options.
Conexus is designed as a modular prefab home and utilizes Liv-Connected’s proprietary Component Linked Construction (CLiC™) system that allows the home to fold up extremely tightly and reconfigured into a variety of floorplans. The CLiC system also allows for additional elements—like health care technologies to be added to the home over time. “We love the idea that the house is a more permanent thing that can change over time, and that includes the health equipment,” Jordan Rogove, COO and director of architecture and design at Liv-Connected, previously told gb&d. “If you don’t want to buy it right off the bat you can add it later when you get a little older.”
Via, on the other hand, is a traditional manufactured home and is designed for a life in motion. As of 2023, the Via home is available in three semi-customizable models—Standard, Modern, and Farmhouse—all of which support a variety of different layouts.
All Liv-Connected modular units are designed with sustainability in mind and only generate 10% of the waste that a conventional stick-built construction project would create. Each modular unit comes solar ready, meaning photovoltaic panels may be purchased and installed at a later date if desired.