Story at a glance:
- Prefab Homes are built in modules off-site and then transported to be assembled on-site.
- In just three days in July 2020, Plant Prefab installed a four-unit townhome development in Los Gatos, California.
- Prefab Passive Houses use 80% less energy for heating and cooling than conventional buildings.
Not long ago, the term “prefab home designs” would likely conjure images of cheap, unattractive mobile homes. But nowadays, as more architects are seeking inexpensive yet sustainable solutions, the market for stylish and durable prefabricated homes is growing.
Prefab homes are built in components and/or modules that are then transported and assembled on-site. This manufacturing process often leads to less wasted material and time. We’ve compiled a list of prefab firms leading the way in creating quick yet sustainable prefab home designs.
1. Ecocor
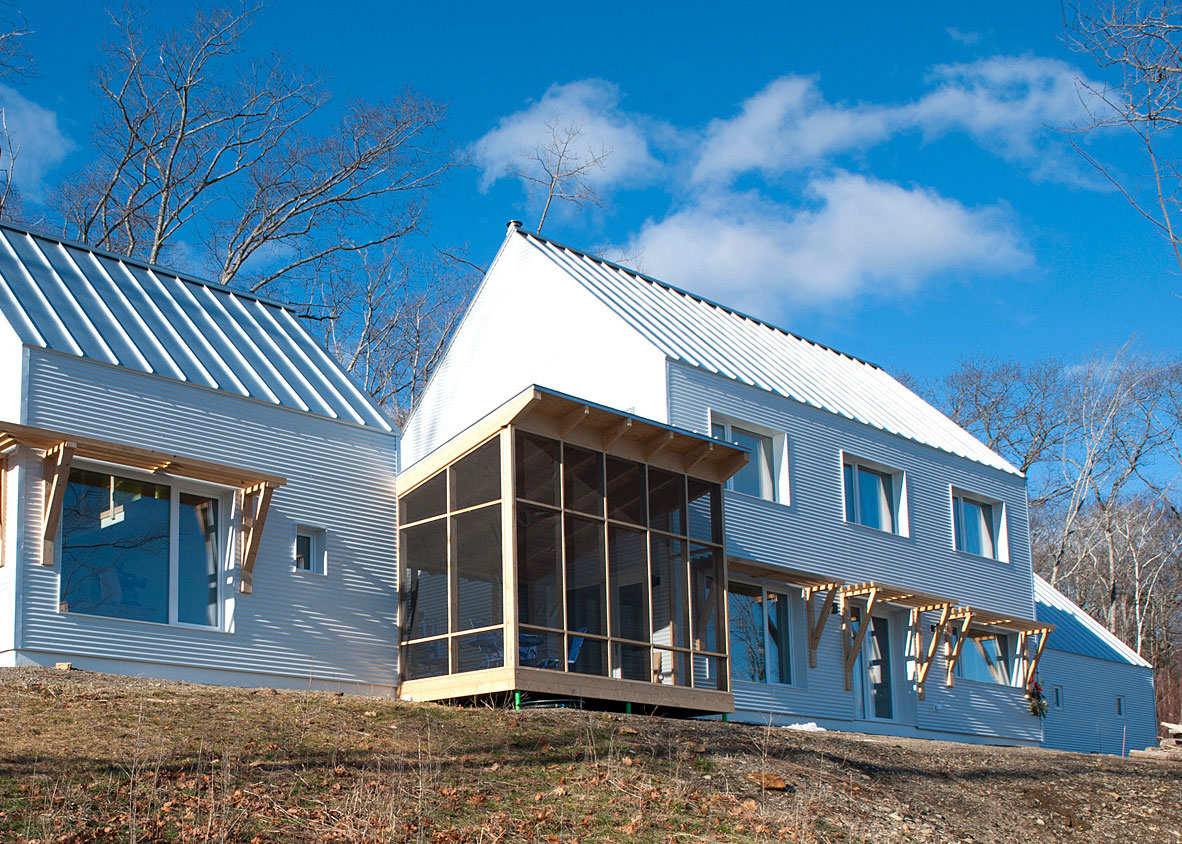
Ecocor has sustainability in mind as they build their projects by focusing on using 80-90% less waste. Photo courtesy of Ecocor
Since its inception Ecocor has focused on the design, manufacture, delivery, and assembly of high-performance Passive House buildings, while cutting construction waste and shortening time-to-occupancy. Although they didn’t begin their prefabrication process until 2013, in just three years they built more than 35 passive homes, Ecocor owner and technical director Christian Corson previously told gb&d.
In the Ecocor factory, panelized walls, floors, and other components are fabricated in a highly controlled environment, and much of the construction waste is reused in other projects. The reduction in waste and time-to-completion transfers to cost savings for the customer, making these types of modular homes even more accessible.
“It makes no sense to ask our clients to raise their families and children in a home built out of toxic materials. At the same time, not using these materials means the people working for us, on the floor of the factory day-to-day, they stay healthy, too,” Corson said.
2. Plant Prefab
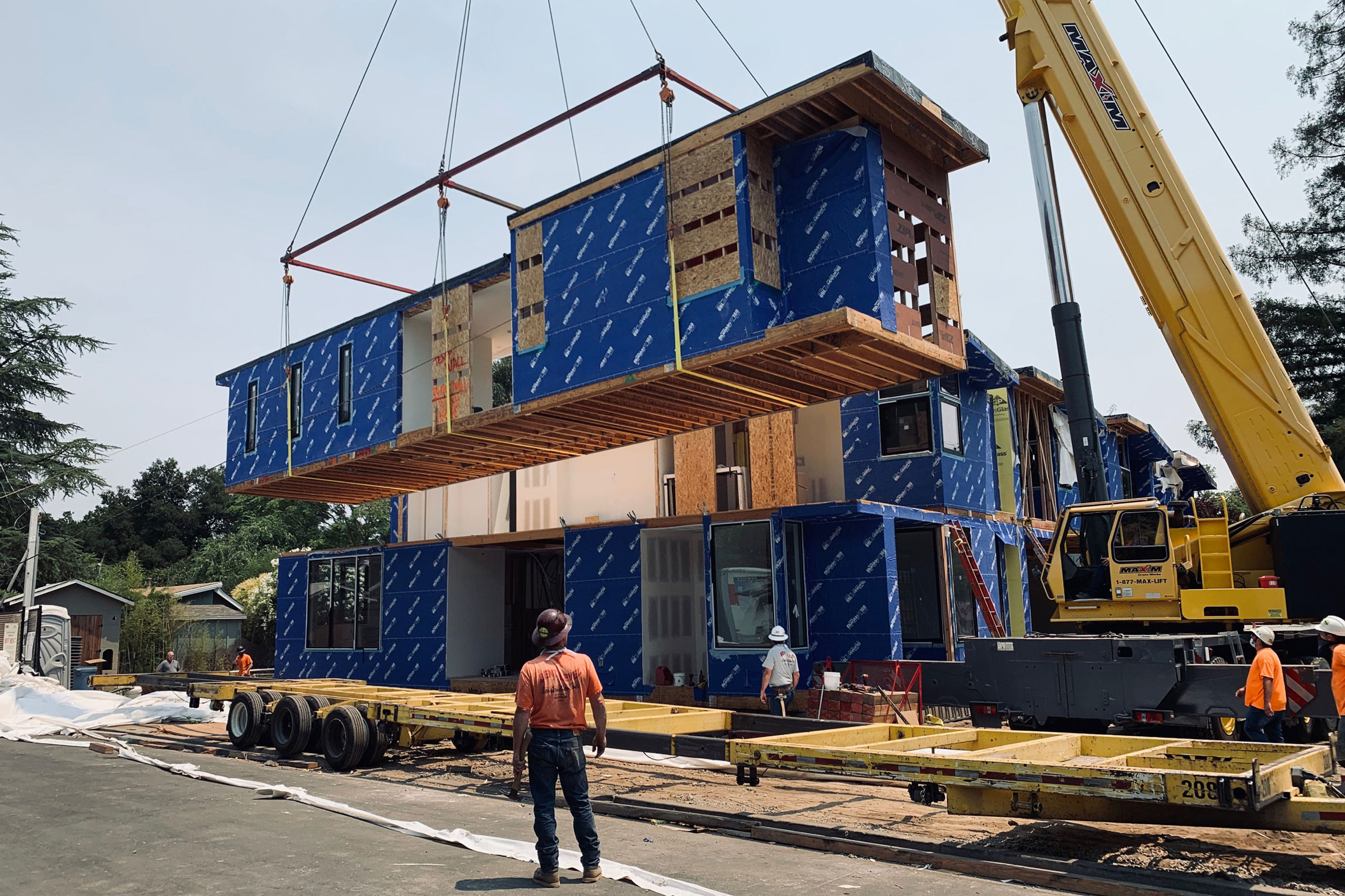
Three days is all it took for Plant Prefab to install custom-designed homes by Metro Architects.
Photo courtesy of Plant Prefab
Plant Prefab started as a spinoff from founder Steve Glenn’s LivingHomes prefab firm in 2016, when Glenn wanted to meet the needs of consumers while also addressing rising emissions and sustainability standards.
“We can’t and don’t compete with builders who use unskilled labor or inferior-quality, unhealthy building materials,” Glenn previously said in an interview with gb&d. “Our efficient processes achieve drastic savings in labor hours, materials, and energy use. In many markets this makes building with Plant less expensive than building onsite. However, this is not true for markets with very inexpensive local labor or for locations far from our factory, in which case the cost of transportation can cancel out the construction cost savings.”
In July 2020, in just three days, Plant Prefab installed a 11,054-square-foot, four-unit townhome development in Los Gatos, California. The custom-designed residences by Metro Architects are a prime example of how Plant Prefab’s building system allows for faster construction that’s more efficient than traditional, site-based methods. This is in large part due to the fact that most of the construction takes place in the factory before the structure—which is essentially delivered on the back of a truck in large building blocks with everything complete inside—is taken to the site.
3. Richard Pedranti Architect
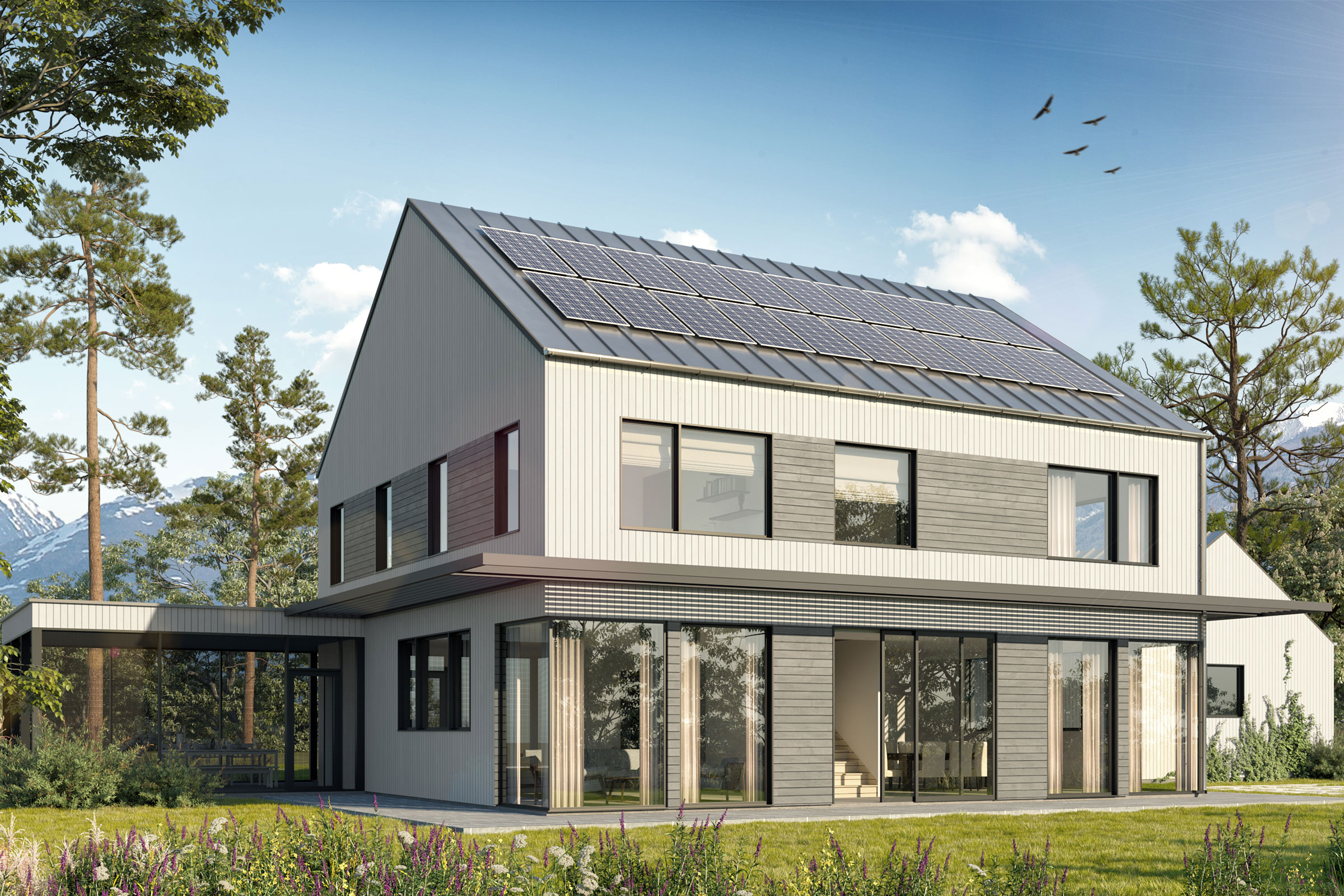
Prefabricated passive houses in three styles are the latest from Plant Prefab and Richard Pedranti Architect. Courtesy of Plant Prefab
Plant Prefab recently partnered with Richard Pedranti Architect (RPA) to launch its Passive House LivingHomes program, with three prefabricated designs they’re calling RPA LivingHome 1, 2, and 3.
Pedranti has been designing and building passive houses for more than a decade and more recently got into the prefab market. He believes Plant Plant Prefab’s RPA LivingHome designs offer the most complete Passive House products he’s ever seen on the market. “By using the Plant Building System—Plant’s comprehensive and flexible off-site building platform—we were able to design custom, high-performance homes with Passive House-level envelopes and sustainable finishes,” Pendrati previously said to gb&d.
Passive House–certified homes use 80% less energy for heating and cooling than conventional buildings, and Plant Prefab’s Plant Building System uses highly specialized modules, and all RPA LivingHomes are designed to meet net zero energy standards.
4. Phoenix Haus
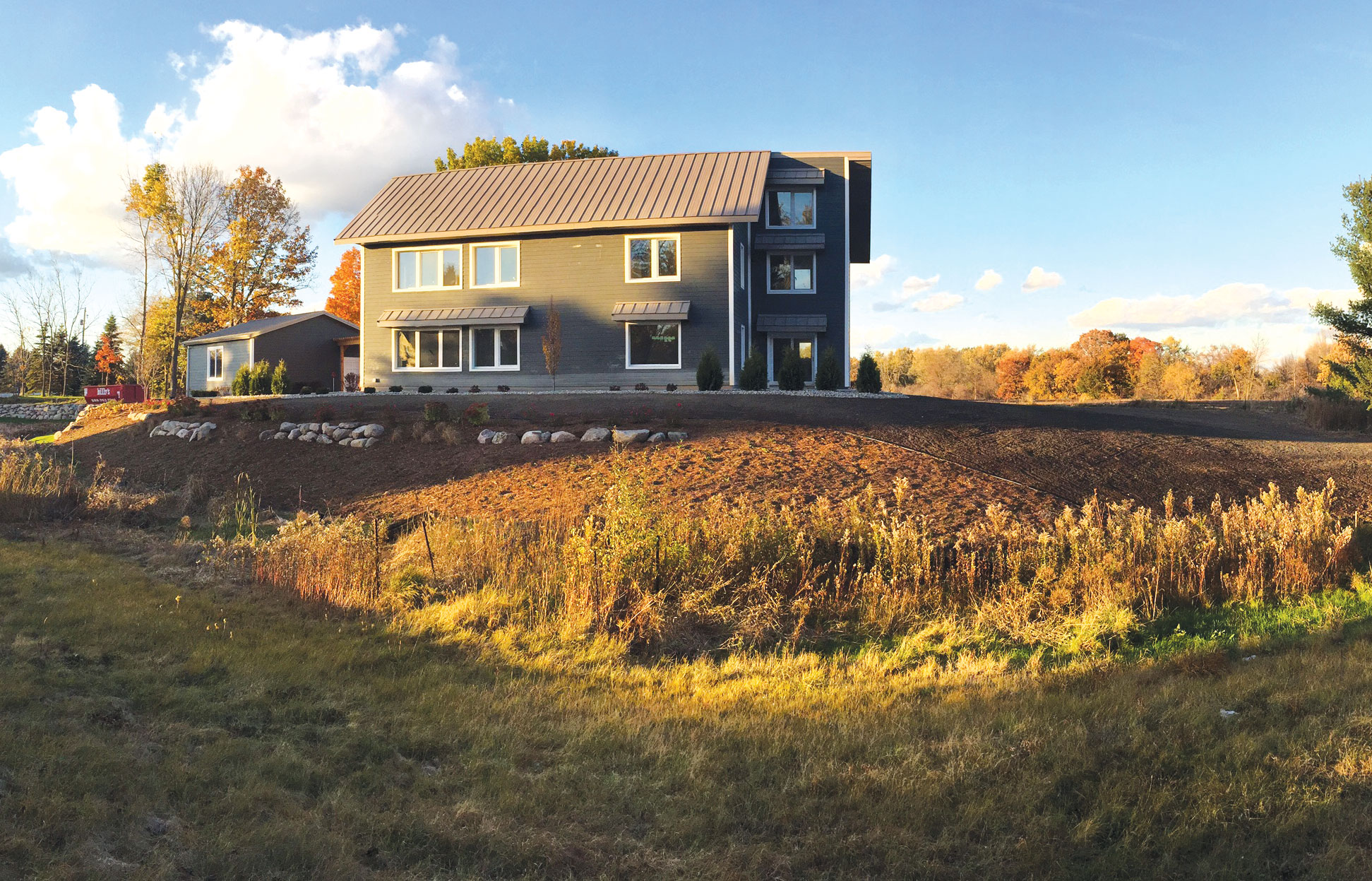
A typical Phoenix Haus prefab home is between 2,500 to 4,000 square feet and one to two stories. Photo courtesy of Phoenix Haus
Anton Cech, a native of northern Germany, emigrated to the US in 1926 and built a successful company from the ground up with almost nothing to his name. Seeing a growing need for a marriage between Passive House and high-efficiency, low-cost prefabrication methods in the building industry, Cech’s children and grandchildren started Phoenix Haus in 2011. Their goal was to influence the construction industry and create innovative, healthy, environmentally conscious buildings.
Today they’re doing all that and more in the heart of the old American manufacturing industry in Detroit, in a 1900s factory that once served as a stamping plant. “Solely from organic growth, without major marketing or PR campaigns, Phoenix Haus receives inquiries almost on a daily basis from around the country,” project manager Kate McDonald previously told gb&d.
A typical prefab green house from Phoenix Haus is between 2,500 and 4,000 square feet and one to two stories. McDonald says their market is mostly middle-income, with ages ranging from 26 to 55.
Although McDonald admits Passive House standards often mean higher costs, even when prefabricated, the return in energy savings—and thus energy bills—is a worthwhile return on the investment.
5. Mobius Architecture
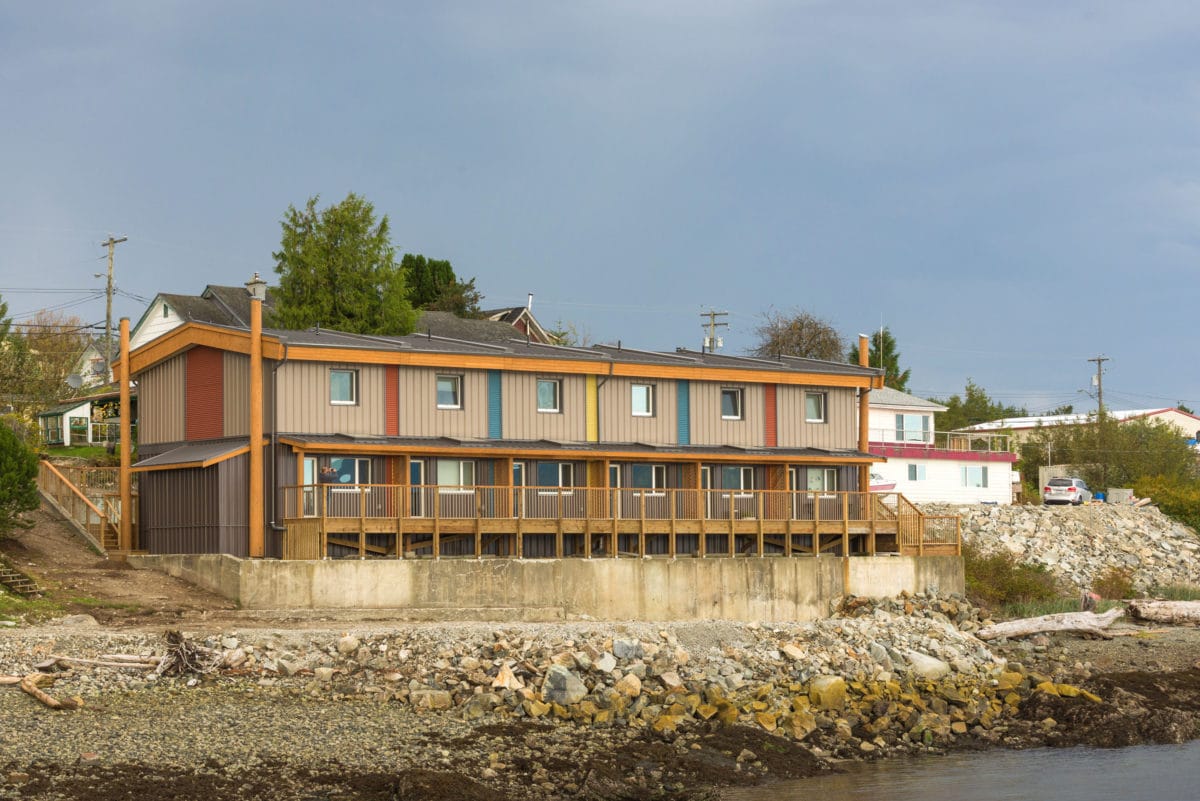
The Bella Bella house for staff of a remote hospital was built to Passive House standards, quickly and efficiently, using prefab techniques. Photo courtesy of Vancouver Coastal Health
When a fire destroyed Vancouver Coastal Health (VCH) staff housing in a remote part of British Columbia, no one was surprised by the plan to rebuild. But its location on rugged Campbell Island—where most of the 1,500 people living on the island belong to the Heiltsuk First Nation—made access to supplies and construction crews tricky. Add to that the decision to go from LEED to Passive House standards, and the undertaking was no small feat.
But it was all accomplished in just nine months by using a prefab home package with design supervision from Mobius Architecture.
“A prefab structure taken up by barge presented a very quick and cost effective way to efficiently meet what would be needed in Bella Bella,” Glen Garrick, sustainability manager, transformation and innovation for VCH, previously told gb&d. “In the end, the project was completed at a cost of $2.6 million—about $500,000 less than it would have cost to construct the development onsite.”
6. Square Root

Square Root built upon Chicago’s first green prefab house, the C3, and is working to create more projects with design and sustainability in mind. Photo courtesy of Square Root Architecture and Design
Armed with some lessons learned after designing Chicago’s first green prefab modern home, the C3, Jeffrey Sommers of Square Root Architecture and Design created version 2.0—a hybrid approach to prefab that draws on the best parts of both modular and on-site construction. “This house was a case study on how and why to build better,” Sommers said to gb&d in a previous interview. The project received EnergyStar and Indoor AirPlus certifications and was third-party tested for a HERS (Home Energy Rating System) score of 43.
The house was constructed with a structural insulated panel (SIP) system. Generically referred to as a flat-pack, this system used to construct the exterior walls and roof forms a highly insulated thermally broken building envelope with minimal opportunities for air and water infiltration. Although this form of prefab requires more onsite construction, it’s a hybrid approach that takes advantage of the better qualities of both prefab and onsite construction, and minimizes transportation and erection costs of the prefab units. “It allowed for lower shipping costs, lower craning costs, and the ability to work within the city’s requirements for on-site inspections,” Sommers told gb&d.
7. Colorado Building Workshop
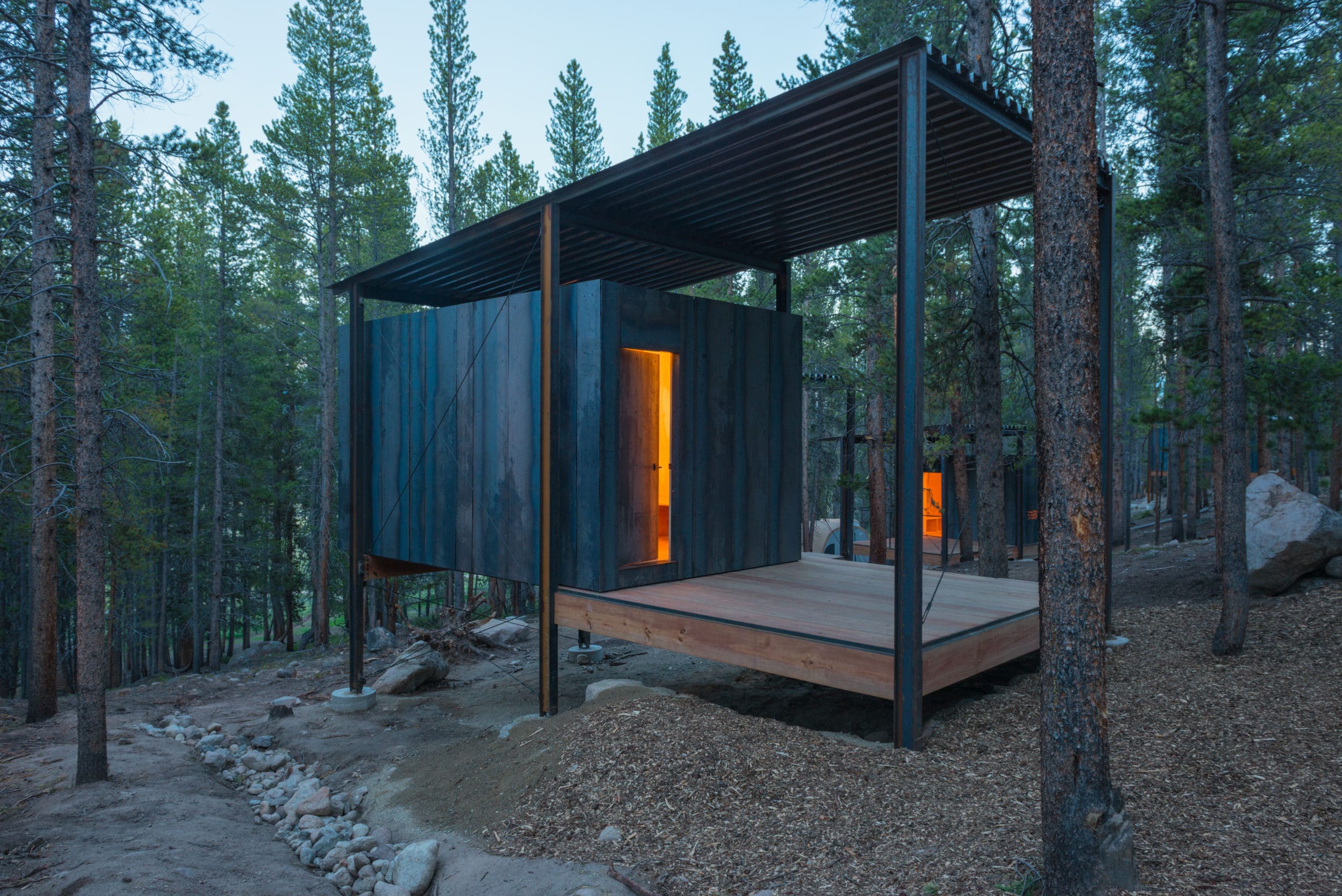
Besides being crafted to handle its snowy environment, the micro dorms were also built with materials selected for their durability and low maintenance. They were designed by Rick Sommerfeld and his design students at University of Colorado Denver. Photo by Jesse Kuroiwa
Rick Sommerfeld, founder and director of Colorado Building Workshop—the design build program at the University of Colorado Denver—led 28 graduate students in the completion of 14 micro dormitories set in a gorgeous pine forest outside the city.
The project was the result of a partnership with Outward Bound, which delivers supervised, educational expeditions in the wilderness for a variety of age ranges. The dorms will provide housing to Outward Bound staff, who come from all over the world and need a place to rest between courses.
Sommerfeld and his students were intent that the cabins meld into the background of the woods. The micro dorms were also built with materials selected for their durability and low maintenance. “There was a want from both the client and the students to create something they didn’t have to paint or refinish,” Sommerfeld said in a previous conversation with gb&d.
Prefabrication increased project efficiency; from budgeting (about $9,000-$10,000 per cabin; to prefabricating the wall pieces in Denver and then flat packing them for their voyage to Leadville; to using nesting software for the cabinetry to avoid wasting a scrap of wood. “It allows us to apply any leftover wood to the next cut automatically,” Sommerfield said. “It’s a more sustainable approach.”