Story at a glance:
- Prefabricated building materials are manufactured in a controlled offsite environment before being transported to the construction site for assembly.
- Building with prefabricated materials offers many benefits, including less waste, faster construction times, lower project costs, and reduced environmental impact.
- Structural insulated panels and precast concrete panels are amongst the most common prefabricated building materials.
As the AEC industry continues to emphasize efficiency and sustainability as guiding design principles, the importance and prevalence of prefabricated building materials in construction has grown exponentially.
This article is an introductory guide to prefabricated building materials and their benefits.
What are Prefabricated Building Materials?
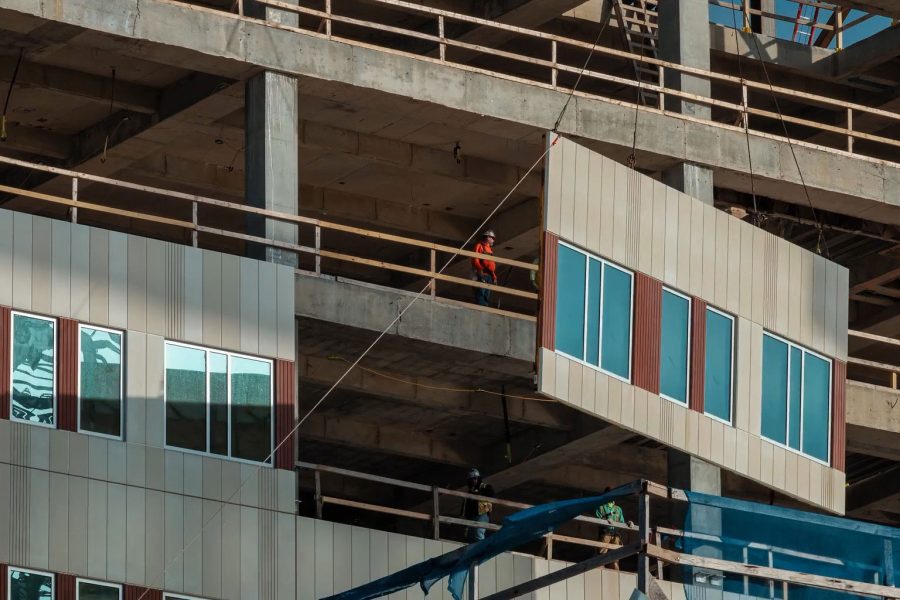
Lightweight GateLite precast concrete panels from GATE Precast helped to accelerate construction on the Baptist Hospital Campus in Pensacola by five months. Photo courtesy of GATE Precast
Prefabricated materials are an increasingly popular subset of building materials that are designed and manufactured in highly controlled offsite factories to rigorous quality standards; once produced, these materials are then shipped to their respective job sites for final assembly.
“Prefabrication involves the offsite manufacturing of building components that are later assembled on-site,” Dustin Stephens, vice president of Sage’s—a leading construction management software company—construction and real estate practice in Beaverton, Oregon, previously wrote for gb&dPRO. Generally speaking there are three core types of prefabricated building materials: panelized, modular, and assemblies.
- Panelized. Refers to any prefabricated building material that is flat; may be used to construct floors, walls, and roofs.
- Modular. Refers to the practice of manufacturing complete rooms, units, or sections of a building entirely offsite.
- Assemblies. Describes prefabricated parts of a specific building component that are then assembled and installed whole; includes things like premade balconies and staircases.
In this article we’ll focus primarily on prefabricated panels and assemblies. For more information on modular and whole-building prefabrication, check out our articles on prefab homes.
The Benefits of Prefabricated Building Materials
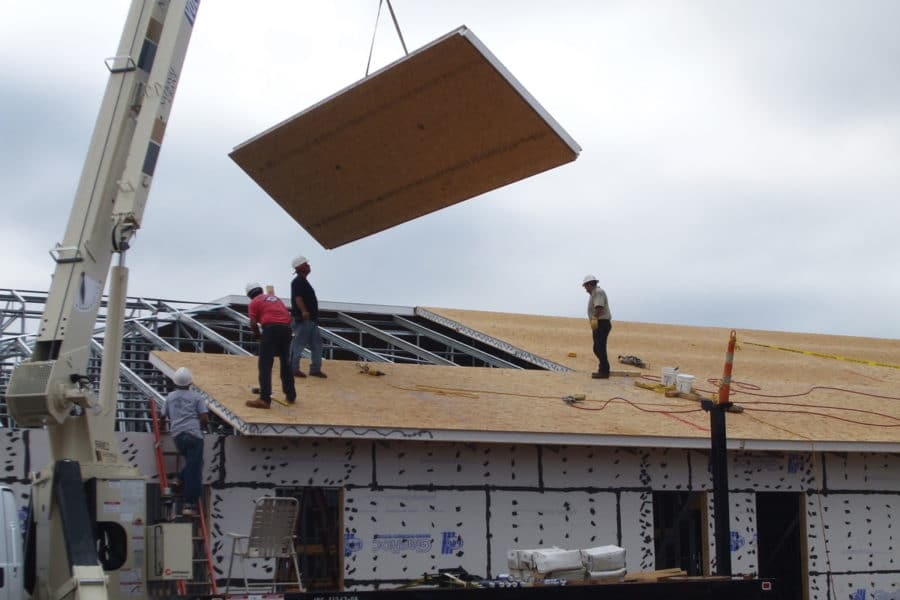
Prefabricated building materials produce less waste, reduce construction times, and help reduce project costs. Photo courtesy of FischerSIPS
Prefabricated building materials have become increasingly popular in recent years, in large part thanks to the range of benefits they offer.
Less Waste
The controlled environment in which prefabricated building materials are designed and manufactured means that they produce less waste compared to building materials prepared entirely on the job site. “Prefabrication can also help offset a project’s environmental impact,” writes Stephens. “When units are created in bulk, manufacturers can utilize more of the building materials with less scrap left over.”
This is especially true of prefab materials that utilize nesting software to cut and prepare each component, as these programs help lay out cutting patterns in the most optimal and efficient way to minimize the amount of wasted material left over. It has also become increasingly common for manufacturers of prefabricated materials to recycle what little leftover material is produced into new products. “Additionally, many prefabrication facilities have implemented recycling programs to further minimize waste,” Stephens writes.
Faster Construction Times
Another benefit of prefabricated building materials is that they help reduce the time spent on on-site construction, allowing projects to be finished faster with less impact on surrounding communities. This is largely due to the fact that prefabricated materials arrive ready for assembly, eliminating the need for extensive measuring, cutting, and other time-consuming preparatory actions.
“A lot of time on job sites you see guys out there scratching their heads, trying to figure out how to cut a complex angle and make it work,” Damien Pataluna, owner of FischerSIPS—a leading provider of structural insulated panels—previously told gb&d. “If we can get it figured out in a safe factory setting and then ship it out to a jobsite where it’s pre-assembled on the ground, think of the time-saving safety factors that are involved with that.”
What’s more, the manufacture of prefabricated building materials isn’t dependent on fair weather conditions, meaning progress can be achieved even on rainy, windy, or extreme temperature days. Prefabrication also means that offsite and any necessary on-site work—e.g. excavation, grading, foundation work, et cetera—can progress at the same time, enabling faster construction. All in all, extensive use of prefabricated materials can, on average, cut construction times by 30 to 40%.
Reduced Environmental Impact
Besides minimizing waste, prefabricated building materials help minimize a project’s total environmental impact in several additional ways, most notably by reducing transportation-related emissions and improving energy efficiency. “Prefabrication helps reduce the time spent driving to and from the job site, lowering carbon emissions by streamlining transportation, and also reducing noise and dust on the job site,” writes Stephens.
And because they are designed and manufactured in controlled environments to high quality standards, prefabricated materials tend to be more precise and possess fewer imperfections than materials prepared wholly on-site. As a result, prefabricated building materials typically make for tighter building envelopes, drastically reducing the amount of gaps through which air and thermal energy may pass.
By creating more airtight buildings, prefabricated materials ultimately help to reduce energy consumption, improving energy efficiency and lowering a project’s total lifetime emissions.
Lower Project Costs
Building with prefabricated materials is considered a cost-effective option that ultimately helps lower a project’s total expenses by optimizing material usage, reducing waste and rework, and improving overall labor efficiency. “During prefabrication units are assembled in factory-like settings using machines and automated technologies,” writes Stephens. “This enables greater quality control and delivers faster production and cost savings for both on-site labor and building materials.”
By minimizing the likelihood of rework and delays caused by weather or other factors, prefabrication can also make budgeting more accurate and predictable.
Types & Examples of Prefabricated Building Materials
As prefabrication technology continues to improve and advance, the catalog of prefab materials grows ever larger. Here are some of the more common examples available today.
Architectural Panels
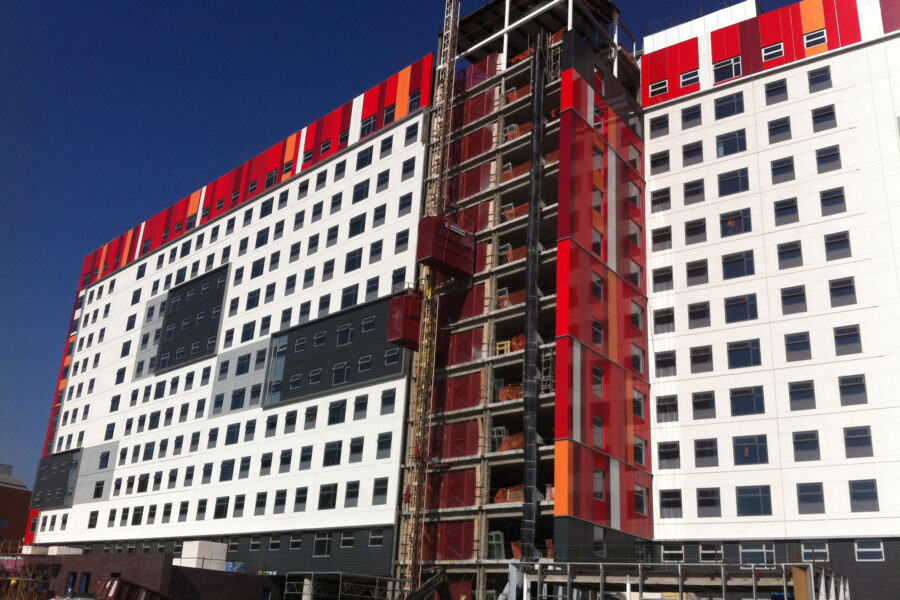
Prefabricated architectural panels are well-suited to deep energy retrofits as they may be installed quickly without displacing occupants. Photo courtesy of Tremco CPG
In a world that increasingly values energy efficiency and sustainability in the built environment, prefabrication technology can help projects meet green building goals in the form of prefab architectural panels. Prefabricated architectural panels are a type of 2D wall system encompassing framing, continuous insulation, moisture and air barriers, and exterior cladding.
Prefabricated architectural panels are particularly useful for deep energy retrofits, as they allow upgrades to be made to a building’s envelope in a timely manner without displacing occupants in the process.
“If you’re in construction, you know the labor force, you know the timetables. You can’t be working on apartments, for example, for months and months and months,” David Hutchinson, deep energy retrofit specialist at Tremco CPG, previously told gb&d. “Retrofit projects have very tight windows to get completed. The only way to do an envelope with the timeframes that we’re looking at, with the labor shortage, and everything else, is through prefabrication.” Tremco is a leading construction products manager and offers a variety of prefab architectural panel solutions.
Prefabricated architectural panels also help address one of the biggest challenges of deep energy retrofits: their cost. “Prefabrication can drive the price point down, which will help accelerate opportunities and create the budgets that make deep energy retrofits a lot more affordable,” Chuck Bundrick, key account executive for commercial construction and renovation at Tremco, told gb&d in a previous interview. That’s because architectural cladding panels are manufactured indoors and can be installed in most temperature conditions, reducing the likelihood of costly weather-related delays.
Beyond their ease of installation and affordability, prefabricated architectural panels are well-suited to deep energy retrofits as they may be designed to meet specific energy requirements. “Every deep energy retrofit project starts with an energy model. The panels allow you to design exactly to what you need,” Hutchinson says. “You can design to your thermal performance, your air leakage, to everything that you’re requiring to meet your standards and the state’s standards.”
Prefab Aluminum Balconies
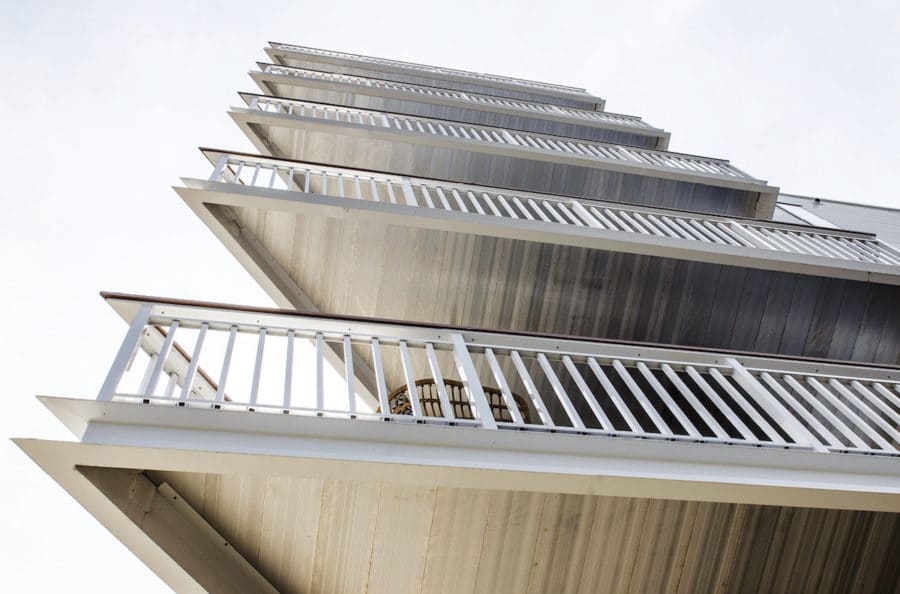
Prefabricated aluminum balconies can be installed in a fraction of the time required to assemble and install traditional balconies. Photo by Nicole Agen
Over the last few decades balconies have become a staple of multifamily housing projects, but balcony installation can be a difficult and expensive process—one that requires onsite laborers to assemble the structures while simultaneously attaching them to the building. To help remedy these issues companies like Midwest Iron have begun manufacturing prefabricated aluminum balconies that arrive onsite as completed assemblies ready to be installed as a single unit.
Once delivered the balconies are unloaded and workers simply bolt them on to the building; as many as 25 prefabricated balconies can be installed in six hours, greatly reducing the overall time and labor involved. “There is no finding all the pieces to put together and constructing them on-site, which is a huge value,” Howard Wurgler, owner of Midwest Iron, previously told gb&d.
Midwest Iron makes each balcony to order and offers a high degree of design flexibility that allows for ample customization. The company has 12 standard colors, thousands of color options for the powder coating, and offers a range of different rail patterns as well as etching patterns for glass balconies.
This customization combined with ease of installation has made prefabricated balconies an extremely appealing choice for architects and designers. “We’ve found so many options for customization—the rails, the decking itself, and colored glass,” Eric Ponto, partner at Engberg Anderson Architects—who have worked with Midwest Iron on multiple projects—told gb&d in a previous publication. “We’ve been able to use the same product but customize the look for each project.”
Structural Insulated Panels
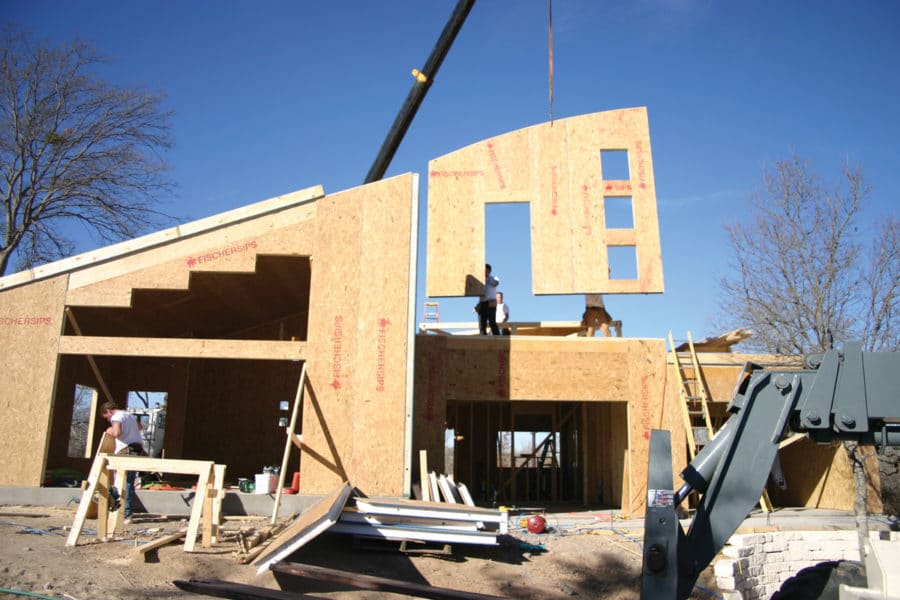
SIPs are an extremely popular prefabricated building material thanks to their positive impact on a project’s energy efficiency. Photo courtesy of FischerSIPS
Structural insulated panels (SIPs) are a type of lightweight, high-performance composite paneling used in residential and light construction projects to create walls, floors, roofs, and even foundation systems. SIPs consist of an insulated rigid foam core sandwiched between two sheathing panels and are designed to share the same structural properties as traditional I-beams or I-columns; the insulated core acts as the web while the sheathing fulfills the function of the flanges.
Most SIPs use oriented strand board (OSB) for their sheathing, as OSB is engineered to provide maximum strength and durability; high-grade OSB sheathing gives each SIP the strength to maintain a vertical point load of just a ton and a total vertical uniform load of two tons. The insulated core of an SIP is typically made from extruded or expanded polystyrene foam, graphite polystyrene foam, polyurethane foam, or polyisocyanurate foam.
The vast majority of SIPs are prefabricated offsite in highly controlled, low-waste environments before they are then shipped to job sites and installed. In the United States, SIPs are available in sizes ranging from 4 feet to 24 feet in width (though longer widths may be requested in special circumstances), typically measuring 8 to 9 feet tall, and range between 4 to 12 inches in thickness.
Aside from being incredibly energy efficient and easy to install, SIPs are also surprisingly strong. “The way SIPs are tied together with the long panel screws creates incredible sheer strength,” Pataluna says. “You won’t typically have situations where the trusses or individual pieces of sheeting can be ripped off the roof because the roof panels are one solid sheet inside and outside that are screwed down to the walls. You’d almost have to pick up the entire house to rip it off the foundation.”
Mass Timber
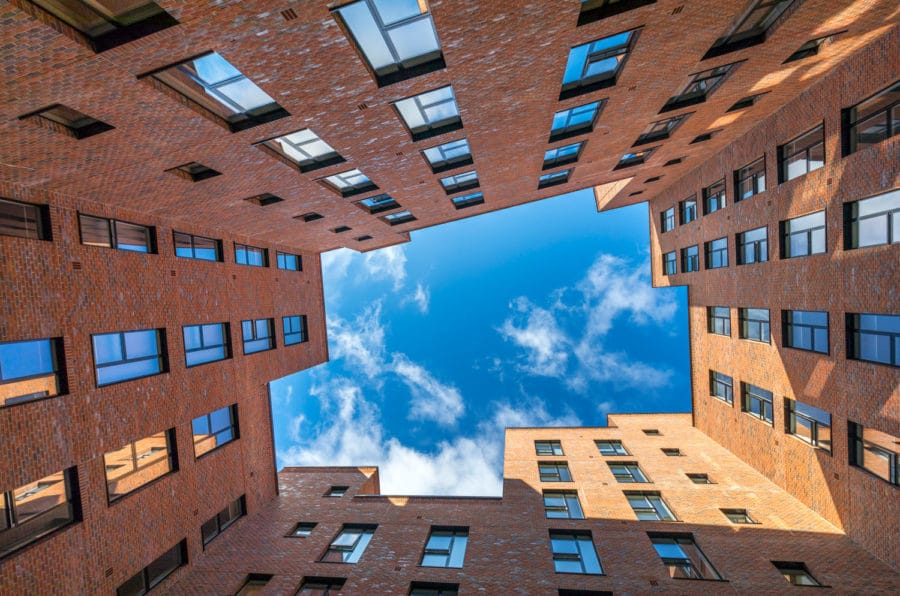
The use of CLT in Dalston Works eliminated an estimated 80% of on-site waste and cut construction time by about eight months. Photo by Daniel Shearing
Mass timber refers to a subset of prefabricated, engineered wood made by binding multiple layers of wood planks together; the resulting product is much stronger and more structurally sound than traditional timber, which allows it to be used as a viable, low-carbon alternative to concrete and steel.
There are four basic categories of mass timber: cross-laminated, nail-laminated, dowel-laminated, and glue-laminated.
- Cross-laminated timber (CLT). Several layers (typically an odd number) of wood planks are glued together, with each layer laid perpendicular to the one above and below it.
- Nail-laminated timber (NLT). Created by binding multiple layers of wood together using nails; NLT is considered to be one of oldest, if not the oldest, forms of mass timber.
- Dowel-laminated timber (DLT). Wood planks are drilled and then bound together by long wooden dowels.
- Glue-laminated timber (Glulam). Layers of wooden planks are attached to one another using glue; glulam differs from CLT in that each layer of planks is laid in the same direction.
These prefabricated timber products offer increased compressive strength and flexibility compared to traditional raw timber while also allowing for faster construction times. As a result, they can be used to construct load-bearing features such as structural panels, beams, and posts, opening up a whole new world of possibilities for large-scale timber construction.
One of the world’s largest mass timber buildings, Dalston Works, was built primarily from prefabricated CLT—the usage of which helped reduce waste and onsite deliveries by an estimated 80% while also shaving an estimated eight months off of the construction timeline.
Precast Concrete Panels
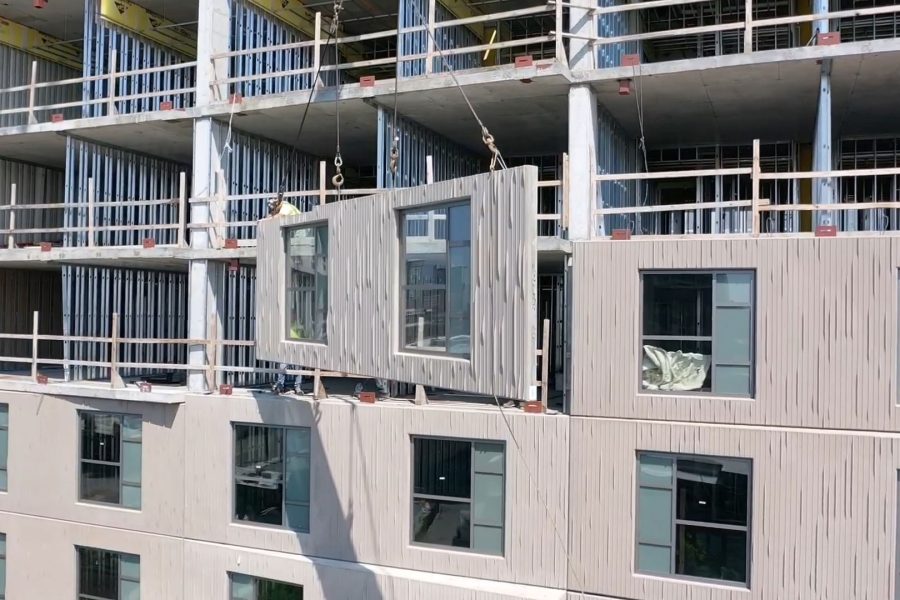
The Printing House Hotel, part of the Tapestry Collection by Hilton, in Nashville, uses GATE Precast’s unitized precast solutions. Photo by Chad Baumer Photography
Traditionally concrete is mixed and cast onsite, which can make it difficult to maintain a consistent product quality. Precast concrete slabs and panels, on the other hand, are prepared, cast, and cured in a highly controlled setting before being shipped to the project site. This helps minimize waste production, uses less water than pour-in-place concrete, and ultimately reduces the amount of soil and water contamination.
Some precast concrete manufacturers like Fabcon and GATE Precast also use recycled materials in their precast slabs, which helps keep waste out of landfills and reduces carbon emissions. Today precast concrete is used to build everything from foundations and walls to bridges and even entire buildings. “It’s a timeless material that doesn’t weather,” Brian Griffis, vice president of sales at GATE Precast, previously told gb&d. “It holds up to the elements and is very sustainable in its fabrication and longevity.”
And despite concrete’s reputation as a drab, brutalist material, precast concrete is actually quite flexible from an aesthetics standpoint, with many companies offering finishes in a variety of colors, textures, and styles. GATE Precast, for example, is a leading provider of resilient architectural precast concrete systems; their GateStone finish is designed to mimic the look and texture of natural stone while also supporting an expansive palette of colors to choose from.