Story at a glance:
- Advancements in green hydrogen technology can help facilitate a transition to cleaner fuel sources.
- Modular construction and prefabrication can help to reduce material waste and improve energy efficiency in the built environment.
- Innovations in carbon capture, storage, and utilization technologies help industries and other entities decarbonize and combat climate change.
As the world continues to suffer the effects of anthropogenic climate change, efforts continue across sectors to build a greener, more environmentally friendly future.
Here are 12 sustainable innovations that are helping to make the world a greener place.
1. Low-Carbon & Ultra High-Performance Concrete
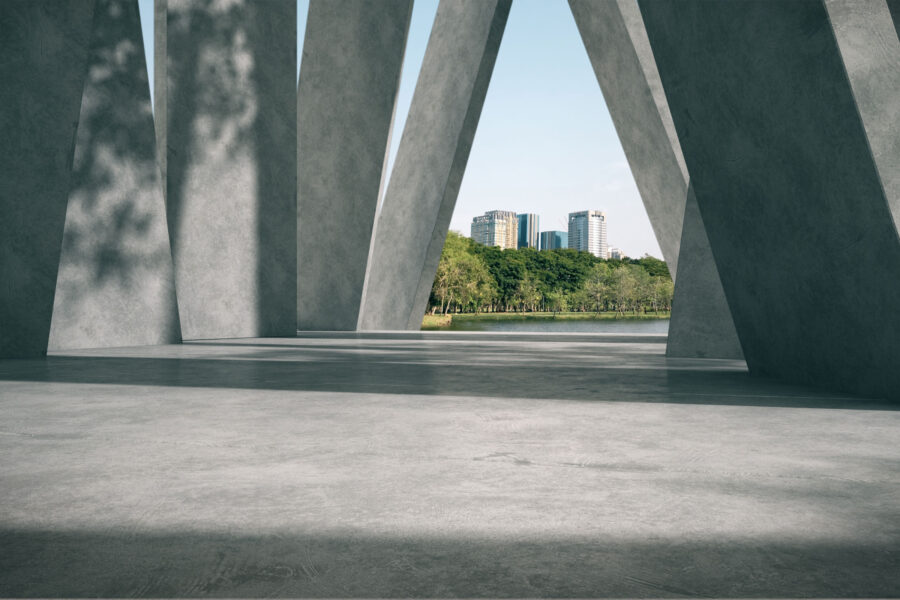
Photo courtesy of Chryso
As the second-most used resource in the world, concrete is a staple within the AEC sector and is found in most residential, commercial, and infrastructural projects. The problem with concrete is that it is an extremely carbon intensive material. The concrete and cement industry is responsible for approximately 7 to 8% of the world’s total CO2 emissions.
The bulk of these emissions are produced during the production of cement—one of concrete’s core ingredients. “The production of cement contributes an estimated 85 to 95% of concrete’s carbon footprint,” Lisa Barnard, sustainability and customer engagement program manager for Chryso, previously wrote for gb&dPRO. “CO2 is produced during a chemical reaction that takes place when cement is being manufactured.”
Fortunately the concrete industry has made strides when it comes to the material’s overall sustainability, as exemplified by two revolutionary innovations: low-carbon concrete and ultra high performance concrete.
Low-Carbon Concrete
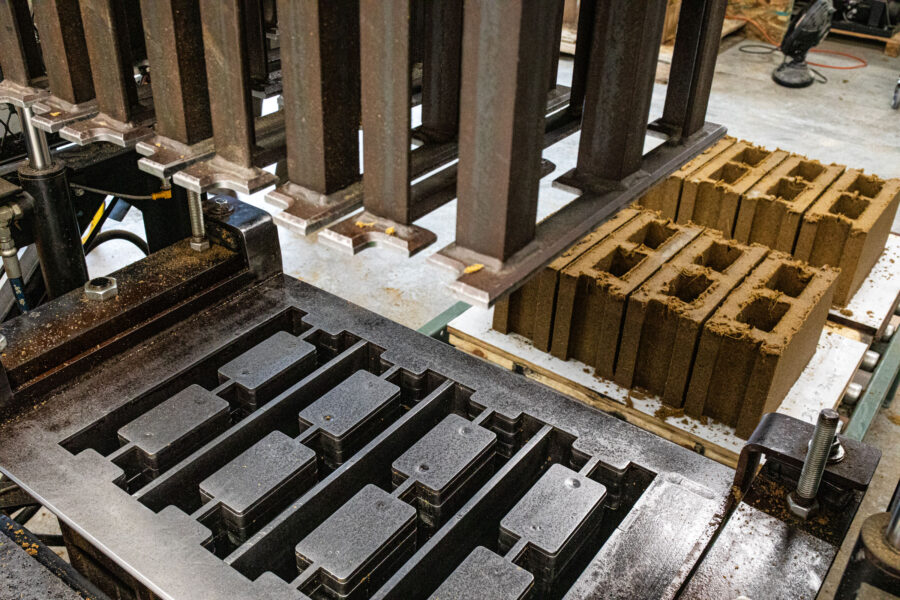
Prometheus Materials’ ProZero is a zero-carbon bio-concrete solution that eliminates the need for carbon-intensive limestone-based cement. Photo courtesy of Prometheus Materials
Low-carbon concrete refers to any concrete produced with a lower carbon footprint than conventional concrete, typically as a result of incorporating cleaner energy sources into the manufacturing process, using alternative/recycled materials to reduce cement requirements, or a combination of the two.
Holcim—a leading building material supplier—has made a commitment to power all of their US operations with 100% renewable energy by the year 2030. The company’s Fort Totten ready-mix plant in Washington, DC, was recently equipped with a solar array capable of generating between 1,300 and 1,500 MWh per year of renewable energy. They’ve also made strides in reducing their concrete products’ cement content, as evidenced by ECOPact, a low-carbon concrete solution that achieves anywhere from a 30 to 90% reduction in embodied carbon. “The primary motivation [for developing ECOPact] was the urgent need to reduce our CO2 emissions,” Michael LeMonds, chief sustainability officer for Holcim US, previously told gb&d. “We now have the capacity to deliver that change.”
Prometheus Materials has pioneered innovations in the use of alternative raw materials, culminating in the creation of ProZero, a zero-carbon bio-concrete solution that virtually eliminates the need for limestone-based cement. The revolutionary product is produced by stimulating microalgae to create biomineralized calcium carbonate that is then dried and used as the basis for bio-cement.
Beyond transitioning to cleaner energies and making use of alternative materials, concrete manufacturers can also reduce their carbon footprint by way of carbon capture, storage, and utilization technologies. More on that later.
Ultra High-Performance Concrete
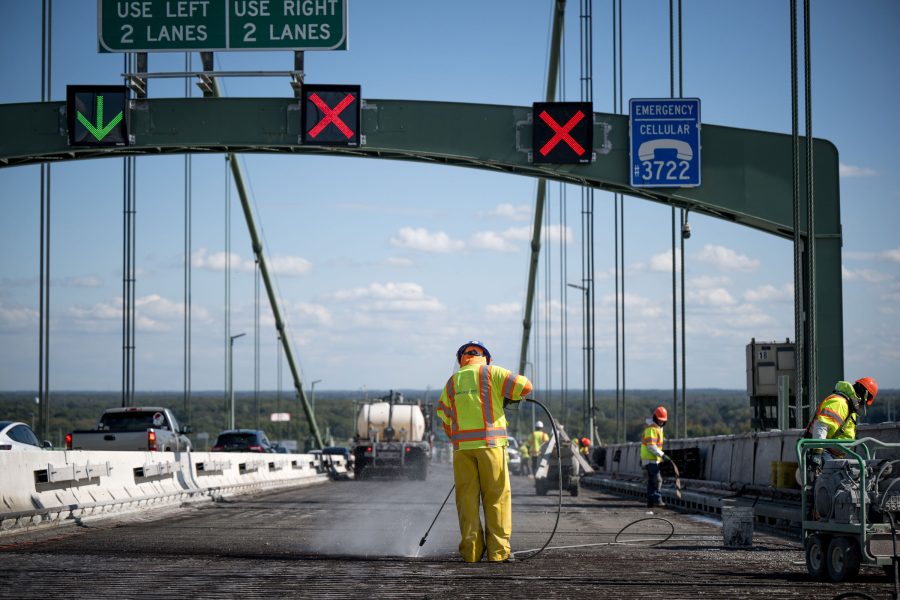
Ultra high-performance concrete formulated by Ductal and containing admixtures from Chryso helped the Delaware Memorial Bridge rehabilitation project save time and reduce embodied carbon emissions. Photo courtesy of Chryso
Ultra high-performance concrete (UHPC) is a type of high-performance concrete renowned for its exceptional durability, strength, and flexibility—qualities that come from the addition of fiber reinforcement and super-plasticizing agents to the concrete mixture. UHPC possesses a compressive strength up to 10 times higher than that of traditional concrete, meaning projects require less of it to achieve the same ends, reducing overall embodied carbon.
UHPC played a crucial role in the rehabilitation of the Delaware Memorial Bridge, a pair of twin suspension bridges that span the Delaware River and connect Delaware with neighboring New Jersey. The project made use of over 5,000 cubic yards of Ductal-supplied UHPC containing Chryso admixtures that reduced water requirements and provided a consistency which allowed the contractor to pave downhill, saving both time and money.
The Delaware River & Bay Authority chose a UHPC overlay in place of a traditional concrete overlay to help minimize the amount of weight added to the structure and improve the bridge’s long-term durability. “The future of UHPC in construction is bright,” Chryso North America President Steve Williams previously told gb&dPRO. “The greater strength with less material needed and longer service life of more than 50 years makes UHPC a key component in the sustainability goals of the construction industry.”
2. Green Hydrogen Production
As public interests begin to shift away from fossil fuels as the dominant form of energy production, renewable energies and cleaner-burning fuels are picking up steam. One promising form of clean energy is green hydrogen, a fuel created via the electrolysis of water. This process involves the use of a direct electric current to facilitate a chemical reaction that splits the oxygen and hydrogen molecules in water.
Green hydrogen differs from the more conventional grey hydrogen—or hydrogen gas produced using electricity derived from fossil fuels—in that the electrolysis process is powered exclusively or almost exclusively by renewable electricity, meaning it produces zero or near zero greenhouse gas emissions.
Green hydrogen is particularly useful in industries and applications where electrification is difficult or simply not feasible, such as in refineries, chemical production, and the international shipping trade. Green hydrogen also has potential for use in long-term energy storage.
3. Prefabrication & Modular Construction
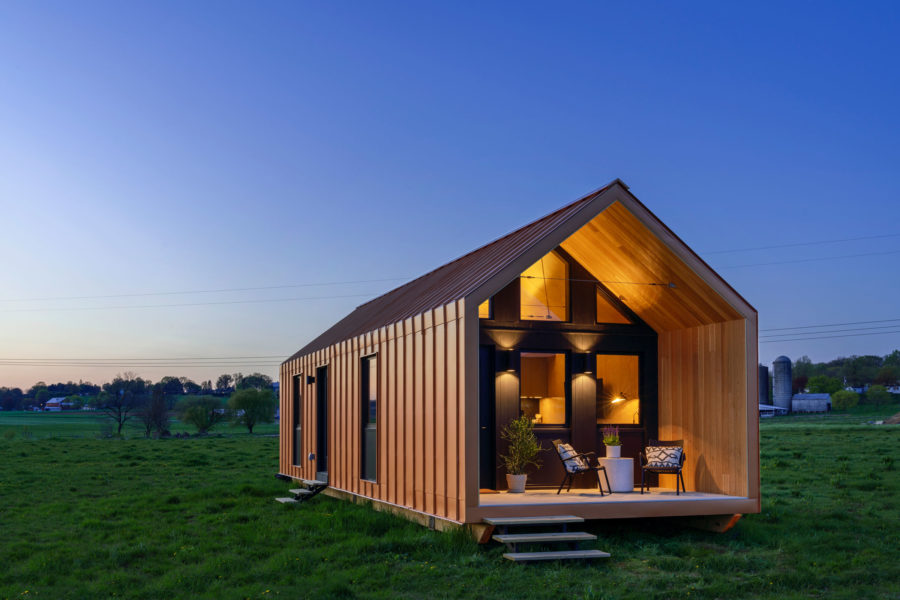
Liv-Connected manufactures design-focused modular homes that can be rapidly deployed and endlessly customized. Photo courtesy of Liv-Connected
Prefabrication involves manufacturing all (or most) of a building’s pieces in an offsite factory before those pieces are then transported to and assembled at the build site. Thanks to recent advancements in prefabrication technology, the process has become an increasingly viable means of improving energy efficiency, reducing waste, and shortening construction times.
Modular construction takes prefabrication to the next level by preparing and assembling entire rooms and building units in highly controlled environments. These modules are then transported to the build site for final assembly—a process that typically involves the modules being lifted into place using a crane—drastically reducing on-site construction times.
Liv-Connected is one company pioneering innovations in the world of modular home construction. Started as a disaster relief project, Liv-Connected has since become a leading designer of rapidly-deployable prefab modular homes marketed towards the general public, with the Conexus and Via being the company’s two base options.
Conexus makes use of Liv-Connected’s proprietary Component Linked Construction system that allows the home to fold up extremely tightly and be reconfigured into a variety of floorplans. To accommodate flexibility, additional pods can be added to Conexus for quick and easy growth, while various health-care technologies—like LiDAR systems and telemedicine portals—can be integrated to help facilitate aging-in-place.
All Liv-Connected modular units are designed with sustainability in mind and only generate 10% of the waste that a conventional stick-built construction project would create. Liv-Connected has also worked to establish an environmentally-conscious value chain and is committed to sourcing materials responsibly.
“We’re establishing a partnership with a lumber and plywood manufacturer that does everything based in the United States, uses rapidly renewable trees in all their products, and doesn’t use formaldehyde in their adhesives, so it’s the most thoughtful type of lumber you can use,” Jordan Rogove, COO and director of architecture and design at Liv-Connected, previously told gb&d.
Each unit comes solar-ready, meaning homeowners can purchase and install PVs at a later date if desired; they also offer battery storage options to help accommodate off-grid living.
4. Low-Carbon Fireproof Coatings
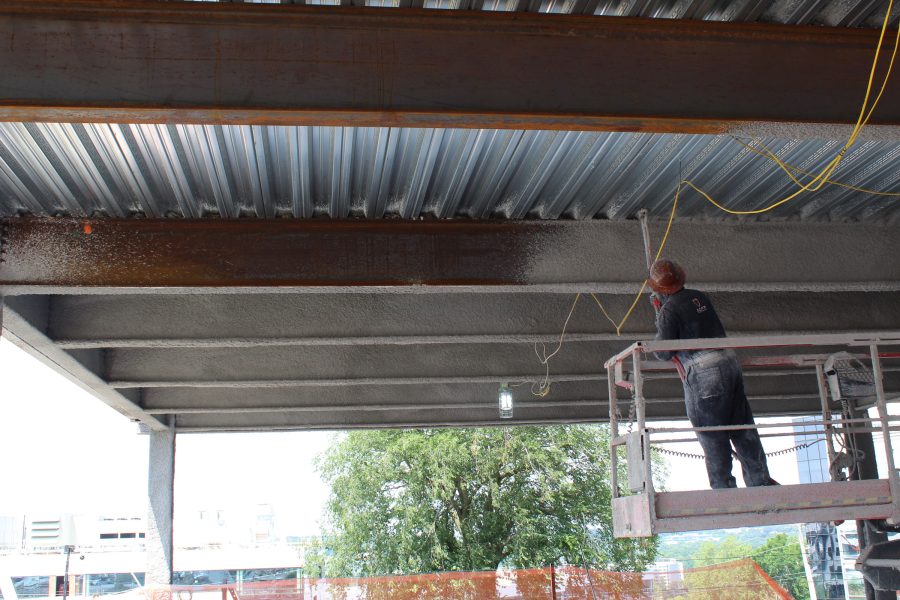
GCP’s MONOKOTE has a low GWP and is designed to reduce the rate of temperature rise in steel or concrete in the event of a fire. Photo courtesy of GCP Applied Technologies
As wildfires continue as a result of our rapidly changing climate, fireproofing the built environment has never been more critical. What’s equally important, however, is making sure the fireproofing solutions we implement aren’t contributing to the problem by way of their own embodied carbon emissions.
“Fireproofing can be as much as 2% of the embodied carbon in a building. While not huge like, say, steel or concrete, it’s big enough to make a measurable difference—like the recycling of your single soda can. Certainly more than carpet,” John Dalton, GCP’s fire protection technical service manager, previously told gb&d.
That’s why companies like GCP, a Saint-Gobain company, are always working to reduce the carbon footprint and overall global warming potential (GWP) of their fireproof coatings, going above and beyond what most architects and building codes require. “We have been at the forefront of that development for almost a century, and we are keen to be around for the next one,” Dalton says. “I am excited about what the next five to 10 years will bring in terms of our formulations and product characteristics.”
GCP’s MONOKOTE, for example, has about half the GWP compared to competing products, with 70% of its materials made at a hydro-powered plant. As further testament to GCP’s commitment to both sustainability and transparency, MONOKOTE meets LEED V4 requirements and has a third-party verified Environmental Product Declaration to back up its eco-conscious claims. And if that’s not enough, MONOKOTE is also durable with a 50+ year operational lifespan, reducing long-term maintenance costs and new material needs.
5. Insulated Glass
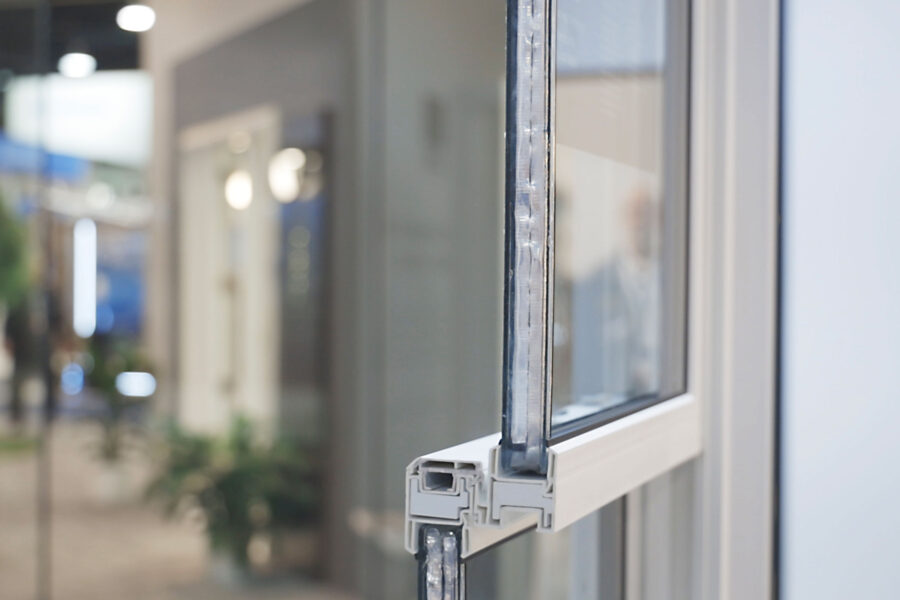
Thin triple insulated glass unit. Photo courtesy of PGT Innovations
According to the DOE, approximately 25 to 30% of a building’s heating and cooling energy is lost through its windows, leading to a significant amount of energy waste and increasing operational emissions. Installing insulated glass can help prevent a significant portion of this energy waste, reducing heating and cooling loads.
Insulated glass units (IGUs) contain at least two panes of glass, with three- and four-pane varieties also available. The space between each pane is filled with an inert gas—typically argon or krypton—which in turn acts as an insulative buffer, helping to prevent unwanted heat transfer. Double-pane IGUs have almost entirely replaced the traditional single-pane window, serving as the industry standard over the last 50 or so years.
Triple pane IGUs are still something of a novelty, despite being up to 20% more efficient than their double-pane counterparts. “Less than 5% of windows sold in the US today are triple pane units, so most window frames are not able to fit a triple-pane unit,” Bob Keller, senior vice president of product innovation and technology at PGT Innovations, told gb&d in a previous publication.
PGT Innovations is looking to change that with their groundbreaking Thin Triple IGU technology, which comprises two outer panes of traditional glass and a single pane of incredibly thin, ultra-lightweight Architectural Technical Glass from Corning Incorporated.
“With our Thin Triple IGU technology, most windows will be able to drop in a triple without changing the rest of the window,” Keller says. “This will give end customers significantly more options for meeting their higher energy efficient needs.”
6. Hydronic Radiant Heating & Cooling
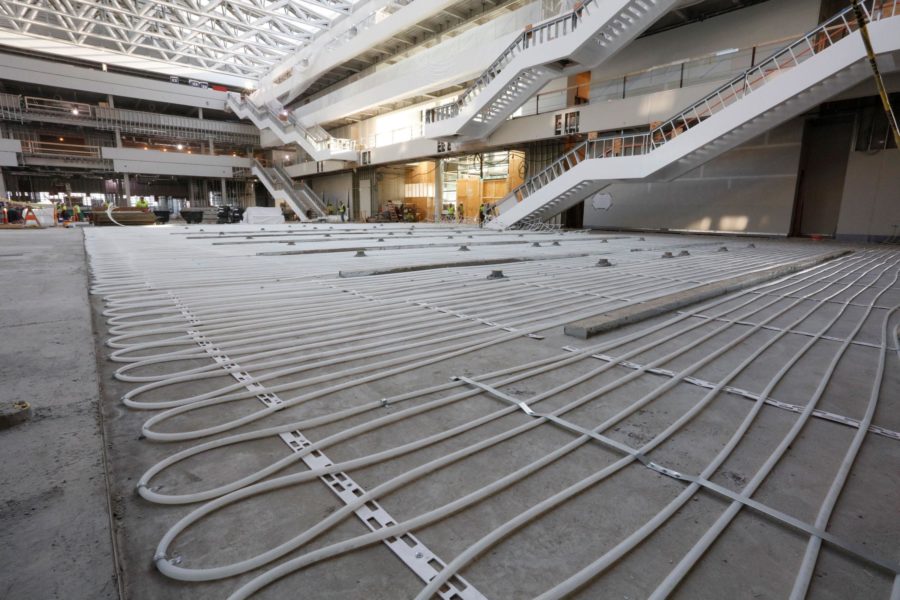
Hydronic radiant floor systems not only promote cleaner indoor air, but also boast a higher energy efficiency than standard air heating systems. Photo courtesy of Uponor
Approximately 28% of global carbon emissions are attributed to the operational emissions of the built environment, with heating and cooling accounting for over a third of those emissions. Improving the insulation capabilities and overall airtightness of building envelopes can help reduce operational energy requirements, as can the installation of hydronic radiant heating and cooling systems in place of traditional forced-air HVAC systems.
“Water has the capacity to transport energy 3,500 times greater than air,” Kim Bliss, content development manager at Uponor, previously wrote for gb&d. “That means a hydronic radiant heating system that uses water to heat a space rather than air will be much more energy-efficient.” On average, radiant systems operate 25% more efficiently than forced-air HVAC systems.
Hydronic radiant heating systems circulate heated water—or a mixture of water and antifreeze—through a closed-loop network of pipes laid underneath a building’s flooring. These pipes make contact with the floor assembly and transfer heat by way of infrared radiation directly to the air, occupants, furniture, and any other objects in the space.
By directly transferring heat through contact, hydronic radiant heating systems align more closely with the body’s ideal heating curve, allowing occupants to actually feel warmer at a lower temperature. “People are more comfortable with a radiant floor heating system at a lower thermostat setting, such as 68℉, than with a forced air system at a higher thermostat setting like 72℉, writes Bliss. “Those four degrees can make a big difference in energy use over time.”
Similarly, hydronic radiant cooling systems use contact to absorb and remove heat from interior spaces. Pipes and panels are pumped with cold water, which slowly absorbs heat within the space and lowers the room’s ambient temperature. When paired with appropriate dehumidification measures and/or a dedicated outdoor air system, radiant cooling systems can be effective in almost any climate.
In addition to being energy efficient and comfortable, hydronic radiant systems also help to improve indoor air quality as they do not stir up dust, dander, and other airborne pollutants during their operation. They are also much quieter than traditional forced-air HVAC systems, bolstering indoor environmental quality and reducing distractions that might otherwise be detrimental to occupant productivity.
7. Metal Cladding
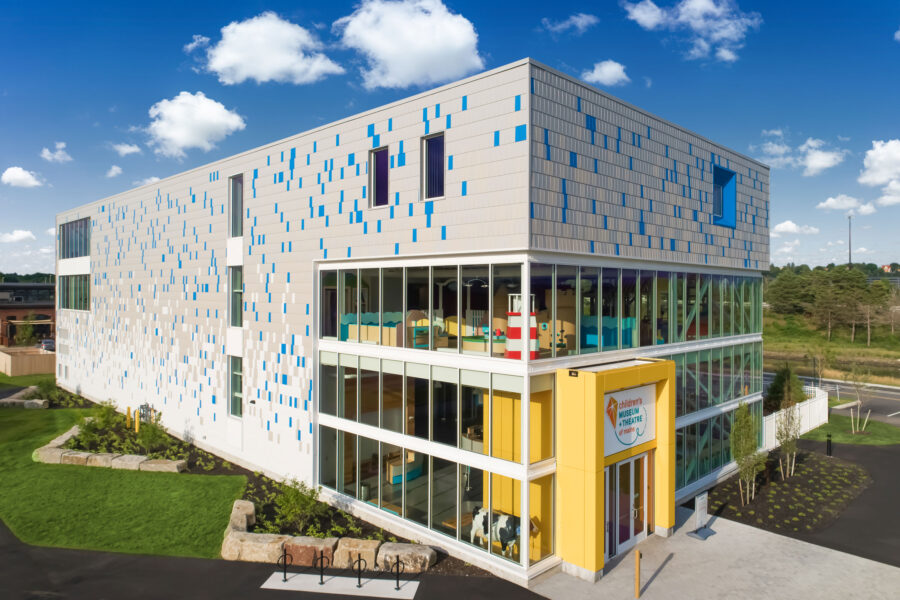
The Children’s Museum and Theatre of Maine features PAC-CLAD Precision Series TS Tile. Photo by Matt Horton
Energy efficiency has become one of the single most important factors in contemporary building design, especially when it comes to cladding and the building envelope.
“The building envelope has evolved, and we’ve been evolving along with that envelope,” Kenneth Holler, outside sales representative for Petersen, manufacturer of PAC-CLAD architectural metals, previously told gb&d. “Metal has become a very popular cladding product because of that evolution.”
As an extremely malleable and flexible material, metals like aluminum and steel support a range of styles and aesthetic preferences while simultaneously providing high durability, weather resistance, and longevity—and once they reach the end of their operational lifespan, metal panels can be recycled and their materials reused in other products.
Metal panels—like those that make up Petersen’s PAC-CLAD catalog of products—can also help block UV rays and reduce building cooling loads for greater energy efficiency. All PAC-CLAD panels are finished with Kynar, a durable resinous coating with a high solar reflectivity index that prevents excessive solar heat gain. “Just by putting our metals on the walls or roof you will help reduce the heat gain inside the building and therefore reduce the strain on the HVAC system,” Tom Becka, a regional sales manager at Petersen, told gb&d in a previous publication.
Manufacturers have also started offering metal cladding panels with built-in insulation, drastically improving their thermal performance. “We’re now moving insulation to the outside of the building. The wall panel becomes part of the whole rainscreen system. We’re using it to get better efficiency, better sustainability, and better energy performance,” Holler says.
Kingspan, for example, carries a range of insulated metal panel solutions that make use of their proprietary QuadCore technology. QuadCore insulation boasts up to 11% better thermal performance than polyisocyanurate foam and as much as a 60% thermal improvement over rigid polyurethane foam, possessing an impressive R-value of 8.0 per inch of material.
QuadCore insulated panels are also GREENGUARD Gold certified—meaning they are low-VOC—and carry Environmental Product Declarations, showcasing Kingspan’s commitment to both transparency and sustainability.
8. Mass Timber
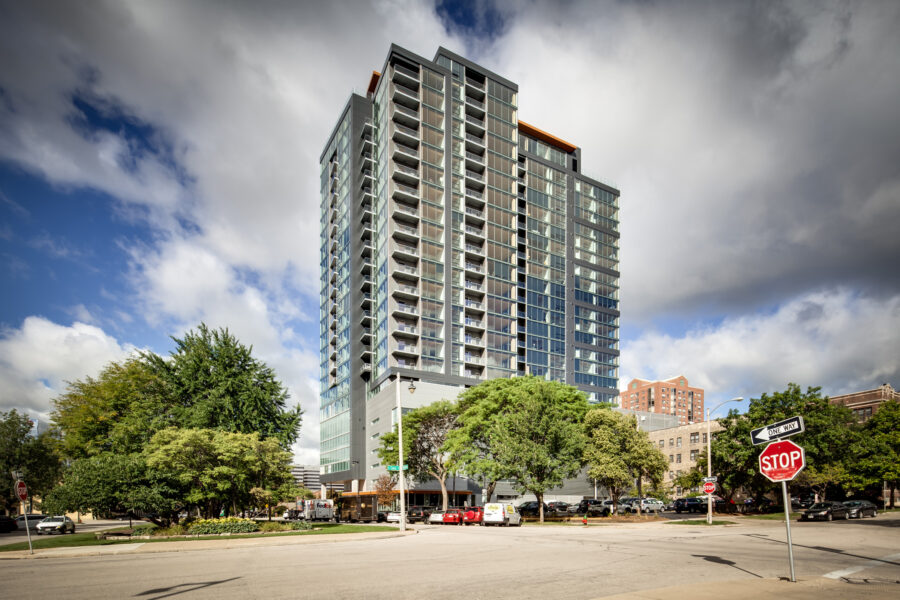
Designed by Korb + Associates, the Ascent MKE building in Milwaukee is the world’s tallest mass timber building. Photo courtesy of Korb + Associates
Mass timber refers to a subset of prefabricated, engineered wood made by binding multiple layers of wood planks together; the resulting product is much stronger and more structurally sound than traditional timber, which allows it to be used as a viable, low-carbon alternative to concrete and steel.
There are four basic categories of mass timber: cross-laminated, nail-laminated, dowel-laminated, and glue-laminated.
- Cross-laminated timber (CLT). Several layers (typically an odd number) of wood planks are glued together, with each layer laid perpendicular to the one above and below it.
- Nail-laminated timber (NLT). Considered the oldest form of mass timber, NLT is created by binding multiple layers of wood together using nails.
- Dowel-laminated timber (DLT). Holes are drilled in wood planks and then bound together by long wooden dowels.
- Glue-laminated timber (Glulam). Layers of wooden planks are attached to one another using glue; glulam differs from CLT in that each plank layer is laid in the same direction.
As an organic material mass timber actually sequesters CO2 throughout its operational lifespan, allowing buildings to drastically reduce their total embodied carbon. The tallest mass timber building in the world, Ascent MKE, for example, is estimated to sequester approximately 7,200 metric tons of CO2 thanks to its extensive use of glulam and CLT.
The true sustainability of mass timber products partially depends on where the timber is sourced and how it is manufactured. When considering mass timber it’s important to look for companies that source their timber from responsibly managed, FSC-certified (or regional equivalent) forests and who practice sustainable business strategies.
Binderholz is a sustainability-minded Austrian mass timber provider whose sites all meet strict Programme for the Endorsement of Forest Certification standards. The company also adheres to a stringent zero-waste policy, ensuring that 100% of all timber raw material—from core to bark—is utilized in some manner; wood processing byproducts like sawdust, shavings, and wood chips, for instance, are converted into biofuels or climate-neutral energy via the company’s proprietary biomass combined heat and power station.
9. Ultra Low-VOC Floor Coatings
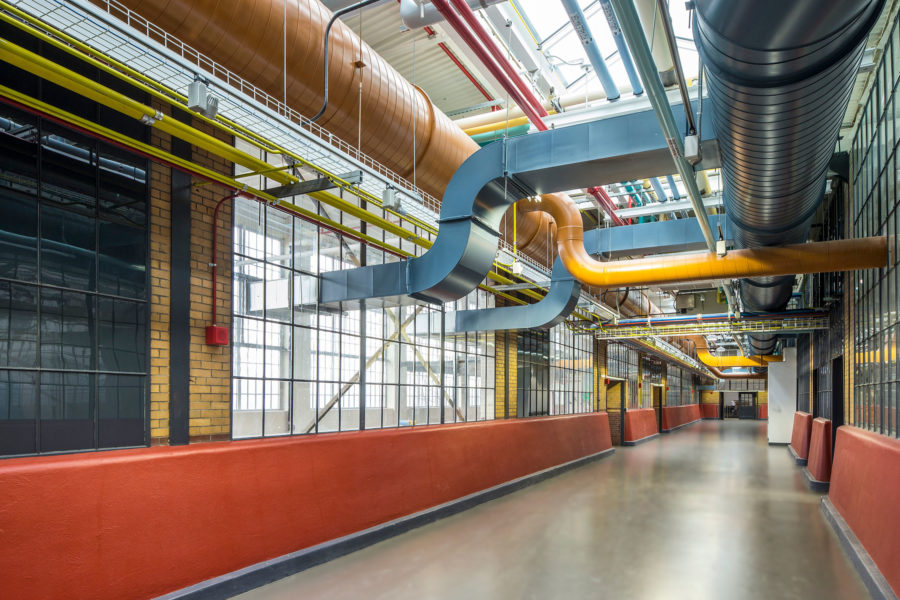
The Energy Innovation Center’s central “racetrack” floor is enhanced with ultra-low VOC polyurethane floor coatings. Photo courtesy of Covestro
Volatile organic compounds (VOCs) are a classification of compounds characterized by their high vapor pressure and low water solubility, qualities that allow them to vaporize at room temperature. Prolonged exposure to certain VOCs indoors can lead to the development or worsening of respiratory issues and other health issues, while VOCs themselves can contribute to both air and water pollution as well as ozone layer depletion and climate change.
Many materials and products emit VOCs, but floor coatings are some of the worst offenders when it comes to interior spaces, especially in large commercial projects. That’s why companies like Covestro have started manufacturing ultra-low VOC alternatives to conventional floor coatings.
Low-VOC coatings are relatively common, but these products are typically more concerned with complying with regulations than actually reducing VOCs to the lowest possible level. Such coatings often hover somewhere in the vicinity of 30 to 50 grams of VOCs per liter, whereas true ultra-low VOC coatings generally achieve 10 grams per liter or less. The chemical makeup of ultra low-VOC polyurethane floor coatings also means they last three to four times longer than many traditional floor coating products, reducing their long-term carbon footprint.
“On a per-gallon basis, ultra-low VOC polyurethane coatings take about the same amount of energy and release similar quantities of CO2 in production as conventional coatings, but the higher durability means you reduce Scope 3 emissions on those materials by roughly 75% over the life cycle of a commercial floor space,” Steven Reinstadtler, market manager of construction coatings at Covestro, wrote in a previous gb&dPRO article.
Covestro is a leading manufacturer of high-quality polymer materials and carries a wide range of ultra low-VOC floor coatings. Their products have been used in a range of applications and contexts, including the renovated Energy Innovation Center in Pittsburgh. “Low-VOC polyurethane floor coatings were used throughout the building on both concrete and wood surfaces, but the best example of their combination of effectiveness, durability, and green factor is in the ‘racetrack’—a common space that loops around the interior of the main floor,” writes Reinstadtler.
10. Artificial Nature
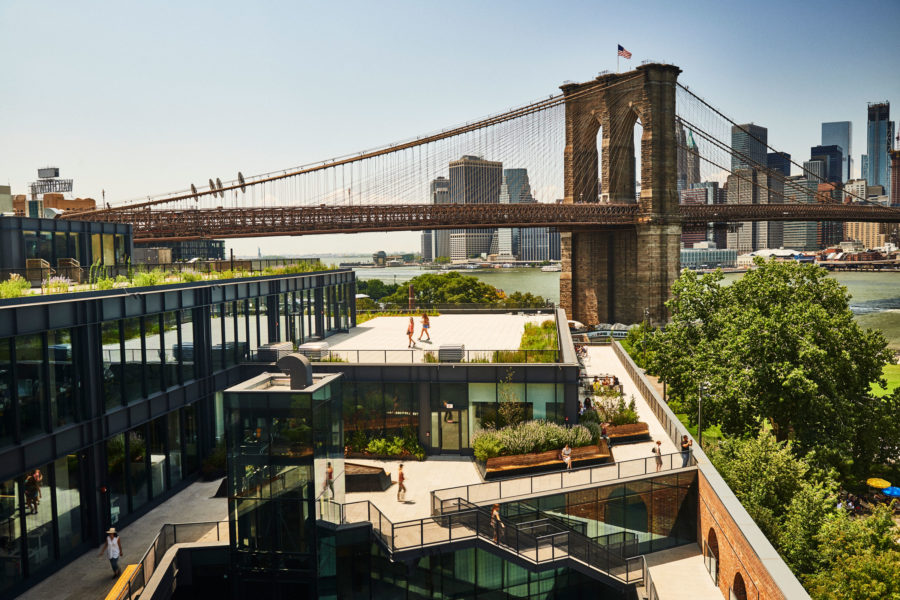
View of rooftop and bridge. Photo by K. Taro Hashimura
Artificial nature by no means refers to something that is fake—rather, artificial nature describes the green spaces cultivated within our man-made environments. And while artificial nature isn’t new, architects and urban planners have become much more intentional when it comes to the design of functional, sustainable green spaces.
Green roofs, living walls, and other green architecture systems are becoming more common in dense urban centers where ground-level green space is scarce. These features not only provide respite amongst the hustle and bustle of city living, but also help mitigate stormwater runoff—thereby reducing the risk of urban flooding—improve air quality, and combat the urban heat island effect through evapotranspiration.
Innovations in artificial nature continue at the ground level in the form of bioswales, rain gardens, urban forests, park networks, wildlife corridors, and the like, with districts and neighborhoods being designed alongside—rather than imposed upon—existing ecosystems. Landscape architects are also much more conscious about selecting native plant species already adapted to regional conditions, reducing the need for supplemental irrigation, fertilizers, and pesticides while simultaneously helping to restore native habitats.
Healthy soil, too, has become an increasingly important factor in the design of urban green spaces. “Utilizing and manufacturing soil is central to artificial nature; reconstructed waterfront edges mitigate sea level rise, and composting for urban farming removes methane,” Jay Valgora, founder and principal of STUDIO V, previously wrote for gb&d. “Combined tree pits, use of structural soil, soft engineered edges, and conjoined plant networks encourage competition, biodiversity, and resiliency.”
11. Product-as-a-Service Models
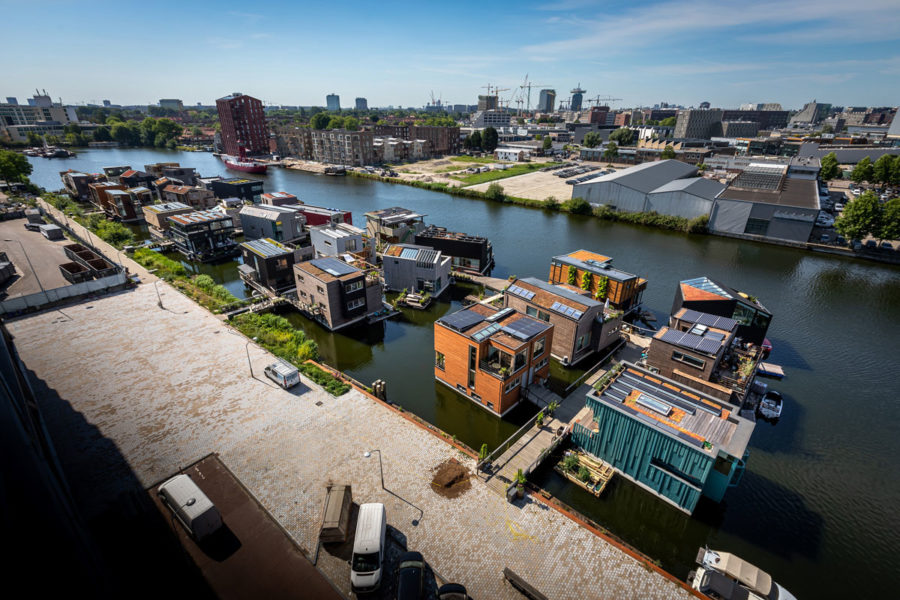
The residents of Schoonschip Amsterdam utilize Hely, a PaaS-provider that allows members to share cars, cargo bikes, and electric bicycles with one another instead of outright owning them. Photo by Isabel Nabuurs
As more and more organizations, companies, cities, and industries embrace circular economic principles, producers and consumers alike are increasingly questioning whether ownership is necessary when it comes to certain products.
This notion is born out of the realization that, more often than not, customers only require temporary access to a product, after which point the product may be passed on to a new user or returned to the service provider for redistribution. This has in turn led to the rise of the product-as-a-service (PaaS) business model wherein customers pay for the use of a product—via a subscription service or on a pay-per-use basis—rather than the product itself.
The residents of Schoonschip Amsterdam—a floating community built on the twin ideas of sustainability and regenerative design—have, for example, reduced their individual reliance on personal vehicles by partnering with Hely, a sharing mobility platform that allows members to share cars, electric bicycles, and cargo bikes between one another.
12. Carbon Capture, Storage, and Utilization
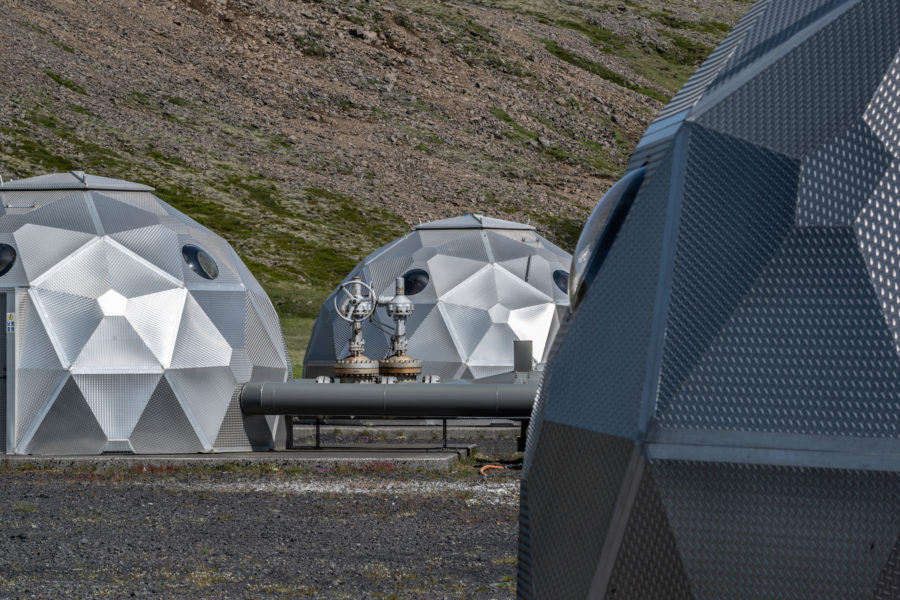
Photo courtesy of Carbfix
Decarbonization is a hot-button issue when it comes to global sustainability efforts—one that has spurred countless innovations in carbon capture, storage, and utilization technologies. CO2 is typically captured onsite as it is produced, but it can also be removed directly from the atmosphere after the fact.
“The direct air capture method is important for capturing emissions that cannot be captured directly, such as CO2 emissions from airplanes,” Sandra Ósk Snæbjörnsdóttir, the geoscientist at the helm of Carbfix, told gb&d in a previous article.
After the CO2 is captured and separated it is then compressed into a liquid form to make it easier to store and transport. Once compressed, the captured carbon is then transported to a storage site, where it is injected into geological formations—like saline aquifers, depleted oil reservoirs, or basalt deposits—and left to form carbonate rock in as little as two years.
Basalt is especially well-suited to this, as it contains many of the necessary metals for efficient mineralization—a characteristic that makes it the rock of choice for Carbfix, an Icelandic company pioneering permanent CO2 storage solutions. The company has successfully stored upwards of 70,000 tons of direct-air-captured CO2 since launching in 2014 and aims to establish storage hubs around the world.
“Carbfix is going to play a big part as industries are struggling to find a manageable solution to get rid of their carbon,” Silja Y Eyþórsdóttir, digital media specialist at Reykjavik Energy, previously told gb&d. “The biggest obstacles for Carbfix going forward are not technological but rather the willingness of governments and the private sector to transition to a green economy.”
Alternatively, captured carbon can be used as an ingredient in other products, a process known as carbon capture utilization (CCU). CCU involves using captured carbon directly (i.e. not altered at the chemical level) or indirectly (i.e. transformed) in the production of products like carbonated beverages, fertilizer, and some cleaner-burning fuels. Untransformed CO2 can even be injected into concrete during the mixing process as a means of strengthening it and reducing the amount of required cement content.